Getting an engine to run is easy. All you have to do is provide the right amount of fuel, mix it with the right amount of air, compress this mixture to a fraction of its normal volume, fire the spark plug at exactly the right time to ignite the air/fuel mixture, and you have a running engine.
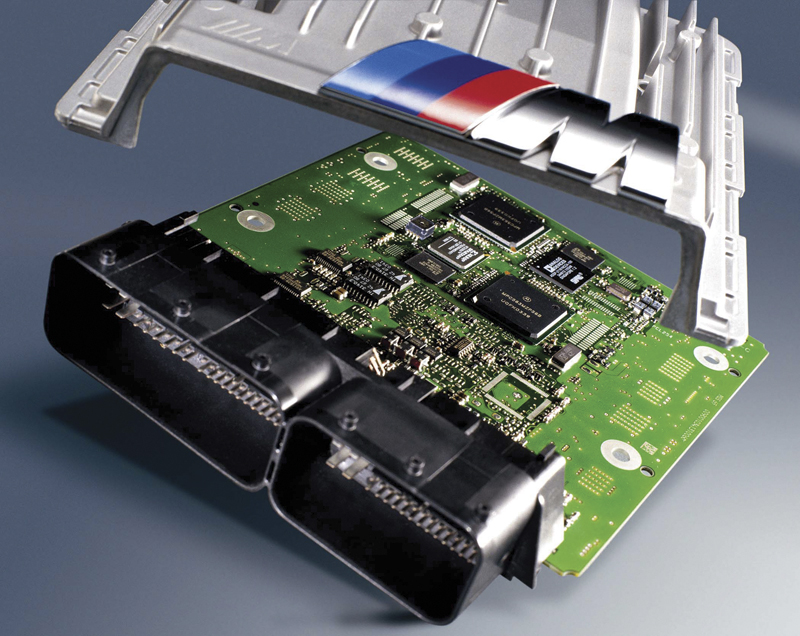
Of course, nothing would happen if the ECM/PCM didn’t complete the circuits to the fuel pump and the injectors by providing ground. Still, look for other problems before condemning this dependable (and expensive) component.
Okay, so it really isn’t that easy. Modern BMW engines are carefully designed to provide optimal performance and minimal emissions across their entire operating range. Precise amounts of fuel and air must be present in the combustion chamber when the plug fires to provide the performance BMW owners expect, and to meet the emission levels the government demands. Fuel, air, and spark are equally critical. A problem with any of the three will cut performance and possibly prevent the engine from running at all. This article covers troubleshooting the typical return-type fuel system; future articles will cover returnless EFI, air management and ignition systems.
On BMWs, the Engine Control Module or ECM (called by BMW the DME and also known generically as the PCM for Powertrain Control Module) regulates fuel pump operation and the amount of fuel entering the combustion chamber, but it does not monitor actual fuel delivery. In other words, the onboard computer system turns the fuel pump on and off, and precisely controls injector operation, but there is no sensor to actually detect fuel flow.
