Electrical problems that appear downright baffling are invariably solved by getting back to basics. A review of over 200 BMW electrical issues reported on international Automotive Technicians Network (iATN) suggests that half a dozen “best practices†could significantly speed the repair of even the most mysterious electrical troubles.
Bulletin search
The first “lesson learned†was that techs will save themselves considerable time by initiating all gremlin hunts with a search for Technical Service Bulletins (TSBs). If the symptom was a radio that cut in and out, or a steering wheel that telescoped as if it were possessed, would you instinctively know to replace the ignition switch? Otherwise, a lot of time could be wasted looking for the cause of an intermittent 800mA parasitic draw that kept flattening batteries. A review of TSBs would have eliminated these and dozens of similar requests for assistance.
After a TSB check, obtaining a schematic of the affected circuit(s) should follow. As one successful BMW independent puts it, “Since you can’t see electricity, electrical problems have to be solved in your head. All you do on the vehicle, meter in hand, is confirm or disprove what you already suspected from looking at the schematic, and thinking about the symptoms.â€
Sufficient straight DC
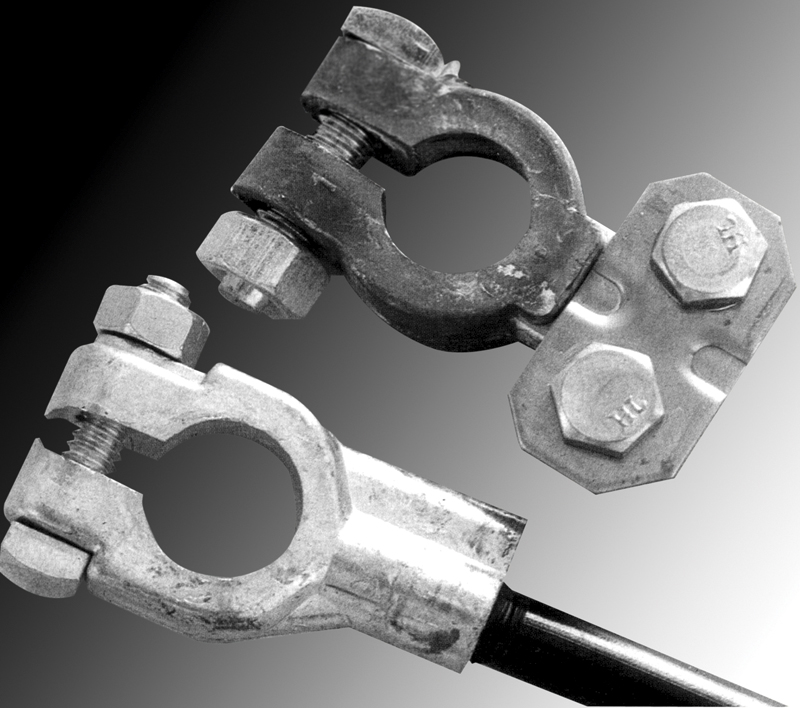
Emergency clamps are just that, but are often considered a permanent repair. Install a new cable and clamp assembly and you’ll head off problems.
Next is checking for the availability of clean power from the battery and charging system. Never start looking for a gremlin with a battery that isn’t fully charged (12.6-12.72V or better), or with an alternator that fails a load test, or puts out excessive ripple. The figure most techs agree upon as the maximum permissible ripple is .5V AC, measured at 2,000 rpm using a Digital Mult-Meter (DMM) set on AC voltage, and lights, heater, or some other load on. Scoping the alternator output is an even better practice. Spikes shouldn’t exceed +/- 1.0 V. Measure or scope directly across the alternator battery terminal and the case, not at the battery.
Battery basics
As one BMW technician tells TechDrive,”A bad cell in the battery can raise havoc with engine management systems. I load test the battery to spec and then use a Midtronics battery tester for the final test.”
Numerous BMW techs in the survey reported vehicles that would start and run, yet experienced all manner of gremlins due to a single bad cell in a failing battery. Naturally, this should have been the first thing they caught. Even with a surface charge, a battery with only five cells working could never achieve 12.0 volts. Battery service (that is, cleaning or replacing corroded battery terminals and clamps) should be performed before chasing electrical problems.
