Just like a blacksmith’s bellows, the Mercedes-Benz AIS ” fans the flames,” promoting rapid oxidation of pollutants in the exhaust stream
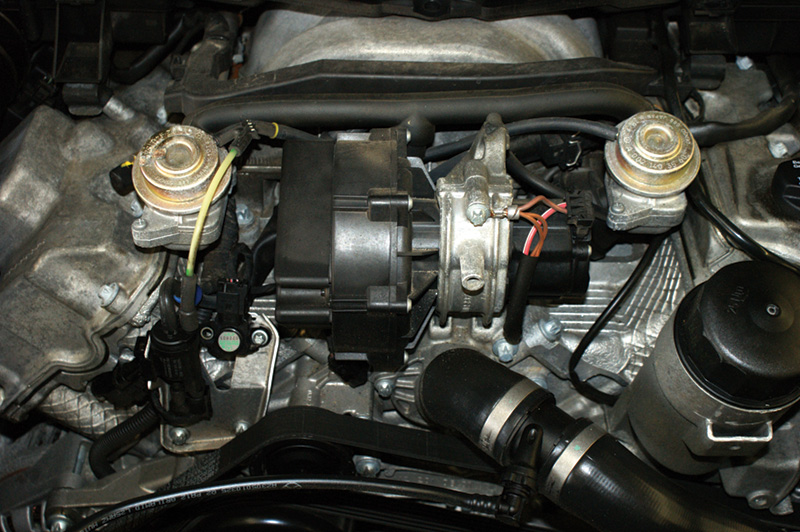
On V8 engines, the
secondary air system is easy to test. Everything is right in front of you. Here we have the air pump, shut-off valves and switch-over solenoid, all nicely accessible.
Whether you believe technological developments are motivated by tightening government regulations, or by the desire to add value for new-car buyers, there’s no doubt that they are coming along at an ever-increasing rate. Secondary air injection systems, however, have a long history — they’ve been fighting air pollution since the 1970s. Of course, they’re way different today from what they were then.
Originally, a belt-driven pump forced air into the exhaust manifold to help oxidize escaping HC and CO. This was taken one step further when that air was used to feed the fire in the old two-way catalytic converter. In the early ’80s when the three-way cat became popular, the air was piped into the cat downstream of the reduction section after the engine warmed up so that it wouldn’t interfere with the reaction that broke down NOx, yet was available for the oxidation section.
Beltless
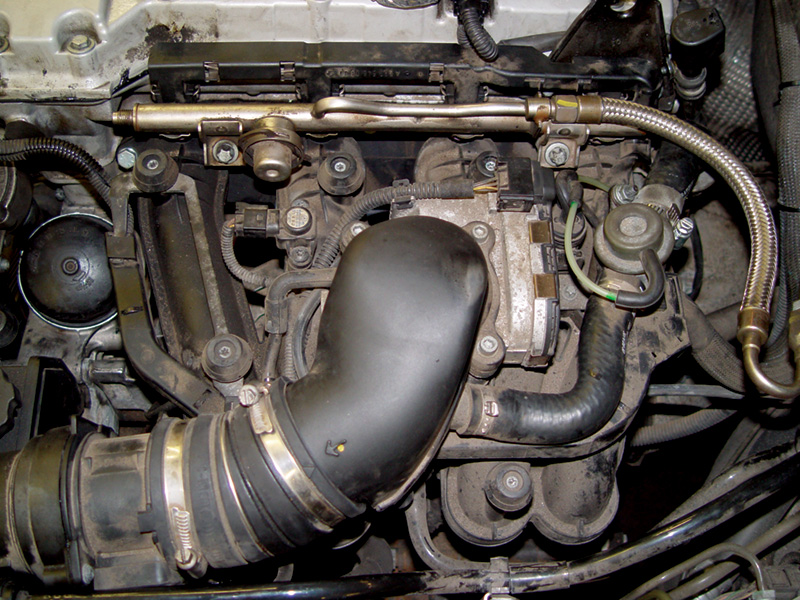
On supercharged models, the
compressor generates the air that is
supplied to the exhaust ports through this shut-off valve. Notice the solenoid mounted nearby that supplies vacuum to open the shut-off valve.
