Computer controlled systems are everywhere, and they do add a certain level of complexity to diagnostic procedures. On the other hand, they can also make mechanical troubleshooting easier.
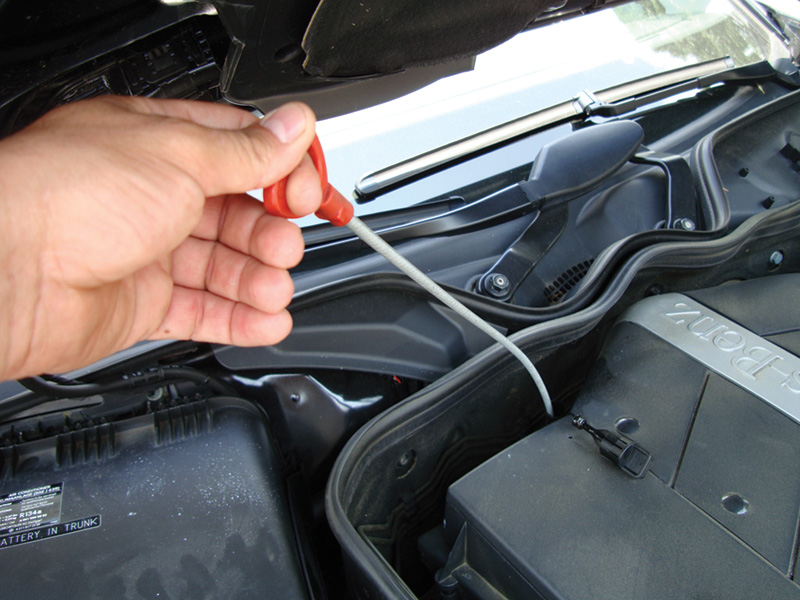
Before reading any adaptation data, the first step is to verify proper fluid level. If the level is too low, you cannot trust the readings to tell you the true condition of the transmission. Here is the special tool available from your Mercedes-Benz dealer for checking fluid level.
One of the benchmarks of a well-engineered motor vehicle is its road manners. In the case of an automatic transmission, the goal is smooth, seamless shifting. This is accomplished by applying exactly the right hydraulic pressure at exactly the right time to the clutch assemblies. If the pressure is too high, the shifts will be too firm and very noticeable. If too low, the clutches will slip, causing long, slow shifts that accelerate wear and are also noticeable. The key is precise control of both the pressure and timing of the shifts, which results in a transmission that offers maximum fuel efficiency, performance and durability, and imperceptible shifting. Of course, aggressive drivers require firm shifts, while more easy-going drivers want smoother shifting. So, engineers have always had to strike a balance between the two during the design process. Sophisticated electronic control of line pressure and shift points makes that less of a compromise.
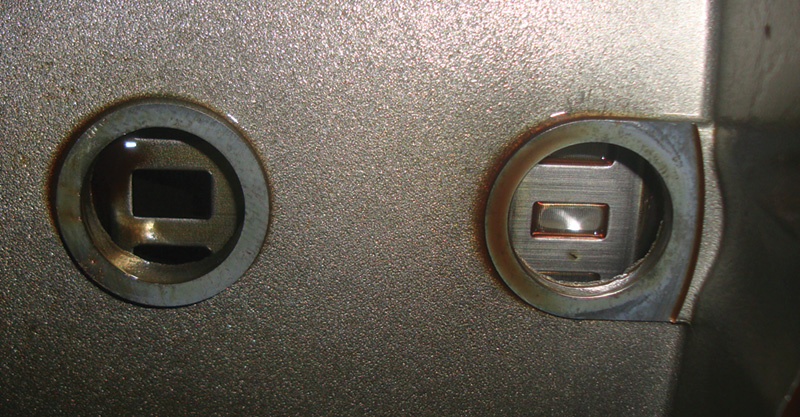
Above the valve body are speed sensors N2 and N3. They fit into the lower part of the case and indicate the speed of the clutch basket tone wheel. This is how the control unit determines slippage. Make sure you do not have any speed sensor problems before trusting scan data.
