Diesel Efficiency
‘Everyone knows’ Diesel engines are more efficient than gasoline engines doing the same work, but ‘everyone’ does not know why that should be. Or worse, everyone ‘knows’ something that’s mistaken. And ‘knowing’ something that’s false can mean servicing or repairing a car inaccurately. The owner of a Diesel Mercedes-Benz probably expects a long useful life from the car and good fuel economy over that long useful life. Those are reasonable expectations, if you avoid ‘knowing’ something mistaken.
It’s a mistake to contrast a gasoline engine with a Diesel without saying something more. The defining characteristic of a gasoline engine is the fuel it burns, gasoline or an alcohol blend very similar to gasoline in most respects. But the defining characteristic of a Diesel engine isn’t the more energy-dense Diesel fuel it burns, but how it lights the combustion, by compression ignition instead of by spark ignition. In principle you could use anything as fuel for a Diesel engine as long as you could hammer it into the combustion chamber at the right moment, as the piston neared the top of the compression stroke. Some dual-fuel Diesel stationary engines today use ‘Diesel fuel,’ that is fuel oil, to start the burn and natural gas for the bulk of the torque production. Both the injectors and pumps of such Diesels are, of course, more complex than conventional injectors and pumps. There are even special military vehicle engines using both spark and compression ignition simultaneously. They can run on any flammable liquid, from drycleaning fluid to cooking oil to perfume or brandy. Or even on gasoline.
The real contrast is between efficiency of the spark-ignition engine, the ‘gasoline’ engine, and the compression-ignition engine. And the latter’s real efficiency comes from what the Diesel doesn’t have, a throttle, and (to a lesser extent) what it does have, a higher compression ratio. To understand, look back for a moment at the gasoline-, the spark-ignition engine. You vary the output torque by varying the intake air-fuel mixture volume. Actually, torque output follows the intake mass, but mass and volume are in cahoots, so you vary both at once with the throttle.
Gasoline engines rarely operate at sustained wide-open throttle. But anytime a throttle closes even partially, intake manifold vacuum rises (or equivalently, manifold pressure declines). Any vacuum in the intake manifold translates, once the intake valves open, into the same vacuum at the top of each piston during the intake stroke. It takes torque, that is, work derived from the chemical energy of the burned fuel, to pull that piston down its intake stroke because the pressure in the crankcase pushing up is at or about atmospheric. If there’s a 10 psi. pressure difference between the crankcase pressure pushing up and the intake pressure (partial vacuum) above the piston, and if the piston top has an area of five inches square, you need a force of 50 pounds to pull that piston down. This is work the engine must derive from the torque it produces during the power strokes, work subtracted from the work delivered to the transmission and accessory drive pulley.
Multiply that work by the number of pistons, by the stroke and the engine rpm, and you can see why the gasoline engine has a lot of work to do internally even when, at idle, it’s doing no useful external work at all. This unproductive ‘work,’ from energy consumed just to keep running, is often called the engine’s pumping loss. That represents almost all the work done at idle, and it is an inefficiency at every power setting below wide-open throttle at the high point of the engine’s rpm/torque curve.
The Diesel, in contrast, doesn’t have to do any of this work overcoming manifold vacuum because its unthrottled manifold develops no significant vacuum (except for the aerodynamic drag through the intake channel surfaces). Dodging that unnecessary work is the main reason for the Diesel’s much greater partial-load efficiency. It’s also the reason, you’ve probably already figured out, why a Diesel has virtually no engine-braking downhill, absent an auxiliary compression brake. Not for nothing did people once say a gas-engined car coasting in gear downhill was “hanging by its connecting rods.” It was converting downhill kinetic energy into pumping losses.
A Diesel engine operates with about equal efficiency over most of its dynamic range, from off-idle to high-cruise. That absent throttle is also why it burns so little fuel at idle: Many Diesel engines won’t reach operating temperature if started cold and just left idling. In fact, they can ‘coke’ up since the combustion chamber surfaces never get up to operating temperature. Some cool down more quickly idling than shut down completely because coolant circulates heat to the block surface.
Industrial Diesel engines are usually direct-injection designs. The fuel injector sprays fuel directly into the combustion chamber, just above the piston or even into a pocket cast into the piston face. Direct injection provides greater manufacturing simplicity and about 18 percent better fuel economy (you don’t lose heat through the prechamber if you don’t have a prechamber).
