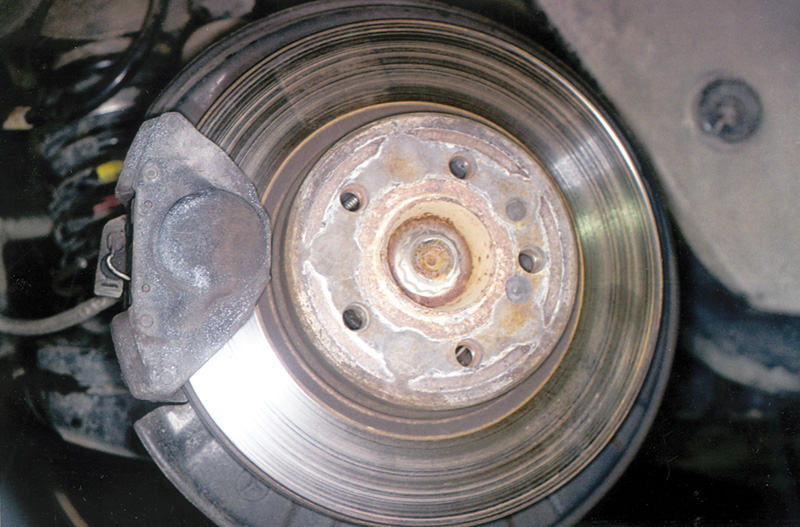
The brake disk is the machine that converts vehicle movement to heat and gets rid of the heat to the air. Large brakes not only provide large friction surfaces for more deceleration-force, but also dissipate the heat better.
There’s a good chance, if you cut your tool-teeth working on domestic or Asian cars, the first thing that astonished you about a Mercedes-Benz was the sheer size of the brakes for the size of the car. The main reason they’re so large is the Autobahn, the German superhighway system on which drivers choose their own cruise speed according to their vehicle’s capacity and their own skills. Typically those vehicles and skills are very good, so average driving speeds on many stretches of the road are between 85 and 110 mph in dry weather. But many vehicles hold sustained cruise much higher than that.
Mercedes-Benz voluntarily limits their vehicles’ top speed to 155 mph (250 kph), though many of their cars could drive considerably faster, absent the maximum speed governor. If you’ve ever driven a car at that ground-covering clip for any distance, you’ll recall you were hardly clogging your lane at the time. It requires sustained attention to other traffic and the road in a way we don’t experience here. It requires a road quality, a pavement engineering and construction economically incompatible with our multi-thousand-mile North American distances. But in a medium-sized country like Germany, that speed over a couple of hours means door-to-door car travel is about as fast as airline travel between most cities when you add to the flight time the ground connections at each end. The speed also presumes you have a well-engineered highway, first-quality tires and powerful brakes. Evidently they manage: The Autobahns are safer than our Interstates, factoring in all the variables.
More to the point of brake systems, such high cruise speeds mean a much higher level of work for the deceleration machinery. Momentum goes up with the power of two, with the square of the speed. So stopping from 150 mph takes four times the distance and transfers four times as much heat as stopping the same car on the same surface under the same conditions from 75 mph – no sluggish pace, itself. If you’ve ever measured brake disk temperature after a 75-mph stop (Don’t test one with your fingers! And don’t ask me how I know that!), you can imagine what it is after a stop from a much higher speed. The decelerating Autobahn cruiser blows invisible plumes of brake-heated air through its wheels.
Momentum by the Power of Two
Have you ever driven in the mountains where there were runaway truck escape runs built at the end of steep stretches? These escape lanes provide some relatively safe way to stop a heavily laden, downhill truck if its brake pedal falls through the floor. There are two dynamic features of the escape lanes: First, they are ramrod-straight with no turns at all because a runaway truck isn’t likely to turn very responsively. Second, the construction actively slows the truck, by soft sand, by a sequence of berms and by a steep uphill angle. I’ve only seen those lanes used a few times, and it’s clear from the deep furrow in the sand and gravel, the excitement level was more than enough for that truck driver’s day. While the experience surely beat running off the road anywhere else, it must certainly have been nothing like a gentle kiss from the tooth fairy.