Be safe
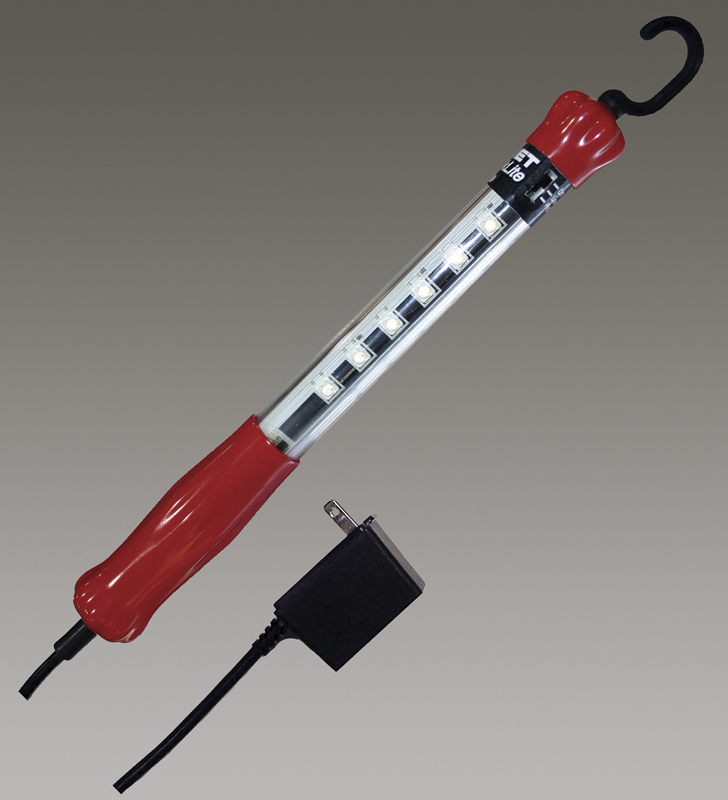
Most auto repair shop fires are started by droplights. So, use the fluorescent or LED type when working on the fuel system (courtesy Ferret Instruments).
Remember, gasoline likes to burn — in fact, it really has no other purpose except to catch fire and burn rapidly, almost explosively. It doesn’t matter to the gasoline where it burns. Inside an engine’s cylinders is no better a place than under the hood, on your clothes, or all over the shop. Always observe all the safety rules whenever you are working on the fuel system:
- Have a fire extinguisher handy.
- Never smoke or have any open flame near gasoline.
- Make sure other technicians in the area are not smoking, using a grinding wheel, or creating a spark.
- Always store gasoline in an approved safety container.
- Make sure your work area is well ventilated
- Use a fluorescent or LED droplight, never the kind with a regular incandescent bulb. It’s a fact: More shops burn because of droplights than from any other cause.
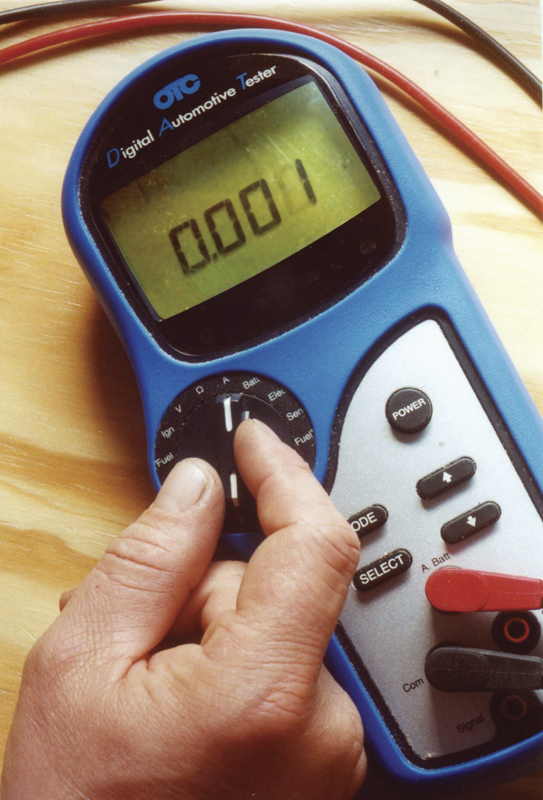
Although not as impressive as a lab scope or a scan tool, a good DMM will always tell you the truth — if you know how to use it.
Several special tools are needed to efficiently diagnose BMW fuel delivery problems, including:
- The Modic/DIS/GT1 (BMW offers Online Diagnostics as a low-cost alternative. Go to www.bmwtechinfo.com).
- A good digital multimeter (DMM).
- BMW’s Universal Adapter (Part Number 88 88 6 614 410), which makes it easy to test connections with out damaging the pins or harness.
- The Fuel Hose Clamp Tool (Part Number 13 3 010).
