It’s not always easy to check something simple
In days of techno-yore, when carburetors mixed the fuel and air for an engine’s intake, you could usually check for fuel with a glance at the dash gauge followed by a look down the venturi as you cycled the linkage. If you saw a squirt from the acceleration-enrichment pump nozzle, there was fuel; otherwise, the bowl was empty. Then the question was why.
Fuel injection brought many combustion and emissions advantages, but it did not bring diagnostic simplicity. You still glance at the dash gauge first (and if a functional Benz gauge says the tank is empty, it’s empty), but you need more than your eyes and fingers to check fuel delivery now. If you don’t find the right pressure and volume, of course, the question is still why.
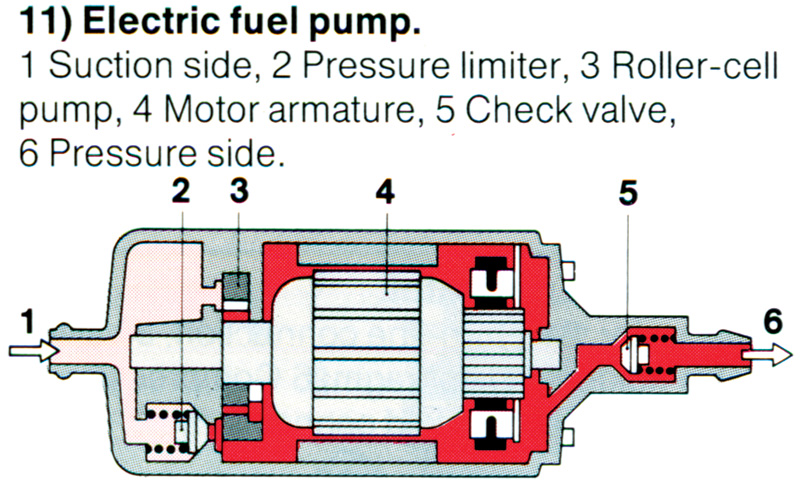
The electric fuel pump used for fuel injection is an electric motor and a meshed lobe or roller forced-displacement pump running in and cooled by the fuel. Wear points include the brushes and commutator at the pressured end of the armature, the bearings at either end, the check valve and the pressure relief. With enough grit in the fuel, there could even be wear of the lobes or rollers themselves.
The tools necessary are a fuel pressure gauge and suitable adapter fittings, a graduated two-liter flask or beaker, a switchable electric jumper (like a remote starter button), a clock with a second hand, and (for many models) a hand-actuated vacuum pump and gauge. You also need to know what to do with them, which is our business here. Finally, though we certainly hope it’s permanently unnecessary, have a fire extinguisher within reach. For safety, disable spark and any other source of flame. Don’t smoke or let anyone else smoke nearby. There’s a lot of heat energy in sprayed gasoline, and it catches fire very easily. That’s why we suggest the pushbutton jumper – if you suddenly jump back, the pump stops.
Generally, we think of pressure and volume tests as the procedure to check the fuel pump. That’s true, of course, but that’s not all. Those people who think working on cars is easy now because ‘the computer detects the problem and tells you what to replace,’ should consider what you can find with pressure and volume tests, neither one of them from the computer. Ten potential problems immediately sprung to mind, though pinpoint tests remain on the agenda to determine which. You can probably think of more:
-
As on an oil pump, the armature is slightly eccentric to the pump housing centerline, so the rollers move in and out as the armature turns, forcing fuel by positive displacement through the fuel filter and through the supply lines to the fuel rail and injectors. Wear or scoring on the lobes, rollers or races allows fuel to bleed back toward the low-pressure side.
The fuel pump. An electric motor coupled with a roller pump, the fuel pump lasts a long time. But not, usually, as long as a car. Bearings, brushes and the commutator all wear; the check valve may develop leak back after time. How long the pump lasts depends largely on the quality of fuel, but you can begin to wonder about a pump when a car has between 100 and 200 K on the odo-clock.
- The fuel filter. Current fuel filters can contain an amazing amount of dirt and grit before they clog up, and modern fuels are cleaner than ever. But some people still manage to collect enough debris into their tank to block passages. A motorist who regularly uses offbrand fuel or drove with the tank filler cap open for a time is a good candidate for a new filter.
- The fuel pressure regulator. If it spills fuel back through the return line before there’s enough pressure, a bad regulator can prevent starting or cause reduced power at every throttle setting. Like a defective check valve in a pump, a defective pressure regulator can dump system pressure right after the engine shuts down, requiring a long crank to restart.
- The fuel lines. The most obvious loss of pressure and volume comes with an active leak, but that’s rarely hard to diagnose. A more subtle and difficult problem comes with an air leak upstream of the pump, drawing in bubbles to displace fuel and absorb pressure.
- The fuel injectors. If you clamp off the return line to eliminate the regulator from question, know the pump holds pressure but observe loss of pressure in the fuel rail beginning with shutoff, you have good reason to suspect one or more injectors of leaking.
- The fuel sock and pickup. Most problems with these components arise after a tankful of dubious gasoline, leaving a coating on the initial filter and blocking suction to the pump. Sometimes you may discover problems resulting from earlier work in the tank.
- The fuel tank. Some cracks or broken welds at the top of a fuel tank can go unnoticed since there’s no visible leak, but they can allow moisture into the unprotected steel interior, producing rust that abrades the pump’s working surfaces and plugs the filter.
- The vapor/evap system. If a car has good pressure and volume to begin with but gradually loses both as it travels a hundred miles or so, the fuel delivery problem may not arise from the pump but from a plugged vapor/evap system vent. That can produce a vacuum in the tank working against the pump, enough of a vacuum sometimes to let the fuel vaporize at the pump intake.
- The pressure retention valves. The regulator and the pump contain check valves and pressure limiting valves that can allow pressure loss if the seal between their mating surfaces becomes pitted or a piece of grit lodges in between.
- The electrical circuit. If there is notable resistance on the power line to the pump or on the ground line returning the current, that resistance effectively throttles the electric motor down, reducing both speed and torque. It doesn’t take much loss of electrical power to drop the pump below minimum delivery thresholds.
Keep in mind the delivery specifications are not approximations and rough guesses. If the pressure doesn’t reach the minimum, the injectors may deliver no fuel at all. If the volume isn’t enough, the car will run out of power before the pedal runs out of travel. Be sure the pressure reaches the specified level and there is the specified amount of fuel in the beaker within the time limit.
The general procedure is this: Connect the pressure gauge to the test port following the diagrams for that model; clamp off the return line with a suitable, non-damaging clamp; route the line into a suitable graduated container.
When you complete a fuel pressure and volume test, make perfectly certain all the fuel lines you opened are securely sealed, without the slightest seepage of fuel. As dangerous as a fuel fire is in a shop with knowledgeable professionals available to put it out, it’s much more so as a surprise on the road with no equipment or people to extinguish any flame.
In following issues we’ll cover fuel pressure and volume tests model by model.
0 Comments