Throughout its history, BMW has been in the forefront of engine innovations and has won many awards for clever, sophisticated designs. From our discussions with service professionals who work on these cars, they’ve also garnered a reputation as having great general durability and very few particular internal engine problems. But any mechanism more complicated than an anvil will eventually wear out or break. When that finally happens, typically after propelling the vehicle for many years and a great number of miles (you have, of course, noticed that people are driving their cars up to mileages that would’ve been unthinkable a couple of decades ago), you’ll be presented with the challenge of finding out what, exactly, has failed, and a mistaken diagnosis would be an embarrassing blotch on your reputation.
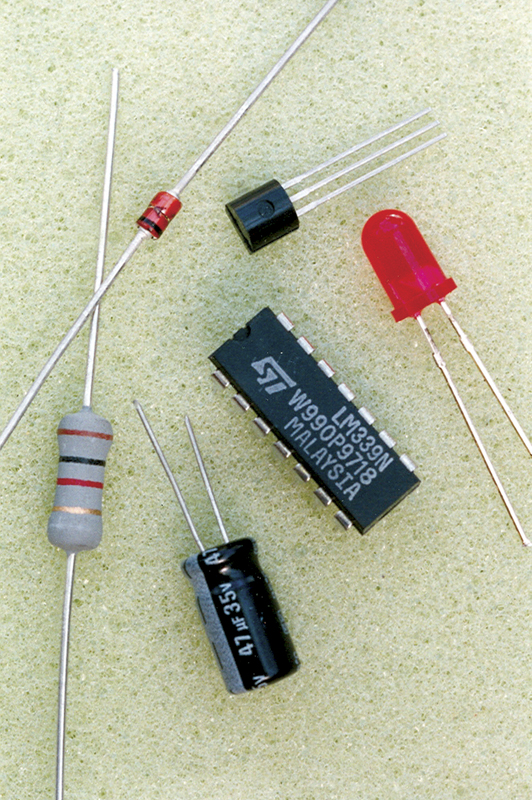
All the electronics in the world can’t make up for a serious internal engine problem. So, make sure your customer understands that changing plugs, replacing sensors, or reflashing the computer won’t help. He or she needs a skilled tech to get inside and fix actual metal parts.
Consider also that what made a person an “A” technician in the past was consummate skill in internal engine diagnosis and repair. Today, that’s been skewed to refer to the ability to troubleshoot electronic engine management systems, but motor work is still part of the “A” package.
Big Picture
As with all repairs, careful communication with the customer at the outset is of primary importance, and that’s especially so given the high costs involved in this kind of work. What, specifically, is the complaint? Rough idling, high oil consumption, noises, poor performance and puddles of oil on the driveway are probably the most common symptoms of something amiss in the engine assembly. Taking a test drive with the car’s owner aboard will help prevent misunderstandings.
Next, we all should remember to step back and look at the big picture before we jump to any unfortunate conclusions. For example, we recently had a European OHC V8 in our shop with a low-power, rough-running complaint. The car was in beautiful condition otherwise, so we jumped right into our standard diagnostic mode, neglecting to note the odometer reading. After wasting quite a bit of time, we finally noticed the mileage – 243,000! No mystery then that the nylon timing chain tensioning components should have disintegrated. Lesson: Look at the big picture. Besides mileage, how was it maintained? Has anybody else ever been inside that motor? What kind of driving has the vehicle been subjected to (long-trip cruising takes a lower toll than commuting in stop-and-go traffic, or short hops)?
A bulletin search is another crucial preliminary. It would be pretty embarrassing to miss a pattern failure.
One of the keys to successful internal engine diagnosis is how much ground work you do before rendering the engine inoperable. The best “major men” we know all commented that getting as much information as possible from the full assembly prior to teardown gave them the best chance at locating and repairing the problem once they were down to the dirty parts.
First, compression
Compression:Â You can’t leave home without it. It’s one leg of the tripod that supports internal combustion, just as important as fuel and ignition. Regardless of all the gee-whiz technology in modern engines, that basic physical fact is exactly the same now as it was well over a century ago when the Otto cycle was invented. So, underneath that high-tech exterior there’s still just a piston pump.
Sure, today’s cars typically go a long, long way before they develop conditions that reduce compression. But the key word here is “typically” — there will always be plenty of exceptions. Then there are vehicles that have exceeded that long, long way, but are still worth fixing. BMWs are a prime example of that. People love them, so will commonly want to get them back up to snuff at any price.
