The names Mercedes-Benz and Diesel fall together so naturally it’s a surprise to learn the company’s first Diesel car, the four-cylinder 260 D, was not built until 1936, comparatively late in the firm’s history, after they’d built gasoline-fueled automobiles for 50 years. The 260 D found favor as a taxicab, as Mercedes-Benz Diesels have throughout Europe since. Earlier both the Benz and the Daimler companies (they merged in the late 1920’s) had separately produced Diesel engines for trucks, for agricultural and marine use; but they had not previously applied the Diesel advantages of durability and fuel economy to passenger cars.
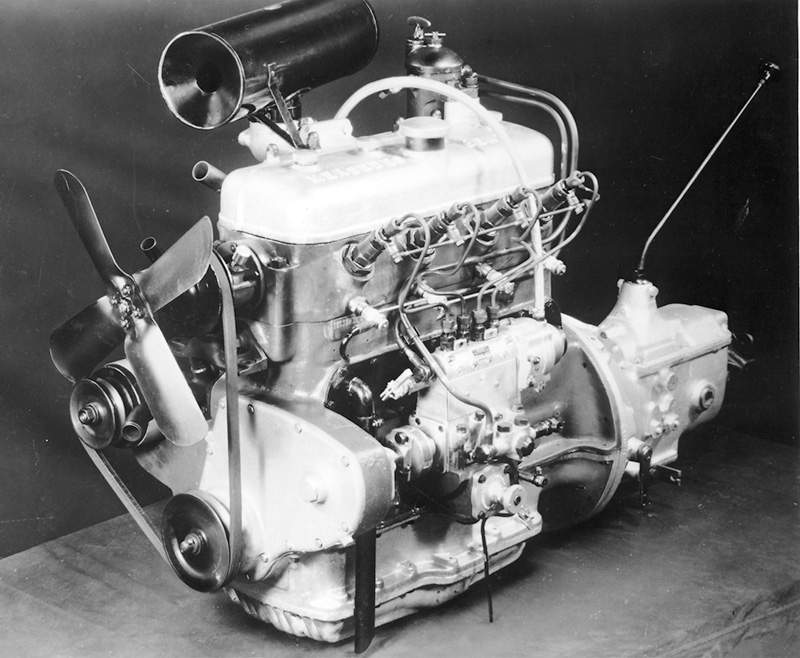
The 260 D engine, though a cam-in-block, is strikingly similar to later Mercedes-Benz prechamber Diesels. It’s also much like the Diesel engine they built for many years for refrigeration units, lacking only a four-gallon oilpan.
Rudolph Diesel, a French engineer of German ancestry, patented his first compression-ignition engine in 1892. Employed as industrial and marine powerplants for the first 15 years or so, Diesel’s engines worked pumping water from coalmines, generating municipal electricity and chugging around Hamburg harbor in tugboats. At the turn of that century, there was as yet no industry-standard technology to get a fuel mixture burning dependably in the combustion chamber for every power stroke. A few engines used newfangled, then-high-tech ignition magnetos, or coils, vibrators and spark plugs, but most others used such contraptions as glowplugs or gas-heated tubes to light the fire. Every engine designer sought a reliable ignition system.
When you’re trying to achieve something everyone else finds very difficult, sometimes the best solution is to do something very different, something everyone else is not trying to do, something that avoids that recalcitrant problem altogether. Diesel avoided the ignition problem by basic gas physics: If you rapidly compress a gas, it gets hotter just as rapidly, roughly in proportion to the degree you compress it. Compress the air enough, and its temperature exceeds the flashpoint of your fuel. When the injector sprays oil into the combustion chamber as finely atomized droplets, each one immediately starts burning, raising the cylinder pressure and temperature still more. So Diesel didn’t need an ignition system. Incidentally, he didn’t need a carburetor, either.
What he and later designers of compression-ignition engines did need was a hydraulic pump and injector system capable of delivering the fuel in exactly the right quantity and at exactly the right moment, maintaining that fine atomization and spray pattern regardless of engine speed or load.
