New steels, alloys and materials are forcing a collision repair reboot.
The collision industry continues to be under the gun. According to the American Iron and Steel Association, 60 percent of the steels and alloys used in manufacturing cars today did not exist a scant 15 years ago. Since then, the use of new steels and metal alloys by Nissan and other automakers has grown quickly; it is also expected to accelerate over the next two decades.
These new metals must be identified early, as their higher costs impact estimates. Moreover, because they require radically different repair procedures than conventional mild steel, this trend presents a variety of dynamic challenges for collision repair facilities.
The New Mantra: Higher Strength, Lighter Weight, Improved Occupant Safety
In the 1990s, Mild Steel (MS) accounted for nearly all of the steel used in vehicle manufacture. MS offered adequate strength and enabled easier collision repair because of a more stable collision repair knowledge base, somewhat stable manufacturing materials, and simpler repair procedures and skills.
Increasing consumer demand for better performance, improved safety, reduced noise, smoother rides, solid handling and infotainment features are prime change agents. In addition, regulatory initiatives for better crash safety and roof crush standards, improved fuel economy and lower CO2 emissions have also spurred the OEMs to move away from MS. Also, the advent of heavier, alternate hybrid and all-electric propulsion systems have made the use of higher-strength steels a cost-effective, practical solution.
Over the past decade, innovative new steels, aluminum, magnesium and titanium have been increasingly used by automakers to meet new and inbound regulatory statues for improved fuel economy, emissions, safety and environmental responsibility. In addition, other new nonmetal materials, such as carbon fiber, polyurethanes and adhesives are being used increasingly.
Compared to mild steel, the newer steel classes (listed in order of increasing strength and formability) include:
- High Strength Steels (HSS), such as bake-hardenable and some dual-phase steels, handle more stress, provide better resistance to fatigue, improve crash energy management, and allow overall vehicle weight reduction and associated cost savings. Better suited for any structural and crash-sensitive parts, HSS are often found in rocker panels, B- and C-pillar reinforcements and cross members.
- Advanced High-Strength Steels (AHSS), which include more advanced Dual-Phase Steels (DPS) and Transformation-Induced Plasticity steels (TRIP), have similar initial yield strengths as HSS, but also have much higher final part strength and provide higher energy absorption at a lower overall cost than both MS or HSS parts. AHSS content is typically found in roof panels, front rails, crush cans, and reinforcing inner rockers and pillars.
- Ultra-High-Strength Steels (UHSS), such as boron steel, incorporate molybdenum to create steel with benefits that only higher-priced aluminum or titanium could offer in the past, but at a lower cost. Applications include door beams and bumper beams.
For Nissan and Infiniti vehicles, these benefits translate into increased strength, lightweight composition, improved energy absorption at impact and safer energy transfer around the passenger cabin during a collision. It is not unusual today for 40 percent of a new vehicle’s composition to be AHSS or other high-strength metals; in a number of cases, such as the Nissan GT-R, that percentage can be much higher.
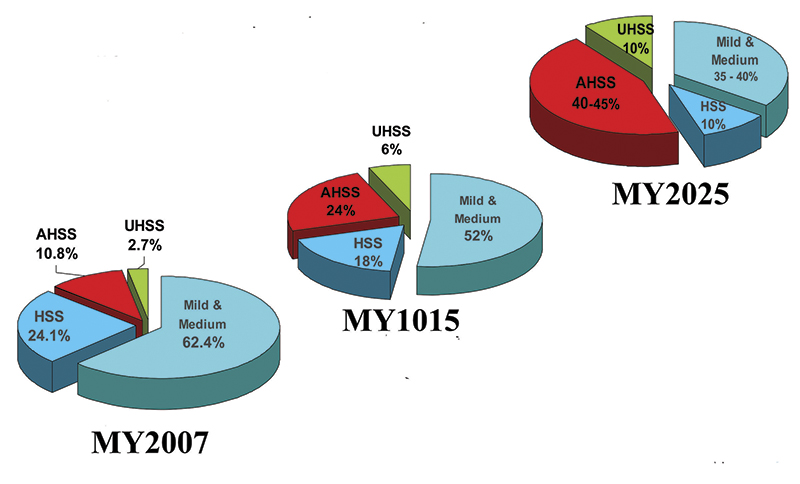
The shift from mild steel content in automobile body and closure structures to increasingly more high-strength steels (HSS), advanced high-strength steels (AHSS), ultra high-strength steels (UHSS), other metal alloys and even nonmetal materials is forcing a shift in collision repair
Rethinking Collision Repair
“Increasing vehicle structure complexity has the potential to put us all out of business,†says Jeffery Poole, performance training coordinator for the Inter-Industry Conference on Auto Collision Repair (I-CAR). “But maximizing survivability has been the driver in automobile design, not repairability.†By incorporating stronger steels in key areas — such as B-pillars, rails, cross members and fuel tank reinforcements — collision energy forces can be controlled and transferred away from occupants.
