When you first noticed one on the road, you probably thought, “What an unusual looking vehicle.†And the first service problem you ran into was likely when your customer needed brakes. “What, you want me to bring them down so you can match them up? Who ever heard of such a thing?” was a common customer response to your likely request. Eventually, parts suppliers learned the difference between Ate and Bosch, so that problem smoothed out. When it comes to diesel diagnosis and repair issues, however, things are not so easy. Given this winter’s cold weather, you’ve probably run into more than your fair share of “no-starts,†“hard starts,†and “extended cranks.†You probably have some experience with American diesels, such as Ford Powerstroke, Chevy DuraMax, and Dodge Cummins, and may feel pretty comfortable with them. While the same basic principles apply, you can reduce your diagnostic time if you know the particulars of the systems found on the Dodge Sprinter. Scan tool diagnostics used to be readily available to us, but now not so much.
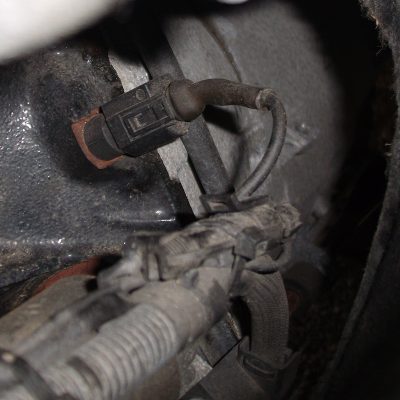
When dealing with no-starts, hard-starts, and extended cranks on pre-2004 Sprinters, you often have to go on a road call and/or tow them in. Or, some incautious person may have tried the dangerous practice of spraying starting fluid or carburetor cleaner into the intake to get the engine started. You’ve probably heard the appropriate cautions: Leave the key on to time out the glow plugs, and spray while cranking. You may do this every day, but it’s our duty to inform you that it’s foolhardy. Suppose, for example, that somebody else accidentally cycles the key — kaboom! While we won’t go on record as recommending it, silicone spray is a much safer alternative.
Actually, nobody should have to add an explosive fuel source to get the engine started regardless of the weather. What engineer would allow a non-starter to be produced? You just have to figure out what the problem is. Glow plugs? Fuel delivery? Injection? These 2.7L vehicles use a direct-injection, common-rail diesel fuel system developed by Mercedes-Benz. Instead of the traditional pump timing high-pressure pulses to the injectors, this works more like gasoline EFI, albeit at much, much higher psi. The common rail is continuously supplied with ultra-high pressure, and the injectors are electrically triggered by means of electronic logic. So, there’s a computer in control of timing and pulse width. Obviously, that control unit needs to know when to fire the injectors, partially on the basis of signals from crankshaft and camshaft position sensors.
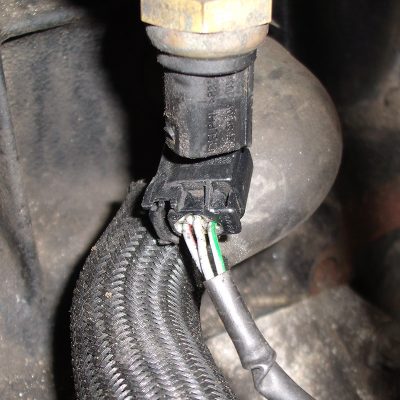
The fuel injection control unit is mounted under the driver’s side of the dash, to the left of the brake pedal. The crank sensor resides on the driver’s side of the engine block toward the back by the transmission bell housing. The engine will not start at all without the crank sensor signal. This sensor is an AC pulse generator. Like most AC pickups, it uses a two-wire design. A good sensor will “ohm out†at about 900 ohms between pins #1 and #2 on the sensor. If you crank the engine at normal speed, you should see about one volt AC. If you’re scoping the signal, expect over 4 VAC peak-to-peak. A normal cranking rpm would be about 200 to 220. A weak battery will yield a lower cranking speed and AC voltage output, so check the battery first.
The engine will start without the cam position sensor signal, but you’ll have a MIL (Malfunction Indicator Lamp) and a code will set. If you have extended crank time, you still need to be concerned with fuel pressure and the glow plug system. There are two halves to fuel pressure: the low-pressure delivery system that draws fuel from the tank and supplies it to the next phase, and the high-pressure pump that is driven off of the camshaft. The high pressure goes to the fuel rail and distribution pipes that supply each injector. Excess fuel is collected in a manifold at the rear of the cylinder head, and returned through the fuel filter, and, finally, a cooling coil.
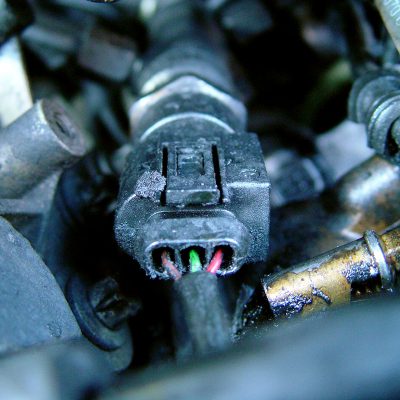
The low-pressure system comprises a mechanically-driven pump that draws fuel from the tank through a filter. That is, unless there’s a blockage somewhere. A clogged fuel filter from additives and contaminants is a common problem. Additives intended to improve lubricity can, over time, settle in the filter and restrict flow. Dodge recommends changing the filter every 30,000 miles, or once a year. The water-in-fuel sensor is mounted in the bottom of the filter up to the 2004 model year. It’s a three-wire sensor with a 12V reference, 12V signal line, and ground. The signal line gets pulled towards ground when there’s water in the fuel.