- The Relay Bypass Switch (Part Number 61 3 050) should be used when fuel vapors are present. The switch eliminates the risk of electrical arcing.
- Check fuel pressure with the handheld fuel pressure gauge (Part Number 13 3 060), or equivalent.
- Special Tool (Part Number 13 5 270) is used on systems with “quick release†couplings between the fuel filter and the pressure supply hose.
- Adapter (Part Number 13 5 220) is used on systems with a treaded fitting on the fuel rail.
- Injector leak down is tested using Special Tool (Part Number 88 88 5 000 362).
Fuel system basics
BMW now uses polyethylene fuel tanks to reduce weight and eliminate the possibility of corrosion, which can introduce rust flakes into the system. Early SULEV/PZEV vehicles (M56 engine) used a stainless steel fuel tank. All late models have a “saddle tank†that straddles the drive shaft. This design allows for a lower profile, space saving tank, but it creates two low spots, one on each side of the drive shaft. Instead of using two fuel pumps, a single electric pump is in the right (passenger) side. Gasoline in the left (driver) side of the tank flows to the right side via a siphon tube.
When the ignition key is turned to “on†the ECM energizes the fuel pump by completing its ground. This primes or pressurizes the fuel system. However, if the ECM does not receive a signal from the Crankshaft Position Sensor that the crank is indeed turning, the ground connection is broken and the pump stops running. Only if the ECM gets a signal that the engine is turning over does the fuel pump remain on. Any physical restriction upstream from the pump will cause the pump’s pressure relief valve to open.
Fuel leaves the tank, passes through the fuel filter, and pressurizes the fuel rail and injectors. A one-way check valve prevents fuel from flowing back toward the fuel pump. The check valve also helps keep the fuel rail and injectors “primed†after the engine is shut off.
In the typical return-type fuel system, the pump provides more volume and pressure than the engine requires. During normal operation, the Fuel Regulator Valve maintains the system at the required pressure and returns excess fuel to the tank. Fuel flow in the return line not only goes back to the tank, but also provides the siphon effect to draw fuel from the left side of the tank.
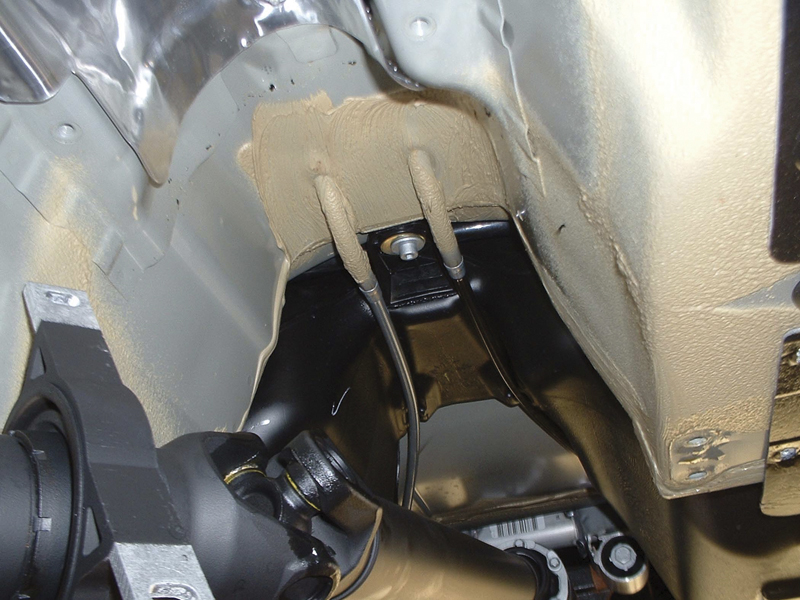
With the exhaust system and the driveshaft dropped, you can see the part of the tank that connects the two sides of the saddle.