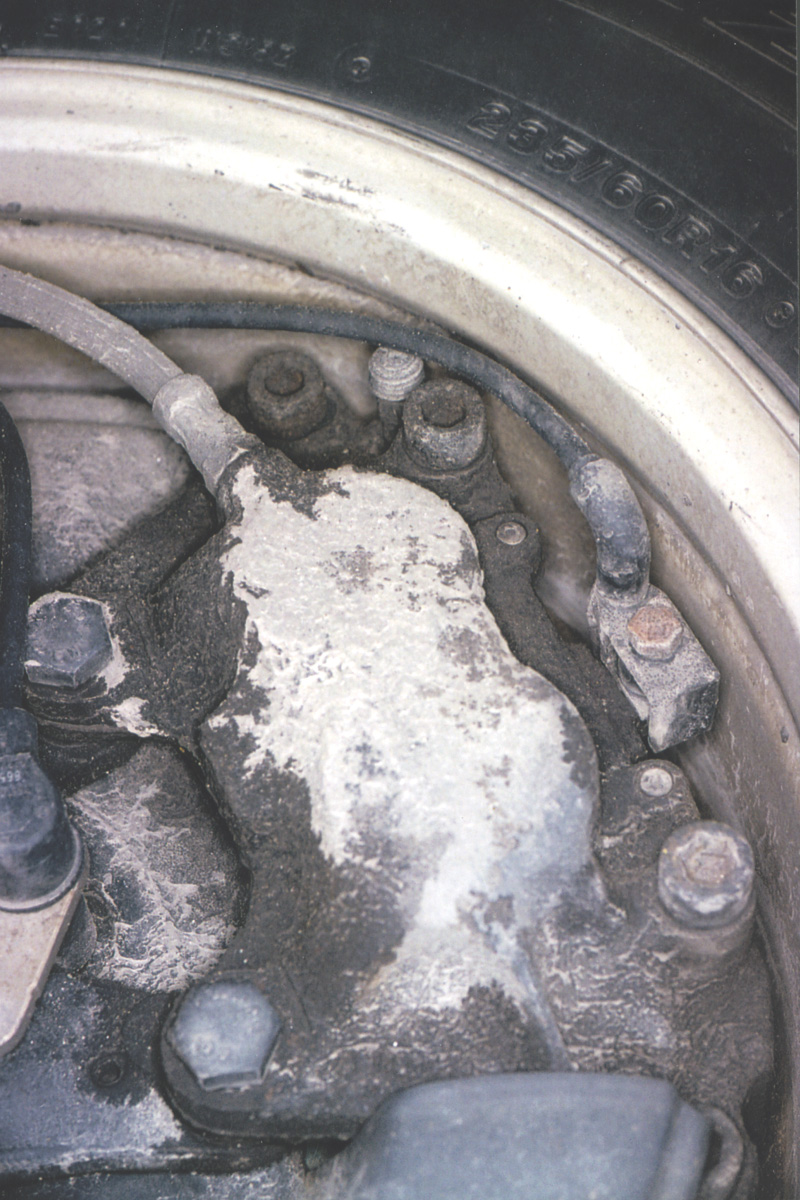
The bulk of the deceleration in any car comes from the front brakes. This front caliper has the pad wear sensor on the outside of the disk and the wheelspeed sensor toward the hub. While road salt crusts the casting, good materials in the original part means there is little or no rust developing.
The indications of dispersed kinetic energy were literally widespread. The halted truck blasted tons of sand for many yards in all directions, bashing through and propelling three of the huge, transverse sand berms. All the energy of the truck’s runaway, gravity-sped descent down the mountain went into accelerating the sand and dirt forward, upward and outward. The soft surface let the truck sink to its frame, plowing with its wheels and bumper all the way. Whether the truck was repairable afterward, I don’t know. It surely took many days’ work with earthmoving equipment to put the runaway lane back into the emergency deceleration business. But the driver walked away, however shaken. That’s because the runaway truck lane kept directional stability constant and provided sacrificial mass to absorb the energy.
Cars don’t weigh nearly as much as tractor-trailers, but they have to disperse the heat of deceleration, too. People don’t always realize the power-equivalent of their brakes, so let’s look at it from the other end to get a more accurate picture. Suppose if you hold a 300-horsepower engine at wide-open-throttle for 30 seconds, you’ll accelerate a 4000-pound car to 100 mph. I’m pulling these numbers out of my hat, of course, to keep the math simple, but they’re reasonably close to the real world. Notice (except for a bit of air drag), it would take an equivalent of the same 300 horsepower to bring the same car to a stop in the same 30 seconds. In fact, however, brakes on every model car can vastly outperform the engine: Stand on the brakes and stand on the throttle, and you’ll just overheat the engine and cook the transmission. But you won’t move an inch.
Actually, it would be a rare car that would, given good pavement and tires, take even ten seconds to stop from 100 mph. Mercedes-Benz braking systems, designed to provide sustained braking up to the traction limit even on Alpine Autobahns, have an even higher power equivalent. I don’t have 100-to-zero performance figures for Mercedes-Benz cars, but feel entirely confident that any Benz built in the last 50 years can handily beat that ten-second figure. Newer ones could easily out-brake earlier. Chances are, Benz car brakes can put out well over 1500 horsepower-equivalent as long as the pavement and the tires cooperate. This is probably true of many manufacturers’ current vehicles as well.
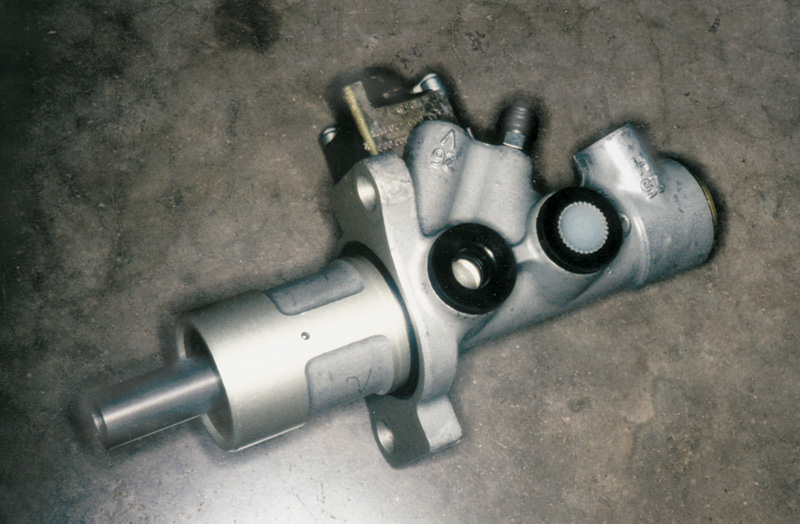
Later model vehicles have more complex master cylinders to deal with the more complex brake systems. The extra bleed screw allows removal of all the air in the master cylinder itself should it require replacement or repair. The electronics control the pressure differential between the two hydraulic circuits.