As far as probabilities are concerned, the most likely culprits are burned valves, a violated head/block seal, valve train or lift troubles, failed rings, and damaged pistons, in that order.
Listen up
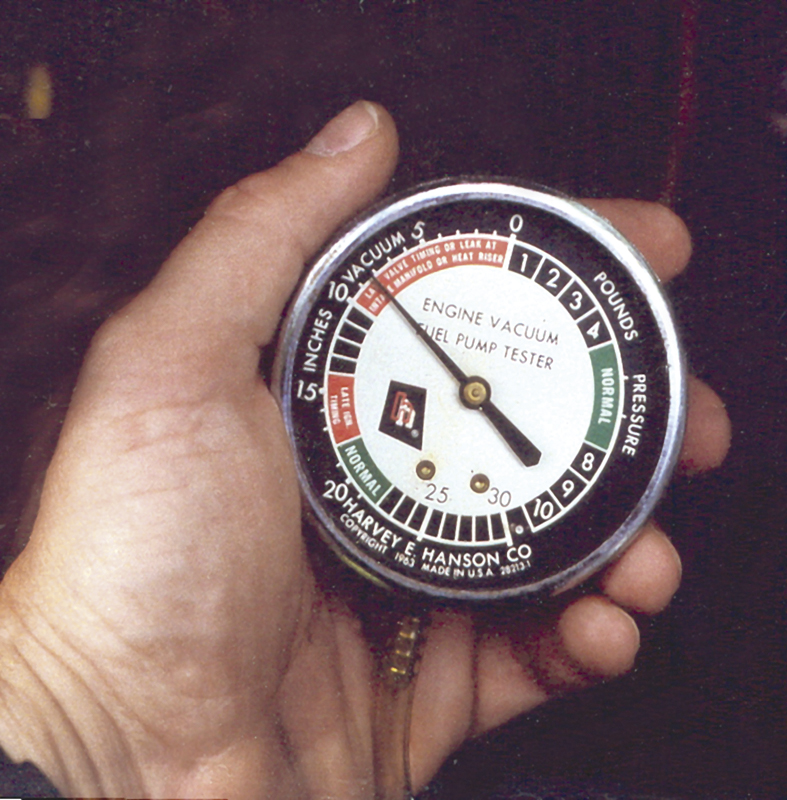
Although the results will usually be inconclusive, the use of an old-fashioned vacuum gauge can at least give you an idea of an engine’s pumping ability.
The first thing to do is listen carefully, both to what your brain is trying to tell you about the symptoms and to the powerplant itself. Asking a few question in your head will help: Is the idle uneven? Are power and fuel mileage declining? Does it smoke and use a lot of oil? How about backfiring, hard starting, or high emissions that resulted in failure of a pollution test? Start it up and note if it cranks unevenly or takes a long time to fire up, both of which suggest poor compression.
Use your scope to find out if the ignition system is in good shape — we’ve seen heads pulled when the real culprit was a bad plug, wire, or cap. Then, do electronic or relative compression and cylinder balance tests.
Of course, many old-fashioned technicians like to get an initial idea of the situation with a manual cylinder balance check. Pulling one plug wire at a time to find out if a particular hole has little or no effect on idle quality and speed when disabled is about the most useful troubleshooting trick known to man for older cars, especially where there’s a definite miss. That is, if you remember to disable whatever computerized idle stabilization device is present. And use well-insulated boot pliers or that hot-stuff electronic ignition might blow your pacemaker. With coil-over direct ignition, of course, this isn’t so easy anymore. Where possible, kill injection instead of spark.
Sucker
A vacuum gauge can be helpful at this point, although its readings may be inconclusive or ambiguous. You’ll get the most useful results at curb idle speed with the engine fully warmed up. A typical healthy powerplant will produce 15-20 in. Hg.
A steady low reading may be caused by a vacuum leak or late valve timing due to a worn or jumped camshaft drive mechanism. If the needle drops at regular intervals, suspect a leaking valve, whereas if such drops occur irregularly, a sticking valve is indicated. Floating over a wide range suggests a bad head gasket seal. Rapid needle vibration is evidence of loose valve guides.