Next, of course, is checking fuses. Don’t just look for blown fuses, but for fuses missing altogether. You may not be the first tech who’s tried to solve this particular problem, and the last tech (or the vehicle owner) may have given up in mid-repair, leaving one or more uninstalled. Compare the guide printed on the lid of the fusebox to what’s actually in a problem circuit to make sure someone hasn’t installed a larger amperage fuse.
Minifuses don’t always have to be removed and visually inspected. With power applied, you can touch DMM leads to the two tiny contacts on the face of most fuses to determine which show a 12V voltage drop, indicating they’re blown, or use an inexpensive clip-on tester.
Asking your customer about seemingly unrelated symptoms is the third “best practice†TechDrive’s review of 200+ requests for assistance suggested. The customer may have come in to get a single problem fixed. Perhaps this problem is all he or she can afford to repair at this time, or is simply the most annoying of several problems. Something that didn’t get mentioned will often give you critical clues toward solving the primary problem.
Ask, “Has your car been doing anything else strange, even if you don’t want it fixed today?†Invariably, weird symptoms are somehow related. “Other customer comments†duly noted on the repair order may not always prove helpful, but the times when they do may make you look like a super diagnostician!
After the customer interview, it’s time to head on over to the Internet. Pattern failure information is a tremendous time saver on ghostly electrical problems. With a service like Identifix/DirectHit, you can type in symptoms and see if there are any known causes. You can do the same thing searching iATN’s archives, or even just using Google. Our review of 200+ electrical issues saw techs repeatedly seeking help on symptoms that turned out to be caused by failed:
- Ignition Switches
- Blower Resistors/Final Stage
- Fuel Door Actuators
- Alarm hood switches
- Wiper Relays
- Power Seat Switches
- Oil Level Sensors
- Door Lock Actuators
- Water seals on modules & connectors
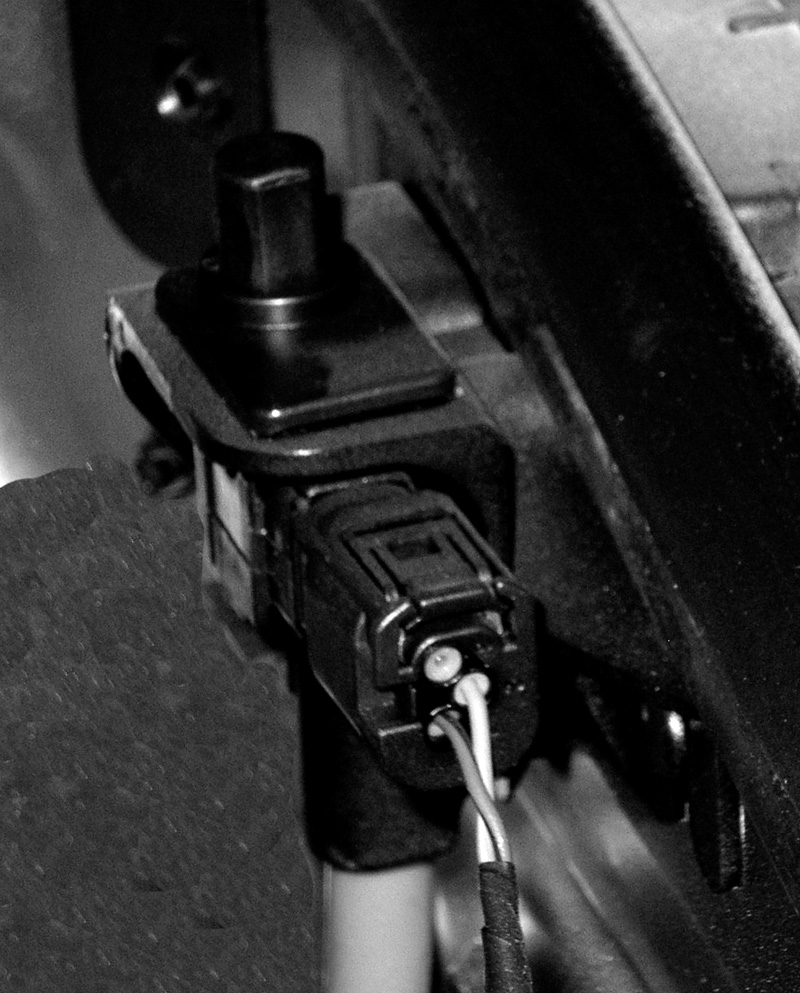
Switches that are in exposed locations, such as this one for the hood alarm, are often the cause of electrical glitches.