It isn’t merely that the brakes convert the vehicle’s movement into heat by forcing the friction surfaces of the brakes together. You have to get rid of that heat, too. The braking system must air-cool the brakes so they can keep absorbing more, newly developed heat. Without such heat transfer, the brakes would just heat up until either the components got so hot the pedal fades to the floor or the parts just melted.
The fundamental job of the brake system is to convert the structured kinetic energy, the momentum, of the moving car to the scattered, chaotic kinetic energy, the heat, of the surrounding air, just as the runaway lane converts the truck’s downhill roll into flying sand and gravel. The brake system also holds the vehicle stopped at a standstill sometimes, but that does not involve the conversion of one type of energy into another. If hybrid vehicles ever become commonplace, they will perhaps succeed in recovering much of this energy through regenerative braking – drawing from the inertia of deceleration.
Braking consists of forcing friction surfaces, pads and disks together with a pressure corresponding to a multiple of the force the driver puts on the brake pedal. Since every car’s braking capacity far exceeds its traction even under ideal circumstances, many current vehicles and all Mercedes-Benz include antilock brakes. The phrase antilock brakes is somewhat misleading: this is not really a system to optimize braking but a system to retain steering under any circumstances that might arise. The thinking is quite simple: If you were to lose controls of the vehicle one at a time, the last one you’d want to lose is steering – up to that point, you could always aim for something soft or cheap.
There has been a progression of antilock systems on Mercedes-Benz vehicles, integrated into other traction-control systems like ASD, ASR, 4MATIC and so on, systems we’ll treat in upcoming articles, systems you can get extensive information about from Mercedes-Benz Technical Information. The earliest, ABS alone, used three wheelspeed sensors, one on each front wheel and the third in the differential. The control unit and its connected hydraulics pulse the front wheels individually but the back brakes together. The reasoning is that in any situation requiring ABS activation, the rear brakes contribute minimally to the deceleration but very significantly to the directional control (lose rear traction and you spin), so the system can pulse them together to correspond to the wheel with less traction. This also insures retention of rear traction, or else there is no steering even with good traction at the front because the vehicle loses directional control.
Wheelspeed sensors are electromagnetic pulse generators and seldom go bad unless there is physical damage either to the sensor, to its connecting harness or to the toothed ring machined into the hub, generating the signal pulses in the sensor’s coils. Conduct a thorough visual inspection and check the sensor for continuity and for resistance within specs. Be sure to rotate the wheel through a complete turn so you can look closely at all the spaces between the teeth. Road grit and debris often includes metallic particles, and should one lodge between the sensor teeth, that can disrupt the magnetic field. The sensor expects equidistant teeth, so a gap filled with the metal particle just looks like one long tooth to the control unit. That signal looks just like what you’d get with a wheel in the first stage of lockup, so the system may pulse the brake pressure, or on later self-diagnostic versions it may flag the wheelspeed sensor circuit as flawed.
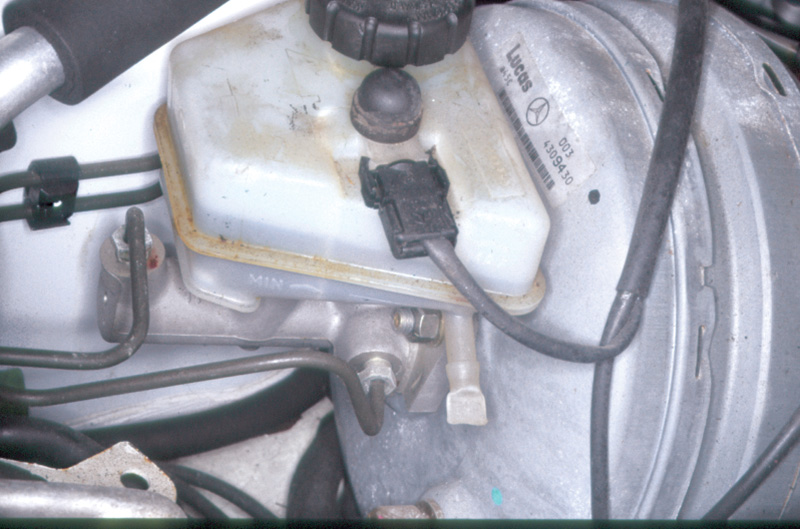
When flushing brake fluid, first draw all the fluid out of the reservoir itself and replace it with new. Some shops prefer using a pressure bleeder; some prefer either gravity or vacuum bleeding procedures. In any case, follow the bleed sequence for the vehicle you have on your rack.
The control units for ABS are among the most reliable, seldom requiring replacement except after physical damage, in an accident for instance. As you know, should the ABS system toggle itself off for a sensor or actuator fault, or should it merely fail for some other reason, the car still has full power braking that can stop the car with full force. What’s lost with ABS off is the capacity to selectively pulse individual brakes to retain steering and directional control simultaneously during full braking force.
One of the service problems entailed by ABS, however, is the increased complexity of the work when bleeding the brakes to flush the brake system of old brake fluid during regular replacements, or when bleeding the air out after some work that required opening a hydraulic circuit. If the procedure does not proceed in the correct sequence, there can be old fluid left in part of the system or even air trapped if the system was open. Just as on any brake system, air will not eventually circulate through and out; the system is hydraulically closed. If there is air in the system, making the pedal spongy and the braking consequently uncertain, it will stay there until you or someone else bleeds it out.
