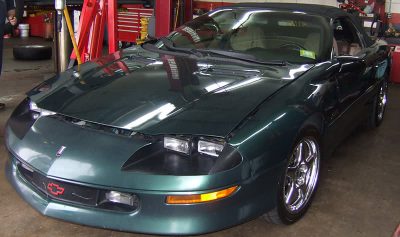
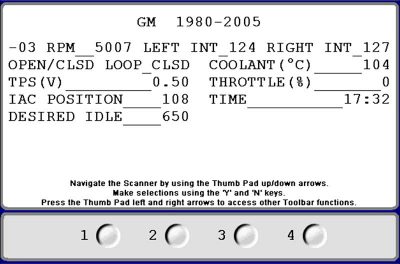
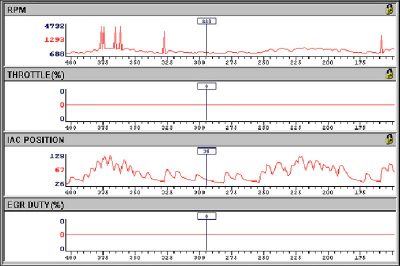
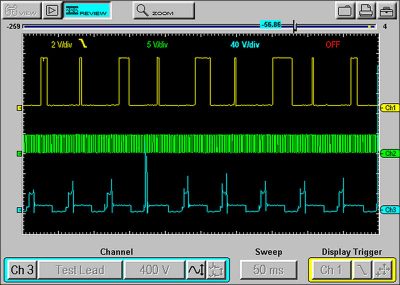
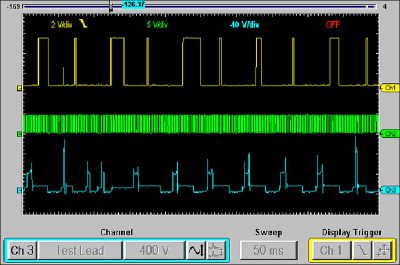
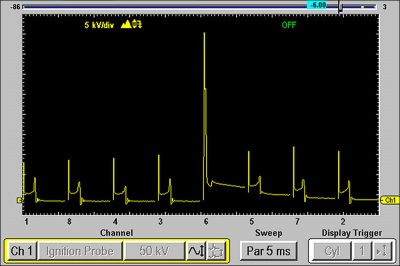
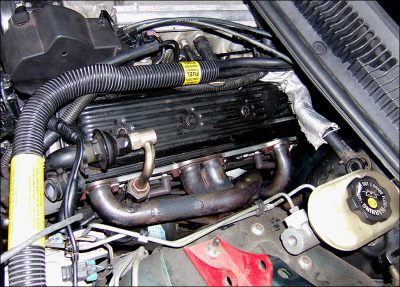
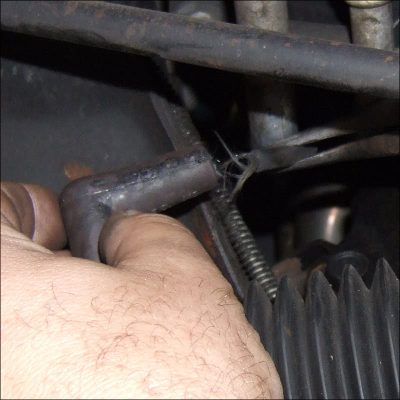
A was called to a shop for a surging idle problem on a 1994 Chevy Camaro with a 5.7L Engine (Figure1). The shop had scanned the ECM for codes and found no codes in memory but noticed that the ECM was not controlling the idle properly. The IAC counts were very erratic and the engine would race up and slow down for no reason at all. When the vehicle was cold there were no problems but as soon as the engine got hot that was when all the fun started. The shop had recently tuned up the engine about 2 months earlier replacing spark plugs, spark plug wires, PCV valve and filters. This problem just started within the past week.
I arrived at the shop and started the engine and it ran like a champ. I could feel nothing wrong with the engine at all. It accelerated fine and had plenty of power with no apparent misfire. I raced the engine to get the engine fully warmed up so I could experience the problem but it still seemed to run fine. I looked at the shop tech and asked him if he was crying wolf or not. This car must have known that I was coming and decided not to act up. These intermittent problems can be a real thorn in the side and in my line of business I usually give the garage a half hour to get the problem to act up or I have no choice but to go to my next stop only to revisit this problem again when the shop can duplicate it.
I had just turned my back on the car to boot up my computer on my truck when suddenly the engine starting running real erratic. It was racing up real fast and then idling back down and racing up again. I could not believe how bad it was running. I grabbed my MODIS to scan the ECM to see what was going on within the DataStream. I chose the main signals that were related to the idling system (RPM, TPS, CTS, IAC counts, Desired Idle, etc). The IAC counts were all over the place and I thought at one point I saw a higher than normal RPM reading without an actual high RPM event. I placed the scanner in movie mode hoping to catch some data to see the erratic RPM input. The problem happened again and I hit the movie capture. When I reviewed the data I was surprised to see one frame of data showing a 5000 RPM increase (Figure2). There was no way the engine reved that high while I was standing there! I next placed the scanner in a graphing mode to get a better picture of what was going on. Number crunching is not made for the human mind and I would rather leave that work up to the MODIS.
While graphing the data (Figure3) I was able to see what was finally going on. The ECM was seeing false high RPM inputs and was only doing its job to counteract the high RPM’s by moving the IAC motor accordingly. The culprit had to be the crank angle sensor because it was responsible for RPM input. I backed the MODIS out of its scanner mode and placed it into a scope mode to get a better look at what was going on with the crank angle sensor. I tagged the low resolution signal, high resolution signal and the coil primary and everything seemed fine except for one primary pattern showing a higher than normal spike (Figure4). Then the engine raced up again and at this point I stopped the scope to play it back. I quickly saw that the coil trigger was erratic at one point but just prior to the event the low resolution signal had a spike in its pattern (Figure5). By looking a little closer you could see that this spike was caused at the exact time that one primary pattern was spiking. The spiking event would occur every one revolution of the low resolution sensor every time one particular cylinder was fired. I wanted to get a closer look at the secondary patterns because it seemed that the spike was caused every time that one cylinder’s primary was released to create secondary voltage.
I backed the MODIS out of the scope mode and went next into the engine analyzer section. I placed the analyzer in parade mode to view all the cylinders and I was stunned to see that the #6 cylinder was spiking close to 45 KV’s (Figure6). This car had a bad plug wire that was kicking back high KV’s into the distributor housing causing a corruption of the low resolution signal. Think about this poor crank angle sensor only trying to do its job while getting hit with some serious lightning bolts. Just imagine you going out to the back yard during a stormy night while carrying in some wood for the fireplace and then all at once a lightning bolt heads your way. Do you really think that you would continue walking to the house carrying the wood or would you drop the wood and run for your life?
I took a closer look at this engine and noticed that someone had changed the stock exhaust and installed header pipes (Figure7). There was no room to get at some of these plug wires from the top of the engine. The #6 plug wire was only accessible from underneath the vehicle. We lifted the vehicle and removed the #6 spark plug wire and the boot actually separated itself from the wire (Figure8). By the looks of the boot end you could see that these new wires were exposed to some serious heat. I had suggested that maybe the owner may have to invest in another wire set that would be able to handle the heat from these header pipes.
I must say that this was one interesting story with a happy ending and I hope all you techs out there have learned from it. It just amazes me how a high resistance in a secondary wire did not cause a serious misfire but yet created a serious drivability problem. Thanks to the MODIS and its multi-use capabilities I was able to stay in one place with one piece of equipment to nail this problem to the cross.
by John Anello
0 Comments