Hybrid construction techniques have provided Mercedes-Benz vehicles with even stronger and safer bodies. Your job as a professional collision repairer is to maintain the vehicle’s structural integrity in all phases of collision repair. This can only be done through the use of the company’s comprehensive technical information resources.
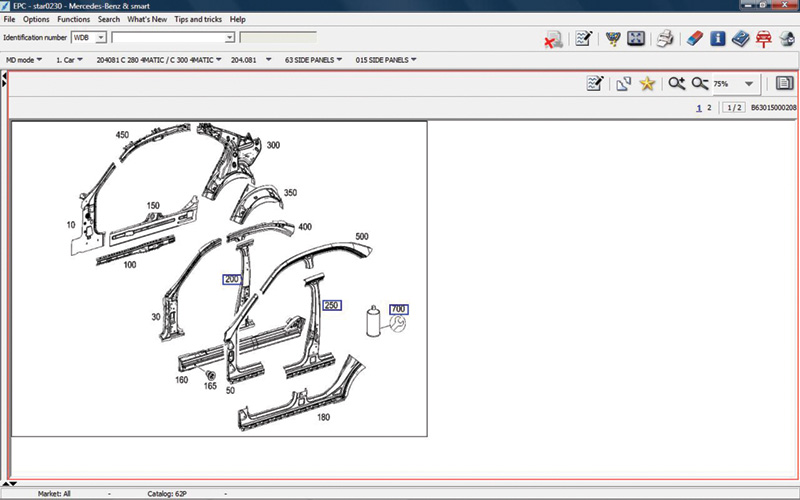
Using the Electronic Parts Catalog (EPC), you can follow along with the dealer during your parts order. In this case, you will need body cavity foam to finish the job. If a panel is workable, you can compare the cost of working to the price of a replacement panel.
If you’ve been in the collision repair field for any length of time, you’ve probably noticed the changes Mercedes-Benz has made over the years to chassis construction, and its use of advanced materials such as ultra-high-strength boron steel and magnesium. The CL (215) was one of the first models to require technologically-advanced collision repair techniques due to its hybrid construction. Its innovative combination of materials requires special assembly techniques, which must be performed by well-trained technicians with approved equipment, as required by Mercedes-Benz Certified Collision Facilities.
Any modern Mercedes-Benz chassis is designed to be not only strong, but also repairable. Crumple zones are replaceable, and body panels are modular. This is one important advantage of owning a Mercedes-Benz vehicle. Not only will the body protect its occupants in the event of a collision, but after the proper repairs are made the crashworthiness is maintained. Mercedes-Benz believes strongly that only the approved procedures and materials can achieve this goal, and has made sure all the information you need for this work is available.
Higher standard
Too many customers either just want their cars back as fast as possible, or only care that the paint has that “new†look. Any body shop can satisfy those desires, but you hold yourself to a higher standard. A certified Mercedes-Benz repair shop guarantees its work. The auto body industry is consistently looking into sub-standard repairs made with inexpensive replacement parts and is finding that many do not even meet minimum requirements.
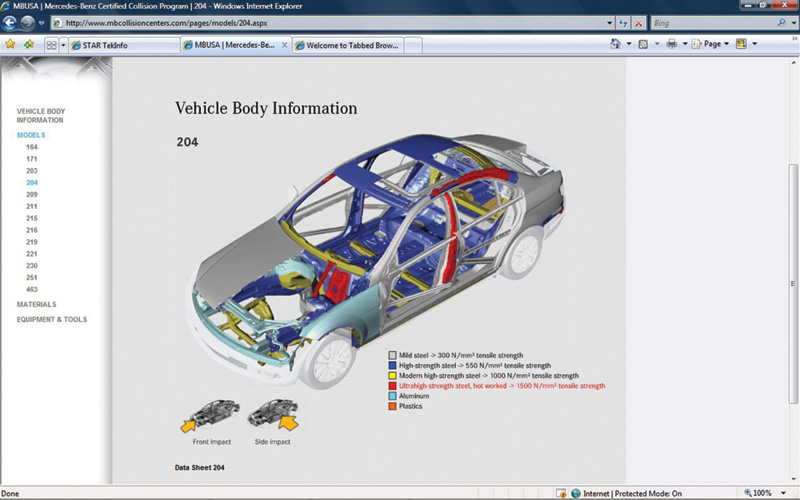
In this computer-enhanced image, the red color of the B-pillar indicates that this is ultra-high-trength steel. It is formed while heated, so it cannot be worked back into shape easily. You will need highly specialized tools to cut out the panel and drill out holes for rivets.