With the fuel rail and injectors uniformly pressurized, the ECM controls the amount of gasoline injected by varying the length of time it opens the injectors by grounding their solenoid windings. This is called “pulse width,” “millisecond value,” or “ms value.” The amount of fuel that enters each cylinder is, of course, based on the computer’s programmed response to input from various engine sensors. Pulse width/ms value is determined by ECM programming and numerous inputs, including those for:
- Battery voltage
- Throttle position
- Air flow in mass
- Crankshaft position and engine rpm
- Cylinder ID
- Engine coolant temp
- Exhaust oxygen content
While cranking, battery voltage goes low, so the ECM increases the ms value to compensate for injector “lag time.†After the engine starts and battery voltage jumps to normal, the ms value is reduced because the injectors respond faster when voltage is higher.
Cold starting requires additional fuel, so the ms value is higher. The ECM adjusts ms value as signals from the Engine Coolant Temperature Sensor change.
For the first few crankshaft revolutions during cranking, additional fuel is provided by all injectors simultaneously (Parallel Operation). Then the ms value is gradually reduced as the engine comes up to speed. When the engine speed approaches idle rpm, the ECM recognizes the Camshaft Position and switches to Semi-Sequential injection.
During cold start-up, the ECM opens all injectors at the same time (Parallel Operation) for every complete revolution of the crankshaft. However, during warm-up, the ECM takes inputs from the Camshaft Position Sensor and shifts to “Semi-Sequential†operation, which times injector opening closer to intake valve opening.
When the engine is cold, optimum fuel metering is not possible due to poor air/fuel mixing and an enriched mixture is required. The Coolant Temperature input allows the ECM to adjust the injection ms value to compensate during warm up, then minimizes the injected fuel at normal engine operating temperature.
At idle, minimum fuel is needed and the ms value is low. At wide open throttle, maximum fuel is needed and the ms value increases. The exact ms value at any time is changed as inputs to the ECM change.
BMW engines are governed or limited by the ECM, which shuts off the injectors when engine speed reaches 6,500 RPM. Injector operation resumes when engine speed drops below the governed limit. The engine speed governor is independent of vehicle speed. However, this protective feature can be overrun if the engine exceeds redline because the driver missed a downshift with a manual transmission.
If there’s a malfunction in the ignition system that would cause excess unburned fuel to enter the exhaust stream, the ECM will shut down the injectors to the affected cylinders to protect the catalytic converter.
Troubleshooting
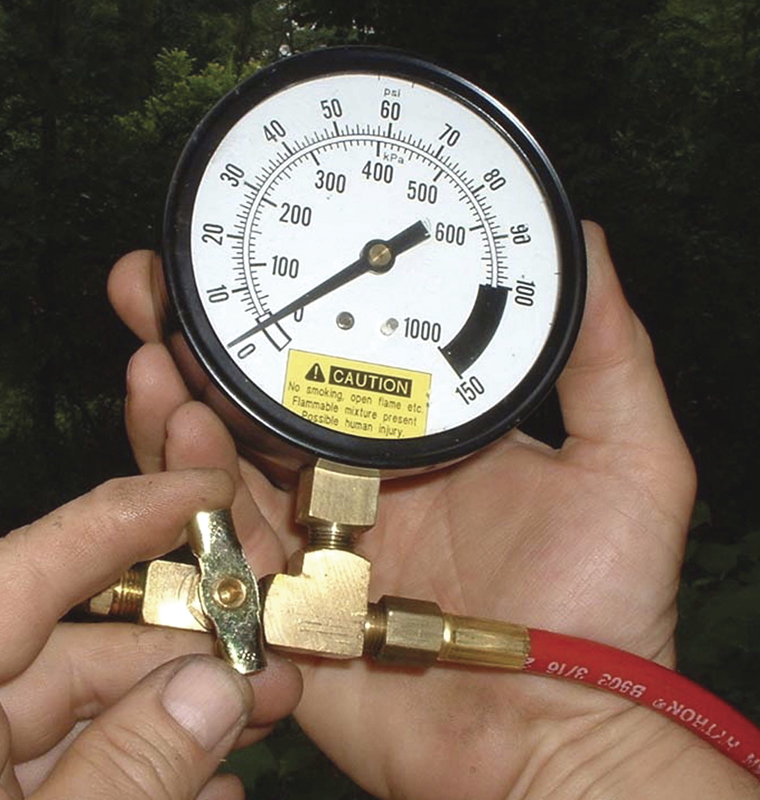
Very few troubleshooting steps can tell you more than a simple fuel pressure check. Check KOEO, running, and “dead head” (fuel pressure valve or regulator hose clamped).