Since backpressure can interfere with cylinder filling, check for a clogged catalytic converter or crimped pipe by holding 2,500 rpm. The reading will drop when you first open the throttle, then stabilize. If it starts to fall afterwards, there’s probably an exhaust restriction.
Squeezability
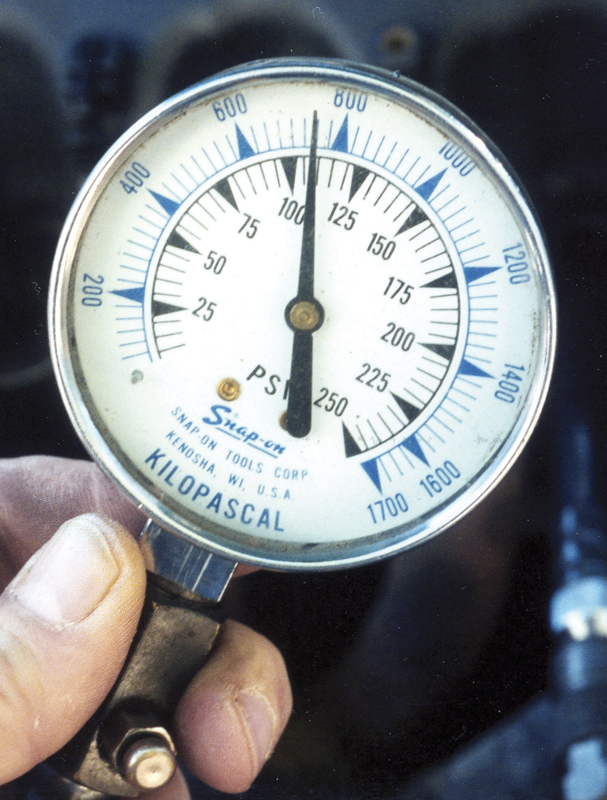
There’s still nothing that can give you such a good inside picture of the pressure tightness of that cylinder than the traditional dry/wet compression test. But don’t just look at the max reading. Instead, observe how the needle jumps with each of four impulses.
Whether or not you’ve isolated a cylinder or two as the source of the problem, it’s time to unscrew the spark plugs and do a traditional dry/wet compression test. Old hat? Maybe, but a medical analogy we’ve run into is apt: A fellow automotive editor had a routine check up, and his cardiogram (a very simple, quick test) showed a problem. His cardiologist ordered a stress test, an echo cardiogram, then a nuclear stress test. Nothing further showed up — in fact, the patient scored very well on all counts. But the cardiologist was like a good mechanic. He said no matter what the high-tech exams had shown, the old-fashioned cardiogram had indicated trouble, so something was wrong. He sent the man to have a heart catherization (also called an angiogram, it’s the gold standard of cardiac tests), which showed that there was an 80% blockage in the “widow maker” artery. In other words, if that were to occlude, there would be no chance of survival. They installed a stent, and the man is healthy today. So, the old-fashioned cardiogram probably saved his life. The situation with the compression test is similar. You’ll know if there’s a problem even if nothing else says so.
You already know how to do a compression test, of course, but here are a few subtleties that’ll help you avoid a costly mistake:
- On aluminum heads, better loosen those plugs with the engine cold, then just snug them back down enough to fire it up.
- Readings will only be accurate at normal operating temperature.
- Blow out the plug wells or flotsam and jetsam could hold a good valve off its seat.
- Pull all the plugs at once to make cranking easier.
- Make sure the battery and starter are up to the task of achieving normal cranking rpm.
- Block open the throttle plate.
- Disable the ignition, preferably on the primary side. Letting those dangling wires arc won’t only zap the secondary circuit components with more voltage than they might be able to take, it’s also asking for an explosion.
- Even though the clear-flood mode is supposed to halt injection during WOT (Wide Open Throttle) crank, you can be doubly certain to eliminate gasoline spray by shutting down the fuel pump and blowing the residual pressure through the rail’s test Schrader into a rag, or by unhooking injector connectors.
- To do the test right, you need at least four pulses per cylinder
Record the first and fourth pushes of the needle. Why? Let’s assume a normal reading of 185 psi. A constant (unwanted) hole in the cylinder will allow pressure to built uniformly with each push. For example, you may see 30-60-90-120. This tells you that the leak is there all the time and is uniform in size — a burnt valve, perhaps, or a badly blown gasket. On the other hand, 90-100-110-120 tells you that the cylinder is sealed up to a point, after which something breaks down or leaks. This is typically how rings fail, but a leaky head gasket will also behave this way. As a rule, the first push should be half or more of the fourth push. For our 185 psi cylinder, we’d expect to see 120-145-165-185, or thereabouts.
