I was called in to a shop for a complaint of no power window operation on a 2003 Pontiac Bonneville SSEI (Figure 1). They had already checked the power and ground feeds at the driver door master switch and everything seemed okay. The odd thing was that the other door windows would not operate from their individual switches. It was just hard to believe that this vehicle could have four bad window switches. The window motors all worked okay when power and ground were applied to each motor individually. The garage was uncertain where to turn, so rather than throwing parts at this car they decided to call me in for a second opinion.
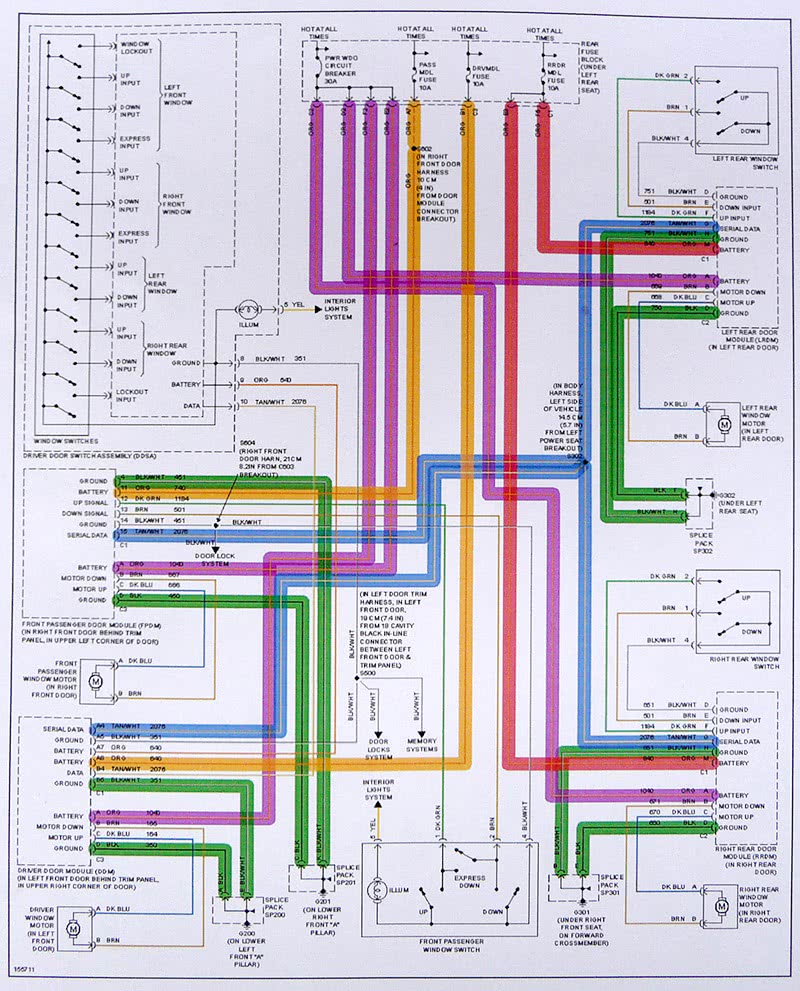
Figure 2: Color-coded Power Window Circuit diagram. Green: Grounds, Purple: high-current circuit breaker feed, Orange and Red: low-current battery feed.
When I arrived at the shop I verified the complaint by trying each power window switch and nothing responded. I next decided to print out a wiring diagram to familiarize myself with the system layout and see if I could find something in common that would affect power window operation at all four doors, such as a main power or ground feed. As I viewed the diagram, I found out that these were not your everyday “how you doin'” window switches. Instead, they were all separate door control modules. Each module in turn controlled window motor operation through an internal window motor driver. Operating the window switch only created a high/low signal to command the window up or down. The switch no longer had to transmit a power or ground feed to the window motor directly, which made for less wear and tear on the switch contacts.
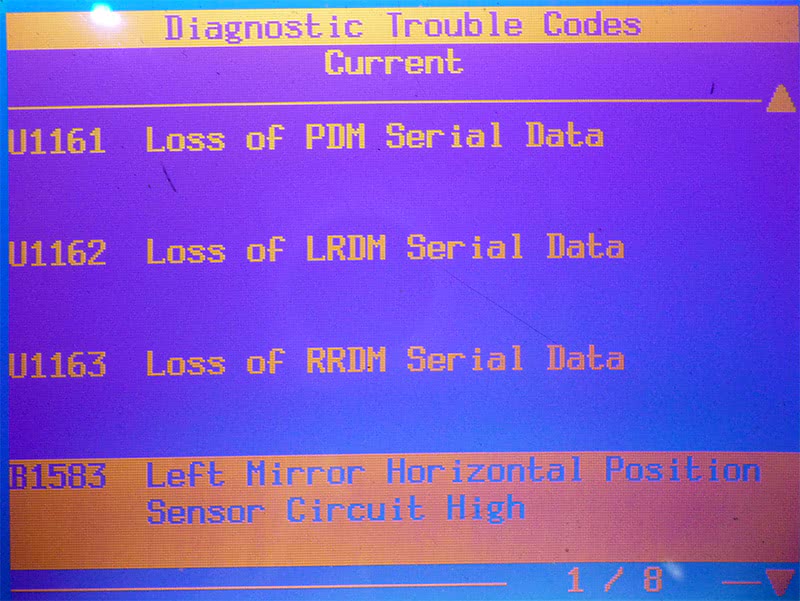
Figure 3: I discovered that the driver door module had the ability to communicate with a scan tool by looking at a data communication wiring diagram, which showed all the onboard controllers on the serial data network linked to the ALDL connector.