Looking forward, collision shops must adapt their repair knowledge, procedures and skills at an accelerating rate to keep pace with technological changes being made to vehicle structures. While some shops may find the task overwhelming, others will seize the opportunity. Either way, a facility’s survival will hinge on replacing old repair paradigms with a thorough understanding of these new materials.
The shift from mild towards increased higher-strength metals has fostered a number of wide-ranging challenges for collision professionals, including the ability to:
- Source accurate service information for collision repair, with specific access to locations of various steels in a vehicle structure. For example, some structures may require partial disassembly before you are able to prepare an accurate estimate for repair. Nissan’s www.nissan-techinfo.com and Infiniti’s www.infiniti-techinfo.com websites provide the most current and accurate information available.
- Identify the type of steel in an assembly to then determine whether to repair or replace. While automakers provide guidance specific to each type of steel present in their vehicle structures, repair professionals should be aware that Nissan and Infiniti recommendations for steel classifications may differ from those of other automakers. Don’t assume that what works for one manufacturer works for all.
- Determine whether or not there are multiple steel types within damaged assemblies. B-pillars, for instance, can be made from a combination of MS, HSS and AHSS; repair procedures may vary according to each steel type. Both service information and industry-recognized training are resources to help you determine the appropriate repair procedures for each Nissan and Infiniti model and year.
- Learn the specific and appropriate repair procedures that must be used to restore a vehicle to its pre-collision state. Repairers must know, based on steel type, whether heat or cold straightening is appropriate, whether sectioning or replacement is needed, what type of welding is required and more. I-CAR, for example, offers a one-day course focused entirely on collision repair for the GT-R supercar. In addition, I-CAR has just successfully piloted a new course titled “Best Practices for High Strength Steel Repairs†that addresses the challenges of working with HSS, AHSS, UHSS and some of the identified best practices that a shop should utilize whenever working with these materials. Expect this course to be available to the industry shortly.
- Equip facilities with Nissan and Infinfiti-approved collision repair equipment. Visit Nissan Tech-Mate at www.nissantechmate.com to seek advice or lists of required/recommended collision repair equipment that has been approved by the automaker. For example, Nissan recommends the use of a Celette dedicated fixture system for GT-Rs to help restore the original accuracy to the vehicle.
Customers should also be informed that they can insist that only genuine Nissan collision parts be used to complete repairs. Nissan provides a form that facilities can provide to customers for this purpose. Insisting on genuine parts meets Nissan design specifications maintains vehicle and corrosion warranty protection, provides time-saving form and fit and avoids compromising post-repair occupant safety, should a repaired vehicle be involved in a future collision. For example, the hood on an electric LEAF is designed with hood buckling creases to help prevent the hood from penetrating the cabin interior; non-genuine aftermarket hoods may not provide such built-in safeguards.