More than half of the complaints related to ignition switches discussed symptoms dealing with radios and telescoping steering columns. Five minutes searching pattern failure information could save a tech hours of panel-removing and trying to figure out why a steering column, radio or dome lamp was misbehaving.
Time for the DMM? Not yet. Instead, get out the GT-1 or other scan tool. On a couple of the “downright nasty†problems that led BMW techs around the block and over the curb a few times, superior engineering was the cause. Specifically, failsafes designed in by engineers. One vehicle refused to turn on its interior lights. Another refused to turn off its headlights. Both vehicles had codes, which, until read and cleared, caused a module to enter a failsafe mode. Headlight failsafes may be great for getting the vehicle home after dark, but not knowing that the interior lights had been disabled by the module just about sent one independent BMW tech to search for a new career.
Okay, you can get out your DMM now. Gremlins seem to breed in body shops. Overcome by paint fumes, they often pass out and end up in your shop as grounds placed on top of freshly painted metal, or connectors that didn’t get physically re-connected, and/or damaged pins in connectors unskillfully jammed together. Anytime you have SRS, lighting, window, door, or hatch problems in the physical area where body work was performed, start by checking grounds and connectors. While physical inspection is viable, voltage drop testing is the preferred method for checking any and all grounds, and will sometimes allow you to avoid pulling off body panels.
Keep this in mind: Aside from module and sensor failures, the majority of electrical problems result from mechanical failures of electrical conductors, including chafed wires, corroded connectors, bent pins, and the like. Besides body work, major component jobs such as engine or transmission replacement often result in these kinds of failures.
Intermittents
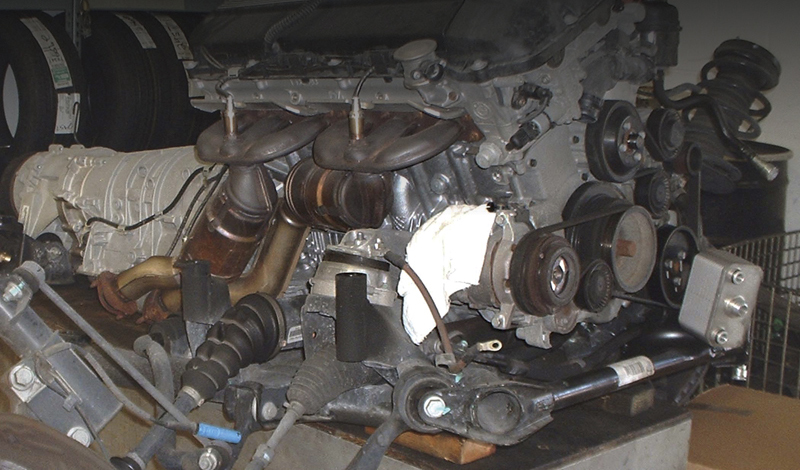
Any time major work is done, such as engine R&R, there’s the potential for damaged wires, poor connections, bad grounds, etc.
Now for the fun part: chasing intermittents. The key to diagnosing intermittents once again lies with your customer interface. Before an intermittent is run down, you may need to go for a ride-along with the customer. It’s hard enough to catch intermittents “in the act†in order to solve them, and next to impossible if you haven’t personally experienced them. It becomes too easy to doubt the customer’s word.
Furthermore, his or her description of the symptoms usually won’t be in clear tech-speak. As well, you may notice other symptoms, warning lights, or clues to diagnosis the customer didn’t mention.
