An important part of any well-engineered vehicle is its handling. A taut suspension provides precise control and safer driving. But when the components involved wear out, the suspension can’t perform as designed.
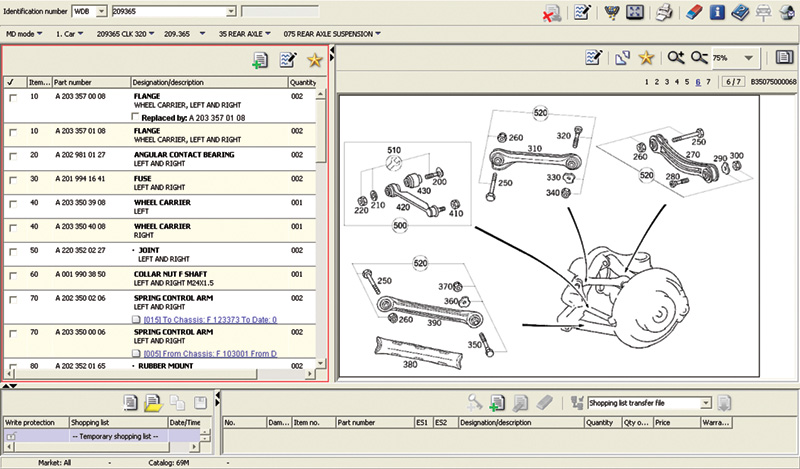
Using EPC, you can get a good idea of what type of suspension a vehicle uses. This 209 chassis rear suspension is one of the few with a tie-rod end in one of the rear links, similar to the 202/203 chassis. EPC will also help you communicate with your Mercedes-Benz parts dealer about your parts order.
Superb handling is one characteristic of Mercedes-Benz vehicles that sets them apart from all others. Two basic factors in that are a taut, yet compliant, suspension, and versatile steering geometry. Any mechanical system made by man, however, will wear over time. In this case, excessive wear will change the vehicle’s dynamics, reducing both its fun-to-drive quotient and safety. Since the degradation is gradual, the driver may not notice it right away, but sooner or later there’ll be symptoms such as vibrations in the steering wheel or the whole front end, and noises while driving over bumps. Damaged or worn-out ball joints and bushings are the most likely culprits, but troubleshooting them isn’t always so easy.
If you are going to efficiently isolate a problem in the front or rear suspension, you should take a good look at the components involved. Struts are used in the front suspension system of the 203 chassis of the C-Class. You will see a strut, spindle, lower control arm, and a strut arm. The lower control arm anchors the lower part of the spindle, and the strut assembly secures the upper part, and determines camber. The strut arm controls caster, preventing the strut assembly from moving fore and aft. Both the lower control arm and the strut arm have a ball joint at the spindle end and bushings at the sub-frame end. The bushings are serviceable separately. Some 4MATIC vehicles have a single lower control arm with one ball joint and two bushings that are not serviceable separately.
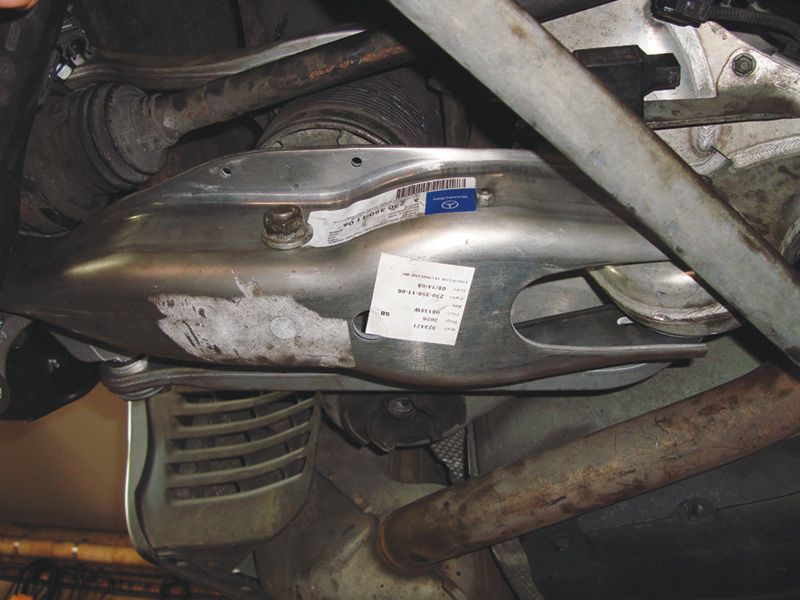
Here, a rear lower control arm needed to be replaced. Using OEM parts supplied by our Mercedes-Benz parts dealer, the fit of the component was the same as the original, so there was no extra labor wasted in trying to get an aftermarket part to fit.