Beyond hammer and dolly
Non-Genuine replacement parts are subject to improper fit and finish. Wasted time, correcting mistakes and additional steps prepping the surface can take the profit out of a job. You must make sure the inner structural panels are fastened properly by means of the correct established process. Two of your most important tools, aside from your hammer and dolly, are no longer in your tool box, but on your computer. STAR Tekinfo combined with the Mercedes-Benz Collision website are the first things you should use before starting any repair job. If you are managing a repair, you can look at the steps involved in the repair, and plan for the hours required. This information is also very useful for informing adjusters of the time and cost of certain procedures. Without these resources, you might not be getting paid for all the work you need to perform.
Another time saving tool is the Mercedes-Benz Electronic Parts Catalog (EPC). Here, you can look at the same exploded views of available collision repair panels as the dealer and be reading off of the same page. There are distinct advantages to ordering only genuine Mercedes-Benz replacement parts. Your dealer’s parts department can help you with additional support components and hardware. Rivets to attach panels, structural adhesives, and special fasteners are all part of a repair job now. Where welding isn’t possible, a combination of riveting and bonding is used . These hybrid-construction vehicles now require new repair procedures to maintain structural strength.
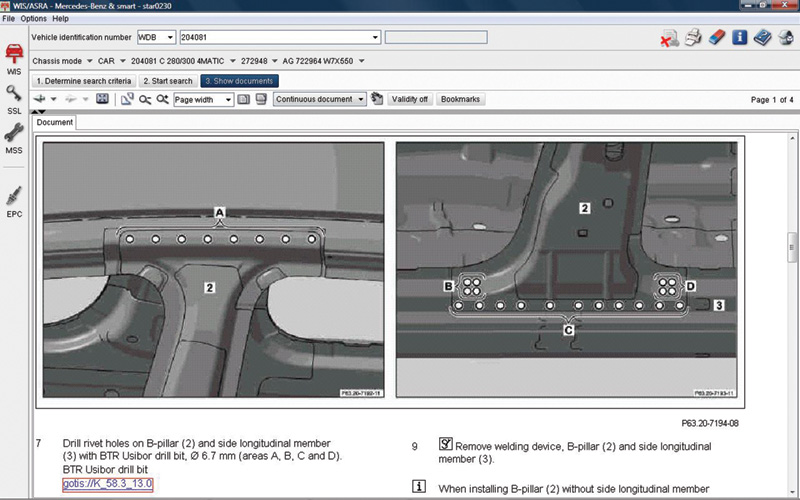
For step-by-step replacement procedures for the B-pillar, consult WIS. It will guide you through everything you need to know, including panel preparation, attachment methods, and tools required. Detailed instructions on bonding, riveting, and locations ensure that the job you perform will have the same strength as the original.
Your repair staff can follow step-by-step procedures with drawings that show panel arrangement and proper fastening methods. This will make their work easier and increase their productivity.
B-pillar example
Two major concerns must be addressed during a repair: Proper procedures and the latest materials. Being a Mercedes-Benz Certified Collision Center grants you access to the Mercedes-Benz Certified Collision Program website. Here, you can access body construction cutaways. You are informed of what a certain panel is constructed of and how to attach the various metals. Look at a driver’s side impact to a 2008 Mercedes-Benz C300 4MATIC (204.081) four-door at the B-pillar, for example. The B-pillar will have to be replaced. Looking at EPC, you can see that the B-pillar has two separate inner and outer pieces. Also, a special foam is used to fill body cavities and reduce road noise. Without this site, you might not be aware that you must order this foam along with the other parts.
