“Faulty welds spur inspection of 7 more ships†was the headline for the Navy News on December 18, 2007. The article covered the need for the U.S. Navy to inspect at least seven more new ships, including the $4.5 billion aircraft carrier George H. W. Bush that was commissioned in October, 2006. Mike Petters, sector president for Newport News where the ship was built mentioned that the “welding discrepancies†would delay the sea trials. “The matter is a technical issue that has called into question the discipline of our processes. We are also putting into place a rigorous set of corrective actions that include mandatory training for each and every welder and every welding foreman. What really matters the most to me is that we conduct our business with the highest level of integrity…in support of America’s freedom!â€
Now that we have answered your question as to why BMW certifies and de-certifies welders, and stresses the importance of training and certification, let us take a look at the entire welding process and what BMW recommends.
A summary of welding these past 40 years or so
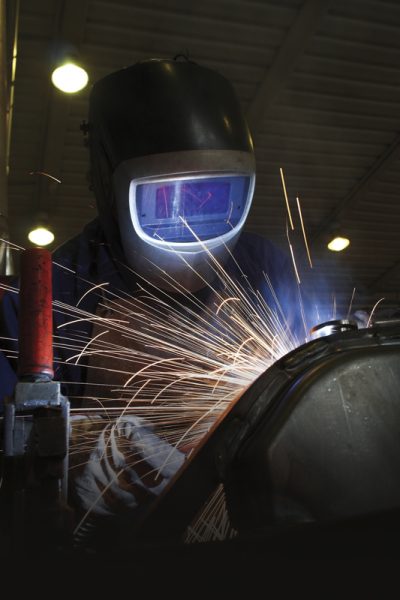
It is 1965 and the vehicle you are repairing requires a new quarter panel. You quickly summon the counter person to pull your parts while you head over to the corner to “unbury†the welding torches, stumbling at the same time on the spot welding unit. Not having much luck in the past and fearful of the shock you may receive from the spot welding unit, you roll the set of torches over to your stall. You then take your grinder out with #36 grit sandpaper and begin grinding the sheet metal where you will be welding. Clamp the panel together, light up the torch and begin stick welding the panel into place, all the time trying to reduce heat to not warp the sheet metal.
Move ahead to the late 1970s and a new type of welder becomes the talk of the industry: the “MIG welderâ€, or Gas Metal Arc Welding (GMAW). MIG welding is a process that joins metals by heating them with an arc. The arc is between a continuously-fed filler metal (consumable) electrode and the workpiece.
Externally-supplied gas or gas mixtures provide shielding. Metal is deposited only when the wire actually touches the work. No metal is transferred across the arc. MIG welders continued to become easier to use, to require less maintenance, and to be more cost effective and more adaptable to various types of welds.
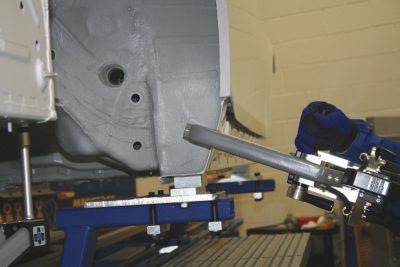
Late in the nineties, squeeze-type resistant spot welders/resistance pressure spot welders make their debut in North America, producing cleaner, better, factory-like spot welds with limited heat displacement. Within the next couple of years, power conversion and duty cycles are improved making the tool more attractive to collision repairers, and demand increases for the new welders.
Resistance Pressure Spot Welding (RPSW) – the reasons
The metals being used in today’s vehicles continue to change at a rapid rate. As auto manufacturers continue looking for lightweight, fuel efficient and safe vehicle designs, the advances in various steel and other metal types will continue. RPSW delivers the appropriate weld needed while limiting the heat levels to the area of the weld and maintaining the molecular makeup of the advanced steels. For example, mild steel has a tensile strength of around 180-200 N/mm2. Compared that to today’s best steels at around 1,500 N/mm2.