Benz Prechamber Diesels
Prosper L’Orange, a German engineer of French ancestry (evidently in the Nineteenth Century European boundaries moved around more frequently than European families did), was chief designer of the prechamber Diesel engines used in early Benz tractor and truck engines and in Mercedes-Benz car engines until recently. A prechamber design makes it easier to machine each combustion chamber to identical size (since the cylinder head can be dead flat) and lends itself to somewhat higher engine speeds, allowing use of common or similar transmissions and differentials for vehicles available with either Diesel or gasoline engines. Note that the Mercedes-Benz prechamber uses shaped-top pistons and multiple exit holes from the prechamber through which the mixture of burning fuel oil and air enter the combustion chamber proper. This is different from a Ricardo- or swirl-prechamber, which uses a single larger aperture and works by spinning the air in the chamber before and during the fuel injection. The Mercedes-Benz prechamber uses diffuser pin and the multiple flame holes to turbulate the combustion.
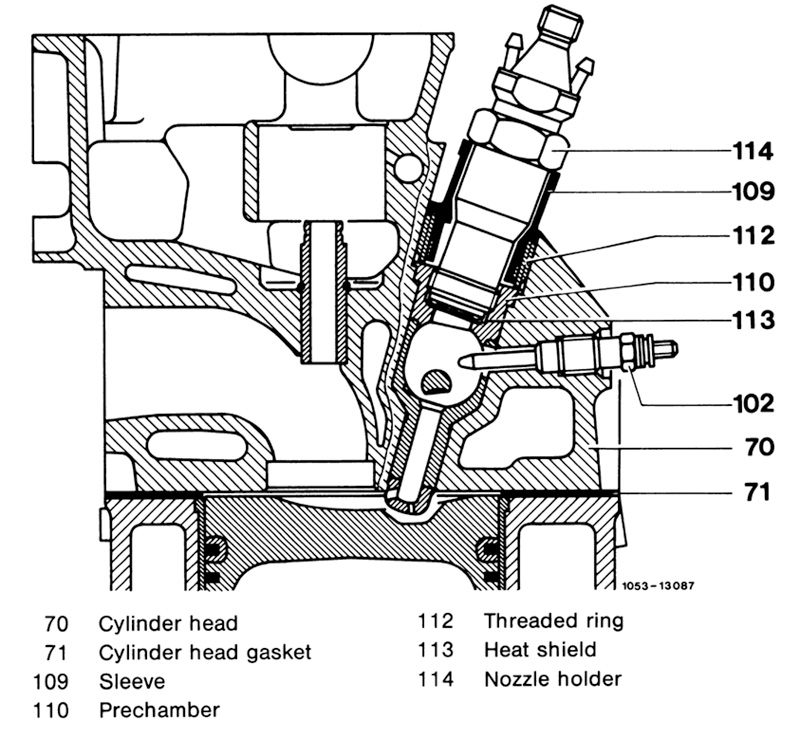
The prechamber Diesel houses injector, glowplug and diffuser pin all in a small chamber above the cylinder. Once combustion begins, the burning air-fuel mixture blows through apertures at the bottom of the prechamber into the main cylinder area.
Mercedes-Benz car Diesels up to the late 1990’s use the prechamber design. The injector nozzle and the business end of the glowplug share a small chamber above the main combustion chamber and connected to it through a series of metering orifices. In most Mercedes-Benz automotive Diesels, the third inhabitant of the prechamber is a diffuser pin, straddling the prechamber, deflecting and scattering the injected fuel spray. The diffuser pin also helps vaporize the fuel once the engine is running at operating temperature, using residual heat from the previous power strokes of the engine.
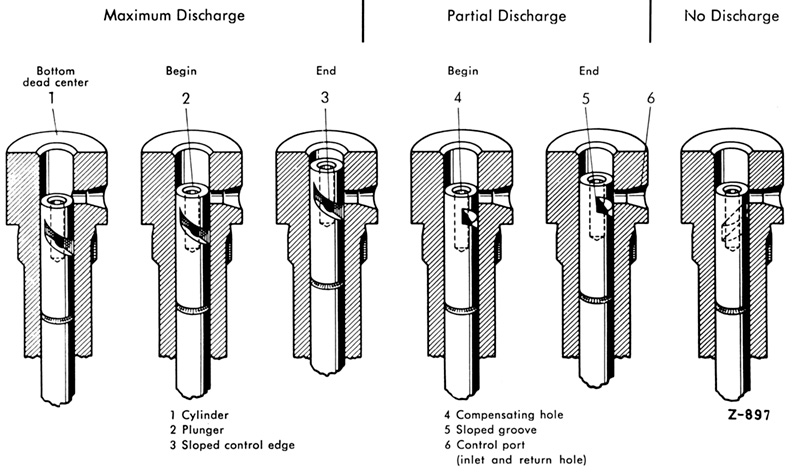
The plungers make a full stroke for each rotation of the pump camshaft, but the amount of fuel injected depends on their rotational position, as determined by the toothed control rod.
