When Karl Benz patented the first real car back in 1886, a three-wheeled conveyance he had built in stages over the previous couple of years, igniting the fuel/air mixture in an engine’s combustion chamber was a very difficult problem, one that had taxed engine inventors for a long time. Benz’s solution was to route a tube through the combustion chamber and sustain a flame inside that tube, a flame hot enough to light the fuel and air around the metal tube, just as the piston reached the top of each compression stroke. This hot-tube ignition worked like glowplugs on two-cycle model airplane engines, except that fuel constantly burned inside the hot tube to keep the temperature up. This hot tube had to stay hot from its internal flame; the very low-compression, slow turning engine didn’t leave enough residual heat in the chamber to dependably fire the fuel mixture the next time.
Did it work? Well, yes and no. Over two years had passed since he’d first driven around his shop in his Motorwagen, but most people regarded it as a silly toy and its inventor as a harmless ninny. Laws as well as the painstaking inventor’s sensible precautions meant not traveling on the ordinary horse roads, for fear of spooking the livestock and the locals. He just operated it near his shop experimentally, returning to tinker with it long hours every day.
This might have continued indefinitely, but early one day in August 1888 before Herr Benz was up and fiddling in his shop, Frau Bertha Benz, as practical as she was beautiful, took matters into her own hands and set out with her teen-aged boys, Richard and Eugen. They began the very first overland trip by car – without mentioning their purpose or itinerary to her husband, the reclusive inventor. The journey was from their home in Mannheim to her mother’s house in Pforzheim, about 100 kilometers distant, over horse-trails through mountains. Before Karl Benz was awake and puttering, they rolled Motorwagen No. 3 out the door and down the road so they could start the engine without alerting him to their plans. In the course of their numerous stops along the way, Frau Benz would telegraph her husband about their progress. All the odds were against them: No one had ever done such a thing in a horseless carriage before.
Nonetheless, the intrepid mother and her young sons set off anyway. For a cooling system, the one-cylinder engine just boiled off uncirculated water from its jacket as they drove along, but water was easy enough to collect from wells and streams. Fuel was a problem, though – gasoline hadn’t been invented yet: The car ran on ligroin, a kind of drycleaning fluid, but Herr Benz had never driven his Motorwagen far enough to calculate fuel consumption, and the travelers hadn’t thought about it at all until the tank first went dry. They were lucky: a local pharmacy sold ligroin by the flask. They could complete their trip provided they didn’t drive past any more pharmacies without stopping for more of the stuff.
The three-HP, 1886 Motorwagen didn’t have enough power or low enough gears to climb the steeper hills, so Frau Benz and her older son got out and pushed while the younger one steered. The brakes consisted of a leather strap rubbing against a small drum, and wore out quickly. Fortunately, resourceful German master shoemakers along the route helped out and did the first brake reline – on a machine they not only had never seen, but couldn’t even have imagined. The drive chains, like a bicycle’s, showed signs of rapid wear, but they held.
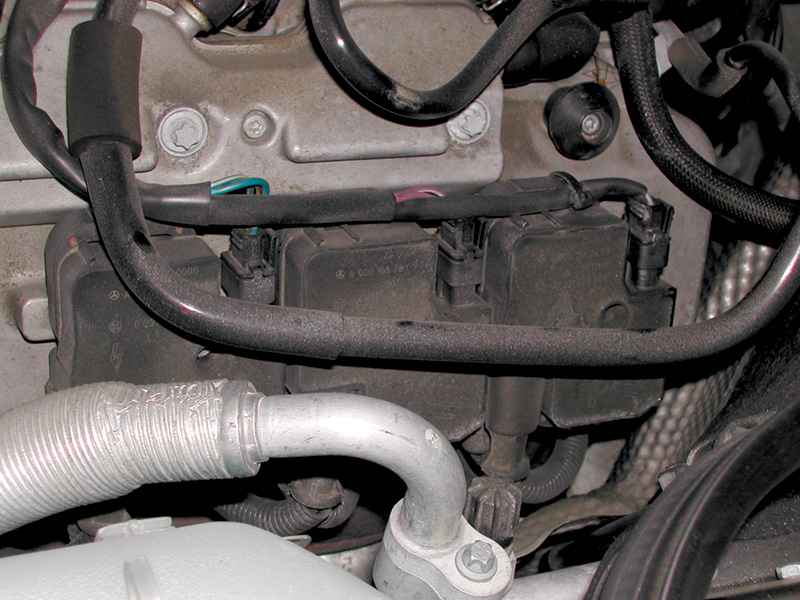
Over its long history building cars, Mercedes-Benz has used just about every ignition system there is. On current V6 engines, there are individual coils for each cylinder, with two spark plugs apiece, both fired by the same coil.