Compression ratio also contributes to the Diesel’s efficiency. Spark-ignition engines use compression ratios from about 8:1 to about 10:1 and must use elaborate knock-avoidance measures toward the top of that range. Diesel compression ratio ranges from about 17:1 to perhaps 23:1. The advantage of a higher compression ratio is thermal, deriving from the chemistry: The more oxygen molecules you can get into a cylinder before the intake valve closes, the more power you can develop in the next power stroke from burning that oxygen with the fuel. What’s more, the Diesel combustion can expand over the same increased ratio during the power stroke, a major reason why Diesel exhaust is hundreds of degrees cooler for the same power output than exhaust from a gasoline-fueled spark-ignition engine. Heat that goes into pushing the piston down and turning the crankshaft is heat put to work; heat that stays in the burning mixture and blows out the exhaust is heat wasted; it’s inefficiency.
What does that mean for diagnosis and service of a Diesel engine? Its efficiency depends fundamentally upon the free flow of air into and out of the engine. Let there be any sustained restriction of intake air, and you have a throttle, whatever you call it. The most common causes of such restrictions are clogged air filters and pinched or crimped intake air tubes. Let there be any sustained restriction of exhaust, and you have the same effect on the other end: The engine must do unnecessary work to force the exhaust around or through the restriction. It takes a surprisingly small amount of intake or exhaust restriction to raise fuel consumption and lower maximum power output, and the more work you try to do the larger is the effect of the restriction.
Another aspect of the unthrottled Diesel is the sheer volume of air it pumps through itself. Under the same conditions of atmospheric dust and dirt, a Diesel will collect much more on the intake filter than even a much larger spark-ignition, gasoline engine, because it draws so much more air through. Intake and exhaust restrictions are not the only possible causes of increased fuel consumption and reduced power, of course. Check also for injector timing and spray pattern as well as all the ordinary symptoms of engine fatigue like worn rings or burned valves. And remember forces outside the engine, like dragging brakes or underinflated tires, can have similar effects. Nobody said any of this would be simple!
Emissions and the Return
The emissions characteristics of Diesel engines are a matter of great current controversy, but we won’t go beyond the uncontroversial here. Diesel fuel is chemically very similar to heating oil, kerosene and jet fuel. It is very energy-dense, producing about 15 to 30 percent more Btu’s per gallon than a gallon of gasoline. In addition, Diesel fuel is a much more complex hydrocarbon. Much less energy is required to extract it from crude oil than any other fuel commonly used for transportation (you get more gallons of Diesel fuel oil from a barrel of crude than anything else you could refine for because you’re ‘refining’ less – it’s closer to crude). Methanol, in contrast, is chemically very simple: an oxygen atom, a carbon atom and four hydrogen atoms. But methanol is much more complex to produce, either from crude oil or other sources. Simplicity of the fuel comes at the cost of complexity of the refining process.
Couple the refinery efficiency with the fuel economy and mechanical durability of the Diesel engine, add the dramatic reduction in carbon dioxide (the ‘greenhouse-effect’ gas) because the Diesel requires dramatically less fuel, and you’d think it would clearly be the first choice.
There are other clear emissions advantages, too. Because a Diesel runs so lean, it produces essentially no carbon monoxide (CO), the colorless, odorless and lethal component of gas engine exhaust. While modern gasoline engines produce much less carbon monoxide than earlier ones, they require extensive emissions controls to reduce CO to present levels. Diesel engines just never produced much CO in the first place, not even ancient ones like the 1936 260 D we showed last issue (page 4).
Running lean on the overall mixture scale, however, does not magically solve all emissions problems. If an injector does not atomize fuel finely enough or in the right cone pattern, the result can be the worst of two worlds at one and the same time. You might have black smoke from too rich a mixture in one part of the combustion chamber where the droplets are too large or too close, combined with NOX from a nearby area where the mixture is too lean, in a space between the overrich pockets and the empty air. Proper combustion requires just the right atomization, just the right pattern and just the right timing. If you don’t have those, either the injector or the pump or the setting is not functioning properly.