On rare occasions, a diffuser pin breaks loose in the prechamber, usually hammering away at the prechamber walls, too. This is a fairly hard problem to diagnose the first time because it’s not something you suspect. But there is a characteristic noise the engine makes with this problem, and once you hear it you’ll know a loose diffuser pin if you ever hear another one. You remove the prechamber — no need to pull the head unless there’s other damage — to replace the pin.
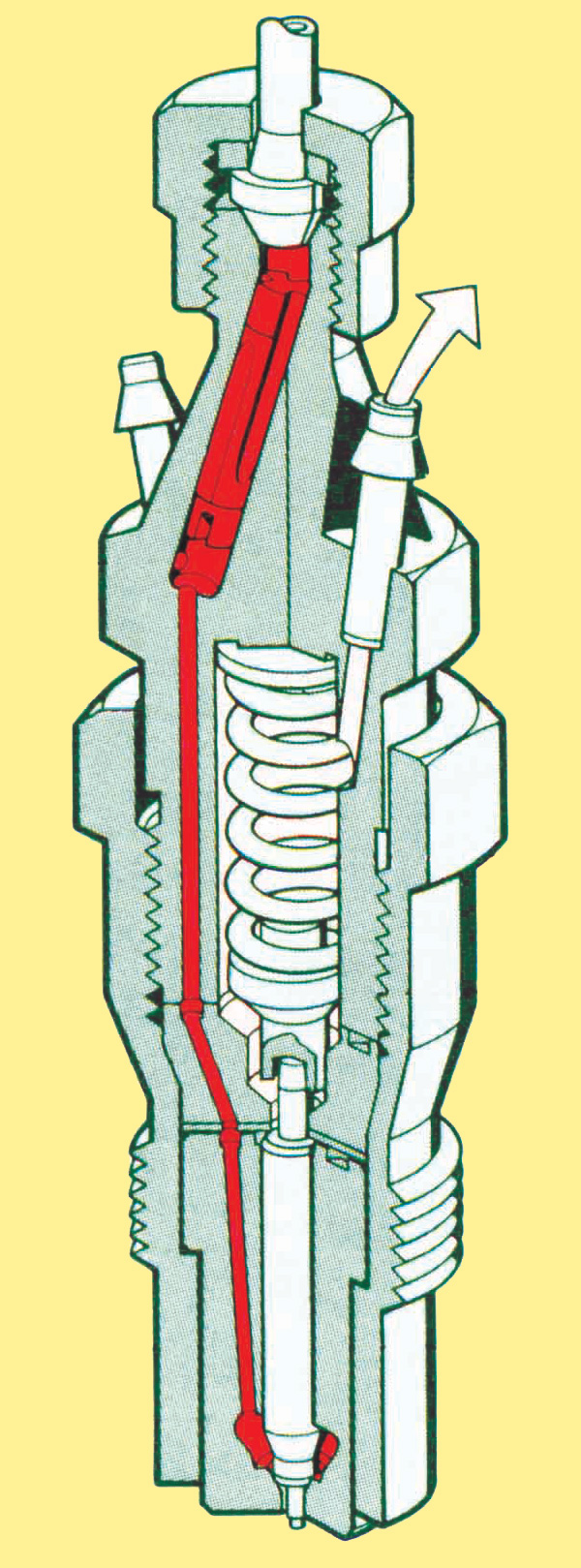
In the traditional Diesel injector, pressurized fuel from the pump enters at the top, follows the internal high-pressure passage to the injector tip, lifts the pintle and injects the fuel. What does not enter the combustion chamber passes around the pintle, around the spring and into the return line.
