Speed into heat, that’s brakes at work
One of the more recurrent questions motorists raise is: “Why do my wheels keep getting dusty, even though I clean them so often? The rest of the car doesn’t collect dirt like that. Can you do something to stop all this dust from settling on my wheels?â€
The right answer should be, ‘Can, but won’t.’ And the rest of the right answer is ‘What’s more, doing anything to reduce the formation of that dust would be a mistake. Just keep cleaning the rims if it bothers you.’ Here’s an explanation we hope will be useful and interesting for your customers as well as for you in the shop.
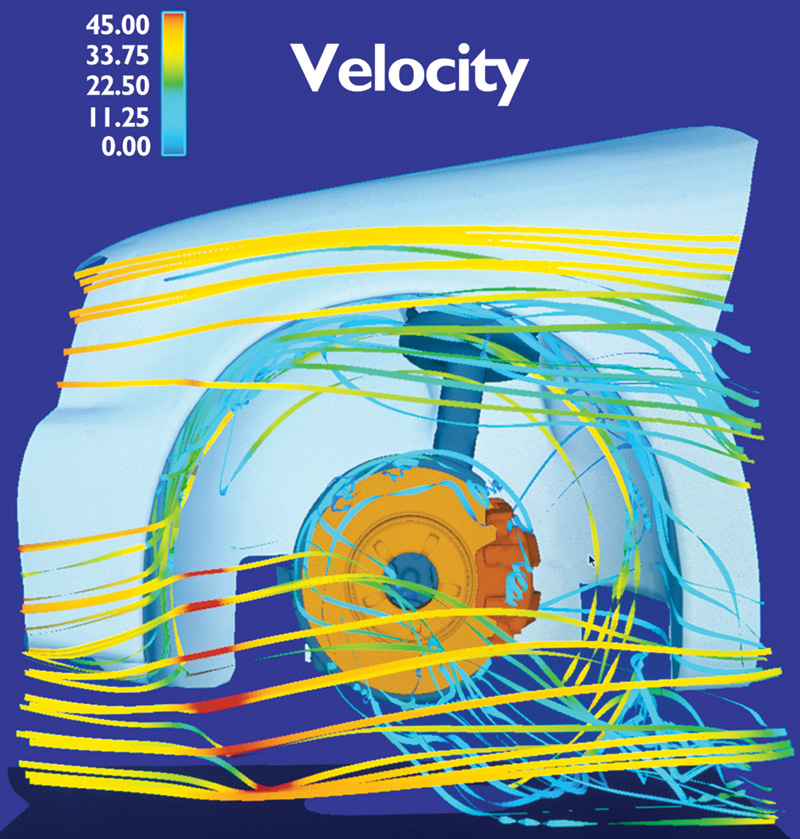
In this computer graphic, you can see by the color-coding the relative speed of the air passing around and through the wheel through different paths. Dust will settle where the windspeed is slowest. That’s also where the brakes generate all the dust and heat
The dust on the wheels is residue from the brake pads and rotors, worn off as the brakes stop the car. It includes some ordinary road grit and tire rubber, too, because the braking system draws air from the underside of the car and blows it toward the outside, carrying whatever road and tire dust it sweeps along. As you can see from the color-coded, virtual smoketrails in the computer ‘windtunnel’ graphic, the air adjacent to the wheelrim is, somewhat surprisingly, the slowest moving air around the car, so that’s where the dust settles.
So why not just trick the car out with solid wheels, after the fashion of ‘moon disks’ from the 1950’s? A chopped and channeled, candy-apple red bathtub Hudson Hornet won’t show dust on its wheels. A manhole-cover, slab hubcap would certainly stop the flow of air and the dust it carries along. And the smooth surface would allow a faster perimeter airblast, preventing most of the dust from collecting on the wheels.
Of course, so would removing the brakes altogether. No brakes, no friction, no dust. Nobody would be so rash, surely, as to consider that option. The ‘manhole/moon-disk’ option, however, is just a once-removed version of that preposterous suggestion. Let’s see why.

Brakes are machines for extracting energy to slow a vehicle. They’re designed to produce and remove heat and deliver it to the outside air, but if they absorb more heat than they can dissipate, as in this experiment, the temperature of the pads, rotor and eventually caliper just increase. The only thing cooling brakes is the air drawn through them and blown out the wheels, and that air channel must stay open if the brakes are to function safely. With no air-dissipation limit to the heat buildup, either brake fade from boiling brake fluid or mechanical failure can occur. You can imagine what this kind of heat, sustained even a little while, would do to wheel bearings and grease seals as well as to the caliper rubber. Enough heat could even set a cast-iron brake rotor on fire.