Oxides of nitrogen (NOX) can form in a Diesel engine at very high combustion temperatures, just as in a gasoline-fueled engine, but an EGR system can prevent that formation by keeping peak combustion temperatures below the NOX formation threshold. On the as-yet-unimported new Mercedes-Benz direct injection Diesels, a new deNOX catalyst cleans up any residual NOX. The system runs superlean for about two minutes, then rich for two seconds, then lean again.
But not so fast! And that But carries the capital B. Complex hydrocarbons and sulfur are the Diesel emission problems. It isn’t that there is significantly higher quantity than on a gasoline engine: With the Diesel’s inherently clean burn and modern engine management systems as well as burnoff particulate traps, you can keep the quantity down just as well. The problem is the variety. Diesel fuel, as we saw earlier, is a much more complex chemical compound than gasoline simply because it requires less refining. But that means the exhaust contains literally thousands of different chemical compounds, most of them untested for their effect on living organisms, atmospheric chemistry and so on.
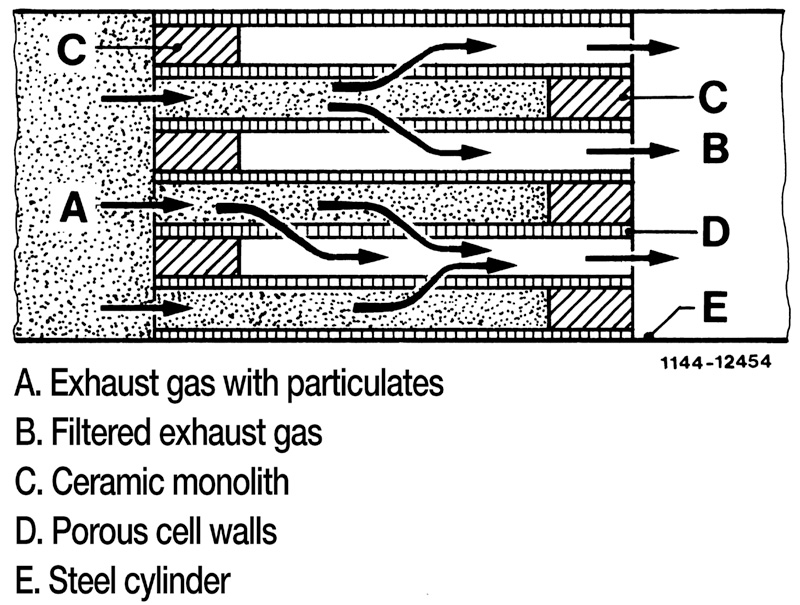
Present Diesel exhaust traps consist in a fine ceramic filter to catch particles of soot. When enough of them collect, they burn off in the exhaust. Later versions of Diesel exhaust treatment use reducing catalysts to remove NOx from the exhaust.
Are they dangerous? Given the large variety and numerous questions about the chemistry, the expense and difficulty of the tests, the tests are not satisfacory or complete and perhaps never will be, so nobody will know with certainty. What’s the reasonable choice to make under these conditions of uncertainty? Well, that’s where the controversies come in. As long as the particulate traps, deNOX catalysts and whatever other emissions controls work properly, the question doesn’t force us to decide.
For years Diesel engines have had what some people call a ‘Diesel catalyst.’ It is, however, not really a catalyst but a ceramic exhaust filter, a particulate trap. When it captures enough waste hydrocarbons, either the temperature of the backpressure-enhanced exhaust or an electric heater ignite and burn off the captured particulates. If something goes wrong with the particulate, it clogs up, reducing the air through the engine and the power it can produce.
Batteries and Glowplugs
Diesel vehicles often have batteries with about twice the capacity of a gasoline engine, and even at that starting in the cold of winter can be a problem. Why?
For two reasons. First, most Diesels generally and all Mercedes-Benz car Diesels use glowplugs to start the engine and keep it running for the first few minutes when cold. A glowplug is a small electric heater, shrouded in a protective metal case, hot enough to push the injected fuel just over the autoignition point during cold cranking. If your hair is grey or gone, you may recall model airplanes, powered by two-cycle engines like the redoubtable Cox 49, which used a glowplug, heated electrically from a dry cell to start and kept hot thereafter by the residual heat of the previous combustion. Unlike the Cox glowplug, the Diesel glowplug is just along for the ride once the engine is running smoothly at operating temperature (though some later Diesel control systems turn the glowplugs back on at extended idle to make sure everything gets burned). The Cox glowplug didn’t have any timing advance beyond the chemistry of the fuel and the temperature of the filament, but perhaps ignition timing is not critical for an engine with a half-inch stroke and an operational speed of 20,000 rpm or so. Just like the Cox glowplug, the Diesel glowplug provides a place in the combustion chamber where it is hot enough to light the fuel-oil fire once the injection occurs, as long as there is sufficient pressure.