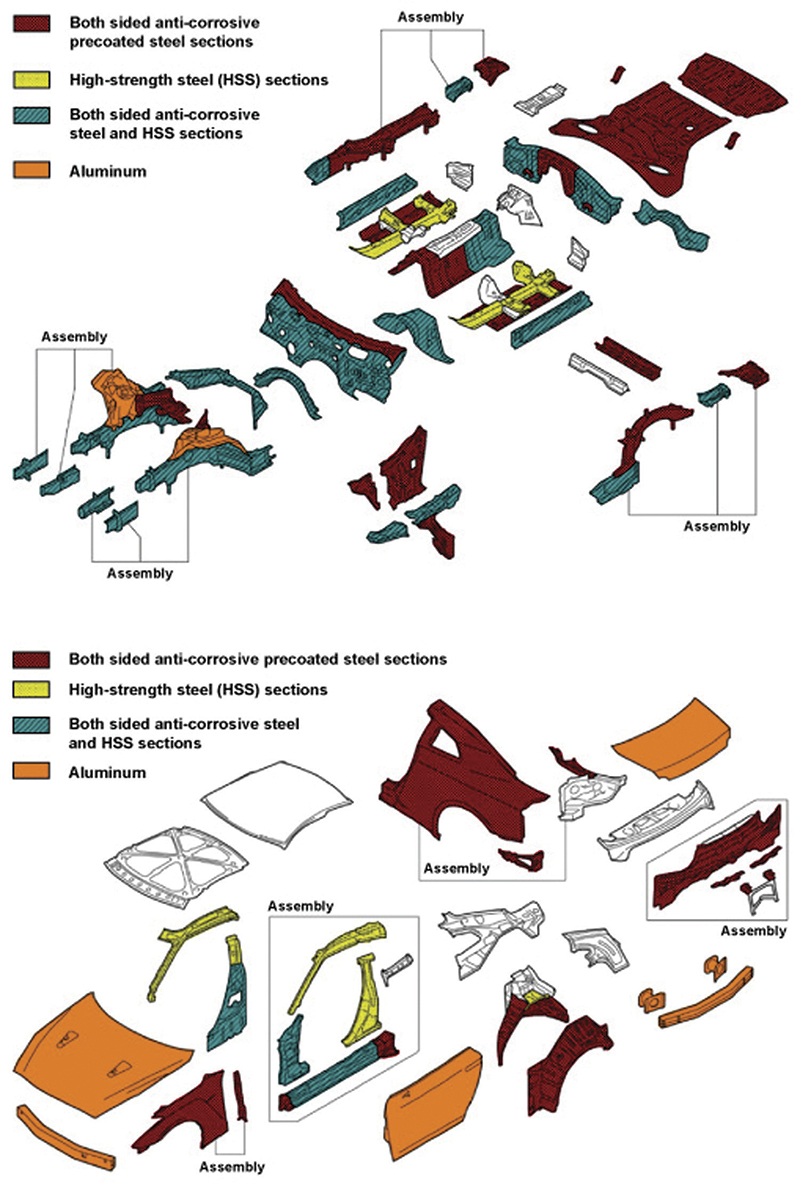
Nissan provides color-coded diagrams of its vehicles that denote the location of various types of steels and other metals in its vehicles, such as this one for the GT-R. Used in conjunction with Nissan service information, recommended repair procedures and proper equipment, these resources help facilitate complete, safe repairs.
Implementing New Repair Procedures
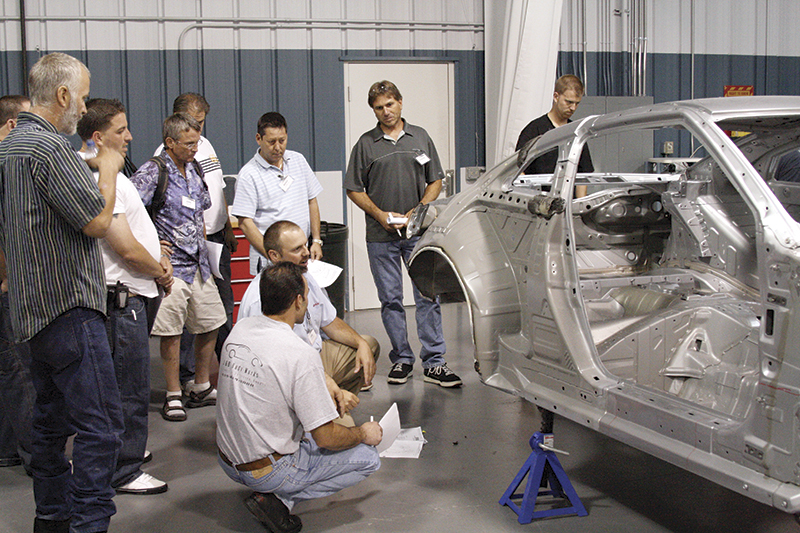
I-CAR offers several collision repair courses focused on higher-strength metals. For example, Nissan and I-CAR partnered in developing a GT-R course, available to professionals, that Nissan recommends.