Because of the additional components on an ABS system, regular brake fluid flushes, at least every other year, are critical to the function of the equipment. Since brake fluid is hygroscopic, it will draw moisture out of the air and get contaminated, even by just sitting with the master cylinder reservoir cap off too long on a humid day. The moisture won’t be confined to the master cylinder reservoir but will travel quickly throughout the hydraulic system.
This can have two bad effects, either one potentially disastrous: Just a three percent contamination of brake fluid can lower its boiling temperature down to about three hundred degrees instead of the five to six hundred right out of the can. Those Autobahn brakes can develop a higher temperature than that, particularly on a long, downhill grade. Should the brake fluid boil, it changes from a fixed-volume hydraulic fluid to a variable-volume pneumatic gas. Then the pedal falls to the floor, and the brakes cease their decelerative work. Your customer could develop a sudden interest in finding one of those runaway truck lanes.
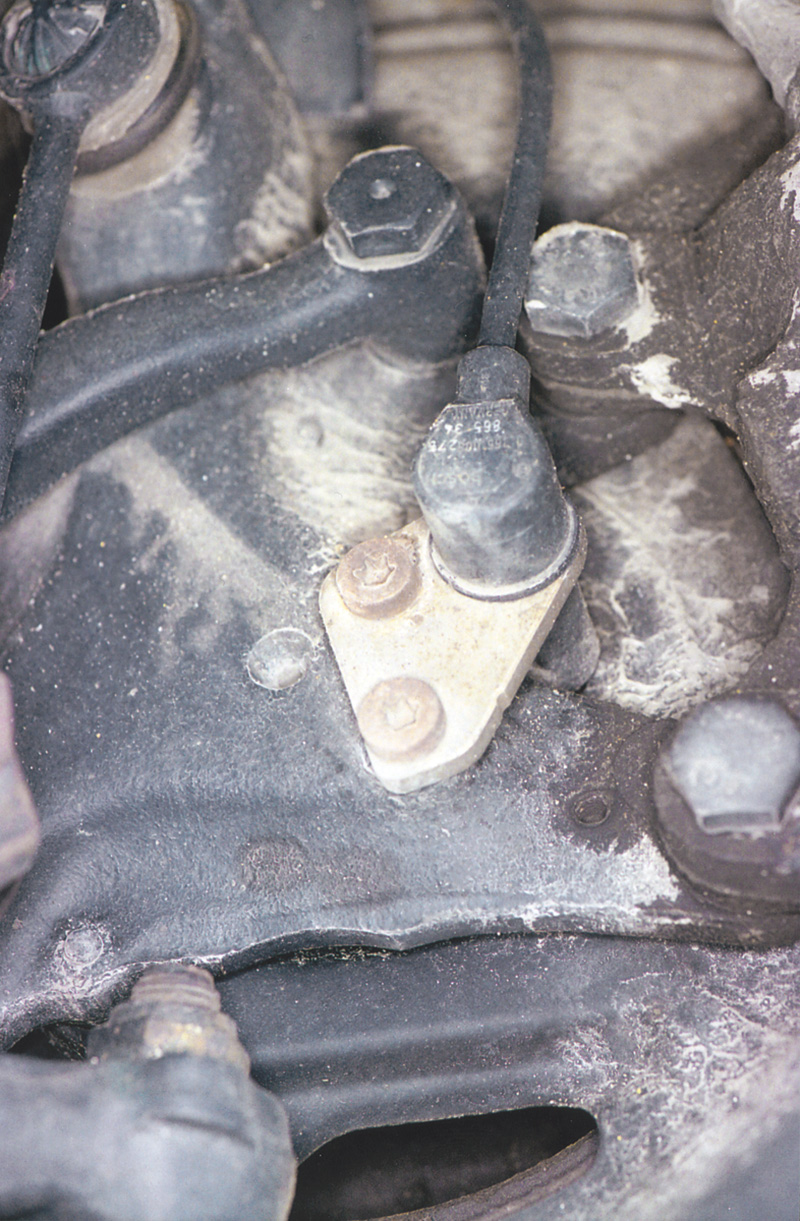
Wheelspeed sensors generate signals for the ABS system as well as whatever other traction control systems may be on the vehicle. These are electric induction coils wound around magnets, placed adjacent to toothed gearwheels machined into the hub or axle. As the wheel turns, the sensor reports its speed to the control unit, which then operates the traction controls, as circumstances require.
The second effect takes longer but could be more insidious still. Rust. The moisture-contaminated brake fluid contains can start the formation of rust anywhere inside the hydraulic circuit. It doesn’t have to be in the master cylinder. Just as, if you accidentally put salt in your coffee instead of sugar, you can taste it at the top of the cup even if you don’t stir, moisture can travel through the brake fluid – to a distant wheel cylinder, to a pressure reservoir, to an ABS pump. None of this area is a good place for abrasive particles that could lodge in valves or anywhere else, locking components internally. No such rust damage would be inexpensive to find and fix; sometimes it could be dangerous.