A fuel delivery problem, causing a no start, hard starting, or poor performance could be caused by a defective sensor. Typically, this would trigger a code. The fuel delivery problem could also be caused by something in the fuel system that doesn’t set a code. If one or more codes are present, follow the recommended diagnostic procedure(s). But if there are no codes present, you will have to troubleshoot the fuel problem the old-fashioned way, step-by-step.
First, make sure there’s gas in the tank! Many “won’t start†and “quit running†complaints have been solved by filling up, much to the chagrin of all parties. If the fuel gauge reads empty, believe it.
Next, and especially important, test pressure by using a high-quality gauge and the correct adapter to tap into the fuel system. If fuel pressure is up to specs in all modes, that still doesn’t mean there’s enough volume. But checking the actual amount of gasoline the pump is capable of supplying is risky business — don’t blow up!
To test fuel pump pressure, install a fuel pressure gauge in the connection between the fuel filter and the fuel pressure regulator. Remove the fuel pump relay from the panel and connect the Rely Bypass Switch across terminals 87b and 30. This will allow activation of the pump without turning on the engine. If the pump doesn’t run, there is a problem in the electrical supply to the pump or the ECM is not completing the ground to the pump.
Pump output should be at least 3 bar (43.5 psi) and the volume should be at least the amount specified for the model car. If pressure or volume is low, the pump may be worn out, its electrical connections may have resistance, or perhaps there’s a blockage.
In cases of low psi and/or volume, inspect all the lines for any evidence of crushing or crimping. BMW has issued several service bulletins for various models. Consult these bulletins. Another possibility, of course, is a clogged filter. We’ve often removed them and found them so blocked that it was impossible to blow through them.
If pressure and volume are both okay, there may be a contamination problem. It doesn’t take much water (or whatever) to shut down a fuel-injected car. Draw a sample of gas from the very bottom of the tank, deposit it in a clear glass dish and inspect it. If there’s a “blob†at the bottom of the sample, you have a bad water problem. Also, any sign of rust or dirt means serious contamination.
If there’s clean gas in the tank and system pressure is normal, either there’s trouble with the ECM’s network of sensors and wiring (or, very rarely, with the ECM itself), or perhaps the injectors are plugged. While the latter condition isn’t as common as it once was, it can still happen.
On most BMWs, access panels to reach the fuel pump and sending units are under the rear seats. Remove the seat cushions to get access to the tank. There are two panels on the “saddle†tanks, the driver side panel is for the siphon tube and one sending unit. The passenger side panel accesses the fuel pump, pump pickup, and pump filter. On SULEV/PZEV vehicles, the fuel pump, carbon canister, and other components are permanently sealed inside the fuel tank. These components cannot be serviced separately.
When the pump is off, pressure should be maintained in the system. If more than .5 bar (7 psi) bleed-off is observed in five minutes, the injectors may be leaking, or the fuel pressure regulator may be sticking open.
The Fuel Pressure Regulator should only open when the pressure in the fuel rail exceeds 3 bar. The regulator should remain closed when the engine is off to keep pressure in the rail. If there is fuel flow back to the tank after the engine is shut off, the regulator is sticking open.
Over the years, various tools have been available for testing injector leakage. In one type, you immerse the injector tip in water, then pressurize the injector with shop air and watch for bubbles.
0 Comments