Test dry, then wet — add a tablespoon of oil to each cylinder. Wet testing isn’t always effective, however, because the oil may not get evenly distributed around the top ring, especially on “V”-type engines. If a low reading jumps substantially after the addition of a few squirts of oil, you’ve got a ring/bore problem. On the other hand, if wet readings are only slightly higher, and this rise is roughly the same for all cylinders, valves are implicated.
The difficult part is judging how much variation among cylinders, or between dry and wet readings, represents a serious problem. Say you’ve got 80 psi in one, but about 120 in the others, and adding oil brings them up only five psi or so. Is a valve job necessary?
That depends. Obviously, the low one is leaking somewhere, probably through an exhaust valve, and erosion is going to make it get worse pretty rapidly, so the proper thing to do is get in there and attend to the seats and faces. On the other hand, if it’s not bad enough to cause a miss yet, and the customer has been frittering away his or her money on luxuries like food and shelter and can’t afford major work this month, maybe he or she can simply live with it. Just make sure the customer understands that no amount of tuning or other external attention will make that engine run any better or go any farther before that cylinder loses it altogether. At least there’s some good news — the rings are okay.
Poor pressure in two adjacent cylinders should make you think about a blown head gasket. Confirm this by looking for coolant in the oil or on the spark plug, and by checking for evidence of compression in the cooling system. Hold the probe of an exhaust analyzer over the radiator filler neck to see if you get an HC reading, or remove the thermostat housing and water pump belt, then watch for bubbles. Another possibility is one of those water-filled testers you stick in the radiator neck — again, bubbles are the tip off.
Hissssss
Gauging compression isn’t the only time-honored procedure that’s still useful for assessing an engine’s ability to squeeze air. There’s also the cylinder leakage test, which is done by pumping maybe 90 psi into the spark plug hole with the valves closed, and listening to where it escapes. Hissing at the intake points to the inlet valve, and the same sound at the tailpipe indicates the exhaust.
There’ll always be some noise at the oil filler hole because even the best rings can’t seal completely (gaps, you know). The trick is to tell when it’s excessive, which you can probably do by comparing cylinders. And this test is great for fingering a leaky head gasket — remove the radiator cap and listen.
An improvement on this theme is the use of a gauge that lets you know what percentage of the available pressure is escaping, which is called a cylinder leak-down test. With the plugs out, bump the engine over until the cylinder in question is at TDC of its compression stroke. Use a regulated air supply of 70 to 100 psi, which you compare to the pressure the cylinder is capable of holding. Older engines tend to run some pretty high leakage numbers, so look for consistency and don’t worry too much about those big numbers if the engine is running smoothly at idle. We’ve seen engines with uniform leakage numbers of 50% perform just fine. We’ve also tried to fix those numbers, and found out that going from 50% to 20-25% made no appreciable difference in the way the engine ran. Newer engines typically produce low numbers — under 10%. If you get a high reading on a cylinder with no recorded misfires, check for carbon. Crank the engine over a few times to dislodge particles and repeat the test. If the numbers come down, you may be fighting carbon.
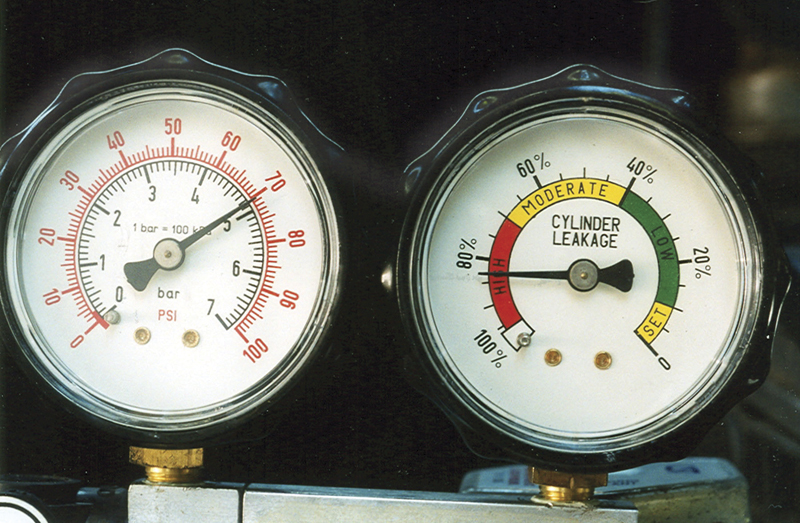
Another excellent troubleshooting procedure is the cylinder leak-down test. The gauge set lets you know what percentage of the pressure being pumped into the cylinder is escaping.
