Soon, diagnosing a charging system will no longer be just about testing alternator output. Energy savings and management protocols such as BMW’s Intelligent Alternator Control (IAC), which will appear on some models in the near future, have placed the Digital Motor Electronics (DME) in full control of charging. Monitoring of operating conditions, current flowing in and out of the battery, and battery temperature help determine the optimum charging strategy. Also, the superior Advanced Glass Mat batteries found in many new BMW models have different charging requirements than ordinary batteries.
Good reasons
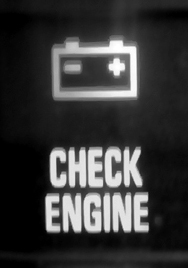
Today, the charging and electronic engine management systems are closely related in more than the relative positions of their warning lamps on the dash.
What’s behind the addition of advanced energy, battery and alternator control? First and foremost is a desire to prevent dead batteries. Frequent short trips with a large number of comfort and convenience features turned on by drivers can quickly develop into no-start situations. An adequate charge level can’t always be maintained by a vehicle’s electrical system under these heavy use conditions. Secondary and tertiary goals of intelligent alternator control include improving gas mileage and vehicle performance. Also, avoiding overcharging extends battery life.
Instead of boosting idle speed to continually maintain a desired voltage, the ideal energy-saving strategy is to make it acceptable for a battery to partially discharge during extended idling on the assumption that it can be quickly recharged once the vehicle begins moving. This saves fuel, but not allowing discharge to go past the point where the engine can’t be restarted is an equally important part of this strategy. Only under DME control, with continuous battery monitoring, do such advanced charge/discharge strategies become possible.
Another IAC feature is sequentially turning off or reducing the power level of comfort features like heated seats and window defrosters when the alternator can’t keep up, even at a boosted idle speed. The speed of a heater blower fan may be temporarily reduced. Knowing that a comfort feature can be disabled by IAC is imperative when diagnosing an accessory that has become inoperative. Is it actually broken, or just disabled?
More output
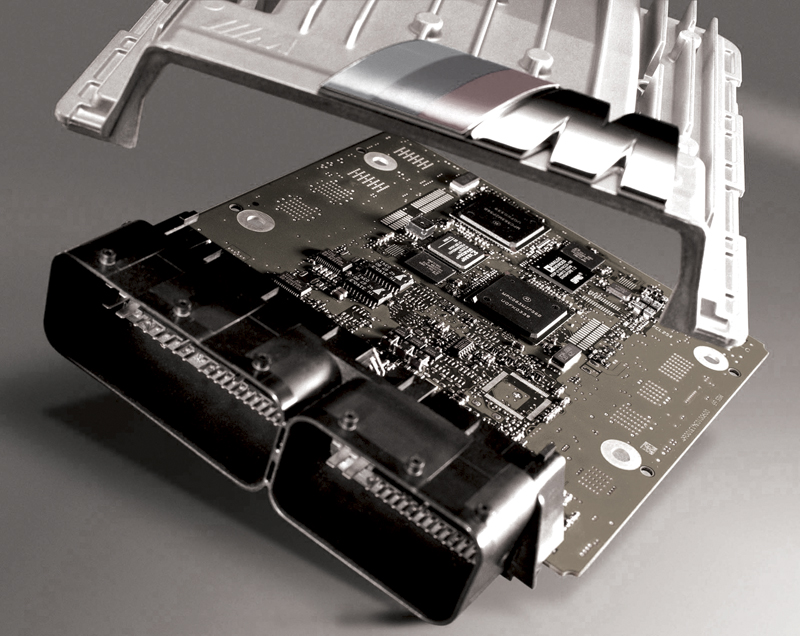
Engaging the “intelligence” of the ECM for the job of controlling alternator output makes for a much more efficient and effective charging system.
BMW combines advanced charging strategies like IAC with traditional improvements such as larger, more powerful alternators — some are even water-cooled — to supply the increasing electrical loads of its vehicles. A BMW equipped with IAC will only charge at idle, cruise, or during acceleration when the battery charge level falls below 80%. This requires the addition of a system that can constantly estimate the battery’s “State of Charge†(SOC).