Late that same day they did arrive in Pforzheim. And, except when they ran short of ligroin and the fire went out, the hot-tube ignition system worked without fail the entire way. The reliability and usefulness of Karl Benz’ invention was now clear, thanks to his confident Frau Benz and his boys. On the other hand, the hot tube was itself fragile and occupied precious space in the combustion chamber, reducing what was available for valves and the piston. What’s more, there was no good way to control the point at which ignition occurred – it just lit off whenever the combination of compression, temperature and speed happened to cross the ‘fire-now’ threshold. On a slow, low-compression engine, that could and did work, at least as long as Frau Bertha’s and her boys’ luck held. But something better was needed.
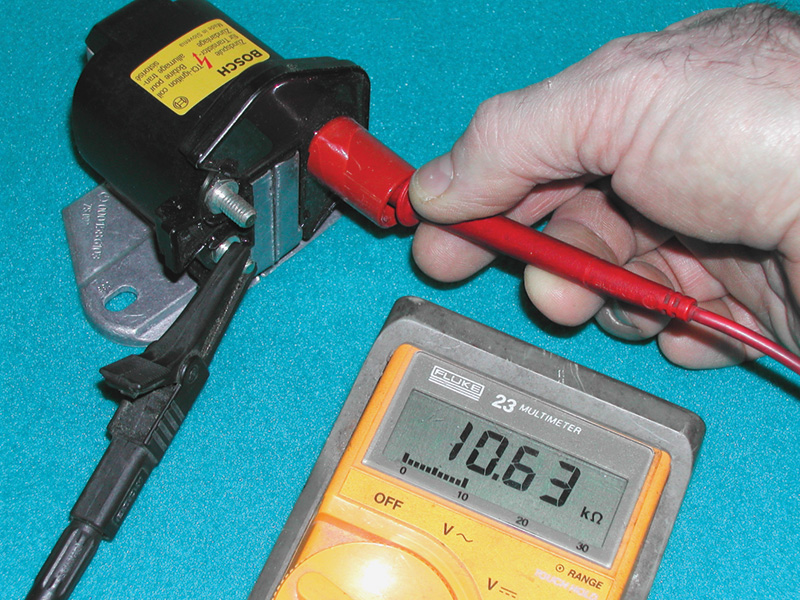
The circuit ending in the high voltage tower begins at the low voltage primary circuit positive post. Because of the relatively high resistance of the secondary circuit and the relatively low resistance of the primary, it doesnÃt actually matter which primary terminal you choose to measure to the secondary tower ñ another ohm or two out of several thousand is below the measurement threshold of most multimeters.
It’s been over 114 years since then, so we expect ignition systems to last longer than 100 kilometers, and they mostly do. Nonetheless, we still need something to reliably light the fuel/air flame to deliver the power to the crankshaft and the drivetrain, and that something has a much more precise job to do. That something, for the last 90 years or so since hot-tube ignition fell into disuse, is spark ignition from an ignition coil. A motorist is at fault if he or she runs out of fuel (ligroin, gasoline or whatever) or boils off all the water, but everyone expects the ignition system on any car will work better than that hot tube did for Frau Benz, and for much longer. Neither you nor I could start a Benz Motorwagen; if someone started it for us, we couldnÃt get it moving; if someone dropped it in gear, we couldn’t steer; once moving, we couldn’t stop it. She could and did all that. However, she was not only competent but also lucky. That’s not enough for dependable ignition, so we turn to electricity.