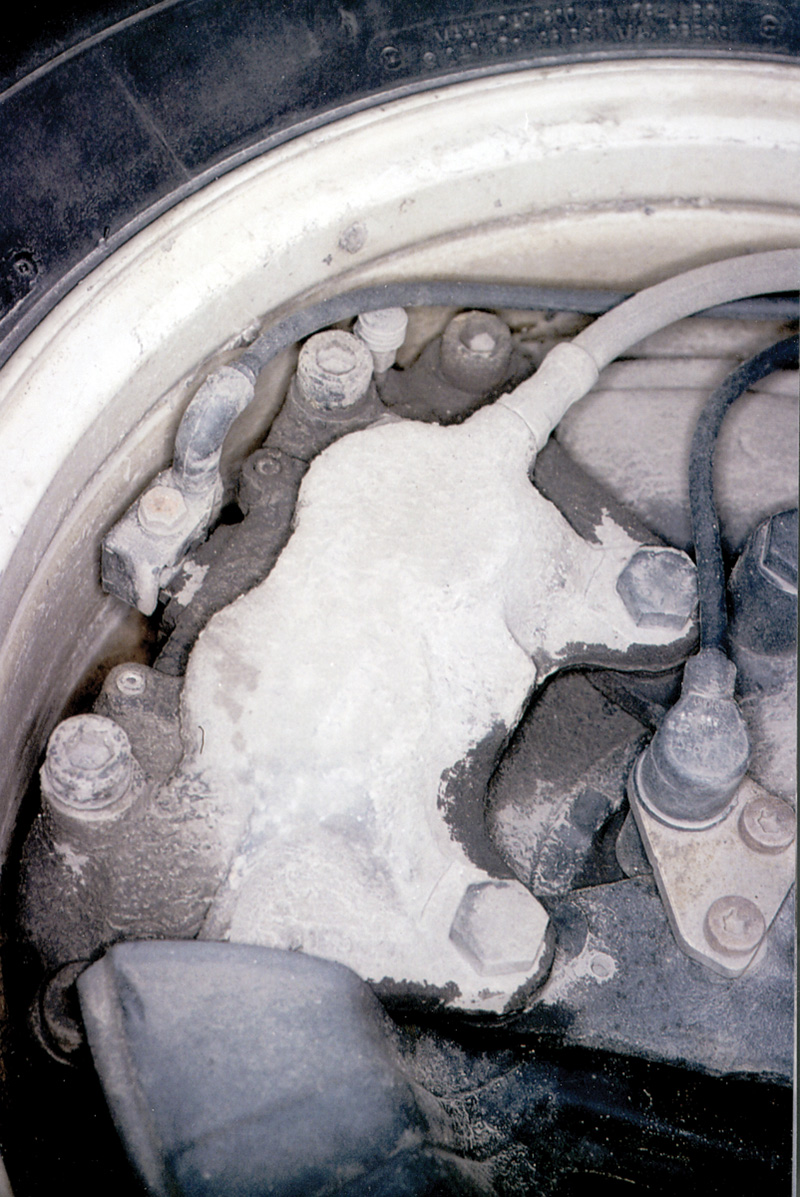
Rear brakes don’t have as much to do with the deceleration of most cars because of the ‘weight-shift’ as a car slows. On larger vehicles, though, there is often enough weight on the rear that it still has a significant role to play reducing speed. At the same time, of course, ABS and the other traction controls must insure the rear wheels always retain traction.
For each vehicle, there is a specific bleeding procedure. There are more models of Mercedes-Benz on the road than there are pages in this magazine, so we won’t try to outline them each, but here’s the way most work. First, vacuum the old brake fluid out of the master cylinder, getting as much of the old out as possible. If there is any visible debris or discoloration in the bottom, use some fresh fluid as a flush to stir the stuff off the bottom and get it with your vacuum hose. Then fill the reservoir to the full mark. There is just no point in bleeding the brakes without emptying the master cylinder reservoir first, because all of the brake fluid in the system shares the contamination very quickly; you’d just dilute the new fluid right away.
Often there are tiny bubbles entrained in the new brake fluid just after you pour it in. Let them float to the surface and pop. The last thing you want from your brake flush is the insertion of air into a hydraulic system that didn’t have any to begin with.
If your job is just an ordinary brake fluid flush and there is no reason to suppose there’s air in the system anywhere, you can go on to bleed the brakes through the calipers. For most models, the sequence is right-rear, left-rear, right-front and left-front, working from farthest away from the master cylinder to closest. However, if you’ve opened the system anywhere to replace a brake line, caliper or whatever, bleed that circuit first, so no air from it can sneak back into the rest of the system. Then do a complete system flush starting at the right-rear.