And that “sufficient pressure” is the second reason for the large battery. A gasoline engine with good rings and valves will have, say, 150 psi. compression at crank. That corresponds to about a 10:1 compression ratio. But prechamber Diesel engines have over 20:1 compression. That’s why, when you switch it off, a Diesel stops now, hard against the next compression stroke. The difficult part of starting any engine is to keep it turning fast enough during the compression stroke that the spinning inertia will carry it just beyond TDC even when the ignition – spark or injection – and the combustion pressure rise occur slightly earlier. If it’s not turning fast enough, the air doesn’t get hot enough to cross the fuel’s autoignition threshold, so no combustion and no start occurs. Or with a weaker crank still, the crankshaft slows or stops on each compression stroke, and there’s not even a full crank. Notice it’s not the horsepower of the starter that’s in question but the torque at the critical combustion moment in the compression stroke.
The starter would never be able to outmuscle the combustion pressure. It’s the inertia of the crankshaft and other rotating mass. Doubt it? Ever watch somebody start an old aircraft radial engine by pulling the propeller by hand? How many old-time aviators do you suppose had multi-horsepower arms? They were able to get things spinning fast enough by hand that the stored rotating inertia of the prop and crank could carry the engine through the compression stroke and into the first power stroke. Thereafter it could run on the normal four-cycle principles.
On older Diesels, some engines could bounce backward at the beginning of injection and continue to run backwards, though not for long: You can imagine how effectively an oil pump works turning the wrong way. Mercedes-Benz Diesels from the 1950’s and 1960’s have spring-loaded air throttles, essentially check valves, in the intake channel, in part to snap closed and stop an engine that tries to run counterclockwise.
So a Diesel battery must have the capacity to heat the glowplugs, perhaps a 50 or 100 amp draw for as long as a minute, yet still retain sufficient reserve to spin the starter against at least twice the resistance a gasoline engine starter must overcome. It must provide about twice the storage and cranking capacity of a battery for a similar sized gasoline engine.
Older Mercedes-Benz Diesels used a bank of resistance coils to limit the current through the glowplugs to an amperage that is sufficient to heat the surface of the glowplug enough to ‘spark’ the combustion when injection occurs but not enough to burn out the glowplug prematurely. Later Diesel systems use electronic current limiters, combined internally with the glowplug control relay. That system conserves electrical energy since there are no resistance coils to heat and in principle allows a somewhat smaller battery.
With all that even on a 40-below winter morning, the compressed air adjacent to the glowplug in a Diesel engine can momentarily achieve the 400+ degrees or so necessary to fire that first power stroke. With the first power stroke, of course, the crankshaft spins faster and generates hotter compression strokes than the electric starter motor could ever wind up, so there’s little continuing problem. Most modern engine systems turn the glowplugs back on for a short time after startup to preclude cylinder miss.
So why don’t gasoline engines need glowplugs at 40-below? It’s just as cold as for them, and gasoline has an even higher autoignition temperature. Besides, their puny 8 or 10 to 1 compression ratio can’t heat the intake mixture very much. Because the spark between the plug electrodes is much hotter than any glowplug and you only need the maximum temperature in one place to start the combustion.
Fair enough, then, why don’t Diesels have spark plugs instead of glowplugs for cold starts? After all, the spark would be just as hot for them. Two reasons: The plugs can’t be made economically to withstand the combustion pressures in the Diesel powerstroke (the ceramic would pound out), and the plugs would foul with carbon after any short trip, grounding the spark.
So why do you need glowplugs in all cylinders, then? It seems like once the engine runs on its own after the first combustion and power stroke, it ought to turn fast enough to compress the next cylinder fast enough to achieve a temperature high enough for autoignition. Seems like it, perhaps, but not necessarily. There’s a certain temperature/pressure/fuel combination that must occur, or there won’t be combustion. The most reliable symptom of a burned-out glowplug, in fact, is a temporary cylinder miss when first started, combined with the telltale white smoke from fuel in the still-cold exhaust. If that problem goes away relatively quickly with the first few minutes’ engine heat, get out your continuity tester and check the glowplug resistances.