The injection pump plungers make a full stroke for each injection, but the accelerator and governor determine the injected quantity by moving the control rod, a toothed rack that rotates the plungers —just the opposite of a steering mechanism, this is a driving rack turning driven pinions. Depending on the rotation position, a plunger’s shaped control edge uncovers the control port after the proper fuel volume sprays and returns unused fuel to the supply reservoir.
As engine speed increases, the centrifugal advance moves injection-start farther ahead of TDC, but there is no retard with load since the combustion flame can propagate only as fuel is injected. It can’t burn prematurely if it’s still in the injector, yet to be injected.
Starting in the 1980’s, an Electronic Diesel System (EDS) replaced the all-mechanical governor. The EDS actuator changes idle speed in response to coolant temperature and the state of the A/C compressor clutch. The control unit works the actuator through the A/C relay. The actuator is duty-cycled, but you can power it briefly to confirm idle speed control. Just don’t leave your jumpers connected for more than three seconds, or you can damage the internal wiring. An electronic governor system, unlike the centrifugal version, can anticipate the A/C compressor’s load and begin to increase idle rpm just before the electromagnetic clutch engages. Later EDS variations add more sensors and actuators, like an intake air mass sensor and the EGR actuator.
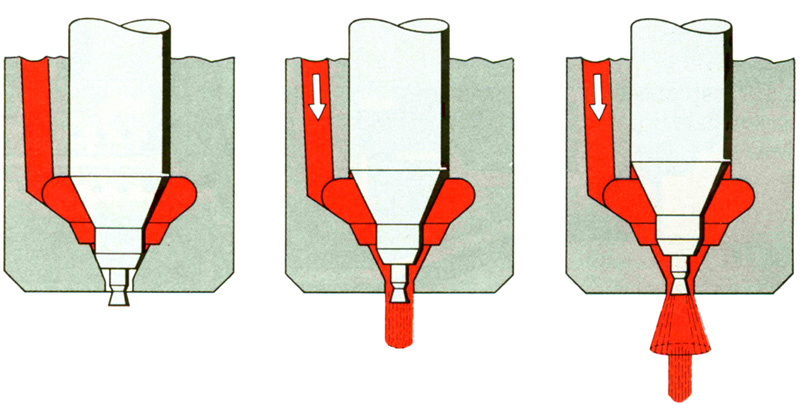
To make the combustion a bit smoother and
quieter, as well as to stretch out the power stroke for better torque, most engines use one variety or another of ‘throttling’ injector. These injectors spray at an initial rapid rate to start the fire, and then continue the volume more slowly to sustain the burn over time.
The fine tip of the injector separates the fuel into minuscule, easily burned droplets. The only way to turn oil into finely atomized droplets, practically into fog particles, yet hold them in a consistent cone shape against the turbulence of the combustion chamber air, is to force the fuel through a very narrow passage under very high pressure and at very high speed, 150 bar/2250 psi. — gun barrel pressures and bullet speeds. So never let an injector spray in the open air. Up close, the oil can slice right through clothing, skin or eyes.
Most injectors work by an initial fast squirt that initiates the combustion flame and a subsequent more diffused and extended spray that delivers the bulk of the fuel more gradually for that power stroke. The purpose is to ‘soften’ the initial combustion and spread out the combustion pressure over the power stroke. Such a design is often called a “throttling injector” since it throttles fuel delivery during part of the injection.
That narrow passage around the pintle and through the injector tip accounts for why good filtration of the fuel is so important on a Diesel engine — the slightest grit can clog an injector, jam it open or skew its spray cone pattern. That also accounts for why it is so important to machine the injectors so precisely. Otherwise they’ll never seal against the residual pressure or won’t open at the right time — to say nothing of lasting a reasonable useful life with their tips exposed to the high temperatures and pressures of the combustion chamber.
The high working pressure also shows why you don’t want to let a Diesel engine run out of fuel: It can be difficult to bleed all the air out, and you don’t need much of a bubble to soak up all that hydraulic pressure.
Such high pressure is also necessary because for much of the time the engine is running injection must continue while the piston approaches and passes TDC and during the power stroke, after early fuel combustion has raised the pressure in the chamber very high. After all, injection pressure must be considerably greater than the combustion pressure to force fuel in against it.