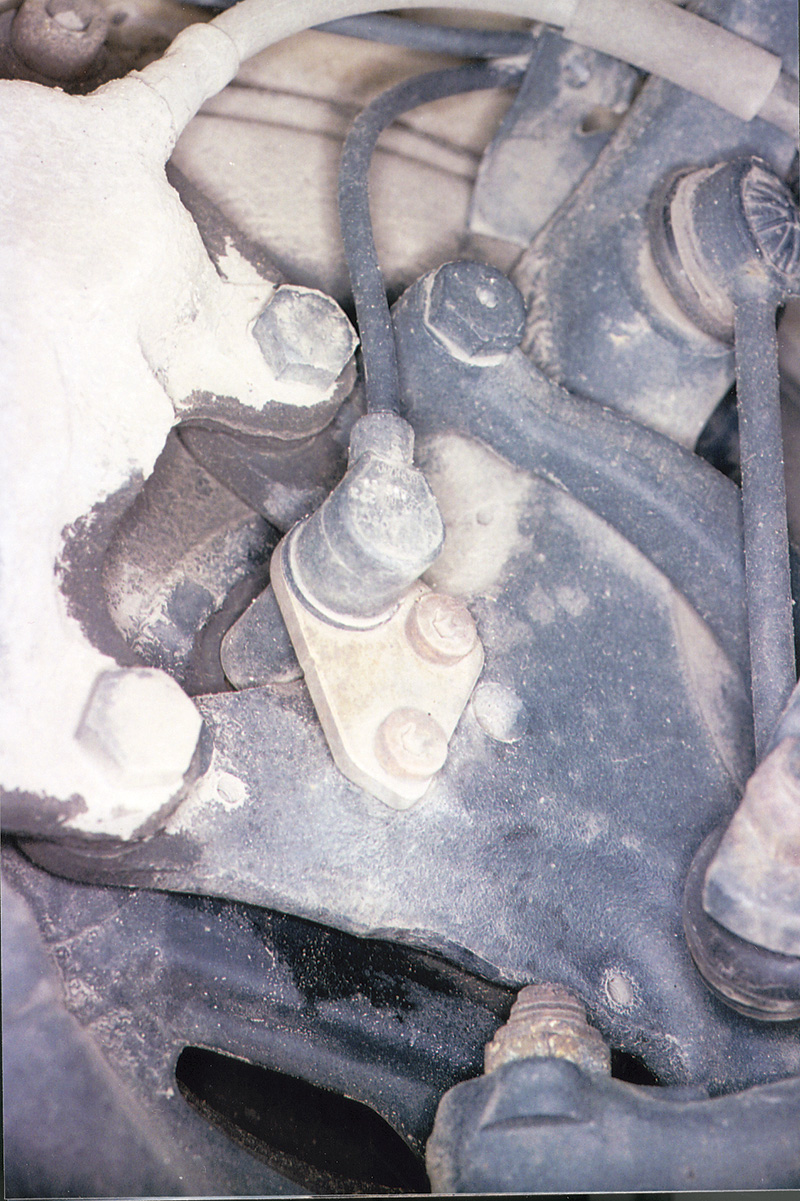
Wheelspeed sensors are electromagnetic generators internally. On most Mercedes-Benz vehicles, the sensors are at each wheel, monitoring the rotation of a toothed wheel on the hub. On some earlier models, however, look for the sensor at the nose of the differential, monitoring the average speed of both rear wheels rather than each of them individually. The sensor works the same way in any case.
For many Mercedes-Benz master cylinders, there is a bleeder on the master itself to allow bleeding it after replacement or repair without risking pumping air through the whole system, perhaps entrapping the air in some particularly recalcitrant backwater of the hydraulics. Many later model cars use a master cylinder with an electric valve that opens or closes to regulate the pressure differential between the separate hydraulic circuits; some have pushrod-position or motion sensors. Be sure to follow the instructions that come with the cylinder to get all the air out of the master cylinder before flushing the rest. Several other components on the more complex brake hydraulic systems also include individual bleeders, used when those components themselves get replaced.
Brake Noise
We talked about the runaway truck escape lanes. There is another connection between powerful brakes and trucks: noise. Sometimes under hard braking even the most elegant of cars will produce brake noise that can alarm the driver and passengers. If the noise is a metal-on-metal grinding or clanking, there is a serious problem, but most brake noise is merely a high-frequency resonance between the brake pads and the rotors. For the most part, this is merely an acoustic nuisance and not a matter of brake safety. The car can still be driven; there is no emergency.
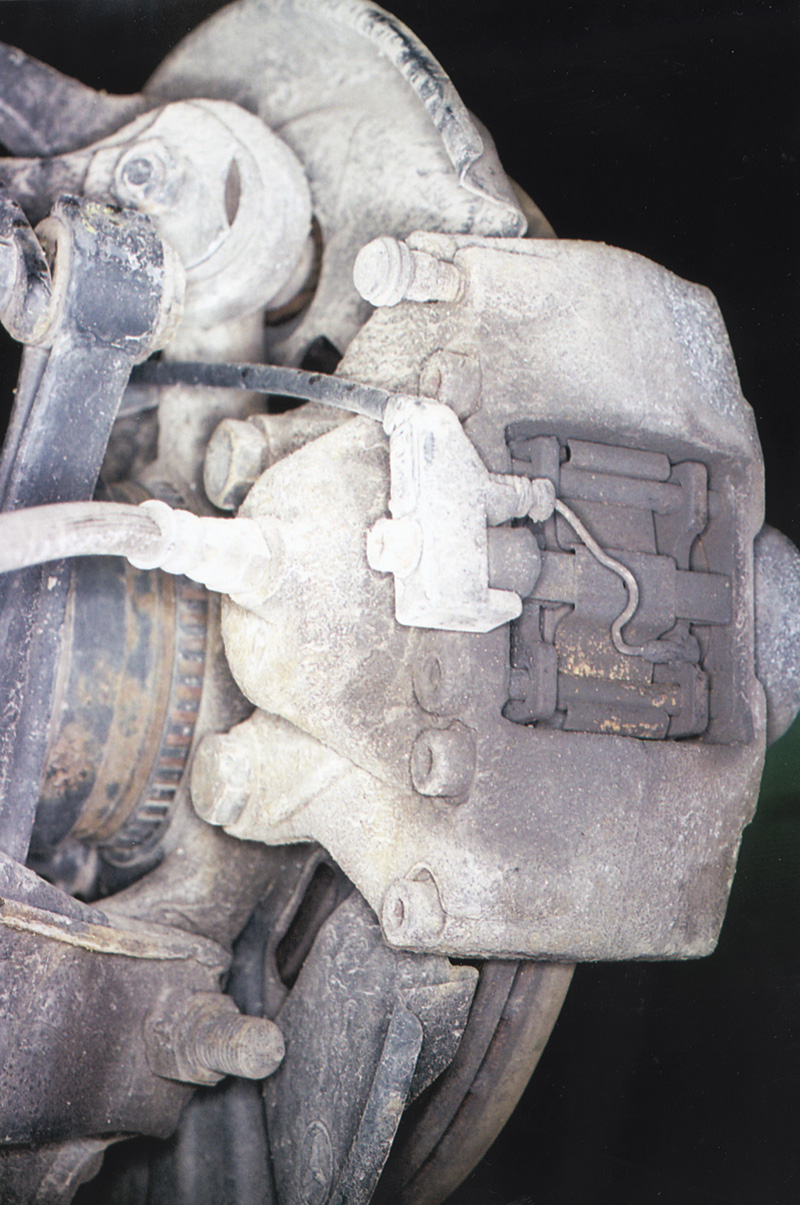
The rear caliper on this 140 shows the wear sensors on the brake pads. When the pads wear to the point of replacement, the driver should see a caution light informing him or her of it.
