by Tom Nash
A few years ago, we were told that all vehicles produced worldwide would be equipped with 36/42-volt electrical systems by the end of this decade. It isn’t going to happen – not for a long time, at least. It may eventually come to fruition, but a lot more research, development and industry cooperation will be needed. The big question at this juncture: Is it needed?
It all started in the mid-‘80s, when automotive engineers – mostly in Germany – were concerned about the ability of electrical systems to handle all the technically-advanced components slated to be included in automobiles of the future. The addition of passenger convenience, safety, infotainment and communications systems, and onboard interactive control and regulating modules would require big increases in electrical capacity.
Big Drag
Another big consideration was engine efficiency. The amount of energy needed to drive auxiliary systems – such as the AC compressor, power steering pump, water pump, etc. – drags down the efficiency of the engine. It was foretold that the savings in fuel realized by the changeover to electrically-powered components could run as high as 20%. As a result of this reduction in fuel burned, we were told, emissions would be lowered and the environment would benefit.
Engine compartment packaging was another justification. Just think, you wouldn’t have to have all those accessories hanging off the front of the engine and being driven by a bulky belt/pulley/tensioner system. Instead, you could mount them pretty much anywhere you wanted. This could also be a boon to serviceability. How about a water pump wide open on the fender apron?
More efficient, lightweight electrically-driven, electronically-actuated and controlled systems (called mechatronics) were being developed, including drive-by-wire throttle, power steering, brakes, suspension, electronically-controlled electrically-powered valves, electric cooling fans, coolant (water) and oil pumps, to name a few. These components and systems, some already in use, provide better dependability, suffer less wear and serve to reduce weight, all the while not stealing energy from the engine.
Addressing the on-board energy crisis and achieving the efficiency, packaging and mechatronics benefits would be easy, according to the experts, with elevated electrical architecture. It all sounded ideal and relatively simple for the industry to change to a higher operating voltage with commensurate amperage and wattage. While it sounded good in theory, it didn’t quite work out as expected. Many, many factors led to the delay and possibly long-term postponement of the 36/42-volt parade.
What’s a 36/42-Volt System?
First, let’s clarify what is meant by 36/42 volts. The present automotive electrical architecture is actually 14 volts, as you know. We all refer to it as a “12 volt†system because the battery has six 2.1 volt cells for a total of 12.6 volts, which charges just right at 14 V. A more accurate name would probably be the “12/14 volt†system. Triple that and you’ve got 36/42.
When automotive engineers began looking for a higher system voltage to establish as a standard, they wanted to raise the level as high as possible, but not so high as to create a shock danger to humans.
Mercedes-Benz is credited as being the first automaker to call for higher voltage systems. An industry-wide research consortium was formed, led by the Massachusetts Institute of Technology. The MIT/Industry Consortium on Advanced Automotive Electrical/Electronic Components and Systems began to address the technical issues of changing over to 36/42 volts. The research was financed by automotive companies, which ponied up $50k each to be part of the consortium.
After establishing that human tissue can be damaged at around 56-60 volts (wattage and amperage levels being considered), and assuming that present components could easily be adapted, the architecture point of 36/42 volts was derived. It sounded simple and eminently logical.
Cast of Thousands
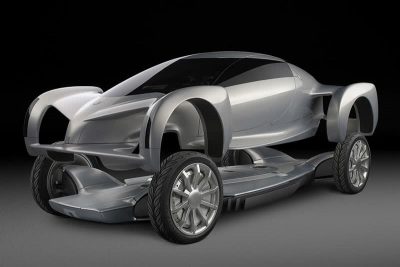
The first entities to get on board would be the planning, standards and regulation associations, organizations and societies. In Europe, automakers and suppliers formed a working group known as “Fourum Bordnetz†to create standards for the Euro-based International Organization of Standardization (ISO).
On this side of the pond, the Society of Automotive Engineers (SAE) became the leader in gathering and sorting out the various methods, devices and knowledge for development of standards. Working with the top engineers from international companies and organizations, SAE began to call for technical papers and form committees to set standards.