Unlike the spark-ignition engine with a spark kernel of indefinitely high temperature, the compression-ignition engine may not necessarily reach the autoignition temperature for the next power stroke. And if it doesn’t, the crankshaft will slow, probably thumping to a stop after one or two more incomplete compression strokes. So even on Diesel vehicles that turn the glowplugs off during cranking (to devote all the battery power available to spinning the crank as fast as possible), the plugs retain heat for the next few cycles. Most systems turn the glowplugs back on once the engine is running on its own power. This avoids misfire, stalling and emissions problems when unburned fuel blows into the exhaust pipe, there to turn to smoke, white or black depending on the temperature and whether there has been any combustion.
It will take correspondingly longer, obviously, to recharge the battery for the next start, the colder the engine and the air are. Short-tripping in a Diesel in the coldest part of the winter is a good way to regularly meet people in the jump-start business. Most later Mercedes-Benz Diesels start relatively easily because the Electronic Diesel System attunes preglow time more accurately to coolant and ambient temperatures than the old controllers with a box of resistors and a relay could, making better use of the available battery power.
Here’s a safety note when jump-starting: You’ll probably be using a gasoline-engine vehicle as the electricity source and jumper cables suited to starting gasoline engines. Because of the gasoline engine’s smaller battery, don’t just set the cables and crank! The gas engine battery and charging system aren’t up to the surge in amp draw. Chances are, the cables aren’t either. Leave the cables connected and charge the big Diesel battery for at least five minutes before you turn the key to preglow. Sometimes an immediate second preglow period is advisable before cranking in the very coldest weather. Oh, and you know about the cable-hookup precautions to avoid exploding the battery? They get more serious as the battery gets larger: The bigger the battery, the bigger the acid-spattering boom.
Check glowplugs for continuity, terminal to block, with the harness pulled. Resistance should be very low when cold and (on older models) go somewhat higher when hot, but when a glowplug burns out, its resistance goes open. Glowplugs have internal resistance-heater filaments. An individual burnt out glowplug will often cause an initial miss with white smoke (fuel) through the exhaust. In very cold weather, loss of that one cylinder can be enough to keep the engine from starting because the crank slows so much for that missing cylinder. In the absence of the auxiliary heat, the compressed air in the cylinder may not quite reach the autoignition threshold of the fuel. Raising engine speed with the fuel pedal can often get rid of the smoke for the moment, and once the engine begins to warm up the glowplugs are no longer needed.
But a new plug is the only fix. Like light bulbs, glowplug useful life is measured in on-off sequences, not in miles traveled. A Diesel cab, with the engine started and stopped just once a day, might use the same glowplugs for many years; another car with the same engine could go through them more often, if it restarts frequently. However, some Diesel drivers have gone for years without noticing a burned out glowplug – if they regularly use a block heater whenever the engine is cold. In northern climates, a block heater is a wise precaution, not just to insure regular starting, but to extend the life of the battery, starter and charging system as well as to reduce the period of relatively high emissions while the engine warms. For the same reason, you should never just start a Diesel engine and let it run at cold idle expecting to ‘warm up’ the engine. A driver who does so is filling his combustion chambers and exhaust with soft carbon that will appear in the form of smoke as soon as he starts driving. The proper way to warm an engine is to get underway as soon as the engine is running reliably and keep it under moderate load until you reach operating temperature. This is true for gasoline engines, too, of course.
Turbochargers and Superchargers
Mercedes-Benz has generally used exhaust-gas-driven turbochargers for Diesel engines and crankshaft-pulley-driven superchargers for gasoline engines, starting with Diesel turbochargers in 1979. Both work by forcing more air into the intake manifold, raising its pressure above the ambient and cramming more oxygen molecules into the cylinder. This allows the injection of additional fuel and results in a still more powerful power stroke. For the same displacement engine and the same crankshaft rpm, you can develop dramatically more torque. A turbocharger consists of two turbine ‘fans’ in separate chambers, sharing a common shaft. Exhaust gas spins one side, and the shaft carries the energy to the other to compress the incoming air. A supercharger consists of two or more counterrotating lobes in a shaped chamber. A belt-driven pulley on an electric clutch like an A/C compressor powers the supercharger. When it spins, it forces more air into the engine than ordinary ambient pressure would deliver.
