The E30 chassis was the first to sport four-wheel-drive here in America, and the original X5 (E53 chassis) was released in 2000 with a 4.4L V8 that produced 282 horsepower. In 2002, the 4.6L M62TU was added, which brought the horsepower up to 340, and this trend has continued.
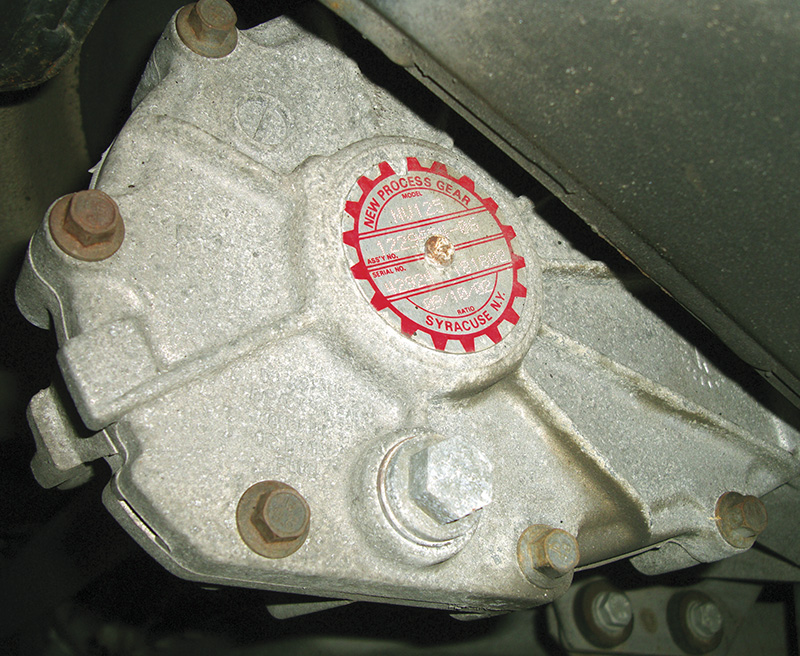
Sometimes a physical inspection is all you need to identify the transfer case model. Look at the top line and you can see this is a New Process NV125. This means it has a planetary gearset that is full-time 4WD, and a 32% front/68% rear torque split.
So, how is all this horsepower translated into acceleration without simply burning up the tires? The logical answer is through 4WD, which feature has grown in numbers at BMW. In 2001, the E46 chassis 325xi Sport wagon and the 325xi and 330xi sedans received the 4WD treatment. In 2004, the new xDrive system was introduced in the X3 (E83 chassis), and in 2006 the 5 series E60 (Sedan) and E61 (Wagon) chassis were offered with the xDrive system. That is quite an extensive offering of 4WD vehicles, and more have been added every production year. Of course, besides harnessing huge amounts of horsepower on pavement, this feature keeps you going in snow, or off-road, and improves weight distribution and stability control.
The X5 in particular was designed to handle well in on-road and off-road situations. There are many technological advancements that come standard on the X5. ABS (Antilock Braking System) and ASR (Anti-Slip Regulation) are standard, with DSC (Dynamic Stability Control) available as an option. All of these systems are specifically tailored to the E53 chassis. They also work with the newer BMW xDrive system. The combination of these various systems helps enhance traction and improve vehicle control. Now it’s our job to maintain their performance.
How does 4WD work?
The first transfer case used in 4WD BMWs was the New Process NV125 unit. The main component of the NV125 is the planetary gear set. This is what divides the torque to the front and rear differentials.
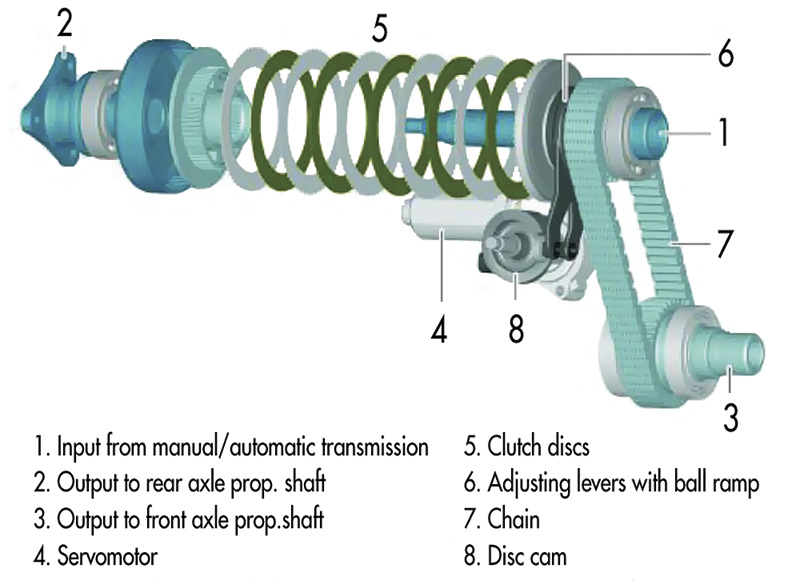
Here are the key components of the ATC transfer case. The input shaft directly drives the rear output shaft. The servo motor can engage or disengage the clutch that drives the front axle. This VTG system has a control unit with self-diagnostic capability.