Since you need to be at TDC only to get both valves closed, on a lot of late models with negative overlap it’s tempting to try to do two at once. But with only a few degrees of negative overlap sometimes there’s not enough seating pressure to get a good reading.
There’s more to throw into your mental threshing machine before you make your grand diagnostic pronouncement. Anything that holds a valve open, such as a broken spring or a sticking guide, will certainly cause a low compression reading. While these can usually be fixed without removing the head, chances are the valve is burned to a crisp (it can only cool when closed, after all) and/or bent. You can try making the repair and see what happens, but there’s no guarantee of success.
Low cylinders that don’t produce more pressure after oil has been introduced into them may not have valve sealing trouble. A wiped cam lobe or other valve train failure can result in a miss because the cylinder isn’t being properly packed. Check lift before you start unscrewing head bolts.
Absolutely no compression in a cylinder does not necessarily mean a valve is stuck open or burned away, either. There could be a hole in the piston, and we remember an engine that was still running, albeit roughly, even though the piston was entirely gone along with the whole rod so that when we yanked the head we were looking down on what was left of the crank pin.
In cases where the car suddenly refused to start and you got weird compression readings, a snapped OHC drive belt or a jumped timing chain is a more likely possibility than bad valves, which deteriorate gradually. If the powerplant isn’t freewheeling (that is, the valves hit the pistons if they’re out of synch), however, you’re going to have to remove the head anyway for the replacement of some bent stems.
Knockers
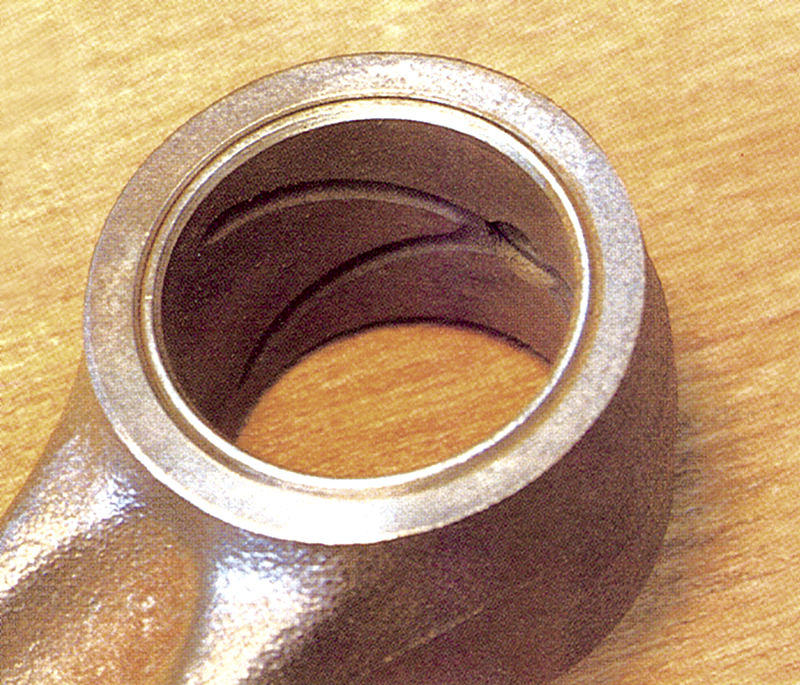
Many a technician has been embarrassed (and probably ridiculed) for mistaking a rod small-end bushing knock for a loose rod bearing. Follow the procedure and you can be pretty sure of your diagnosis. One good thing: After you drop the pan and remove the rod caps, you’ll know if the bearings are okay. If so, you’ll just have to escalate your estimate to include engine R&R.
The sound is distinctive — a deep, hollow rap, not at all like valve train click-clacking. The universal term for this disturbing noise is knocking, and it’s perfectly appropriate because it makes you think of knuckles on a wooden door. And it’s a pretty sure indication of a problem in the engine’s foundation, the precursor of certain catastrophe.