Mortality
Even the most well-built transmissions can’t live forever. Clutch assemblies wear, and the clutch material circulates around the hydraulic circuits. This can cause the pistons in the valve body to stick and possibly affect shift quality. As the plates get thinner, it takes more time for the clutch to grip, which accelerates wear. The way the vehicle is driven will affect longevity as well. Adaptive strategies in the electronic module help to mitigate the damage, and maintain shift quality in spite of the inevitable wear.
How does the control unit know what to change? Input sensors provide the necessary data. There is a fluid temperature sensor, pressure sensors, and speed sensors. By comparing the speed of the input and output shafts, the computer can determine when the clutch assemblies engage. If the sensors indicate slippage, more pressure can be applied by different commands to the hydraulic solenoids. A pressure sensor monitors this change. The temperature sensor is used to manage shifting during cold and hot situations. All of this happens during normal driving.
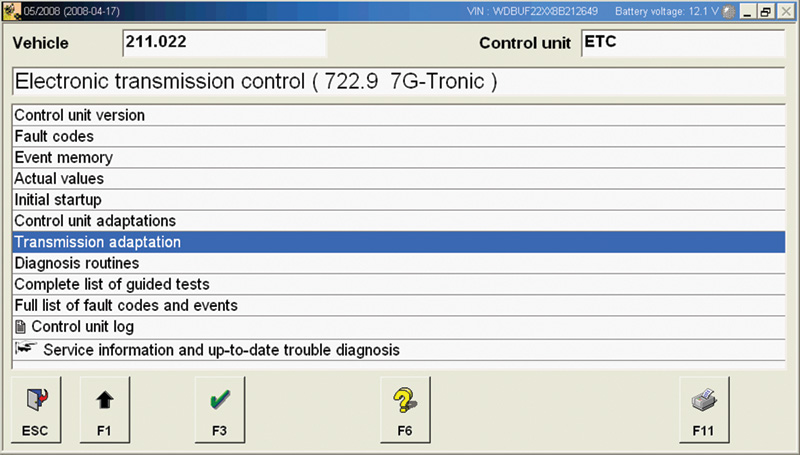
Once you’ve selected the EGS control unit, you can enter the transmission adaptation tables and look at the readings. You have the option to look at upshifts, downshifts, and reset the tables. This should be done if transmission fluid levels were low, or other problems were found (speed sensor codes, for example).
Sensor data
Artificial intelligence in the programming and the electronic transmission control unit (ETC) monitors sensor data, changes shift points, and even compensates for wear. This information can be valuable when diagnosing a problem with transmission performance. The SDS scan tool will display this data and allow you to make a more precise diagnosis. After selecting “Drive,†select “Transmission†on your SDS, or equivalent. Or, you can select it directly after performing a “Quick Test.†From here, you can pull codes, look at live data, and evaluate transmission “Adaptation Data.†Considering the cost of transmission repair, your accuracy may mean the difference between a happy and an unhappy customer.
While monitoring adaptation data, you will notice that you can select to look at up-shifts or down-shifts. If you are trying to diagnose a specific shifting problem, you can look at the “Assignment of hydraulic shift elements.†This tells you what solenoids are active during a particular shift. For instance, let’s say you are looking for a 1-2 shift problem. You can see that in first gear hydraulic brake solenoids B2 and B3, as well as clutch solenoid K3, are engaged. In second gear, solenoid B3 is no longer activated, but B1 is now energized. Now that you are familiar with which solenoids affect which shift, you can monitor the solenoids that have an affect on the shifting problem.