There are a couple of reasons Mercedes-Benz engineers like turbochargers for Diesels and reserve superchargers (which they like to call “Kompressors” because that’s the German word as well) for gasoline-fueled, spark-ignition engines. To raise the pressure of the incoming air by a given measure, a turbocharger heats the gas more than a supercharger does, simply because of the speed and friction of the turbocharger blades. On the gasoline engine, this raises problems of knock, of detonation and all the octane/detonation issues. A supercharger bites off relatively larger ‘pieces’ of intake air, heating less, so it avoids the heat problems. What’s more, most of the time it’s switched off. On a compression-ignition Diesel engine, however, heating the intake gas is far less of a problem – you want the stuff to get hotter; that’s part of the plan. Of course, when you heat air it expands, which flies in the face of the purpose of the turbocharger/supercharger, so very often the turbocharged air runs through an intercooler, basically a radiator for pressurized air. This doesn’t change the pressure, but it lowers the temperature, which means we get the increased number of oxygen molecules we were after for more power.
Many vehicles use a turbocharger to increase the output of their Diesel engines, some with intercoolers as well. This is conjecture, but I suppose within reasonable limits a turbocharger costs the Diesel engine nothing under circumstances when no turbocharging is needed, at part loads and idle. The increased intake air volume merely becomes increased powerstroke pressure by the same factor less a smidgen for heat loss. An unthrottled Diesel engine can use virtually unlimited quantities of intake air with no adverse consequences.
On a gasoline engine, however, you’re locked into a narrow fuel/air ratio and only occasionally want greatly increased airflow, on those very occasions when you signal the engine with your right foot that you want to put distance between your self of the immediate future and your current, more static self. A turbocharger inherently must wait while exhaust pressure builds and then intake pressure builds from that. A supercharger delivers increased intake pressure on the next piston stroke. But a supercharger is more complex than a turbocharger and generally less suited to passenger diesel cars. Turbo- chargers are simpler in these applications, and Mercedes-Benz has generally used them that way.
A turbocharger increases exhaust backpressure, generally a bad thing, as it builds intake pressure, generally a good thing. But what energy goes into compressing the intake air during the compression stroke comes out equally during the power stroke. People often liken this to the energy stored in a spring: Except for a bit radiated away as heat, you get back about as much on the extension as you soaked up on the compression. Some heavy trucks use only pneumatic springs, after all, and don’t gradually sink onto their frames.
Earlier Mercedes-Benz turbochargers were just the two fans and shaft in the nautilus-shell scroll casting we described, but later they include wastegates, to bypass the turbocharger when the pressure reaches a maximum threshold and more recently the variable-geometry turbocharger, allowing constant pressure at differing gas flow and turbocharger rpm conditions.
Runaway Diesel!
As they wear out, most engines just develop less and less power, start smoking more and eventually get junked or overhauled. That’s true of most Diesels, too, but not all. Occasionally one goes out of business dramatically, spectacularly, explosively – a ‘runaway’ Diesel. Often a runaway Diesel stops only when a connecting rod stump punches a hole through the side of the engine block. Poke around Diesel junkyards a bit, and you’ll learn this end is by no means uncommon.
Here’s how the engine runs away: As any engine wears, the rings and valves wear. That means a certain amount of lubricating oil gets into the combustion chamber, past the worn rings, past the hardened seals, down the loosened valve guides. Often, but not always, this means increased exhaust smoke, especially on a gasoline engine. But a Diesel engine runs on oil naturally. It can burn some crankcase oil without much smoke, more than a gasoline engine can.