Bolts From the Blue…
…Sparks in the Dark
In the form of lightning, electricity can very easily start things burning. But lightning is not only dangerous but too intermittent and unpredictable to use. We don’t really need the kind of power that can explode a tree into toothpicks to set a mixture of fuel and air burning, though. A very tiny lightning bolt in the combustion chamber – a spark in the dark – will do the trick just nicely.
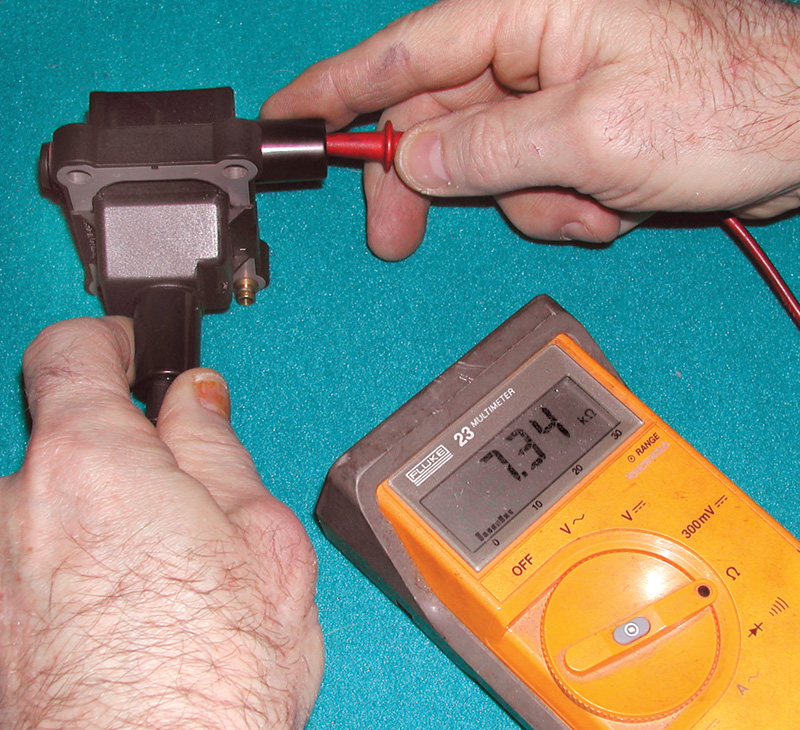
A coil that fires two plugs has a secondary circuit electrically independent of the primary circuit, except in the sense that when the coilÃs magnetic field collapses, it generates high voltage in both. You should measure from one high voltage tower to the other, comparing the result with your specifications book. There should be no continuity between either secondary tower terminal and either primary terminal or ground.
The modern ignition coil generates a short, perfectly timed tiny bolt of lightning. The coil works by converting electric current to magnetism, and then by converting that magnetism it just built back into electricity. While charging and discharging the coil, building and then collapsing the magnetic field, is fast, the collapse is much faster than the buildup, as you can see from any ignition primary circuit pattern.
The conversion back to electricity trades current for voltage, much higher voltage – enough to jump the electrodes of the spark plug and start the combustion burn, even under the difficult conditions in the chamber at the top of the compression stroke. An ignition coil thus functions as a very-high voltage transformer. It’s a little peculiar to speak of a transformer in the absence of alternating current, but the ignition coil uses pulsed current, which is just as good for transforming voltage.
Ordinarily, we speak of two kinds of ignition coil, those that fire one plug at a time and those that fire two. As we’ll see, they are electrically similar. The standard, one-plug coil either fires one plug at a time through a rotor and distributor, eventually firing all the engine’s plugs in sequence; or else the engine has a dedicated coil for each plug, a coil-on-plug system. Both primary and secondary circuits begin from battery positive and end at engine ground. For most one-plug ignition coils, you can measure resistance through each of the circuits and compare them with what you find in your specification book. The primary will always have much lower resistance than the secondary, and neither will have continuity to the coil housing or ground. To protect the system electronics from induced voltage spikes, many coil-on-plug systems use protective diodes that, incidentally, can prevent you from measuring resistance on one or the other circuit.