A modern Mercedes-Benz secondary AIS (Air Injection System) does away with that energy-wasting and space-hogging belt in favor of an electrically-driven pump. This also allows much more precise control of airflow, which is necessary as emissions regulations continue to become stricter on both federal and state levels, and as the quest for improved fuel efficiency continues.
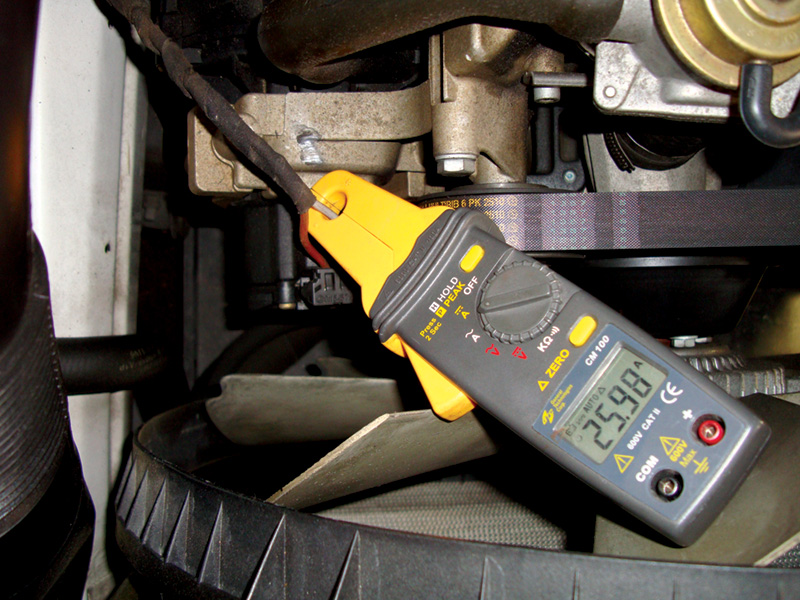
When the secondary air pump motor is activated cold, or you cause it to activate, you can measure the amp draw of the pump. As you can see here, around 26 amps should be your reading with a normal motor. If it is lower, the pump portion is probably worn. If the amp reading is too high (fused 40 amps) the motor may be seizing up.
The secondary air pump motor is only activated when the engine is relatively cold — below 60 deg. F. It is only commanded on for up to two and a half minutes. This is sufficient to warm up the catalytic converters. The pump receives its power supply from the secondary air pump relay, which is operated by the ME control unit. The system is also activated during closed-loop operation, but only to test the system’s ability to pump air into the exhaust — the ME control unit looks at the reaction of the O2 sensors.
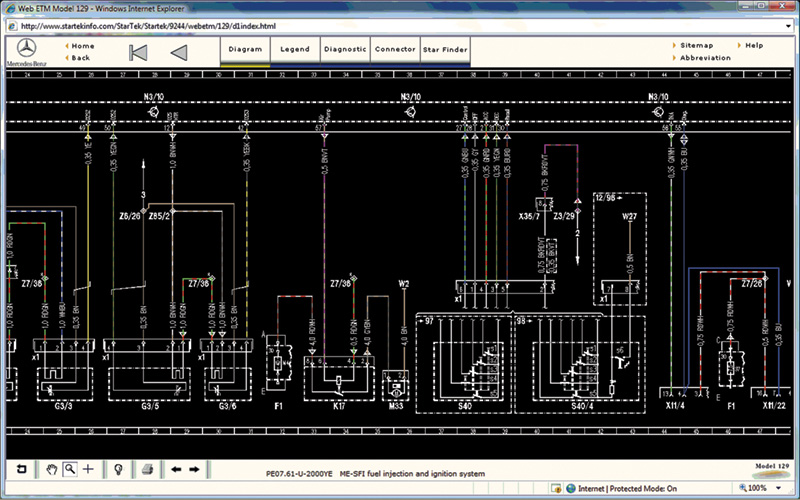
Your paid subscription to www.startekinfo.com allows you to pull up the wiring diagram for the engine management system. Look at components K17 (relay) and M33 (air pump motor), and you should be able to come up with a diagnostic plan to activate the relay and test the air pump.