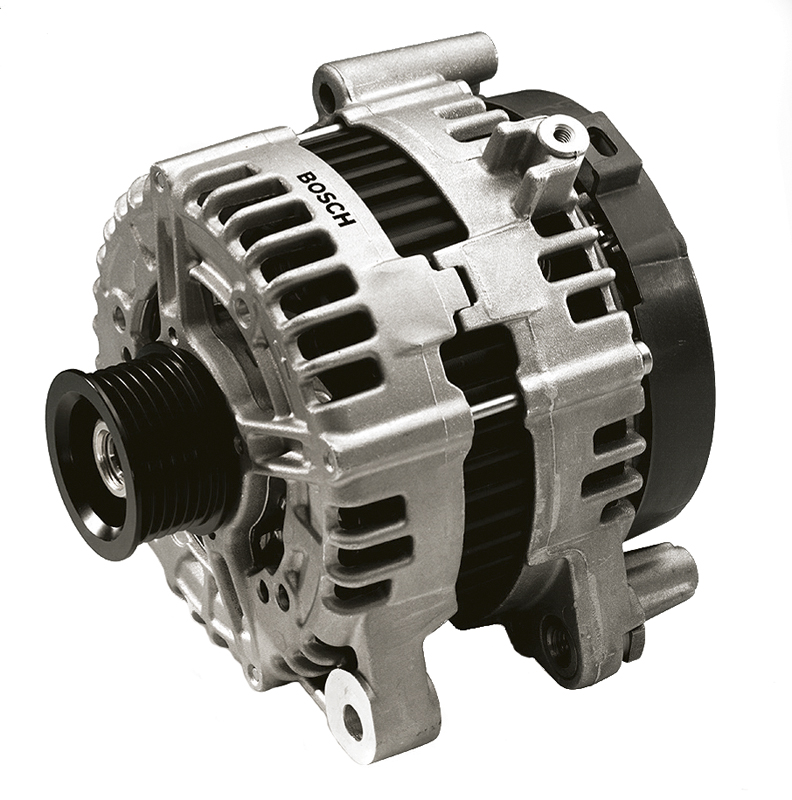
Intelligent controls can only maximize the potential of the charging system. Higher capacity alternators are also needed to fulfill the requirements of modern BMW vehicles.
Place the leads of a DMM across the battery terminals while the alternator is charging and what will you measure? Between 13.8 and 14.5 volts or so. If you can’t obtain an accurate battery voltage reading with the engine running, how can the vehicle’s ECM possibly use battery voltage to determine whether the battery is above or below 80% of charge, which would be approximately 12.5 volts? One can accurately measure battery voltage only when all loads are removed. The solution is placing a current sensor between the battery terminal and the ground cable. Current sensors add up the total amount of current that has gone into, or left the battery since startup. Combine all the current that has flowed into a battery and out of it with the battery voltage before start-up, and the ECM can come up with a reasonably accurate estimate of the battery’s current state of charge.
Total charge added or reduced allows the ECM to do a better job of calculating battery state of charge (SOC) as well as state of health (SOH). Such sensors measure battery temperature as well since a cold battery can be charged “harder†than a warm one, say, 15.5 volts for an AGM (Advanced Glass Mat) battery instead of 15.0V. BMW has set a target of 80% charge above which charging will only occur regeneratively, during braking, and below which additional charging is deemed necessary.
BMW’s battery current monitor “talks†to the ECM/DME by way of a single wire LIN bus connection. Techs may easily confuse a single wire for a ground or battery connection instead of a network connection, but an oscilloscope will quickly show the network traffic. The chemically harsh environment surrounding most batteries suggests techs prepare for diagnosing LIN bus opens/shorts resulting from corrosion of the battery terminal. BMW’s AGM battery, however, should tremendously reduce any such leakage and corrosion. As well, the GT1 should display any network faults on the LIN bus. A primer on the LIN Bus concept is available at http://www.lin-subbus.org.