Today’s RPSW continually monitors the unit while the welding process is being performed, reducing user error and insuring proper weld characteristics. On-board microprocessors and electrical current technologies provide the user with a more accurate, consistent and repeatable spot weld, resulting in assured quality of workmanship. Pre-programmed spot welding is becoming more popular with these units to ensure that vehicle repairs match OEM specifications, thus returning the vehicles to “pre-loss condition.†As metals continue to advance, demand expectations for RPSW will continue accordingly.
BMW’s Currently-Recommended Welders
Car-O-Liner CR600
Car-O-Liner understands that collision repair facilities are different, which is why its CR600 welder will “sense†if your voltage is low and adjust itself so that the power time is extended, thus ensuring that your welds are of proper quality. It also features programs that can be set to vehicle manufacturer specifications so you can be sure that your weld is not any stronger or weaker than it was originally, but rather the way it was designed to be. Car-O-Liner understands that any deviation would jeopardize the vehicle’s crashworthiness should it be involved in another collision, all of which makes it worthy of a BMW recommendation. The Car-O-Liner CR600 also allows the veteran welder to adjust the electrical current and time length for those unforeseen uses.
Celette Midispot QSVM9000
The Celette Midispot also senses if your line voltage is low and adjusts itself accordingly. Its programs can also be set to vehicle manufacturer specifications, making sure that your weld is of the strength the designer intended, which maintains crashworthiness. In addition, the Celette Midispot also allows manual adjustment.
Elektron – Multispot MI-100 Control
One of the characteristics that this welder offers is the ability to measure, record and analyze every weld, and provide a printout for your records. Approved manufacturer repair facilities can access information from a manufacturer like BMW to prevent improper settings that result in inferior welds. The Elektron Multispot MI-100 Control welder also produces consistently accurate spot welds by using a microprocessor to control current and the welding time. It also allows the veteran welder to manually adjust controls, and will record this data.
In all three recommended welders you will quickly see common themes:Â water cooling, programmability, and controllability so that vehicles are repaired in a way that assures passengers safety.
Below is the matrix (updated March, 2007) for RPSW equipment that is currently approved by BMW and is either “Recommended†or “No longer recommendedâ€
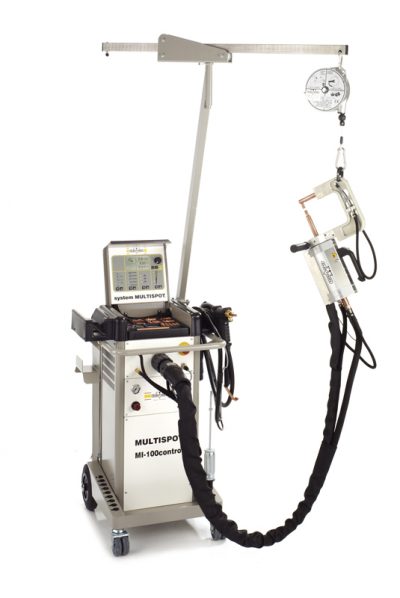
Repair Procedure
Sample spot welds should be performed on separate scrap pieces with destructive test procedures being performed (peel, chisel and twist testing). All surfaces being welded together should have paint removed, be free of contamination and panels should be clamped. Inspect all welds after completion making sure that there are no welds contacting the panel edges, no pin holes, and that the weld surface is smooth.
Here at BMW our vehicles may not cost $4.5 billion dollars each like an aircraft carrier, but our customers’ safety is priceless. Make sure your welds have integrity!
Vehicle | Group 1 | Group 2 |
E93 – 3 Series | OK to use EXCEPT on A-Pillar & Rocker Areas | OK to use on ALL areas |
E70 – X5 | OK to use EXCEPT on B-Pillar | OK to use on All areas |
E64-6 Series Convertible | OK to use EXCEPT on A-Pillar, B-Pillar & Rocker areas | OK to use on ALL areas |
0 Comments