Here’s how it works: The transmission output shaft drives the entire planetary carrier, which provides a 68% rear/32% front torque split between the drive shafts. An annulus gear driven by the carrier directs power to the rear drive shaft. Sun gears in the planetary gearset transmit torque to a drive chain that then drives the front axle drive shaft. This is a very strong design that is usually trouble-free. A key benefit is the ability to split torque under varying conditions thanks to the ADB (Automatic Differential Brake). When the DSC control unit senses a loss of traction based on input from the wheel speed sensors, the brakes are pulsed on the wheel that is spinning. This pulsed braking directs more torque to the other wheel on the same axle. If both wheels on the same axle indicate a loss of traction, the DSC module applies hydraulic pressure to both wheels so that torque flows only to the other axle. This original system is simple and sturdy.
In the ’04 model year a variation of the original 4WD system was introduced. It was called xDrive and included VTG. The new transfer case is the ATC 400 for the M54 engines and ATC 500 for the M62. This new system added a multiple-plate clutch instead of a planetary gearset to drive the front axle off of the permanently-connected rear drive shaft. An electric servo motor controls the application of the clutch pack to drive the front wheels.
When the clutch pack is completely disengaged, no torque is applied to the front wheels. With the clutch pack fully engaged, the torque is split evenly between both axles so they travel at the same speed. Under normal dry weather acceleration, more torque is directed towards the rear axle. If the rear axle loses traction, the servo motor progressively engages the clutch pack and directs more torque towards the front axle. The DSC system can still apply the brakes to any wheel that’s spinning and direct more torque to the opposite wheel. Remember that ABS and traction control systems are still active even when the DSC is shut off.
What Controls the Servo?
For newer vehicles, BMW engineered a Transfer Case Control Unit (VGSG) to control servo operation and installed it on the PT CAN bus. From the PT CAN, the VGSG monitors accelerator pedal position, engine load, wheel speed sensors, and other parameters. Under normal conditions torque is divided 40% to the front axle and 60% to the rear. When the VGSG unit senses wheel slip, it directs the servo motor to apply or release the transfer case clutch pack. Since it is a servo controlled clutch, the VSCG unit can adjust the torque division in very fine increments.
To monitor the position of the clutch pack the VGSG reads the signal from a hall-effect sensor built into the servo motor. To compensate for age and wear, the servo is cycled every time the ignition key is turned off. The VGSG unit monitors the amperage draw of the motor to calculate the full-open and full-closed position of the clutch packs With the stop points determined, the VGSG next looks at the Hall-effect signal. As the clutches wear, the number of Hall-effect signals increases. If a problem is detected during this process, the appropriate code will be set and a fail-safe mode may be activated.
Lubrication is Critical
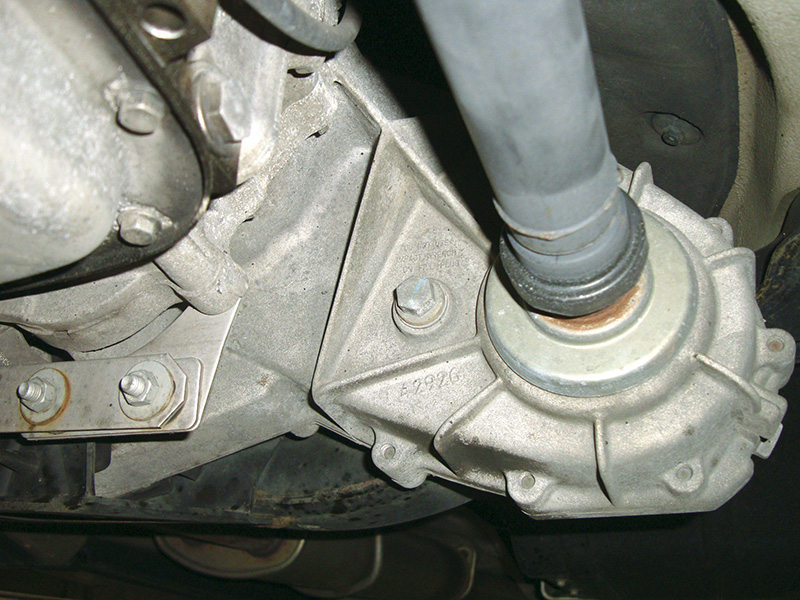
After draining the transfer case (the drain plug is under the ID tag in the first photograph), you can refill the system here. The choice of lubricant for the transfer case is critical. Be certain to use the specified oil, which is available from your BMW parts supplier.
In addition to controlling servo operation, the VGSG unit also monitors transfer case fluid condition and signals when the oil needs to be replaced. Since driving habits vary from one driver to another, there is no set service interval for the transfer case oil. The level should be visually checked every 30,000 miles. This can be done by removing the fill plug on the front side of the transfer case with the vehicle level, and reaching in with a finger to confirm that the fluid level is flush with the hole.