But conclusion jumping is a dangerous sport. Your plans for a simple rod bearing job will have to be greatly modified if the crank turns out to be bad, the rod big ends are stretched so there’s no crush factor to keep the bearings from spinning, or the knock is really emanating from a sloppy wrist pin fit.
Identifying the source of that nerve-jarring rap can be tricky, and the biggest challenge is distinguishing between a loose rod bearing and a worn-out wrist pin. It’s indeed unfortunate that one sounds pretty much like the other.
With a little patience, however, you should be able to determine what’s at fault. Start your investigation by pulling the dipstick to find out the condition and level of that all-important liquid lube. Then, use a stethoscope to listen to the engine while it’s idling hot. A rod bearing makes more noise at the oil pan than elsewhere, and a wrist pin will make more racket up on the water jacket. Hold rpm at 2,500, jerk the throttle open and let it snap closed. This will accentuate rod knock, whereas pin noise won’t change very much.
Oil pressure
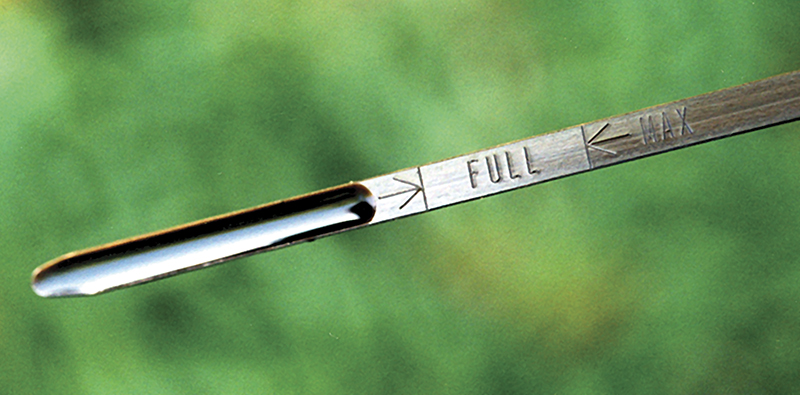
What’s in the crankcase, anyway? Either too thick or too thin is a big problem. Think gasoline contamination (in the days of carburetors, we used to try to light the dipstick), or lack of maintenance that turns motor oil into tar. Your oil pressure readings will vary accordingly.
Next, check oil pressure by screwing in a mechanical gauge. Specifications are usually given hot, at idle and between 2,000 and 2,500 rpm. Why low and high speed? Pump speed naturally affects the volume pumped, and, of course, an oil pump generates volume only. Pressure is built by trying to push that volume through small spaces, such as the bearing clearances. Because the pump is of the positive-displacement variety, it’ll move anything you put into it, pressure will rise as the discharge is restricted up to the set point of the pressure relief valve. The old standard of 10 psi per thousand rpm still works fairly well, but in an effort to reduce horsepower losses, late models often have reduced maximum pressures. Always refer to specs.
Make sure you’ve let it run for plenty of time before you render a verdict — 50 psi cold can turn into 5 psi hot. Also, don’t rule out a pump or bypass relief valve problem or the presence of low viscosity oil (we once knew a guy who liked to fill his crankcase with ATF). The relationship of flow to bearing clearance is important. Assuming that normal clearance is .001 in., flow will increase by a factor of five if you just double the clearance to .002. If you go to .004, oil flow increases by a factor of 25. Sooner or later, the pump’s volume is exhausted, pressure drops and the light comes on.
If the pressure fluctuates, think low level, entrained air or suction leaks. Maybe the pan is running dry due to the installation of a high-volume pump. Or, perhaps a massive internal leak is draining the pan. A high-volume pump needs more pan capacity because at high rpm the oil is pulled out of the pan and held in windage. The oiling system is just that: a system. More is not always better unless all the components are matched. Any suction leak between the oil pickup and the pump will create fluctuations, as will air pulled in due to excess flow through worn-out bearings that sucks the pan dry.
If oil pressure is low all the time, suspect an internal leak such as bad bearings, or a leaky oil gallery plug. A worn-out oil pump can cause low psi, but as it’s the best-oiled piece in the machine it’s not a good sign for the rest of the internals.