Idle state
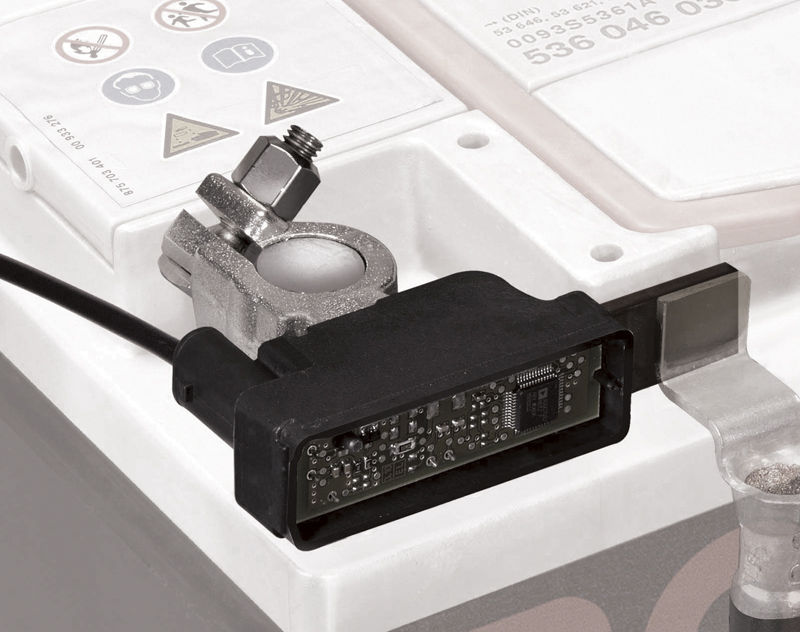
Late-model BMW vehicles have a battery current monitor that supplies the ECM with vital information.
“Idle state management†is another feature of the IAC systems of the future. It might be better named “Long-Term Parking†management, since it has nothing to do with engine idling. When a vehicle has been parked for a long time and the battery slowly discharges, both from parasitic draws and self-discharge, the idle state management feature kicks in. It can progressively turn off components that normally remain powered up even while the vehicle is at rest to try and maximize the time remaining before a no-start situation occurs. Hence, the loss of memory features could be a diagnostic tip that ISM has engaged — or is malfunctioning.
In addition to its primary purposes, the current monitor opens up the possibility of enhanced diagnostics in the form of automated measurement of parasitic currents, perhaps even including trapping intermittents, all accessible via scan tool. When a customer repeatedly has a dead battery, the sensor, combined with the DME and a GT1 scan tool, may allow the technician to view the charge/discharge conditions that preceded a flat battery. It may even be possible for the DME to signal the technician when the battery’s state-of-health has undeniably deteriorated, indicating that it’s time for battery replacement.
Glass mat
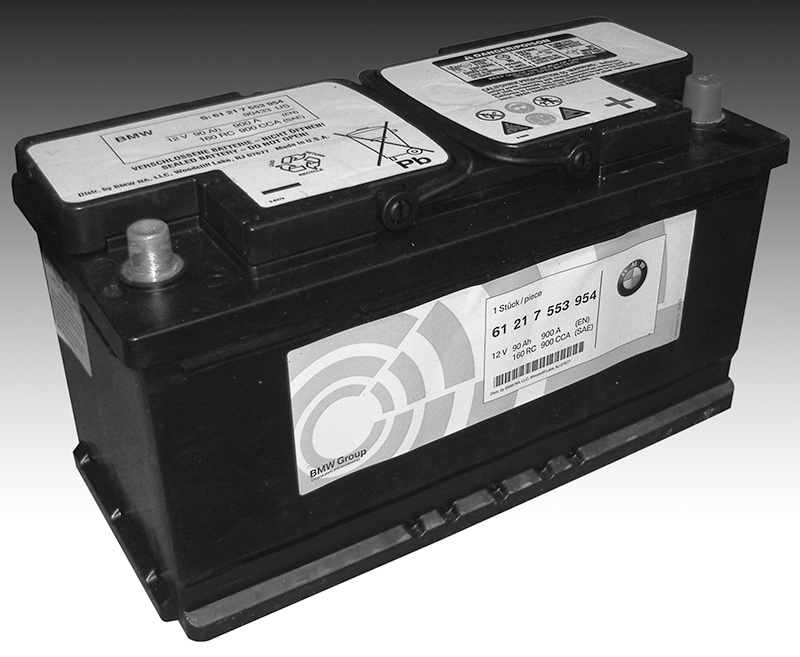
Advanced Glass Mat (AGM) batteries are less apt to gas and leak electrolyte than the traditional flooded-plate type, which reduces the potential for corrosion of components located nearby.