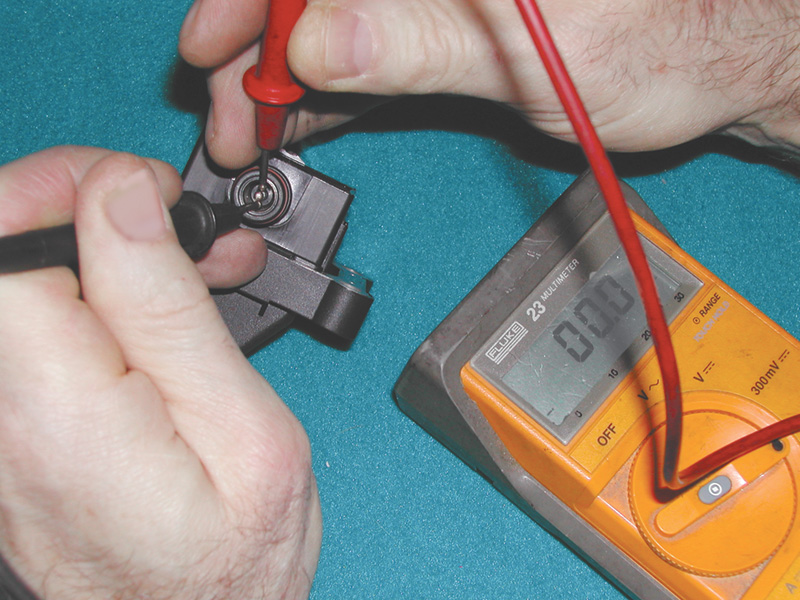
Both primary circuits end at the same connector on this Mercedes-Benz coil. Measure from the center terminal to the side, being careful not to let the probes touch (or youÃll get a false reading). As with the secondary circuit, there should be no continuity from either of these terminals and either ground or the other (the high voltage) side of the coil.
A two-plug (“waste-spark,†“dual-spark,†“twin-sparkâ€) coil fires two plugs almost simultaneously, one at each end of its secondary circuit, firing in opposite polarity. Its primary and secondary circuits are electrically separate: The primary goes from battery positive, through the coil windings to ground via the pulsed ignition module driver. The secondary goes from one plug’s center electrode to another’s, passing through the coil along the way. The two plugs could be in the same or different cylinders: If the same, the dual spark serves to promote more complete burning of the fuel/air mixture; if different, one of the sparks occurs in a cylinder at the top of its exhaust stroke, the so-called “waste-spark.†Aircraft piston engines use a different kind of dual-spark, two completely independent magneto ignition systems, but such redundancy isn’t needed in cars.
You can make similar resistance measurements for the two-plug coil as for the one-plug: There should be continuity (but different resistance) through the primary and secondary circuits individually and no continuity to ground. But unlike the one-plug coil, there should be no continuity between primary and secondary circuits.
The double spark is not as strange as it initially seems. In fact, a conventional distributor-type ignition system requires its coil to jump two spark gaps, also — one between the plug electrodes and the other between the distributor electrode and the rotor tip. A fast oscilloscope can show each gap-jump on its trace. Both those sparks have the same electrical polarity, of course. It does take more electrical energy to jump two sparkplug gaps than one, though, so you’ll typically find lower primary resistance on two-plug coils. The lower resistance allows more current to flow.
Double Windings around a Magnet
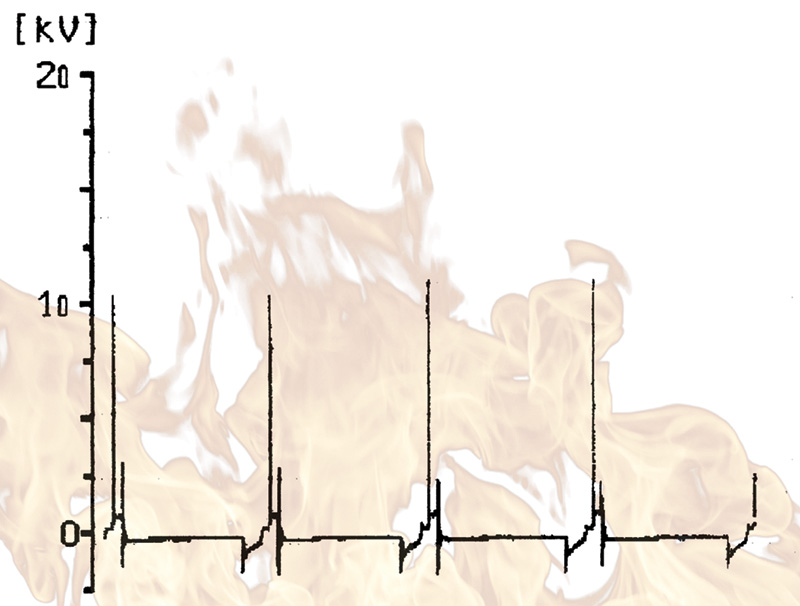
For each type ignition coil, a secondary pattern shows the high spark line followed by a burn line and the normal oscillations.