Diesel Detonation
Many people think they hear ‘engine knock’ when a Diesel engine is idling nearby. That’s not what they’re hearing. The idle rattle is not combustion knock but the mechanical sounds of the fuel pump when the engine is cold, the lobes of the pump cam clicking the tappets to their injection work. The fuel pressure pulses convey the clicking sounds to the injectors at the ends of the fuel lines. It takes a bit more fuel to keep the engine idling cold than idling warm, so the pump does a bit more work even before its parts have begun to expand to their operating size. Engine idle speed — momentary crankshaft speed, that is — also varies more cold than it will warm, further contributing to the rattle. That ‘engine knock’ almost goes away as the engine warms, unlike the real thing, detonation. But what is “the real thing”?
Detonation or knock means somewhat different things in Diesel and gasoline engines. In the gas engine, the entire fuel charge for the next power stroke is in the cylinder at the instant the intake valve closes, ready to burn. At the corresponding point in the Diesel cycle, there’s nothing flammable in the cylinder at all, just air.
In the gas engine, you have detonation anytime the fuel-air charge ‘Diesels,’ that is, when the mixture or any significant pocket of it crosses the autoignition temperature/pressure threshold and burns explosively, all at once. Usually, but not always, this occurs if a hotspot in the combustion chamber triggers a flame before the spark occurs. It also occurs if the motorist uses fuel of such low octane the knock sensor/timing retard system can’t correct for it.
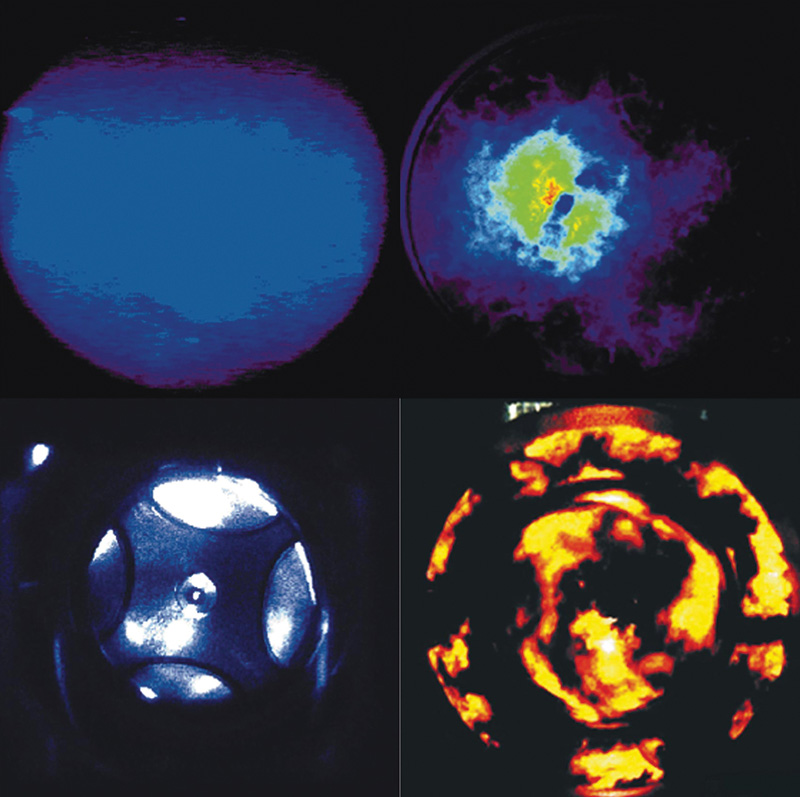
The engineers at Mercedes-Benz built several engines with glass cylinder heads to photograph combustion inside, using special high-speed cameras. Top left is a normal, ideal gas engine combustion, with a blue flame consuming most of the fuel. Top right is inhomogeneous combustion, combustion with local detonation. The red, yellow and green flame indicates incomplete, perhaps explosive fuel-air burn. Bottom left is normal, ideal Diesel combustion, with very good atomization of the fuel through the multiple nozzles of the latest injectors. Again the blue flame indicates complete combustion. Bottom right is inhomogeneous Diesel combustion, with poor fuel atomization, incorrect timing, poor distribution and/or fuel of the wrong cetane rating. Again the yellow and red flame indicates incomplete combustion. This engine would produce substantial smoke.