Another issue in testing BMW charging systems you will soon be seeing in your shop is the adoption of Advanced Glass Mat (AGM) batteries. Simply stated, an AGM is a higher-tech, “better†battery than the flooded lead/acid type, and should last considerably longer. But the one thing an AGM cell can’t withstand is overcharging. Shops that upgraded their battery chargers years ago to be able to handle lead-chloride “Maintenance Free†batteries now must go the other direction. While a completely discharged “Maintenance Free†battery might need a solid 16 volts to begin charging, 15.5-15.6 is about the top voltage you ever want to apply to an AGM, and that only briefly. During normal charging, 15.0 volts is recommended by AGM battery manufacturers. Since testing a charging system normally requires first fully charging the battery, be sure you’re using the right charger, such as the Deutronics units available through the BMW equipment program. Likewise, in-vehicle charging voltages over 15.5 volts in such systems may be indicative of a problem. Consult your factory manual.
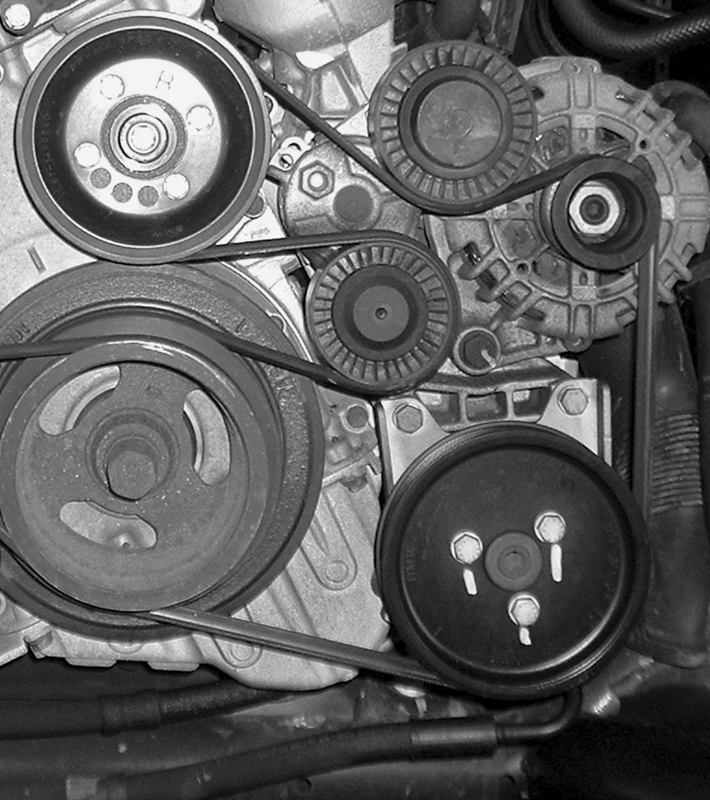
BMW serpentine accessory drives make for extremely long belt life, but there’s still the chance that slippage under magnetic drag will keep the alternator from spinning fast enough to keep up with electrical demands.
Multi-function controllers, which replaced a standard regulator in the back of many traditional alternators, will turn off any charging until two seconds after the engine starts. This minimizes the work the starter must perform. These controllers, fitted to numerous BMW alternators, also control the charging system indicator light on the dash. As a result, the lamp can indicate an overvoltage condition as well as a lack of charging and other conditions. Because BMWs typically have a resistor in parallel with the dash CIL, a simple bulb failure generally won’t cause the vehicle to stop charging. However, it makes performing a bulb test with the GT1 an important part of any charging system evaluation.
Diagnosis
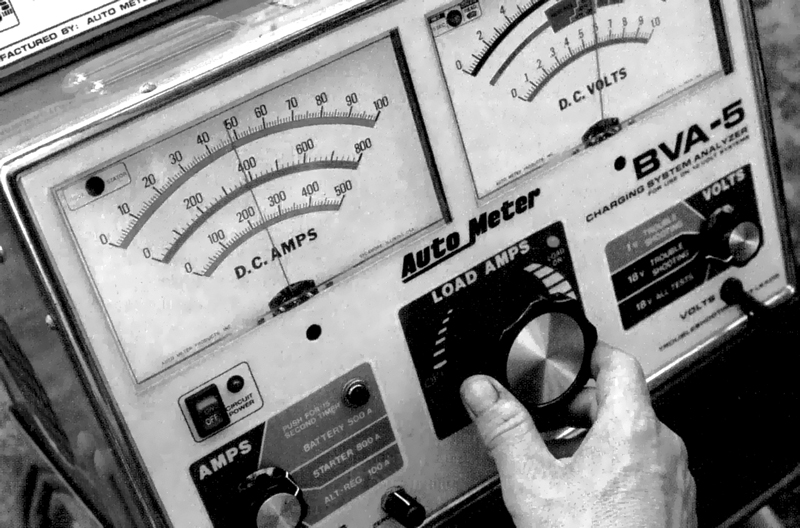
Even though charging system control is now handled by the ECM, the traditional VAT tester can still be used to force the alternator to produce at its maximum potential.