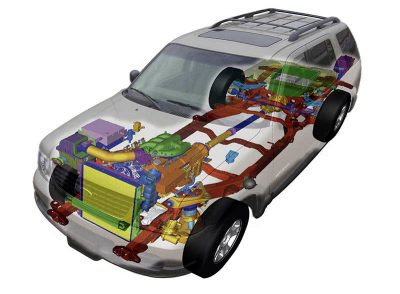
The foremost vehicle manufacturers to become involved – because they had the largest portions of the global market and the biggest technical budgets – were BMW, DaimlerChrysler, GM, Fiat, Ford, Honda, Peugeot /Citroen, Renault /Nissan, Toyota, and VW/Audi.
BMW, GM, Ford and DaimlerChrysler all boasted that they would have 36/42-volt systems on the road by 2003 or 2004. GM showed its AUTOnomy fuel cell concept equipped with a 36/42-volt system and promised to produce everyday drivers with similar systems by 2007. Ford pledged to have a hybrid Escape with 36/42 volts on the road in 2004 also.
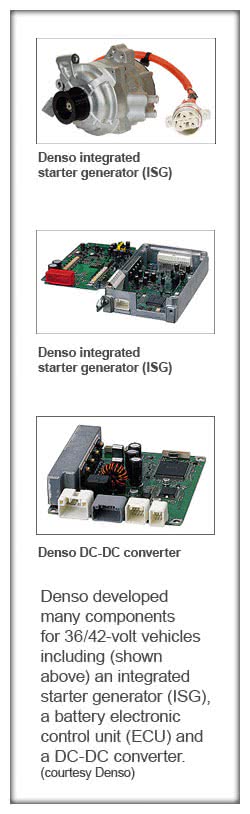
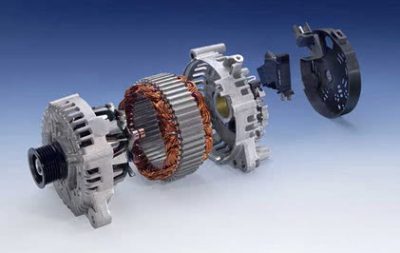
These companies began laying out their plans for integrating 36/42-volt systems and working with their main component suppliers. Among these highly-reputable suppliers were Aisin, Bosch, Continental Teves, Delco Remy America, Delphi, Denso, Johnson Controls, Lear, Magneti Marelli, Motorola, Valeo, VDO Siemens, Visteon, Yazaki and a host of others. They were drawn into the creation of high-voltage systems and began expensive research and development initiatives. Many of the products these suppliers created for 36/42-volt systems still sit in inventory, waiting for buyers.
Implementation Imagination
The steps in implementation were to have followed this pattern:
•The 36/42-volt architecture would be initially applied to high-end luxury vehicles where the cost would readily be accepted. The technology would then trickle down to entry-level vehicles over a few years, once the technologies were perfected and made cost-effective.
•The European manufacturers – primarily the German companies – were slated to convert to the new standards first.
•Dual voltage systems were to be used as an interim solution. Until the design and production of 36-volt components was perfected, 12-volt sub-systems would be used to power devices that have not been redesigned for the higher voltage. This could be achieved by the use of two batteries – one 12-volt and one 36-volt – and coupling them with a DC-to-DC converter, stepping down the electrical pressure to power those components still functioning on 12 volts.
What Went Wrong?
There are many reasons why 36/42-volt standards have not yet been adopted and produced. The three main culprits are technical difficulties, corporate political posturing, and, the big one, financial constraints.
Technically, many theories that sounded good in the laboratories and think tanks did not work out so well when it came to implementation and mass production. Some problems became bigger obstacles than first thought.
Progressing through all the international standard-setting meetings proved difficult because the many parties disagreed on technical details and began to champion ideas that suited their own purposes. European, Asian and North American representatives all wanted to create standards based on their individual technical systems. This campaigning extended to companies that wanted the standards to reflect the use of products and components protected under their own patents. Of course, there’s nothing wrong with trying to protect your own corporate interests and ensure financial growth, but political maneuvering often gets in the way of true progress and bogs down the entire process.
One of the biggest factors in the waning efforts to develop 36/42-volt vehicles has been money. Each company involved has spent millions to design new components and systems, but those devices sit in limbo at this point. The return on investment hasn’t materialized, and may not. The general downward business trend in the automotive market forced companies to look long and hard at how they were spending money. To satisfy the need for profitability, most companies have now turned their R&D dollars toward other emerging technologies such as diesels, hybrids and fuel cells.