There is one exception to this rule. Early 111 Evo engines (four-cylinder supercharged) do not use an electric pump. The ME control unit uses the supercharger to generate the necessary pressure/flow of fresh air to the exhaust. On models with an electronically-controlled “compressor” clutch, the clutch is activated at engine temperatures below 60 deg. F., and can be kept engaged for about two and one half minutes. On later 111 engines, there is no supercharger clutch, so the compressor is always spinning. The recirculation flap is held closed to allow the compressor to make the relatively small amount of air pressure/flow that the exhaust air injection requires.
Shut-off valve
From the pump, the air is directed to a shut-off valve. This valve is vacuum-controlled, and is normally closed to block exhaust gases from reaching the pump when the system is not energized. On four- and six-cylinder engines, there is only one shut-off valve, but there are two on eight- and twelve-cylinder models. When the system is active, a switch-over solenoid supplies vacuum to the shut-off valve(s). This solenoid is ground-controlled by the ME. Remember, with engine temperature below 60 deg. F. the switch-over solenoid is grounded, which supplies vacuum to the shut-off valves, opening them. Air is then supplied to the secondary air passages cast into the cylinder head and exits into the exhaust ports. This oxygen rich air mixes at the earliest point with the hottest exhaust gases and promotes continued combustion. The heat generated from this process in the exhaust manifold heats up the catalytic converter fast and therefore reduces overall emissions quickly.
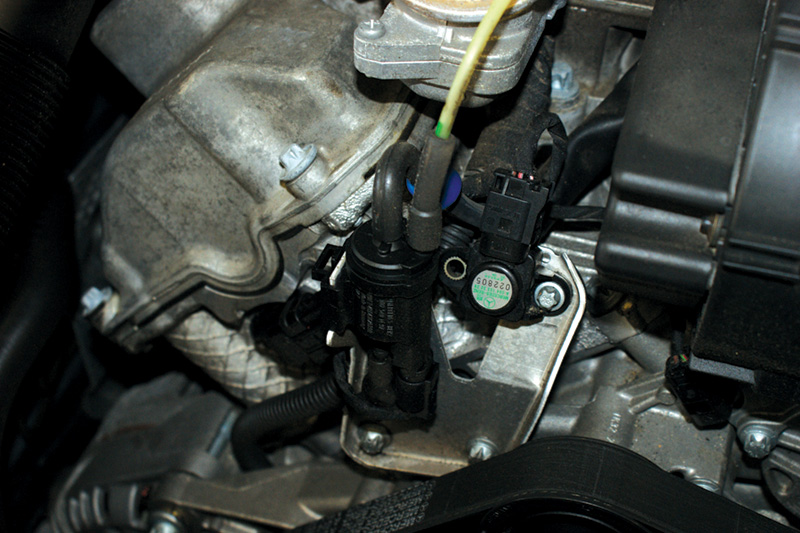
The switch-over solenoid receives
manifold vacuum, and, when
energized, directs this vacuum to the shut-off valve. You can energize this solenoid through the SDS software in your Compact III, or simply ground it with a test light and check for vacuum at the shut-off valve.