Each ignition coil consists of two circuits of fine wire wrapped around a ferrous (thus electromagnetizable) core. The primary circuit conducts ordinary electrical system voltage through several hundred wraps of wire to form an electromagnet and build an electric field around the iron coil. This side of a coil circuit is called the primary circuit; it comes on first. When the ignition coil turns on, current starts to flow through the primary circuit windings.
On earlier vehicles, this occurred when the distributor’s contact points closed, closing the ignition primary circuit. On modern vehicles, this occurs when the computer or the ignition module, working with information conveyed from the crankshaft and/or camshaft position sensors, signals the coil driver to close the primary circuit.
When a coil turns on, less current flows than you’d calculate from a stationary resistance measurement through the primary circuit. Instead, the current only gradually increases – ‘ramps up’ – because the lines of force in the growing electromagnetic field cut through or transect those same primary circuit windings as it grows. Move a wire through a magnetic field, and current flows in the wire. Grow a magnetic field through a coil of wire, and current also flows in the wire.
But this tries to induce a current in the opposite direction from the circuit, a phenomenon called reluctance, almost a kind of dynamic resistance. As the magnetic field nears full strength, the lines of force become stationary and no longer transect the wires, so the current reaches its maximum. On contact-point ignition, a spark occurs not at the low-current extreme when the points close and begin to saturate the coil, but when they open, when the primary circuit carries maximum amps. To be sure, there is additional induced current (and voltage) even in the ignition primary circuit as the magnetic field collapses. Contact-point ignition required a condenser to absorb this voltage surge; modern ignition systems can use Zener and other protective diodes that can withstand the spike.
Once the primary current stops, whether the contacts open in an old car or the transistor shuts off in a modern one, nothing holds the magnetic field up. It collapses almost instantaneously, and as it does, those same lines of magnetic force again transect the coil’s wire windings in the opposite direction. In this stage, however, the excitement happens in the secondary windings. Because there are so many more of them, the voltage that forms is much higher than the voltage the primary circuit used to build the magnetic field in the first place.
One end of the secondary circuit in the one-plug ignition coil connects the battery-positive side of the primary circuit, through the thousands of windings of superthin secondary coil wrapping to the spark plug center electrode. The voltage-multiplication ratio of the coil, like that of any transformer, corresponds to the ratio of windings between the primary and secondary coils. Several hundred windings of primary circuit at twelve volts requires many thousands of windings of hair-thin secondary to achieve the 40,000 or more volts needed to ignite a lean fuel/air mixture under any and all throttle and engine speed conditions.
But it’s not merely high voltage a coil must reach to generate a spark that can dependably light a compressed fuel/air mixture. It’s also the duration of the spark, what we see in the extent of the spark line of a secondary ignition pattern. That energy comes from the additional energy stored in the magnetic field when the primary circuit builds it up before the spark.