Problems, Problems
Dr. David J. Perreault, a research Scientist at MIT’s Laboratory for Electromagnetic and Electronic Systems initially led the MIT/Industry Consortium on Advanced Automotive Electrical/Electronic Components and Systems. Dr. Perreault presented a technical paper and spoke at the Convergence 2000 conference on October 17, in Detroit. He stated that the higher power would allow many new systems to be introduced and many existing systems to work better.
“It doesn’t sound like it would be that difficult to do,” Dr. Perreault said. “But it turns out that there are several subtle technical problems.” This comment turned out to be somewhat understated.
Some of these technical difficulties were clearly explained by Paul Nicastri of Ford Motor Company’s Research Laboratory at the 2001 International Automotive Technician Network (iATN) Convention in Dearborn, Michigan.
Nicastri exposed the problems with electrical connections under a 36-volt load. He stated that the entire system will have to be redesigned to handle the high voltage. Wires, relays, and connectors will need improvements to function without damage. Arcing of 36-volt current is the primary concern. Unlike 12-volt arcing, which is fairly low in amperage, short in arc length and easily disrupted, the arc in a 36-volt system can be much longer and reach extremely high temperatures – over 4,000 deg. F – posing a dangerous situation.
He demonstrated these arcing problems with a video showing normal and slow motion views of a 36-volt connector under load being disconnected. The resulting arc and flash entirely disintegrated the tip of the male connector. The female end was badly damaged and unusable.
Special arc-suppressing connectors, he stated, would have to be developed, and, most likely, the system will necessarily need to be shut off before servicing, using the types of switches found on existing hybrid vehicles.
Nicastri also demonstrated the increased corrosion factor of wires under a 36-volt load, compared to 12-volts. Enclosed, protected connections, he said, will have to be devised.
18 Cells!
Batteries pose a number of problems. High voltage batteries will need to be durably encased for protection in case of collision. The connectors will have to be designed to cut the threat of arcing. Special dual-stage relay-controlled connections that shut off power while the main contacts wed, then reconnect have been proposed. Delphi developed a prototype a few years ago, but it was never produced for the mass market.
The need to jump or charge 36 volt batteries is another concern. Special connections and devices will need to be designed. The ability of a 36 volt lead acid battery to safely withstand even momentary reversal of polarity has not been established. Mistakes can happen, even with professionals. Just imagine the possibilities with a non-savvy vehicle owner.
The SAE began to address these obstacles in the late ‘90s by setting up standards committees. The Electrical Distribution Systems Standards Committee authored a standard known as J2622 – Battery Connections. Its purpose was to “define test methods and set standards for development, production, and field analysis of electrical terminals, connectors, and components that constitute the direct connection to the storage battery of road vehicles having 42 volt nominal electrical systems.†At last check, the committee had developed a model for a safe battery connection, but has not met in some time.
Another obstacle is the adaptation of lighting systems to the proposed 36/42 volt architecture. Preliminary testing indicated many problems with interior lighting, which would need to be stepped down to a lower voltage. Exterior lighting, especially headlamps, require further research to find cheap and efficient ways to utilize 36/42-volt energy. Without some basic redesign, headlamp filaments would have to be much longer and thinner, resulting in increased fragility and shorter burn life.
One possible answer is adapting the technology known as Pulse Width Modulation (PWM). Used in other areas for years (remember feedback carbs?), PWM is simply a switching on and off of the voltage, resulting in a square wave form. With the duty cycle cut in half, many of the problems associated with arcing and corrosion could be addressed. Much research and engineering would, however, be needed to develop PWM devices suited to automobiles.
The SAE launched a program to investigate the use of PWM in late 1999. The SAE 42V Exterior and Interior Lighting Cooperative Research Program brought together automakers and electrical suppliers to discuss PWM adaptation, testing and use on incandescent lamps. These lighting problems are another reason to advocate dual 12/14 and 36/42-volt systems within a vehicle.
Even the top automotive business analysts were way off in their predictions, prognostications and projections. At the beginning of the decade, Standard & Poor’s estimated that car makers would build 46,000 vehicles with 36/36/42-volt electrical systems in 2002. This number was expected by S&P to increase to nearly 13 million by 2010. It isn’t going to happen – at least not anywhere near that quickly.