The rear suspensions on most 202/203, E-Class 210/211 chassis, and C- and S-Class 215/220/221 are spring/shock systems, perhaps with optional pneumatic and hydraulic spring/shock assemblies. The rear suspensions are of the multiple link type with one large lower control arm that supports the spring/strut assembly and four additional links to control camber, caster, and toe throughout suspension travel. Almost all of these links have bushings that are sturdy and easy to check, but may be difficult to replace depending on their location. The leading upper arm of the rear suspension requires that the sub-frame be dropped. With hydraulic suspension, you won’t have to worry about releasing the pressure because there isn’t any as long as the engine isn’t running.
The front suspensions of the 215/220/221 chassis have a combination of multi-links and A-arms. There are still lower control and strut arms, but the upper spindle connects to an upper A-arm with two bushings and a single ball joint. On original A-arms, the ball joint is built in. Newer replacement arms make the ball joint serviceable, so you do not have to replace the whole arm a second time. Lower ball joints are also serviceable on certain models. The 210/211 chassis is slightly different. A strut supports a lower control A-arm and the upper arm controls an elongated upper spindle. The lower ball joint is serviceable, but the upper gets replaced with the arm.
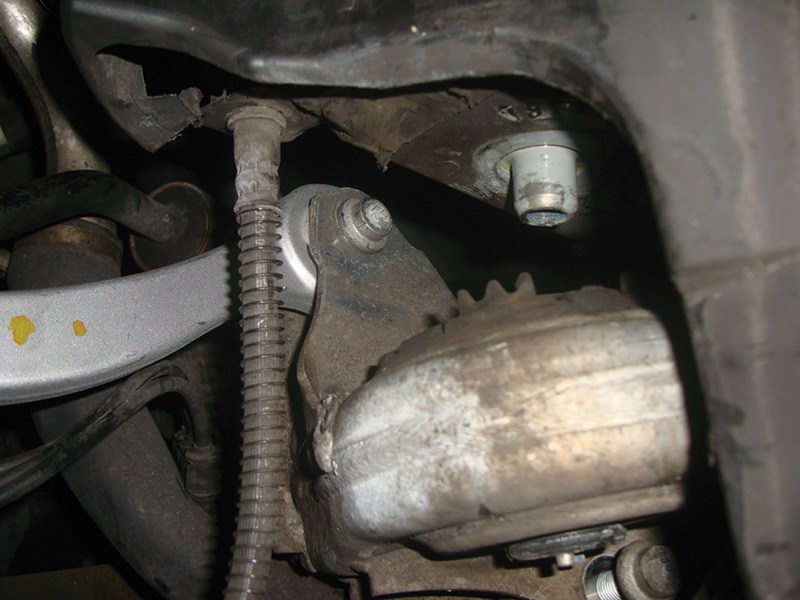
On most chassis, if the forward upper link of the rear suspension needs to be replaced the sub-frame will have to be dropped to remove the bolt. Here, the technician has reversed the direction of the bolt to make future service easier. If the vehicle has a hydraulic suspension it needs to be depressurized with the SDS before beginning the repair.
Bushings can soften and crack over time, so inspect the rubber insert carefully using a good light. Typically, a bushing has an outer housing attached to the arm, an inner mount secured to the chassis and a rubber webbing in between to absorb vibrations. If the rubber has cracked, it will allow the arm to vibrate with road irregularities. This can be felt in the steering wheel and the chassis. If oils from the other systems under the hood leak onto the bushings, they can soften them and allow excessive steering deflection. This changes handling characteristics, especially under heavy loading. In many instances, bushings can be replaced separately, but you should also check the joint at the other end of the arm as it may need to be replaced as well.
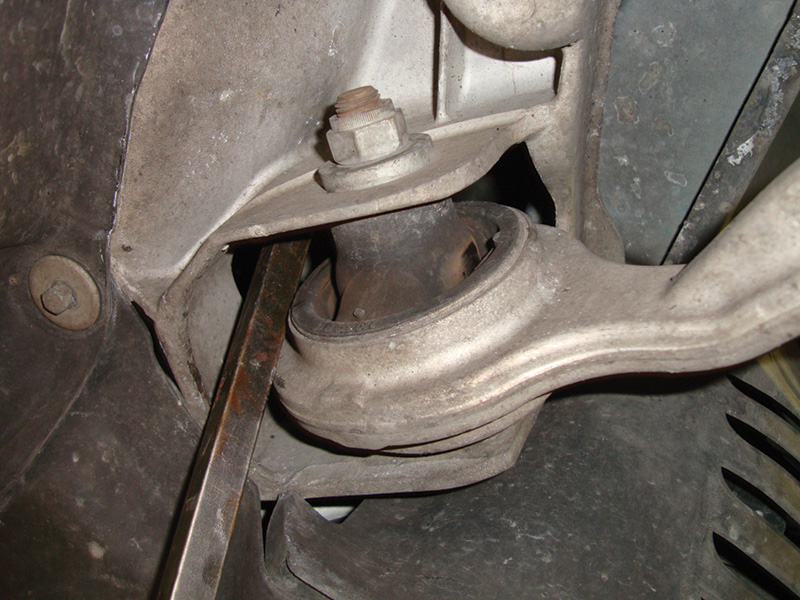
Mercedes-Benz does not recommend the traditional practice of prying between the chassis and the arm to check bushings as it’s too easy to damage them, especially if they are of the hydro-bushing type. Instead, do a thorough visual exam using a good light. Look for deep cracks and leaking fluid. Note that the new ones will probably have to be installed in a specific position. Check www.startekinfo.com for the proper procedure.