You should begin with questions about when the intermittent misbehavior occurs. In the rain, after sitting a while, after a hot or cold soak? After short drives, or long ones? After being in the garage? Where is just as critical. Driving down rough roads or over train tracks? You may have to drive the exact same route the customer drives to work to get it to misbehave, or ride along with him or her. It’s frequently some everyday behavior that didn’t get mentioned – plugging in a cell phone charger and setting it on the unoccupied passenger seat with the resultant Radio Frequency Interference (RFI) setting off an error, for instance – that gets you. Riding along is often the ONLY way to see exactly what customers are doing, even what radio station they listen to, or how they consistently park on a downhill slope.
Since the majority of electrical problems have underlying mechanical causes, heat, moisture, motion, or vibration, can all make an intermittent fault come and go.
If a problem arises only after a vehicle has been driven a certain distance, it usually indicates that it’s heat-related. This could be a cold solder joint, a loose connector, corrosion inside a connector, and so on. There are several techniques for diagnosing heat-related intermittents. You can use a can of freeze spray to try and cool a suspect sensor, or module while it’s misbehaving. The other approach is to let the vehicle idle, or use a heat gun to try to induce a suspected overheating component into misbehaving.
Intermittent problems that show up when crossing train tracks or driving along rough roads often indicate loose connectors, loose ground connections, or damaged insulation that allows a wire to chafe when it is moved. Tugging and pushing on wiring to try and duplicate the problem is about all that can be done, aside from performing a close visual inspection. A DMM with a min/max recording function can be invaluable if you’re diagnosing this sort of problem solo. Don’t be afraid to get aggressive with wiring looms. You won’t solve intermittents by being too gentle and you can always repair any damage you do by tugging too hard. The only crime is NOT solving the problem.
Water intrusion into modules and connectors occurs all too often. On cold mornings moisture can condense into connectors, and then evaporate in the afternoon and the problem will totally disappear. The appearance of “flood cars†from Hurricane Katrina has made inspecting for water intrusion a regular task when mystery problems show up. Visual inspection is the first step. Spray bottles can help. Dielectric grease, which doesn’t contain elemental carbon, and therefore doesn’t conduct electricity, can be packed inside connectors to prevent future water intrusion.
The weapons of war
There are several excellent “weapons of war” available to the tech attacking intermittent electrical problems. A min/max recording DMM is a good start. A digital storage oscilloscope can, during a ride-around, allow you to spot an intermittent waveform, or dropout from a sensor. The scope’s advantage over other tools is that you can set a trigger not to record anything until a suspect signal changes state – a signal suddenly being grounded or driven to battery voltage. But what if the problem only happens once in a LONG while. Longer than you want to hang onto the car.
The ultimate in gremlin capture is a flight data recorder, or FDR. This is a “black box†that allows the vehicle owner to press a “Panic Button†when an event occurs. The box is continuously recording selected signals, in a loop fashion, and will STOP recording 30 seconds or so after the button is pressed, giving the operator a view of the recorded signals both before and after the event. With one of these, you can capture even the most elusive of electrical gremlins.
Once you’ve identified a wire that is open or shorting, a tracing tool such as a FaultFinder will allow you to inject a signal into that wire and trace it, even behind panels or underneath carpets, to where it is open or shorted. A FaultFinder is quite a step up from the old compass and circuit-breaker approach to hunting down broken or chafed wires. Yet even it requires some practice to use effectively. There are several manufacturers of such tracers, including Waekon.
Electrical gremlins are elusive little creatures. They breed in paint and body shops. Only the most methodical techs are able to capture them. Taking shortcuts like not cleaning the battery terminals, or not testing the charging system before starting an electrical diagnosis can make an otherwise simple diagnosis turn mysterious. Once all your “homework†such as checking TSBs and pattern failure information is complete, then diagnostic work can begin. As with all auto problems, intermittents require the most effort to successfully diagnose and repair. Fortunately flight data recorders and other technologies can make previously “impossible†problems not so difficult to solve.
0 Comments