What’s more, on many older engines the owners, perhaps the second or third owners by this time, become less rigorous about engine oil change schedules. Not only does that allow carbon and grit to accumulate in the oil, it also allows fuel to contaminate and dilute it (and every time an engine, any engine, starts cold, fuel drains around the pistons into the crankcase). A gas engine can boil the fuel out if it runs hot long enough because the crankcase oil will reach and hold a steady 220-225 degrees F (gasoline boils at about 168 degrees). A Diesel engine will get just as hot at steady cruise, but the fuel oil doesn’t vaporize at the crankcase oil’s maximum temperature. So that engine must wait for an oil change to flush out the fuel-contaminated oil. Fuel-contaminated lubricating oil doesn’t just lose viscosity and lubricating properties, allowing more rapid wear and further fuel contamination; the oil also develops a lower and lower flashpoint, eventually approaching the flashpoint of the fuel itself. Now the engine is closing in on the ‘runaway.’
Diesel engines can have four different kinds of ‘smoke,’ two white, one blue and one black; none of them good.
White ‘smoke’ can be engine coolant (i.e., antifreeze steam) from a blown head gasket or casting crack, or it can be clouds of tiny fuel droplets and vapor, blown through the engine unburned from lack of sufficient atomization and temperature. Steam doesn’t go away until you run out of coolant; white fuel vapor goes away once the engine reaches operating temperature. Your nose will immediately resolve this diagnostic quandary.
Blue smoke, just as on a gasoline/spark engine, comes from crankcase lubricating oil, drawn past the rings or down the valve guides and partially burned in the combustion chamber. Diesel combustion can mask burned crankcase oil for a while, but once it becomes permanent and noticeable, replacement or remanufacture of the engine is the next step.
Finally, black smoke is unburned fuel after the engine is warm enough to burn it but didn’t. There wasn’t enough oxygen to burn that fuel dose, apparently. Either the air filter is so clogged as to reduce airflow, or the fuel spray atomization is so poor that the droplets are too large, or the pattern is too densely clustered to burn the fuel in the available combustion time.
Let a brew of oil and fuel contaminant leaking back around the rings and down the valves into the combustion chamber reach a certain threshold, the amount needed to sustain combustion, and you have a ‘runaway’ Diesel on your hands, usually after a sustained application of full power. The driver releases the fuel pedal at the top of a hill, but the engine does not slow down. Because ignition does not occur at the most favorable advance angle, the engine doesn’t develop full power, but this ordinarily happens just as the driver also releases the clutch or just tries to coast with an automatic transmission. Because of the uncontrolled combustion timing, there’s usually strong detonation at the same time. The engine increases rpm rapidly, but since it’s not burning fuel from the injectors, when the governor shuts off all the fuel, this has no decelerating effect on the engine. Neither would turning off the ignition key, which also stops fuel. The crankshaft can and will go right past redline. The only ‘governor’ at that point is whichever comes first, valve float or connecting rod failure.
This is not a ‘slippery slope.’ It’s a drop off a cliff. You have seconds, not minutes, to recognize the problem and solve it. Engine speed can increase now without any limit other than the volume of oil past the rings and valves (and less frequently past a turbocharger turbine seal). And the faster it goes, the more oil is likely to blow by. So the faster it goes, the faster it goes. Actually, of course, blowby will stop as soon as there’s a large hole in the crankcase casting, bleeding off the pressure. An engine running beyond redline for even a short time sets up resonances in the connecting rods, and one of them will punch out. When that rod decides to part company from its piston and the crankshaft, the runaway engine stops, with a roar and a bang, in a cloud of smoke and steam.
How can you reign in a ‘runaway’ Diesel? Two ways: Mechanically halt the crankshaft, or mechanically stop the air. With a stick shift car, put it in gear, stand on the brakes and release the clutch. As with any car, the brakes are much more powerful than the engine and will clamp the car and the crankshaft to a standstill. What if it’s not stick shift? Sometimes standing on the brakes will hold the engine to a speed where it will stop, anyway; after all, the engine can’t put out maximum power with the wrong fuel igniting whenever it feels like catching fire. In any case, you’ll probably be able to hold it below redline. That could cook the transmission, but if the alternative is letting the engine throw a rod, it may be prudent anyway.
You can ‘strangle’ a runaway Diesel (or any engine, runaway or not, Diesel or not) by capping the exhaust to prevent the engine from exhaling. That may be harder to do than you expect, of course, considering both the temperature and pressure of the exhaust. There will also be quite a bit of noise and smoke. In principle, you could stop the engine by choking off the intake air as well, but that would ordinarily take too long. Usually a ‘runaway’ Diesel engine runs away for good unless somebody is smart and very quick.Â
0 Comments