Ball joints can be slightly more difficult to diagnose, and there’s a specific procedure for each model in WIS, some involving special gauges. Look it up. If the protective rubber boot is ripped or removed, debris can get stuck in the grease of the joint and cause premature wear. Bushings don’t tend to cause rattling noises when they are worn, but can cause a knock in certain situations. Ball joints can allow metal-to-metal contact that can result in noise as well as vibration. Other components that can cause a light noise over bumps are the sway bar links. They are typically
ball joints that move up and down with the sway bar especially when the vehicle is steered vigorously.
Deteriorated strut bushings can cause unpleasant symptoms in the front end. On some models, they are oil-filled to help reduce vibration, but still remain compliant. Aftermarket bushings can be stiffer, but the stiffer the bushing the more road irregularities will be felt by the driver (that’s why they’re used in racing applications). Polyurethane bushings will not suppress noise and vibration, but will add to it. This is why it is best to replace them with the genuine OEM part.
Wheel bearings are another factor. Older designs used tapered roller bearings that we could clean, repack, and adjust to eliminate excessive play, but more modern hubs have sealed bearings that are not adjustable. They are sturdy units, but when they wear out they can be difficult to diagnose. You can check radial and axial play by rocking the tire at the 12 and 6 o’clock positions, but sealed bearings will often make a roaring noise long before you notice any deflection. While driving in a safe area, turn the wheel side to side and listen for the noise to increase and decrease through the turns. You may want to have someone else driving while you are listening with a tool that allows you to hear the bearing noise at the source.
Front and rear suspension work can be a profitable, cost-effective service you provide your customers. It offers them all of the handling and car control they are used to. When servicing the vehicle with Mercedes-Benz parts, you will find that most customers will appreciate the quality service you provide. What could be better than that?
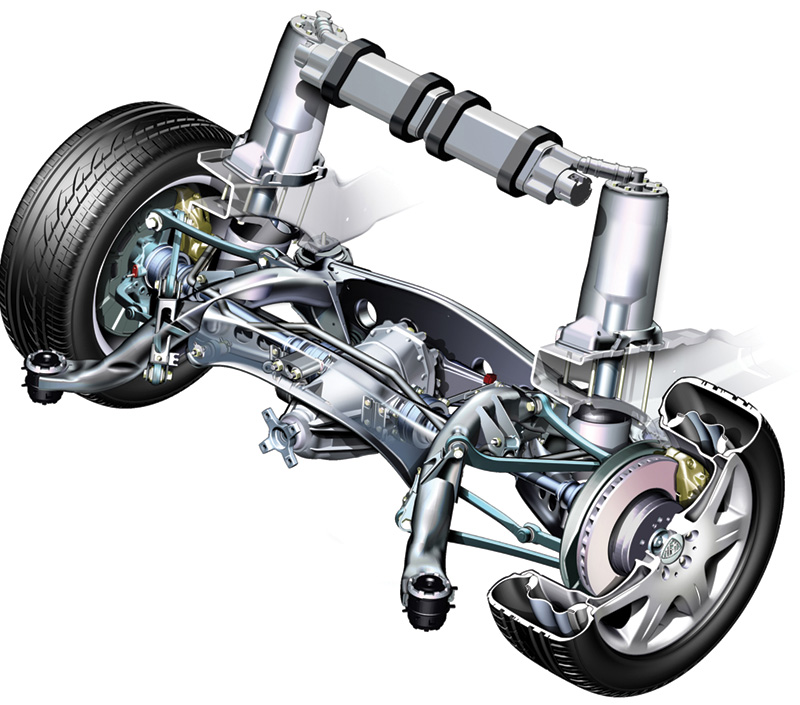
Mercedes-Benz’s multi-link rear suspension helps achieve an unparalleled combination of sporty handling and ride comfort. The many bushings, joints, and other components involved will eventually require that you do a very professional inspection.
0 Comments