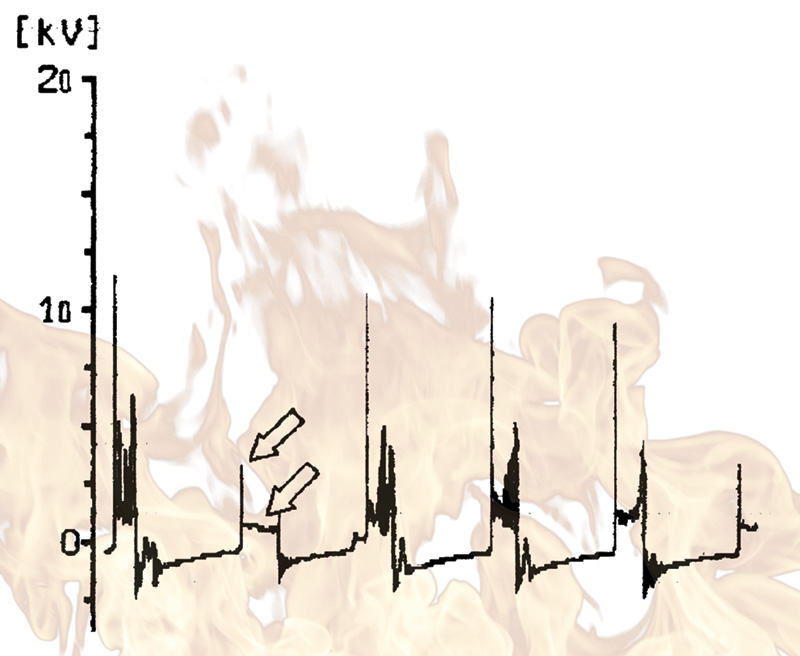
When there is a problem, it will show up in the pattern. Here a spark plug gap that is too small on one plug reduces the spark line and (the energy has to appear some way) extends the burn time.
Just as, if you’re building a campfire, you have to hold the flame of the match to the tinder for a certain amount of time to get it to light, the spark in the combustion chamber has to do more than just jump across the electrode gap. The spark has to continue its electrical discharge across the gap for some time, long enough for the gasoline to start burning, for the combustion fireball to start growing. The amount of time required depends on engine temperature, fuel mixture, engine speed, throttle position, engine load and other factors.
The voltage necessary to jump the electrode gap in the first place also varies, with similar factors. Before the spark jumps, the electrical voltage – that is, the electrons massing on one side of the gap –must ionize the fuel/air mixture in the gap. What that means is that the massed electrons drive electrons out of the gas mixture in the gap and the metal surface opposite, because electrical charges repel one another mutually. With the electrons driven out of the gap and the other side prepared for the spark to jump, that gas is now ionized, that is, richer in positive charge. When the combination of voltage and resistance hits the combination determined by Ohm’s Law, the spark appears across the gap. Notice, it doesn’t ‘jump across.’ The spark appears all the way across the gap simultaneously; it’s a circuit phenomenon, not an electron-projectile.
Once it starts, it takes less energy to sustain the spark. We can see this in secondary discharge patterns. The spark line reaches relatively high voltage for a very brief time; the burn line runs at much lower voltage for a much longer period. There is a total amount of energy stored in the form of the electromagnetic field around the coil’s core. When that collapses, it can take either the form of voltage – the spike that ionizes and jumps the gap – or current, duration – the burn line. There’s only so much energy, and it can only take those two forms.
But you see what that means: If there is a problem anywhere in the circuit, like a high resistance secondary cable or bad insulation somewhere on the high voltage circuit, energy that should have gone into the spark must overcome the problem (raising the voltage to overpower resistance, as long as there’s voltage to spare), or it leaks away to ground, frustrating the combustion burn. Ignition engineers try to maintain confidence the coil can always produce the required spark by designing them to be capable of much hotter and longer sparks than should really be required. But eventually conditions in the combustion chamber present greater demands; supply and delivery connections deteriorate, and wiring loses its integrity; finally the coil itself starts to lose capacity.