Being an emissions control system, AIS must have self-diagnostic capabilities. So, has its own monitor. Both the secondary air pump and the switch-over solenoid are activated during a normal drive cycle. Once the pump supplies fresh air through the shut-off valve into the exhaust stream, the O2 sensors register the high oxygen content in the fresh air and this signal causes the ME control unit to assume that the engine is running lean. The ME’s adaptation programming tries to compensate for the lean condition by adding fuel. The ME looks for a Lambda value change of 25%. If the change is less than 25%, the control unit determines that there is low flow of the secondary air injection system and flags a code of P0410, or one of its variants. This could be caused by no voltage to the secondary air pump, or a weak pump. An inoperable switch-over solenoid or a stuck shut-off valve can also cause codes. If all these components are functioning properly, you may still have the problem of blocked passages in the cylinder heads. How are you going to determine what’s at fault?
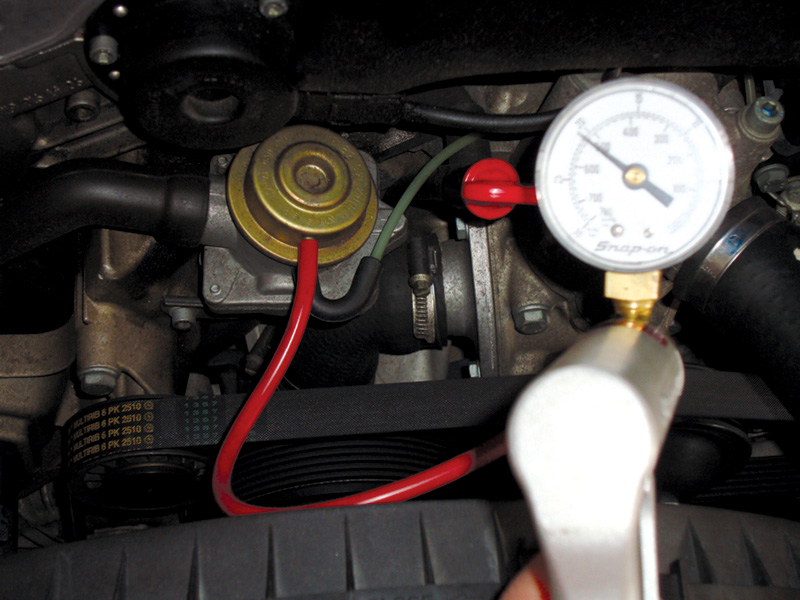
You can apply vacuum to
the shut-off valve and see if it holds. This should also open the valve. If you remove the hose from the air pump motor you should feel exhaust coming out of the valve while the engine is running.
Codes and testing
Since problems in the secondary air system usually do not cause drivability symptoms, you will probably be diagnosing a code in the P0410 range. The customer will more than likely bring in the vehicle with a CEL (Check Engine Light) or MIL (Malfunction Indicator Lamp) on. You are going to have to test components, and you are going to have to start somewhere. Having a Compact III or Basic is a tremendous help when it comes to diagnosing any problem with a Mercedes-Benz system, but we believe you need to back up any scan tool diagnostics with direct component testing for verification.
Testing the pump is fairly simple. Remove the engine covers and provide power to the motor connector. You should hear a loud whirring noise. Whenever you compress air, even though filtered, you are going to condense water, especially in high-humidity climates. This moisture can get into the electrical portion of the motor and cause failures. This is why the motor is usually mounted on the engine. The heat should cause any built-up moisture to evaporate. The current draw of a good pump will be 25 to 26 amps. Any lower and you’re probably not pumping much air, and anything higher and the motor is starting to seize.
If you are lucky enough to have the vehicle overnight, you can verify the air pump relay operation. The pump power supply wire should see battery voltage within a few seconds of a cold start. This voltage can remain on for up to 150 seconds. If voltage is low or not there at all, you will need to locate the secondary air pump relay. You can manually ground the relay and see that voltage is supplied to the pump. With a paid subscription to www.startekinfo.com, you can retrieve a wiring diagram for the vehicle and component location using Star Finder. As mentioned earlier, the relay is controlled by the ME. With your Compact III or Basic, you can command the relay on even if the engine is already warmed up. Or, you can apply a test light to the ground control of the relay. You should hear the relay click and the pump run. The current draw of the relay is around 100mA. If this is not the case, verify that you have voltage to both the control coil and switched circuit of the relay.