Consider what brakes do. A moving car is, besides a transportation vehicle, a climate-control chamber, a portable private space and all the various other automotive things we think of, besides all that, it is fundamentally a kinetic object, carrying momentum in a particular direction. We know from basic automotive physics that a car driving at a steady speed-limit cruise along a flat, straight highway may only require 15 or 20 horsepower to maintain its movement, and much of that goes to power lights, air conditioning, power steering and other accessories.
But that’s not the total power stored as kinetic energy in the moving car. The total momentum is the torque required to raise the vehicle speed from a standstill to highway cruise. For most cars – perhaps not those with the most powerful engines – that requires, let’s say, 30 seconds of the better part of the engine’s power output. Once up to speed, all that engine power it took to get there remains stored as the momentum of the moving car. To bring the car to a halt requires absorbing and dissipating the same total amount of energy – and sometimes in much less time than it took the engine to build it up. The brakes on any modern car can bring it to a stop from a given speed much more quickly than the engine – than any engine – can raise the speed up to the initial velocity. A conservative estimate is that most cars’ brakes can generate deceleration roughly equivalent to 1500-2000 horsepower.
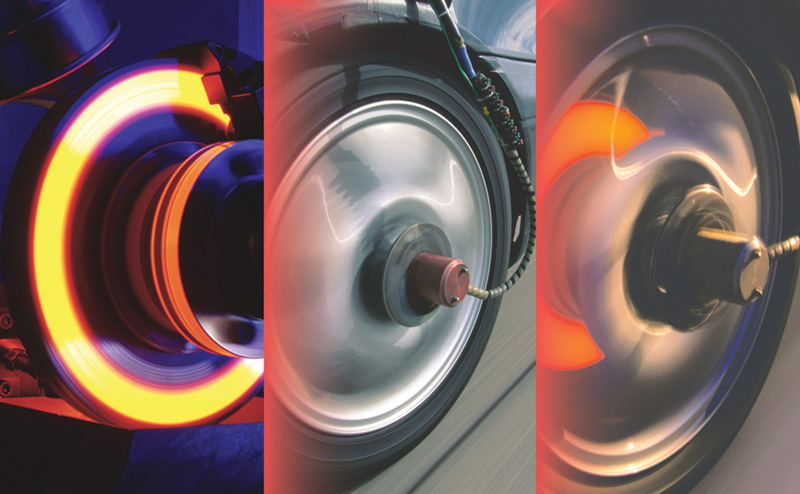
Brake testing is one of the most extensive projects for a car manufacturer. Test cars, festooned with dozens, even hundreds of sensors, record temperature and other changes in many places over any kind of condition the vehicle may encounter. These tests are repeated many times to determine the best combination of design, materials and function. Changing something as critical as the flow of cooling air through the wheel, as in an attempt to stop brake dust, for instance, can adversely affect brake performance and safety. Changing something as critical as the wheel design, particularly for nothing beyond cosmetic reasons, could be a very imprudent amateur modification. It isn’t that form follows function; it’s that long, careful testing has determined the best form for the function.
All of that power, 100 percent of it, has to take the form of heat transferred to the air. The energy transmission path is not obvious, though: The momentum of the moving car is the average kinetic energy of all the molecules constituting it. They vibrate at all sorts of speeds in every direction, but if the car is moving down the road at 60 mph, their average speed is 60 mph forward down the road. What the brakes must do in a stop is to change this average, change it so the molecules of the car still move in every possible direction and speed, but their average balances out to zero relative to the road surface. That means the brakes have to increase the average speed of (let’s suppose the car weighs 4000 pounds) two tons of surrounding and bypassed air by 60 mph, or one ton by 120 mph, and so on.
The heat of any object is the average speed of its constituent molecules, plain and simple, whatever the material, cast iron, engine coolant or air or anything else. The brake system includes all the vehicle components that convert movement into heat at the friction surfaces, the pads and rotors, and from them into the air. Each of the vented rotors includes vanes between the surfaces that function just like the impeller in a water pump, flinging air at the center of the hub outward through the disk and drawing fresh air from the underside of the car to the center of the hub. Heat dissipation occurs, then, by conduction into the adjacent metal parts, and by radiation into space, but mostly by convection (and forced convection) into the air. As a car slows, it blows whirling plumes of hot air through each of its wheels, air drawn from under the car, forced through and around the disks and out to the sides.