Charging system problems were traditionally indicated when a battery tested good, and parasitic draws were nominal. Today, consumer behavior, such as powering a current-hungry accessory from the cigarette lighter, must frequently be considered as a cause of dead batteries, although schemes like IAC will reduce this need. A check on TIS for model-specific TSBs before performing any diagnosis consistently proves to be a huge timesaver.
Charging system problems can be caused by mechanical or electrical failure of the alternator itself, failure of the alternator cooling system, faulty ECM control of the alternator, dirty connections/bad grounds, and failed current sensing devices (which could also lead to
overcharging or undercharging). Mechanical causes such as misaligned, damaged or slipping belts can also cause charging problems. Visual inspection, especially of connectors, can rule out many causes. Simple voltage tests can determine the battery state, and whether the charging system is operating at all.
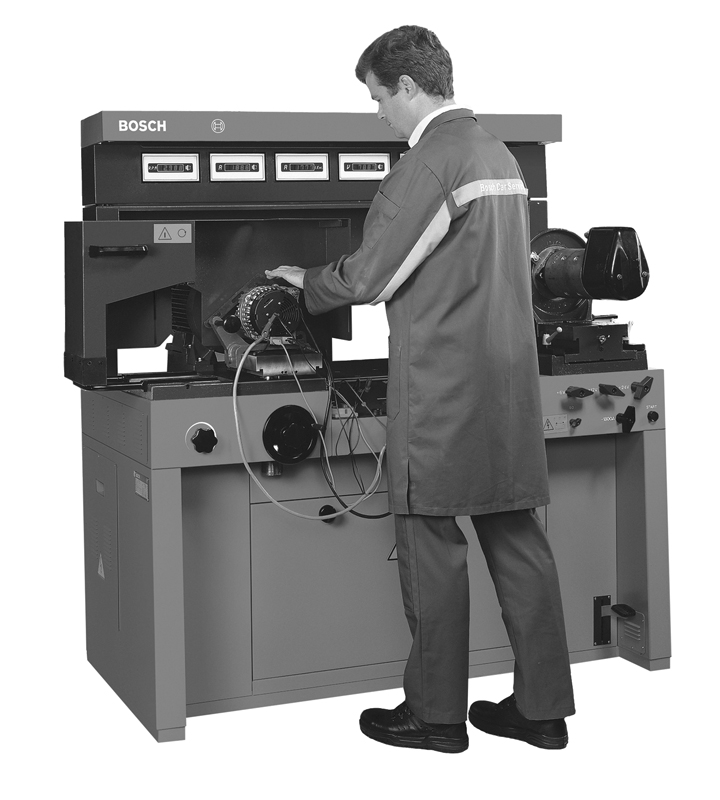
A sophisticated test bench will find problems in the alternator itself, but can’t be expected to address issues of field circuit control.
Since alternators today operate under control of the DME, “full fielding†as a method of alternator testing has gone the way of the dinosaurs. Connection of a scan tool is necessary to command the alternator to generate maximum out put in order to perform load testing. In general, an alternator should be able to put out at least 80% of its rated amperage when fully loaded.
Testing of an alternator itself consists of measuring the output voltage at different amperage loads, and measuring ripple, which can indicate a failed diode (it can also be caused by a battery with poor capacitance, but that belongs in another article). Traditionally, such testing has been done with a carbon pile load tester, which “fools†the electrical system into believing a large electrical load has been switched on. Alternator testing can also be  performed by removing the alternator and testing it on a special test bench. Again, since alternators are now under computer control, such testing becomes limited by the test bench’s ability to “command†full fielding, simulating the commands given by the ECM when maximum output is needed.
0 Comments