I used my Paintbrush function in Mitchell to color-code the wiring diagram. I chose green for the grounds, purple for the high-current circuit breaker feed, orange and red for low-current battery feed (Figure 2). The ground feeds for each door module were at different locations, so it was hard to believe that the system had four open grounds. The rear door modules shared the same low-current battery feeds, but the front door modules had two other separate low-current battery feeds, so here too nothing seemed common to all four door modules. Looking a little closer at the diagram, I could see that all four modules did share the same high-current feed from a 30 Amp circuit breaker, so this was the first place I wanted to look.
I used my test light and checked each door module for high-current battery feed, and they all seemed to be okay. The tech said that all the wiring checked okay, and it did, but I still had to see for myself because you just never know. There have been many times when techs have used a logic probe to do a power and ground check without finding anything, yet a bad ground or power feed turned out to be the culprit. They relied on the logic probe’s ability to light a green or red LED as a valid check, which only required about 20 mA to light up, but when the ground or power had to step up to the plate to handle a a high-current circuit it would lose it’s connection. This is where a standard test light, which can load a circuit up to 300 mA, would be a better choice. Keep in mind, though, that this type of test light cannot be used on computer circuits because it can harm them.
I discovered that the driver door module had the ability to communicate with a scan tool by looking at a data communication wiring diagram (Figure 3), which showed all the onboard controllers on the serial data network linked to the ALDL connector. So, I hooked up my GM Tech II scan tool to see if there were any trouble codes stored in memory that could lead me in the right direction. Looking at the scan tool, I pulled some “U” codes of interest (Figure 4). The codes U1161, U1162 and U1163 all pertained to the driver’s door module’s inability to talk to the other three door modules. There was no access for my scan tool to talk to the other three modules because it was only able to access the mainstream controllers all on one network as seen in the communication link diagram. The door modules had their own private UART network that was shared among them, as can be seen by the blue colored-coded lines in the Power Window Circuit diagram (Figure2). This seemed like a possible culprit if there was damage to this private network.
According to the diagram, there was a splice for this private UART network located under the rug about 14cm from the left power seat breakout. I had the shop remove the front driver’s seat, and as I lifted the rug I noticed a lot of rust build-up on the floor from a prior water leak (Figure 5). I next located a conduit that held the splice internally wrapped with black electrical tape (Figure 6). I slowly removed the tape and was surprised to see a Scotch Lock connector joining all four UART lines going to the door modules (Figure 7). This connector was badly corroded and was barely making a connection for all the wires to share. I removed all of the wires and repaired the splice. Suddenly, all the windows were working fine.
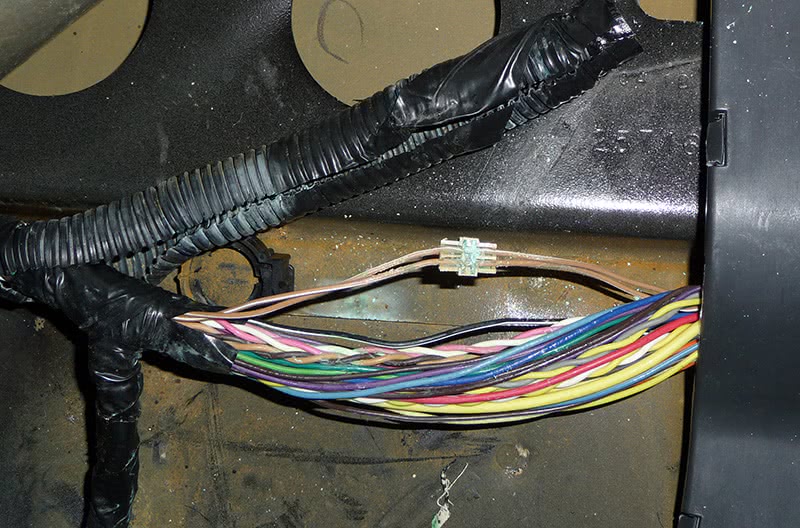
Figure 7: I removed the tape and was surprised to see a Scotch Lock connector joining all four UART lines going to the door modules.
So, now the recap on this whole scenario. I discovered that the door modules were on a private network with each other and even though they had their own power and ground feeds and switch signals, they all refused to operate when they were unable to communicate with one another. It was a default built into the system. What was amazing to me was why any manufacturer would use a Scotch Lock to connect these wires inside a harness running along a floorboard. Wouldn’t it have been better to use a solder joint located in a higher area not so susceptible to water damage? But, then again, who am I to second-guess the engineers? There’s always the possibility that this was a field repair done by another shop.
I hope this story has enlightened you to better understand how a network, whether large or small, needs to be in proper order, or things may not work the way they were intended to. Just doing a simple power or ground check at a component does not always validate system integrity. Parts replacers beware!
by John Anello
0 Comments