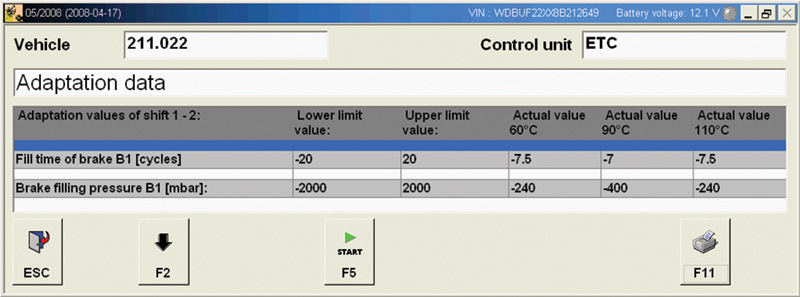
The adaptation tables show you the maximum and minimum limits for each reading. You also see readings for a cold, normal and hot transmission. The upper reading indicates the time it took to apply the clutch basket. The lower reading indicates the pressure required to make that happen.
Reset
With the SDS, you can reset the adaptation data as well as view it. When viewing the data, you are given two parameters. The first one is “Fill Time of Brake (solenoid) B1 through B3,†depending on how many gears this particular transmission has. This counter is measured in cycles. To assist in reading the data, the maximum and minimum readings are displayed as well as the actual value for three different temperature ranges. Ideally, you should see the number “0†in the actual value field. This means the ETC does not have to compensate at all for any component wear.
The second line of data is “Brake Filling Pressure†for each shift. This is measured in mBAR from the pressure sensors. Once again, the maximum and minimum limits are displayed along with the actual values for three temperature ranges. In either case, if you see a negative number, the control unit is reducing pressure to correct the shift. If you see a positive number, the control unit is adding pressure to improve shift quality. This is more common with high mileage transmissions that have significant wear. Resetting the adaptations allows you to bring the counters to zero as if the transmission were new. After evaluating the current data and resetting, you can then perform an “Adaptation.â€
Put the ETC in adaptation mode and go on a road test. The computer will make changes to the shifting patterns faster than it would if the owner were just driving it around. Look to see how quickly these adaptations are made. A worn or malfunctioning component will cause the actual values to change a lot. Adaptation can be read and performed for both the shift solenoids and torque converter lock-up performance.
If either of these values is excessive, repair work is going to be needed. By looking at the value for each shift, you may determine that the transmission is worn out and a single repair will correct the problem, but a remanufactured transmission from Mercedes-Benz may be a more cost-effective solution in the long run because all Genuine Remanufactured Parts meet the same standards for quality, reliability and value as brand new parts. The term “remanufactured†means brought back to production specifications, reassembled, and tested such that the expected performance can be defined and warranted (two years, or 24,000 miles, whichever comes first). It’s an entirely different level of quality than aftermarket transmissions that may be called “rebuilt,†which typically means replacement of only those components that may be broken or unusable, without a complete disassembly and precision inspection.
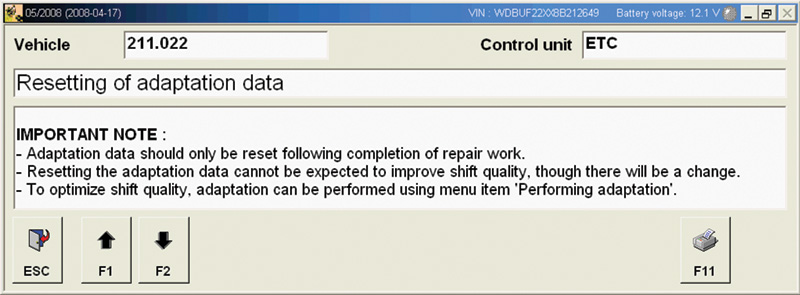
Either as a diagnostic procedure, or after the repair is complete, reset the transmission adaptation tables. There will be a noticeable change in shifting. Drive the vehicle and feel if any shifts are not smooth. From here, you can force the adaptation to improve shift quality.
Finally
Mercedes-Benz transmissions are completely capable of lasting 200,000 miles and beyond. Using smart computers along with regular maintenance increases their life, but ultimately an overhaul will be required. Take the time to read the adaptation data and explain to customers what is in their best interest. In most cases, you’ll find that the typical Mercedes-Benz owner will be willing to invest in the repair.
0 Comments