The purpose of the low-pressure system is to assure that the high-pressure system doesn’t run out of fuel when the engine is under heavy loads. Injection pressure may be as high as 30,000 psi (you read that right — 2,000 BAR!), so a constant supply of fuel is definitely needed. A transparent nylon line feeds the high-pressure pump, so you should be able to see bubbles if there’s air in the system. You can check the low-pressure side by splicing a gauge into this feed line. You should see about 17 psi at idle, but it can go as high as 35 to 45 psi while driving. There’s also a three-wire low-pressure sensor. On the signal line, you should see .5V with no pressure, and about 2.5V at idle. It can go over 3.0V during acceleration.
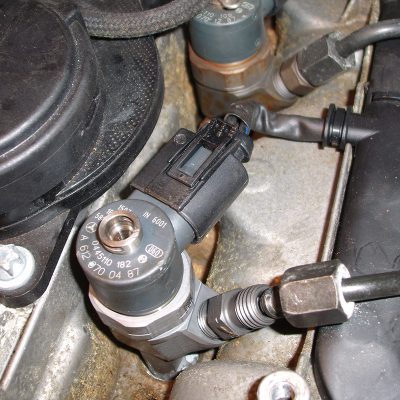
The high-pressure side uses a three-piston pump that runs at 1-1/3 the speed of the camshaft. Like those of all other modern “clean” diesels, it generates tremendous pressure, which is injected directly into the combustion chamber. Full pressure is needed to get the engine started, and volume is relatively low, so even small leaks will bleed off enough pressure to cause a no-start. Be very careful when inspecting the high-pressure side for leaks — wear safety glasses and gloves as there’s plenty of psi to penetrate your skin and give you a diesel tattoo. We’re not aware of any gauge outside of engineering circles that can be tapped into the rail to measure this pressure, but it can be monitored by means of the high-pressure sensor mounted on the front of the fuel rail.
This is a three-wire sensor with a 5V reference, signal line, and ground. You can see these voltages on your DRB III scan tool, but you’ll need the Sprinter Card, a MUX box adapter, and a special red-plug cable. The signal line will have .5V with no significant pressure in the system. While cranking, you should see the voltage rise to about 1.0V as the engine starts. If you do not reach about 875 psi the engine may not start. That’s about .875V at the signal wire. If you don’t see at least that much, look for external leaks in the high pressure lines. There may also be internal leaks. For example, a leaky injector may keep the pressure from building up sufficiently.
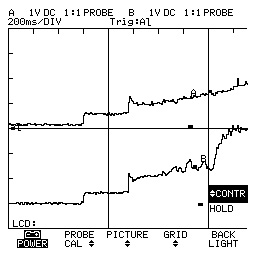
There’s also a solenoid at the back of the high-pressure fuel rail that controls psi according to load. It’s called, logically enough, the Fuel Rail Pressure Control Solenoid, which the fuel injection control unit can close or open to raise or lower fuel pressure according to need. It has an “O” ring at its end. If that should break, it will create an internal leak that will not allow enough pressure to build to allow starting. You may have to physically remove the solenoid to make sure this is intact. If you suspect that an injector is leaking, you can unscrew each injector line one at a time and install a ball bearing to block flow. When you get to the leaking injector, high-side fuel pressure will rise and the engine should start the other four cylinders. If you can’t find any internal or external leaks, you may just have a high-pressure pump that is not up to its task.
Dodge has a test for the high-pressure pump, assuming there are no leaks in the system. You start by unplugging the solenoid and checking fuel pressure while cranking. The engine will not start, but you should see about 800psi on your scan tool, or .8 volts on the high-pressure sensor signal wire. Your DMM’s display rate may be too slow to give you an accurate reading, so you might want to use a graphing multi-meter, or a lab oscilloscope to watch the voltage. You should see a steady signal above .9V. You may see it spike over 1.0V, but then drop down. The drop indicates that the pump cannot maintain pressure, or has a weak piston. This pressure drop will keep the engine from starting, and you’ll have to replace the high-pressure pump. We’ve noticed that they may start to become questionable at between 90,000 and 100,000 miles.
Of course, the glow plug system can cause a starting issue. On pre-2004 models, the glow plug controller is under the battery tray. It has three connections: a battery power cable, a six-pin connector with five wires (one for each glow plug), and a two-wire connector (one wire is ground, and the other is the signal from the fuel injection control unit for how long to energize the plugs). If you want to measure the resistance of the glow plugs, simply unplug the six-pin connector and check ohms between each pin on the connector and an engine or battery ground. You should see about 1 ohm. These are “pencil†type glow plugs, which heat up very quickly. The draw for each is about 20 amps. If you measure the current on all of them, you will normally see 75 to 100 amps depending on how cold the temperature is.
The signal from the fuel injection control unit to the glow plug controller starts off at 10 to 11 volts with the key on and the engine off. A “wait-to-start†light will come on in the instrument cluster. The CTS (Coolant Temperature Sensor) signal is used to determine how long the glow plugs are energized. The signal will then change to an inconsistent square wave. This is normal as the glow plugs are still pulsed on the first few seconds the engine is running to help with combustion on a cold engine. You can unplug the CTS to get maximum glow plug time from the controller — be aware that the electric cooling fan will come on as a fail-safe when you do this.
Starting problems can be tricky, but the more you know about the systems involved the more efficient you’ll be at troubleshooting. Sprinters are typically fleet vehicles, so any downtime is costing your customers money. A fast and accurate diagnosis will keep them happy with you. What more could you want?
by Kerry Jonsson
0 Comments