That being said, a major reason why brakes make such noises is the use of substandard brake friction materials or failure to replace hardware, such as antirattle springs and pins. The difference in cost between the parts is not worth the difficulties caused by the noise the cheaper parts cause.
A similar story can be told about disks. If you’ve worked on Mercedes-Benz brakes for some time, you already know disk warping is very rare because the disks and hubs are so robust. Except under unusual conditions or abuse (like constant left-foot braking), the disks last a long time. Rather than machining them or resurfacing them, the carmaker recommends their replacement if the surface of the brake disk has worn beyond normal limits or beyond normal surface conditions.
Brake Fluid
Everyone knows to change the engine oil with a certain regularity, but the importance of changing the brake fluid is not as widely understood. Brake fluid is, of course, an oil, but a very particular kind of oil. Its most important properties are: It must not cause corrosion in the internal parts of the system, and it must not sustain significant change of hydraulic properties because of heat. The heat of braking a vehicle from a high-cruise speed can be quite high, particularly when descending a long mountain grade.
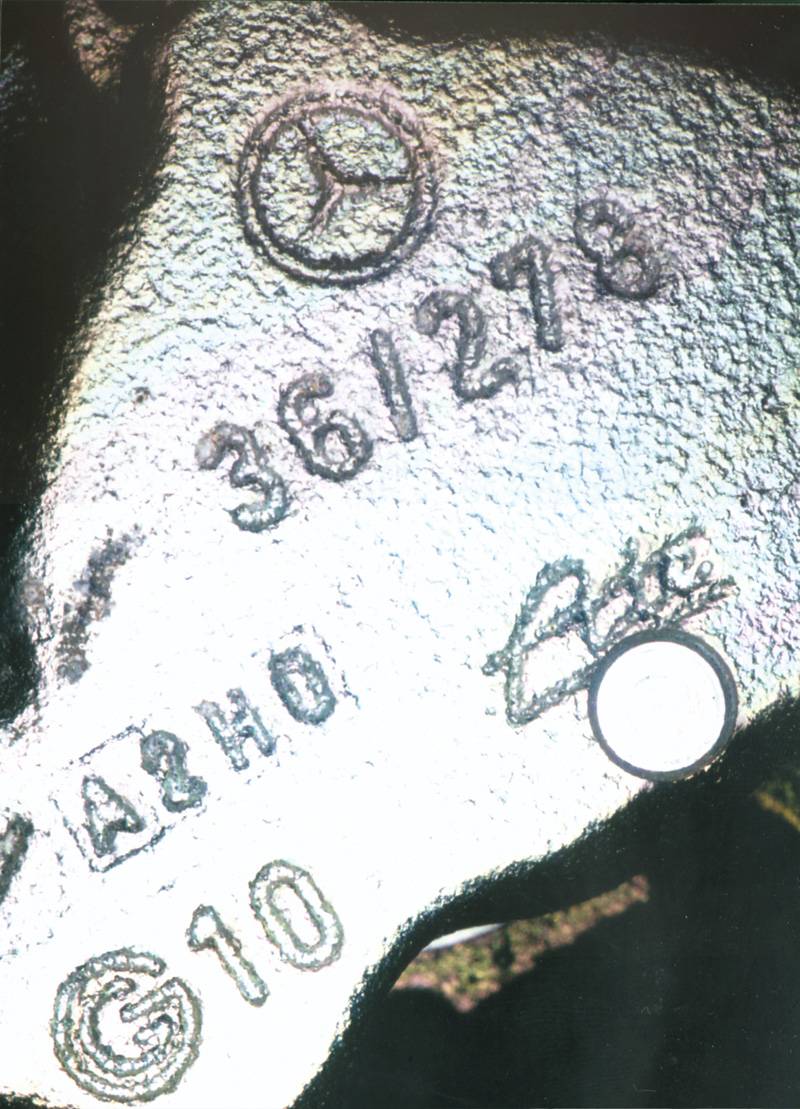
Brake components require not only precise metallurgy for the casting but precise machining to insure all of the mounting surfaces and hydraulic internals fit the car precisely. Ordinarily it is good practice to replace, say, wheel calipers or disks in axle-pairs to keep the braking performance exactly equal from side to side.
Brake fluid is hygroscopic. That means it will draw water from any source it can – from the air, from any local water, from your skin. That property of drawing water from things means it will not allow moisture to puddle anywhere in the system: It will draw it into the oil and disperse it throughout the system. Up to a point, this prevents rust.