What’s Out There Now
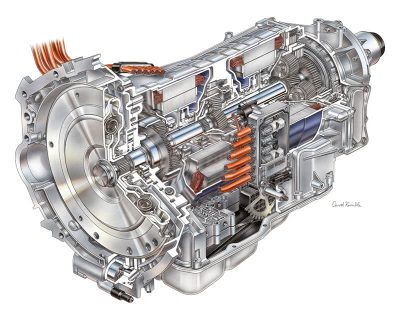
There are vehicles operating with 36/42-volt systems on the road today. General Motors began building and selling light hybrid models of its full sized Chevrolet Silverado and GMC Sierra pickups with dual 36/42-volt and 12/14-volt systems in 2004. The sales numbers have been miniscule and GM has used these trucks as a sort of test fleet.
GM eliminated the conventional starter and generator in favor of a compact integrated starter/alternator (ISA) located in the transmission bell housing. This flywheel/ISA/torque converter creates up to 14,000 watts of continuous power, which is stored in a lead-acid battery pack for use in starting the vehicle, powering the electro-hydraulic power steering system and providing 120-volt AC power for plug-in outlets – two in the cab and two near the rear of the load bed.
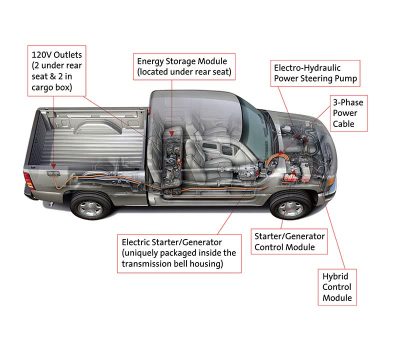
A control module regulates the flow of energy into and out of the starter generator. It also converts the current into different types for different purposes: 42 volt DC is converted to AC for starting, braking-regenerated AC is converted to 42 volt DC for recharging the glass mat battery pack, 14-volt power is converted to 42 volt for jump-starting, 42 volt is converted to 14 volt for the alternator function, and 42 volt DC is converted to 120 volts AC for powering the electrical outlets. Does this system sound complicated enough for you? Regardless, this complex technology makes the two GM pickups ideal for construction, agricultural and industrial uses.
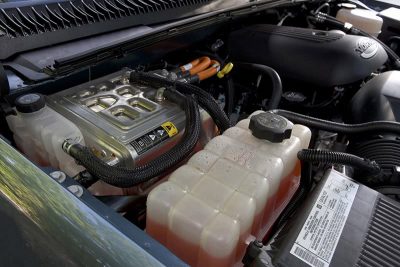
As of last October, Ford, MIT and others were still working on “The acceleration of the development of new 42-volt high-voltage vehicle electrical system standards through the use of virtual engineering concepts and global consensus.†Delphi and many other deeply-involved supplier companies have put 42-volt research on the back burner, or are no longer pursuing it at all.
As It Stands
Many requests for interviews and information on the status of 36/42-volt initiatives to tier one suppliers, automakers and involved associations in the preparation of this article went unanswered or were tersely dismissed. This leads one to believe that the whole idea of converting to 36/42-volt architecture may have been mistakenly undertaken. That nobody in these organizations wishes to openly discuss their conversion efforts speaks loudly.
Perhaps it was premature. or the perceived need caused a competitive panic that resulted in depletion of monetary and human resources. Maybe the rapid advances in ultra-high voltage hybrid technology have leap-frogged the need for 36/42-volt systems. It is to be hoped that the annual global gathering of automotive engineers at the SAE World Congress in Detroit this month will shed new light on the future of these systems. We’ll let you know.
The integration of 36/42-volts – if it ever comes – will impact the entire industry from top to bottom, from beginning to end, involving vehicle manufacturers, tier one suppliers, parts makers and service suppliers, tool and equipment sources and the aftermarket and independent service facilities. It will be the most costly, most time-consuming and most radical event ever to happen in the automotive industry. It would make the switch to automatic transmission, electronic ignition, or disc brakes seem like a walk in the park.
The 12/14-volt architecture we’ve used since the mid-‘50s continues to evolve and still serves us well enough. But, it does have limitations. Just as 6-volt systems needed to be raised after almost half a century, perhaps it’s time to move forward again, fifty years later. The onus rests on those who have the most to gain from the change – the automakers. Once they find it necessary, feasible and cost-effective to make the change to 36/42 volts, we in the aftermarket will have to follow with training and lots of new tools and equipment if we want to keep pace with the rapidly-marching parade of technology.
0 Comments