By viewing the Mercedes-Benz Collision site, you can see that the inside B-pillar is made of mild steel, and the outer portion is made of ultra-high-strength heat-formed steel. This metal is too difficult to work, so unit replacement is necessary. You can go to “Materials†and you will see what methods can be used to secure that panel. In this case, resistance spot welding, riveting, and bonding are permissible, but not MIG welding. To continue with the job, look at WIS. You’ll see in steps 5, 6, and 7 that while the panels are clamped in place, several holes need to be drilled, countersunk, and deburred to prepare for rivets. Since you are working with ultra-high-strength steel, WIS lets you know that a Usibor 6.7mm drill bit will be needed.
These holes will accommodate the special high-strength rivets that will be required to secure the panel. Using any other type of rivet for aluminum or steel will weaken the structure. These weaker rivets will fail if there is a second collision. Your Mercedes-Benz parts supplier can provide you with these special rivets. The recommended combination of welding, chemical bonding, and riveting is the only means of securing this panel properly. Following the steps outlined in WIS will ensure this portion of the chassis will maintain its strength. There are a total of 30 steps for this procedure, so you need WIS to keep track.
While you’re on WIS, you’ll find many other important facts and tips, such as:
- How to perform the “snap-out†test to make sure you’re achieving optimized resistance spot welds.
- Preparing aluminum for bonding, use a CrNi wire brush.
- An adhesive connection will regain its original strength after cooling down as long as it’s not heated above 200 deg. C.
- Bonding pre-treatment primer should be applied in a thin coat with a brush, then bond immediately.
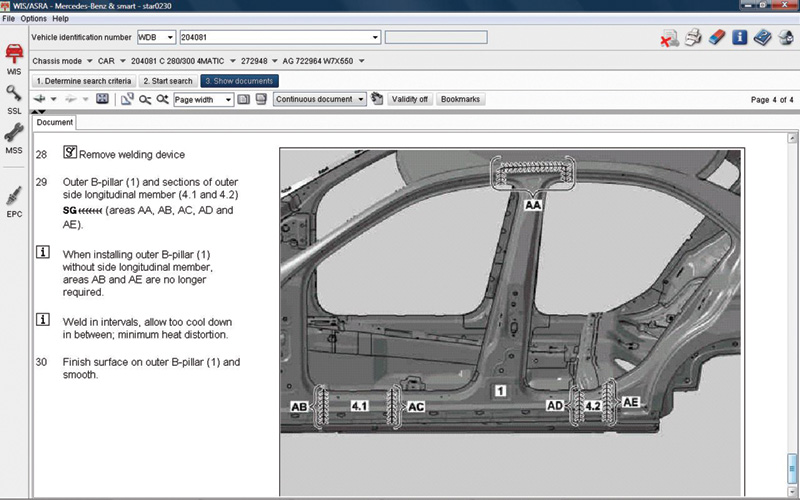
A combination of welding, chemical bonding and riveting secure this panel properly. When welding, let the panel cool between welds to reduce panel distortion from excessive heat. Following the steps outlined in WIS will ensure that this portion of the chassis will maintain its strength.
There’s much more, of course. Once you learn how to navigate through these sites and how to “drill down,†you’ll always be able to find the answer you need.
Keep in mind that knowing approved procedures not only affects the quality of the repair, but legal liability as well. While detailed information on where to use what is available online, the best way to become truly familiar with the proper way to perform the process is to attend a Mercedes-Benz training course.
When dealing with hybrid-construction vehicles, you need to become as comfortable with chemical bonding and riveting as you are with welding. Ultimately, Mercedes-Benz’s main concern is occupant safety. Maintaining this is how we maintain our integrity.
0 Comments