Technological change has impacted the mechanical side of the service and repair industry for a longer period than the more recent innovations now affecting the collision side. As a result, mechanical service information is abundant and service information gaps are few. However, the recent and very rapid influx of newer steels, metals and other advanced materials requires ongoing collaboration among Nissan, the collision industry, trainers and regulators to ensure that vehicles are repaired safely and completely.
“We must employ better repair planning right from the start,†says Bob Keith, senior director of Education and Training, CARSTAR Franchise Systems. “We need to be better researchers in order to find the correct repair information to ensure we’re on the right repair track.â€
Once an accident occurs, it is essential that a facility determine what is wrong through proper identification and accurate measurement. Research may be necessary to discern what metals are present and the associated repair procedures and proper equipment required to return the vehicle to pre-crash condition. Then they must thoroughly document and present this information to both insurers and customers.
Access to repair information can be another hurdle. “We need to continue to work with Nissan to get collision repair service information,†says Keith. “I don’t think repairers are aware how much information is out there and where to find it.â€
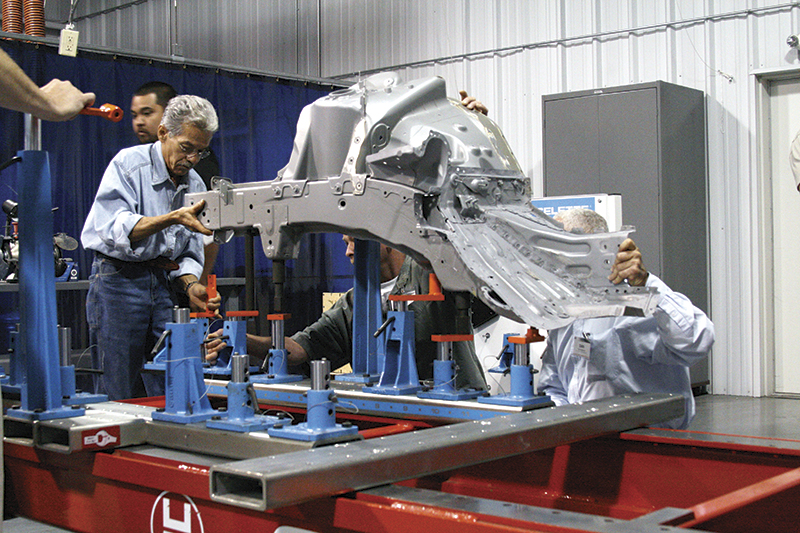
Having a sound repair plan right from the beginning is critical for the collision repair of newer steels, aluminum and other metals. Follow Nissan recommendations and resources regarding the use of heat, sectioning, replacement, welding, documentation and other procedures to ensure that repairs are cosmetically pleasing, maintain the crash-safety rating and protect the facility and staff from future legal repercussions.
Nissan makes collision repair information available through its aforementioned websites. While most information is available, occasionally “time-lags†occur — instances where new vehicles are sold and then involved in an accident before collision repair information and procedures are developed and posted on service information websites. Fortunately, the automaker has signed the National Automotive Service Task Force (NASTF) agreement, which requires that any genuine gap identified by a dealer or independent facility, including collision repair issues, be addressed, responded to and resolved.
Most collision facilities, however, are unaware that they can electronically file a collision-related NASTF Information Request should they have a bona fide information gap that needs to be closed. While not one Nissan collision information request has been filed with NASTF to date, it is important to know the option is there. To file a request, visit www.nastf.org/i4a/pages/index.cfm?pageid=3290 at the NASTF website.