If everything so far is in working order, you will want to test the switch-over solenoid and shut-off valves. The solenoid valve is controlled by the ME, so the Compact III or Basic scan tool will be able to activate the solenoid, or you can once again manually ground the solenoid with a grounded test light while the engine is running. You should measure manifold vacuum at the shut-off valves. What does the O2 sensor say?
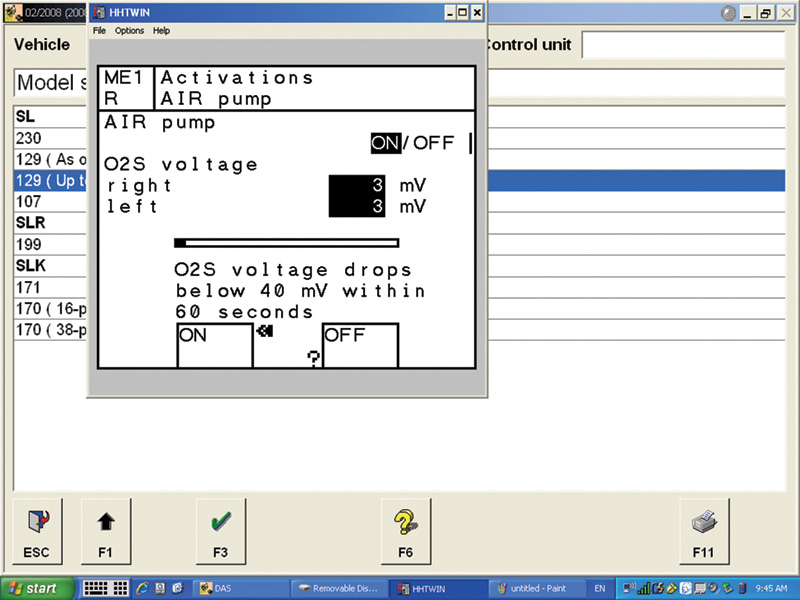
Using your Compact III or Basic scan tool, you can perform a secondary air flow test while the engine is running. Even on older vehicles such as this 129 chassis, you can use the HHT software to command the secondary air system on and see the reaction of the O2 sensors.
To test the shut-off valve, you can apply vacuum to it with a hand-held vacuum pump — it should hold. How will you verify that it is actually open? You could remove and physically watch for movement, but there are better methods. You can apply vacuum to the valve and watch the front (upstream) O2 sensor signal. It should drop to 0 mV with the secondary air pump commanded on and vacuum applied to the shut-off valve. If the O2 sensor reads a lean condition, but does not drop to zero, you can assume that the shut-off valve is working, but there may be an additional problem. The ME control unit looks for the Lambda (fuel trim) reading to compensate for the false lean condition by adding 25% more fuel. If the secondary air passages are clogged or restricted in the cylinder head, the O2 sensor will not see the false lean condition and as a result the ME will set a code for low secondary air flow. This is one of the more difficult problems to repair. Short of removing the cylinder head for a thorough cleaning, you will have to find a way to clear the carbon built-up in the intake passages.
With a little luck and some good chemicals you may be able to clear the passages in the cylinder head without removal. Remove the shut-off valves and pour a reasonable amount of cleaning solution down the ports. You can remove the exhaust manifolds and plug off the secondary air ports, but this is not necessary. You will have to let the cleaning solution sit over night. It also make take a few applications before the passages are clear, but after softening up the carbon in the ports, apply shop air pressure to the shut-off valve exhaust ports and you should be able to open up the passages. If not, the cylinder head will need to be removed for better access to the ports.
You can do it
Although pollution control devices add complexity to an engine’s air/fuel/ignition management system, the above should serve to illustrate that as long as you understand how any part of that system works, you can follow a logical process to come up with an accurate diagnosis. That capability will make you popular among your customers. One more thing: Think about adding the passages of the AIS to any carbon-cleaning service you offer.
0 Comments