Brakes don’t just slow cars from cruise speed, however. Perhaps the hardest stress on a brake system comes as a car descends a long, steep mountain. The driver doesn’t stop the car but uses the service brakes (hopefully in conjunction with engine braking) to govern the descent speed. In this case, the amount of energy is not just what the engine produced to bring the speed up to cruise, but all the power that went into lifting the car up the other side of the mountain. All of that energy must flow through the brake system, translated by friction from kinetic energy to heat in the ambient air. This extraction of stored energy by gravity is the same source that spins turbines in hydroelectric dams or accelerates a roller-coaster downhill, except (until we start using hybrid gas/electric cars with electric regenerative braking) the car must just dissipate that power.
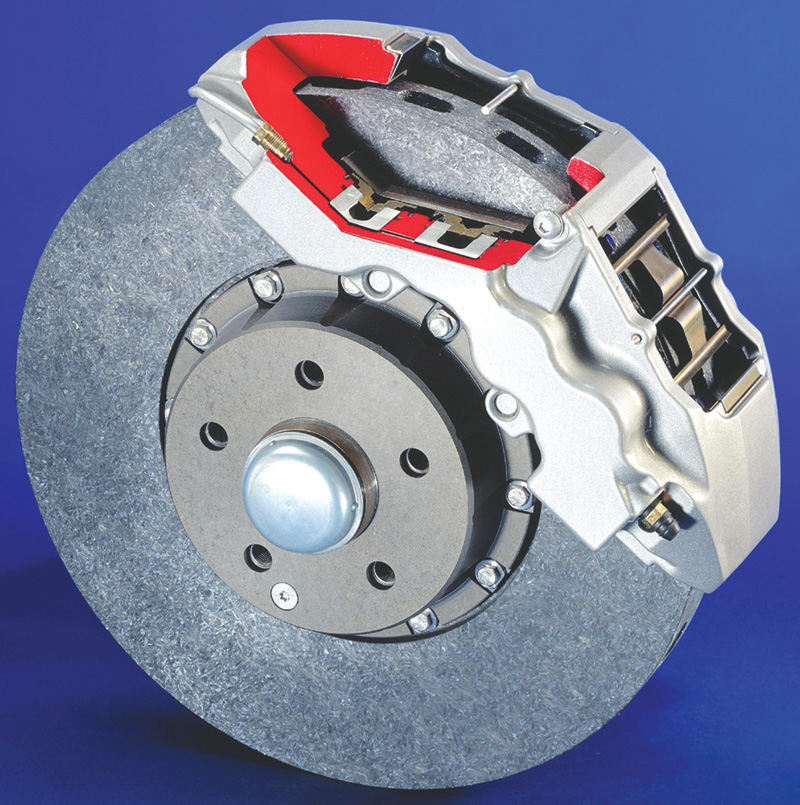
Brake development continues. In this proposed carbon-ceramic brake, both pad and rotor are made from the black, fibrous material. Carbon is remarkably strong and heat resistant, but the manufacturing techniques took a long time to perfect. Its major advantage over a steel rotor is weight: The carbon-ceramic disk weighs only about a third what the traditional brake disk does. That allows many suspension improvements, because that mass comes entirely out of unsprung weight, smoothing the ride and improving the traction.
For effective brake design and materials selection, a carmaker must make very extensive tests, varying the dimensions and geometry of the mechanical and hydraulic components, experimenting with different pad compositions and rotor surface qualities. This can be tedious work, since there are so many variables to test. There are more objectives than just braking power, considerations like the mechanical strength of the components, the durability of the friction surfaces, noise attenuation, the consistent increase of friction with greater hydraulic pressure. Few brake-test experiments involve white-knuckled emergency stops from high speeds; many record nothing beyond the gradual buildup of brake heat over a measured series of modest brake applications to determine just how fast the brakes can dissipate heat in ordinary driving conditions.
But in all of the completed brake systems, the free circulation of air through and around the disks and through the wheels is critical. Yes, the car could make a single emergency stop even if the brakes simply retained all the heat they generated. But it couldn’t make another stop in any reasonable time after the first, and it could not control a long downhill speed with the brakes.
0 Comments