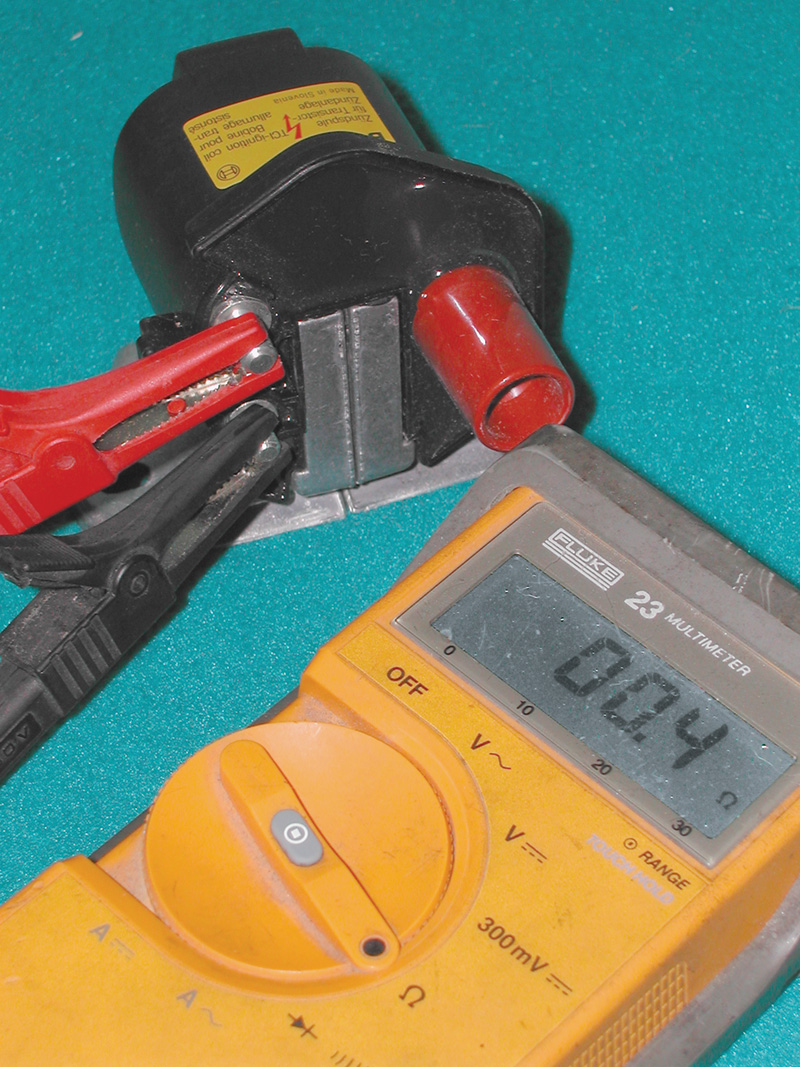
A conventional ignition coil, the type found on most Mercedes-Benz vehicles, uses primary and secondary circuits that share a connection at the battery-positive terminal. The primary circuit tested here builds an electromagnetic field around the iron core of the coil. Resistance through this and all other primary circuits is relatively low.
We’ll just consider the factors internal to the coil here. The major reason why an ignition coil can’t be an infinite-life component is the insulation. If you wrap a thin wire round and round as in both the primary and secondary circuits, the voltage difference between one winding and the next won’t be very high at all. If the primary circuit had a mere 100 windings at 12 volts, that’s only about 1/8 th of a volt per wiring turn. You don’t need the stoutest insulation in the world to hold back 1/8 th of a volt. Traditional ignition coils just ran the thin copper wire through varnish before wrapping it into a coil. Today’s insulation is much better than old varnish, but there’s not much room for it to be much thicker. Eventually, heat will allow successive coil windings to touch at various points. This leads to minor internal shorts. There are probably a few in every brand new coil, but they don’t effectively reduce the number of windings significantly until insulation breakdown becomes more widespread. Of course, as these mini-shorts increase in number, the coil’s resistance goes down, its current draw goes up, and the internal heat increases, further damaging the insulation around the wires.
This tolerance for some insulation breakdown is one of the reasons why ignition coils typically have a range of acceptable resistance. Of course, modern primary circuits have such low resistance anyway that you can’t measure them accurately with an ordinary ohmmeter – you’d have to rig up an elaborate Wheatstone Bridge measurement, and it would be simpler to just replace any suspect coil.
But the importance of the insulation also points to the importance of the quality of a replacement part, if it turns out one is needed. The ignition systems on these cars are quite durable, even though eventually coils and other components will have to be replaced. When you find one with a coil that has ended its useful life, take a look at the odometer to see how long that one was on the job. Given the improvements since that first car trip, get one that can rack up similar odometer numbers. Factoring in the 114 years since then, take the example of Bertha Benz and her Motorwagen’s hot-tube ignition straight from the manufacturer. Get the best parts you can.
0 Comments