A code 54C6 in the VTC system indicates that the oil needs to be replaced. On the older NV124/5 transfer cases (w/o servo motor), Dexron III is the proper lubricant. The E46 chassis with 4WD has its own fluid, MTF-LT-1 and MTF-LT-2. On the E53 and E83 chassis with the xDrive transfer case (w/servo motor) produced before February of 2005, use a Shell Gear oil part #83 22 0 306 816. All models built after February of 2005, such as the E60, E61 and E90 chassis, use a proprietary BMW fluid TF0870 part #83 22 0 397 244. Part numbers do get updated, so the best way to ensure you are getting the correct fluid is to give the BMW dealer’s parts personnel the last eight digits of the VIN to properly identify the vehicle, and also the transfer case model, then purchase the oil.
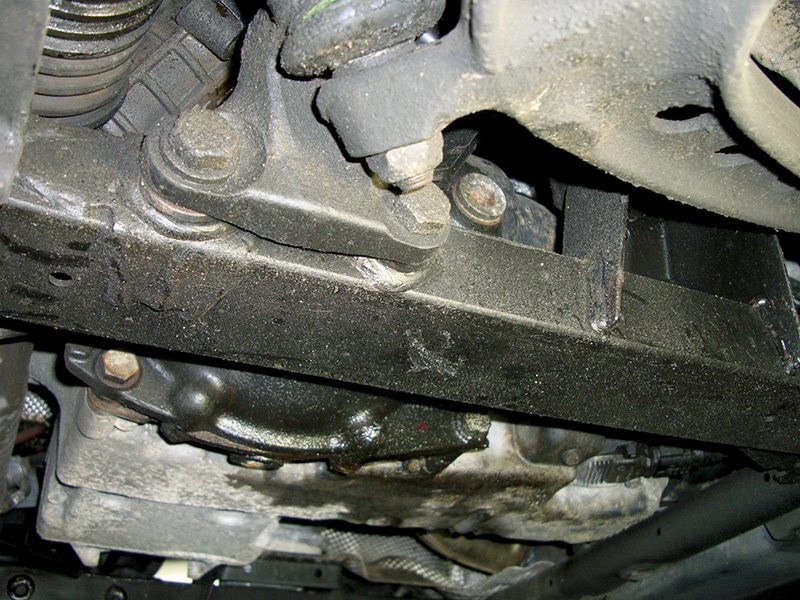
Notice the drain plug at the bottom of the front differential and the fill plug above it and just above the frame rail. On this E46 chassis with 4WD, you need SAF-XJ gear oil for the viscous lock-type differential. It has the necessary additives to prevent clutch chatter. Make sure to shake the bottle thoroughly, which will evenly distribute the additives before refilling.
And Now, the Rest of the Story
A 4WD system is more than just a transfer case. The front and rear drive shafts can cause vibration if they’re bent or out of balance. These drive shafts feed power to the front and rear differentials through CV joints that operate under very close tolerances. If you must remove a drive shaft, be careful not to allow the CV joint to come apart as it will be extremely difficult to reassemble without creating a driveline vibration.
The front and rear differentials should be inspected regularly. In particular, you should look for leaks, and check fluid level and bearing end play. To properly service one of these differentials, you must know if it is a limited-slip (rear differential), or a viscous-lock differential as used in the front axle of the E46. Just as you’ve done with domestic vehicles for decades, you can tell if you have a limited slip differential by spinning one wheel with the transmission in neutral. If the other tire on the same axle spins in the opposite direction, you have a conventional, or “open†differential. If it spins in the same direction, you have a limited-slip differential.
Limited-slip and viscous-lock differentials require the specific fluid SAF-XJ. You can use SAF-XO fluid in conventional differentials. Incidentally, since the introduction of synthetic gear oil, BMW now recommends that you replace any existing fluid with synthetic fluid for all models. Your BMW parts supplier can provide you with the correct fluids for your customers’ vehicles. And never use conventional gear oil in limited-slip or viscous-lock differentials since they will chatter in tight turns and eventually fail.
BMW has always used fully independent suspensions with drive axles and CV joints. During inspection, check wheel bearing end play, and CV joints for excessive play as well as seized or worn components. A ripped or torn boot will allow dirt into the inner and outer constant velocity joints and wear out the bearing prematurely. Many in the industry say that just eight hours of driving with a torn or broken CV joint boot will result in irreparable damage to the joint.
On the E46 chassis in particular, pay close attention to the front axles to assure that the CV joints are not binding. And it’s never a good idea to run the drivetrain while the vehicle is on a lift and the wheels are hanging, especially at speed. The angle between the CV joint and the axle shaft will be too great and can cause excessive wear and/or damage to the CV joint.
In Conclusion
Whether you are simply changing the fluid of a NV124/5 gear box, or pulling codes on the ATC 400/500, knowing what is involved in servicing and maintaining these 4WD systems can be simple and profitable. Your BMW parts supplier can help you achieve this by providing you with factory OEM parts and fluids designed specifically for every BMW you service.
0 Comments