But there is a fly in the brake fluid’s hygroscopic ointment. As the oil draws moisture from anywhere in the hydraulic system and disperses it throughout, that lowers the boiling point of the brake fluid oil.
Right out of a new bottle, the boiling point is well over 500 degrees. There is little chance of any braking emergency that will continue long enough over a long enough downhill stretch to raise the brake fluid to that temperature, no matter what. Even under the highest extremes of racing, with the brake disks glowing bright red under repeated forceful deceleration, the brake fluid itself will hardly come anywhere close to that. The brake pads function as thermal insulators, and the thermal mass of the metal in the steering and rear wheel knuckles as well as in the calipers prevents such a high temperature.
Let some time pass, however, and we have a different story. Regardless of how well the brake fluid is protected from the outside environment by steel and plastic, a certain amount of moisture will creep in. This need not be in the form of beads of moisture condensing on the master cylinder reservoir cap. Individual molecules of water can wind their way up the reservoir cap threads or creep around caliper piston dust boots and seals. You need only an amazingly small amount of seeped and penetrated moisture to poison the batch: When a mere three percent of the brake fluid is absorbed moisture (and an open container could draw that much out of a humid atmosphere in no time), the boiling point of the brake fluid falls to about 300 degrees F.
That seems pretty hot compared to the general atmospheric temperatures in which we drive, but it is much lower than the brake fluid’s original 500+ degree boiling point. Now we have a real problem, a serious problem. Maybe a problem that could result in someone’s injury or death.
If the brake fluid does boil, that’s not just a matter of temperature. When it boils, it changes from liquid to gas. And in a hydraulic system, this is a catastrophic change because a fluid retains a constant high pressure everywhere in the system regardless of temperature because it is incompressible. But when it boils, it’s no longer a fluid but a gas. A gas, however, compresses as easily as air.
In a brake hydraulic system, that’s bad, very bad. It’s as bad as a total loss of hydraulic pressure by a broken line or other complete fluid leak. The brake pedal can fall to the floor under the driver’s panicked foot. The usual hydraulic pressure, multiplied by the ratio of master cylinder piston area against the calipers’ total, adding the multiplication (about three times) the vacuum brake booster adds to the system, falls to almost nothing. In an ordinary brake system, with undiluted brake fluid, the hydraulic pressure can reach well over a thousand psi. – nearly to Diesel injection pressure levels. In a system with boiling from heat, that pressure can fall to three or four psi. That won’t have any useful effect on the brakes; it won’t force the shoes against the disks enough to slow the car. When the brake fluid boils, for all practical purposes you have no brakes. That’s true whatever kind of car you’re driving, whether it has ABS or not.
There’s no way to prevent this other than flushing the brake fluid at regular intervals, usually every two years. The general principle is to pressurize the system from the master cylinder and bleed the old fluid and any air out from the individual wheel calipers.
But ABS, as well as ASR and several other traction-retention systems complicate this procedure. You can’t just pump up the pressure and release the bleeder any more, as though you were working on a car from the 1970’s. There are several additional steps and a specific wheel-by-wheel sequence to follow. Do it another way, and you’ve decided you know more about the system than the engineers who invented it. The best strategy is to follow the procedures set forth by the vehicle manufacturer in Untertuerkheim.
Tire TractionAntilock braking is a steering-preservation system. No matter what the driver may do with the brake pedal (if the system works as designed), there will always be enough traction to steer the vehicle. Here’s how the system works: Every wheel’s tirepatch has a certain amount of traction whenever it’s touching the pavement. That amount of traction may be large or small depending on the type of tire and pavement, the weight on the wheel, the weather conditions and so on. We can visualize this traction as a line extending from the center of the treadpatch; the longer the line, the greater the traction. You can change the traction by changing the conditions – driving onto a wet surface or changing the weight on the wheel by turning or stopping. But if the load you put on the treadpatch by any combination of steering and braking exceeds the traction, the tire will slip. If the brakes are applied, the wheel will rapidly start to lock up. We think of tires as either having traction or not, and we suppose this distinction must reflect the difference between the treadpatch stationary with respect to the pavement or sliding. But the traction story is not that simple. The wheel can affect the direction and speed of the vehicle up to the limit of its traction. Go beyond that, let the treadpatch slide along the ground to any significant degree, and you lose almost all traction. Most tiremakers build their tires so the extremes of traction announce themselves in the undoubted forms of louder noise and more alarming slipping, gradually but quickly evident to the driver. Then he or she knows that turning the wheel sharper or standing on the brakes harder will just disconnect the car from the road. They can do this because the rubber compound from which the business surface of the tire is compounded is relatively soft and flexible (there are really three ‘business surfaces’ when you count the areas where the beads grip the wheel rim). The tread rubber can flex and twist, so in a turn it typically starts to slip toward the rear edge of the moving treadpatch. When the surface slipping becomes large enough, the treadpatch and the pavement part company along their whole length. All-out racing tires, however, often sacrifice that warning feedback range to get a few more foot-pounds of traction at the limit. Racers will gamble their skills against the risk to get just a bit closer to the edge of traction than their competitors. When hard-rubber racing tires do let go, of course, the car has all the traction and directional stability of a hard-rubber hockey puck. Antilock brakes serve to preserve each wheel’s traction up to the point when the laws of physics preclude any more. ABS works by reducing braking force when that force would be enough to push the traction over the perimeter described by the tip of that imaginary arrow we spoke of earlier. ASR and other traction control systems do the same thing by reducing delivered engine torque when that force would exceed the available traction. |
0 Comments