The premature flame causes a rapid buildup of pressure and heat, reaching a pressure maximum before TDC. The engine has to use part of its torque output to overcome that early pressure peak, so there’s a reduction of available power. Before long carbon starts to form deposits on the combustion chamber surfaces because the premature combustion was incomplete. That carbon occupies space and thus raises the effective compression ratio of that cylinder.
Now the cylinder is vulnerable to detonation. Detonation occurs when all or part of the fuel-air charge in the cylinder reaches its autoignition threshold before TDC, exploding at once rather than burning sequentially. Now instead of a rapid buildup of pressure, we have a pressure spike, which outside the engine we hear as a ‘clink’ or a ‘plink.’ Inside, it’s the sound of metal destruction, of microscopic metallic flaking. There’s more carbon buildup, more compression ratio increase, more detonation. If this continues, of course, the damage gets more dramatic, with staved-in pistons and valves hammered back into the cylinder head.
Since the charge explodes all at once rather than burning gradually, the combustion temperature also spikes. This is a bit surprising since the combustion is incomplete, but makes sense when you think of the amount of heat produced per unit of time. Another thing that makes sense is the sudden spike of NOx with detonation. The temperature went over the nitrogen-burning threshold, so NOx goes over the wall.
Shop magazines used to occasionally show a wacky series of drawings, explaining detonation and preignition by reference to colliding flame-fronts. There are, under some preignition circumstances, colliding flame-fronts, but they’re waves; they interpenetrate just like waves in water or air; they don’t collide. They’re events, not objects. They don’t clink or clank or clonk when they meet and pass through one another.
The fuel in a Diesel engine also autoignites, but not all of it at once and not explosively for the simple reason that most of it is still in the injector, waiting in line to get to work. Of course, there can be knock if the injection timing is set wrong or if one of the injectors is defective, leaking fuel in too early or failing to properly atomize the fuel it does inject. Diesel detonation can also occur if the vehicle is misfueled with something that ignites improperly. Finally, detonation occurs during a ‘runaway’ Diesel episode, as we’ll explain in Part Two, next issue. The destructive effects can be identical to those on gasoline engines.
One interesting aspect to the glass-engine photos is something faint they show about fuel efficiency. Even in the gasoline combustion chamber without detonation, the one with the smooth, homogeneous burn, you can see, all around the cylinder just at the mechanical surface of the bore, a slight reddish pink halo where the hot, gas-blue flame burns cooler and goes out as it approaches the surface. This happens in the gasoline engine because the fuel-air mixture fills the chamber uniformly, right up to the surfaces. But the surfaces, though at the operating temperature of the engine, are well below the ignition (burning) threshold of the mixture. The fire can never burn all the fuel charge. This consequence is greater in a real engine, with temperature-conductive metal surfaces.
Now look at the good Diesel burn. You don’t see the flame reaching to the surfaces because the fuel doesn’t. The flame reaches only as far as the fuel spray has traveled but it stays hot gas-flame blue all the way. It isn’t really mixed as homogeneously, just blown into the center of the chamber’s pocket of air. The Diesel combustion occurs inside an envelope of air. That air certainly gets plenty hot as it undergoes compression and ‘packages’ the combustion. But it insulates the fuel from the (relatively) cooling cylinder walls. There’s no red rim of quenched flame in the Diesel combustion chamber. All the Diesel oil can burn.
For years Diesel engines have had what some people call a ‘Diesel catalyst.’ It is, however, not really a catalyst but a ceramic exhaust filter, a particulate trap. When it captures enough waste hydrocarbons, either the temperature of the backpressure-enhanced exhaust or an electric heater ignite and burn off the captured particulates. If something goes wrong with the particulate, it clogs up, reducing the air through the engine and the power it can produce.