If pressure’s low at idle, but okay at high rpm, the pressure relief valve is probably stuck open. In cases where the psi is fine at idle, but low at high rpm, think restricted pickup screen, although a suction leak could be the culprit. Pressure high all the time? The relief valve is probably stuck shut, which can blow the filter.
Carbon knock
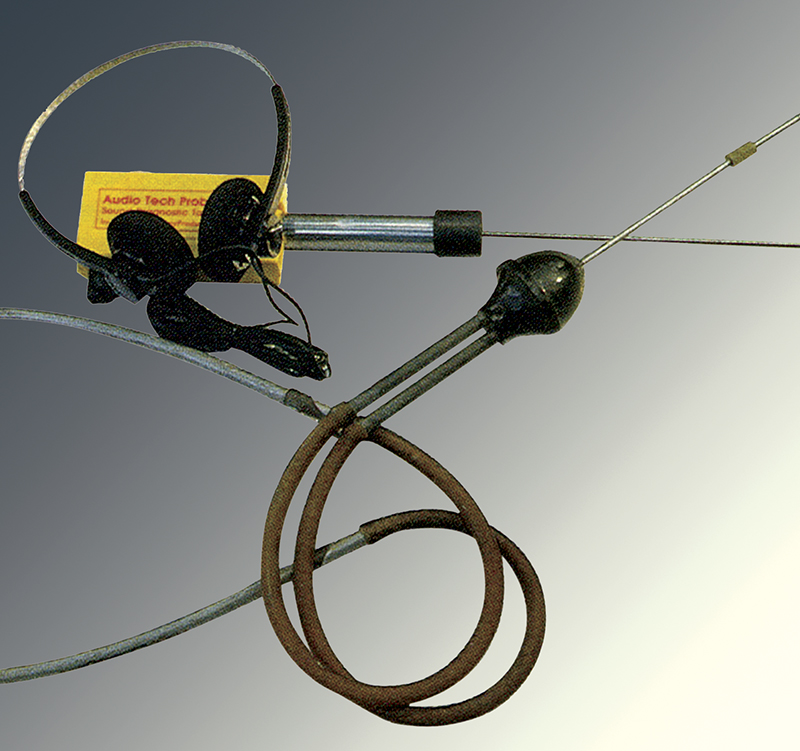
Whether the surgical tubing and diaphragm type, or one of the new electronic amplified versions, a mechanic’s stethoscope is about as indispensable as it gets where nailing down noises is concerned.
Killing cylinders, either with a scan tool or manually, is often mandatory for nailing down the offender. A rod knock tends to quiet down with the cylinder killed, but a pin tends to get louder. Still sounds the same? You may be dealing with a carbon knock. If a heavy carbon ridge has formed above the top of piston travel, it can eventually force a violent rock-over, producing a harsh, loud piston-slap type of noise. Also, carbon can build up in the quench areas to the extent that the piston actually contacts it at TDC, which causes a mechanical knock or even a slap knock. In the early stages, a carbon knock will mimic a slap in that it will go away as the temperature comes up.
We’ve seen enough of this lately to recommend de-carbonizing as a first step. You may have to treat the engine two or three times. If you’ve worked on BMWs long enough, you may remember the walnut shell blasting method of removing carbon, which the company approved a couple of decades ago. Today, we have such good chemical intake tract and combustion chamber cleaning systems that everybody’s abandoned the walnut shell method.
One of the techniques used to find out if that noise is carbon-related is the floating throttle rev test. Take the engine up to about 2,000 rpm, snap the throttle open to increase cylinder pressure, then rapidly close it to pull high intake vacuum. Watch that rpm — it’s easy to over-speed the engine. What you’re trying to accomplish is loading and unloading the pistons, pins and rod bearings. You have to do this rapidly, about two or three times per second, from snap open to closed in order to achieve maximum load. If there’s mechanical looseness in the rod/piston/pin, the rap will get a lot louder as you do this. If the noise remains constant (other than going away some as it heats up), it’s probably carbon.
Lube in the fire
Finally, as we all know, excessive oil consumption is usually due to bad valve stem seals or guides. But not always — rings still fail. Unfortunately, you can’t check an oil control ring because it’s the third one down. The compression rings may be fine, but the oil ring may be varnished, jammed, or “unitized.” Valve guides or seals also cannot be effectively tested. As a rule, if it smokes on start-up or after a long, hard decel, it’s probably guides or seals. If it smokes on acceleration, it’s probably rings.Â
0 Comments