“Automakers, such as Nissan, have gradually evolved repair procedure policies because they don’t want repairers re-engineering vehicles,†Poole points out. “The information is out there, but some of it isn’t easy to get to. Should no repair procedure exist for a part made with these new steels, collision facilities must err on the side of safety, even though more costly, and choose replacement rather than repair. Ensuring the insurer and customer are aware of this, and why, before a repair is essential.â€
No More Repair Shortcuts
Knowing where new metals and materials are located is a good first step. But facilities must also be able to complete a proper repair. Traditional repair procedures often cannot be used, as they can damage or destroy the attributes and performance of new steels. Instead, radically different repair procedures specific to new steel types must be implemented. To be fully competent and do no harm to a vehicle structure, professionals should ensure they attend Nissan training (visit the Nissan-Infiniti service information websites) and recognized industry training such as the several courses facilitated by I-CAR (www.i-car.com) that address the identification, estimate preparation and repair of these new materials.
The newer higher-strength steels, for example, must be handled differently from the MS repairers are long familiar with. For instance, as steel strength is increased, it typically becomes harder, more brittle and more sensitive to heat. HSS is generally cold straightened, while AHSS/UHSS is typically not straightened at all. In addition, when MS steel is heated, it is generally strengthened. However, under that same heat, HSS is weakened and AHSS/UHSS can crack, break or be destroyed.
“The investment in more expensive, specialized equipment and acquiring new repair skills on a continual basis compound the challenge for collision facilities,†adds Keith. “Facilities must invest in specialized equipment and be adept at using more complex welders such as squeeze-type resistance welders that can cost up to $40,000, plasma cutters and specialized tungsten-carbide drill bits.â€
In the case of Nissan and Infiniti vehicles, heat should only be used when recommended. Even when welding, follow Nissan and Infiniti recommended welding methods and techniques to minimize the “heat-affect zone,†maintain warranties and avoid litigation. Increasingly, recommendations are trending towards complete part replacement rather than partial repair using heat.
The days of shortcuts and just repairing vehicles so they “look right†are over. Repairers should be aware that even if an improper heated repair of AHSS looks cosmetically correct, in the event of a future collision it will be unable to absorb or deflect energy as originally designed. Should that occur, collision energy is then transferred into the passenger compartment, which creates a potentially catastrophic liability situation for the facility.
Responsibility and LiabilityGo Hand-in-Hand
“As an industry, we need to know how to repair a vehicle and how to represent that repair to consumers, insurers and others,†Poole explains. “Keeping thorough and complete files for documentation purposes, as well as developing sound communication skills to convey concerns and needs to insurers and customers is no longer an option. Rather, it is a best practice and part of doing business today.â€
Poole notes that crash investigation experts, when surveying a vehicle damaged in an accident, review the “prior loss history†of a vehicle. In particular, they review the following:
- Was any prior improper repair in the vehicle’s history a contributing factor?
- Were incorrect repair techniques used that were cosmetic but undermined the vehicle’s safety?
- Were there prior loss issues that were neglected and/or simply not addressed by the last repairer/insurer?
- If a vehicle has had multiple collisions, which facility is responsible for the improper repair?
“The answers to these questions in court can make for an interesting day at the office,†Poole cautions. “Failure to provide a correct and ethical repair, document and communicate it can result in devastating liability claims, whether caused by a facility’s ignorance or its negligence. Neither is a valid excuse.â€
The challenges that collision shops face today — especially with new steels and materials being integrated into vehicles — have the potential to overwhelm or empower success. A commitment to detail is essential. This includes being aware of inbound change; staying current with new technology, equipment and tools; embracing ongoing training as an enabler rather than a burden; identifying and implementing correct associated repair methods; acquiring and maintaining skill fluency; and documenting and presenting concerns to all vested parties. Clearly, the collision repair learning curve has gone vertical. The question is: Are you ready and engaged in the climb?
0 Comments