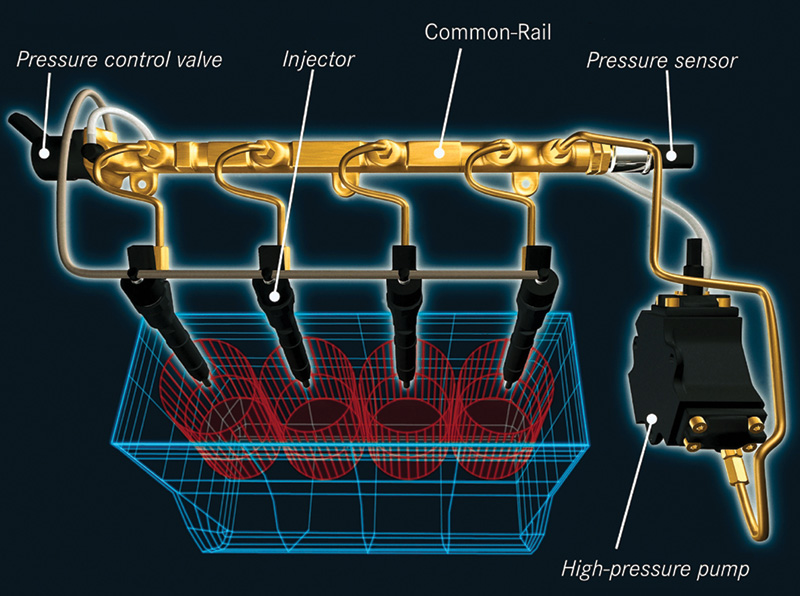
The newest Mercedes-Benz Diesels use a common fuel rail, not unlike gasoline injection systems. Much unlike the gas system, however, is the enormous hydraulic pressure, as much as 2000 bar —28,000 psi! Actuation of the injectors is electrical rather than mechanical. Special Piezo-electric injectors pulse the high pressure fuel into the center of each combustion chamber. A Piezo-electric injector is, in a way, the conceptual mirror-image of the knock sensor, using an electric pulse to cause a pressure pulse.
Industrial Diesel engines are usually direct-injection designs. The fuel injector sprays fuel directly into the combustion chamber, just above the piston or even into a pocket cast into the piston face. Direct injection provides greater manufacturing simplicity and about 18 percent better fuel economy (you don’t lose heat through the prechamber if you don’t have a prechamber).
Mercedes-Benz has not sold Diesel cars in the United States for several years, but they have continued development and manufacture of them in Germany. The new four-valve engines are direct injection, not prechamber designs (there were a few four-valve prechambers in the late 1990s). No longer are the injection systems predominantly mechanical (they have been at least partially computerized since the earliest versions of the Electronic Diesel System in the late 1980’s), but now use electrically pulsed Piezo-injectors. Pressure still comes from a mechanically driven pump, however, into a very high-pressure version of the common rail fuel system seen on gasoline fuel injection systems. Timing is electronic, not mechanical. High pressure (almost 2000 bar!) is available even at idle, so they can use injectors with multiple very tiny nozzle holes instead of one. This allows even finer fuel atomization and approaches a more homogeneous mixture, avoiding those pockets of rich mixture (black smoke) and lean mixture (NOx). Since pressure is constant, there’s no ‘Diesel noise’ as cam lobes tap plungers — there are neither injection pump lobes nor plungers.
Will the new Mercedes-Benz Diesels show up in this country? Nobody’s saying for now, but it’s likely the emissions regulations for Diesel engines will have to settle before the company decides that.
A major problem right now is that the new direct-injection Mercedes-Benz Diesels use the new NOx-reducing exhaust catalyst incompatible with sulfur in the fuel. European fuel sources are relatively low-sulfur, while those for North America have more of the unsought element. Perhaps economical means will unfold for removing the sulfur, perhaps they’ll find some way to modify the catalyst system, or perhaps they’ll figure out an economical way to make sulfur-free synthetic Diesel fuel from natural gas. Stay tuned.
As there’s more emphasis on a reduction of CO2 because of ‘greenhouse-gas’ concerns, the return of the Diesels seems assured. The enormous improvement in fuel economy, and the corresponding enormous reduction in carbon dioxide emissions, will leave no alternative. Add to it the reasonable prospect of clean synthetic Diesel fuel, derived from local sources, and the future of the Diesel is also assured. In the long run, it may be the gas engine that’s imperiled.
0 Comments