In today’s collision industry, materials, manufacturing processes, and fastening technologies are advancing at an incredible rate. To keep pace with these changes, collision professionals must ensure they are up-to-date with the innovations being employed by automakers, such as BMW AG (BMW) and its subsidiary, BMW North America LLC (BMWNA).
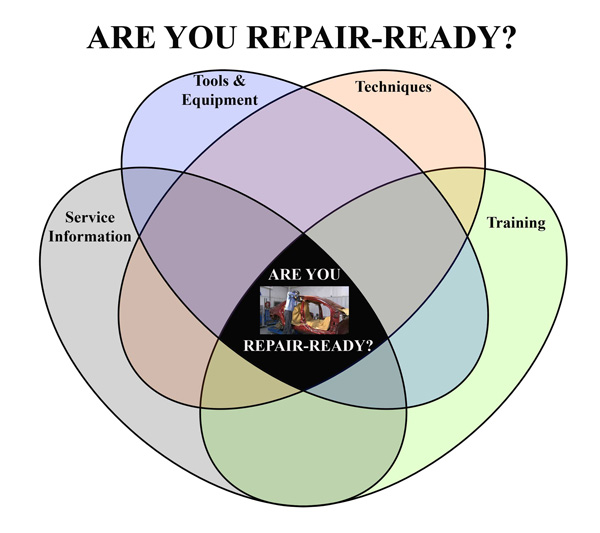
The Collision Repair Sweetspot: Collision professionals must remain current in the four key resource areas shown above. Only then can they be fully competent to perform complete, safe repairs for customers (courtesy ManicMedia LLC).
Chemical bonding is one such emerging and growing trend in collision repair, and it’s being driven by the increased use of lighter, yet stronger materials such as high-strength steels and alloys, innovative plastics, and carbon fiber. Though the use of structural adhesives is not new to the collision industry, the current rate of change and depth of penetration is. It’s critical that repair professionals get familiar with innovative adhesives, tools and equipment, and procedures now.
BMW first introduced new bonding and riveting repair procedures in 2009. Since then, the use of rivet-bonding has expanded to all current models. In addition, improvements in adhesive technology have been incorporated into BMW collision resources. More recently — in response to demands for lighter vehicle weight, better driving and environmental performance, improved safety, and lower manufacturing costs — the introduction of thinner components and new materials is driving the increased use of bonding.
These new high-strength steels, alloys, and plastics come in different grades, which affect how they perform under various stresses not only in normal operation, but also during a collision and the subsequent repair. Body panel repair instructions increasingly prescribe chemical bonding procedures. Others may require the use of adhesives and rivets — a process known as rivet-bonding — or the combination of riveting and spot-welding.
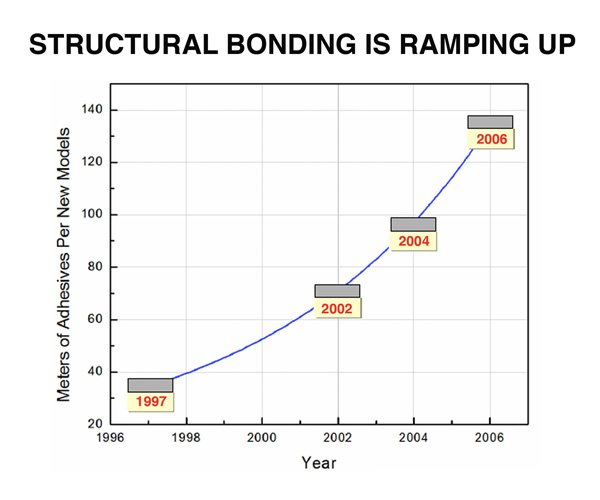
Left: The amount of adhesives used in new vehicle models has been accelerating since their introduction (courtesy Dow Automotive Systems).
Automakers are now aware that the mix of material choices used to manufacture a vehicle requires adhesives that were specifically formulated to match those materials and the time needed to make a repair. Going forward, the repair of BMW body panels, roofs, and other components on production-series vehicles, such as the M3 or M5, demands an understanding and commitment to training to ensure that the correct bonding techniques and practices are employed. It’s also an opportunity.
Advanced adhesive formulations are now available
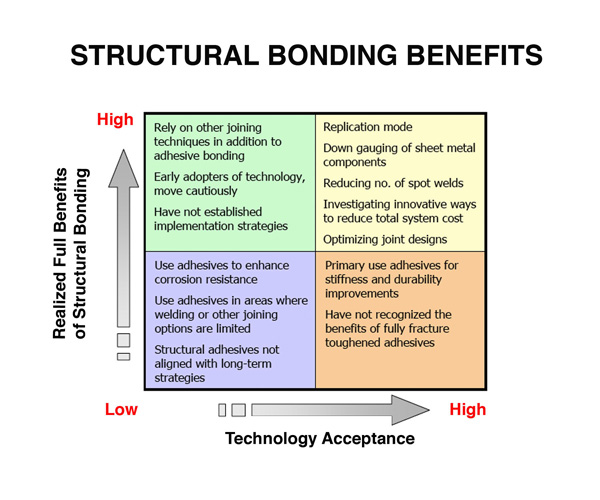
Many benefits have been realized from the shift to chemical bonding, some of them pleasant surprises. One example is the use of thinner body panels without sacrificing strength or safety (courtesy Dow Automotive Systems).
Adhesives are nonmetallic, malleable, liquid, or solid materials that connect one part to another through surface bonding (i.e. adhesion) and internal strength (i.e. cohesion). There are two primary types of adhesives: physically-curing (escaping solvents-seam sealer) and chemically-hardening (typically epoxy resins). Only the latter type is suitable for BMW repairs.
These chemically-reactive adhesives require a mixing ratio specified by BMW. When placed into a joint, the adhesive’s components react with one another and solidify. They are available as one-, two-, or multiple-component products. Their processing time, known as pot life, begins immediately upon mixing; the adhesion forces develop during this period. The processing time depends primarily on environmental conditions, such as humidity and temperature. To ensure proper curing, the temperature of the components and adhesive must be at or above the minimum listed in BMW ISTA information.
Adhesives offer a number of advantages. They prevent thermal component distortion, improve strength and NVH dampening, allow the joining of very thin parts, and reduce weight. The best place to use a structural adhesive is in a location where the primary stress is either compression, where the joined pieces are pushed together, or shear, where the force tries to slide the joined surfaces against one another, like pressing your hands together and trying to slide them apart. In many BMW-approved repair procedures, the combination of adhesives and rivets, screws, etc. can further increase strength.
There are also some disadvantages to using adhesives that limit repair possibilities. These include low peel stress resistance, limited thermal resistance, and the need for meticulous process control including the use of special tools and equipment, and surface treatment of the parts to be bonded with cleaners and primers. For example, structural adhesives are typically not good to use if the force acting on the joint would pull the two pieces apart. Another poor location for a structural adhesive would be one where there are forces that would bend the joint, which could allow it to cleave, then peel. In these latter two cases, repair procedures may specify that adhesives be used together with rivets (rivet-bonding), or in conjunction with certain welding techniques.
Chemical bonding enables stronger, more durable repairs
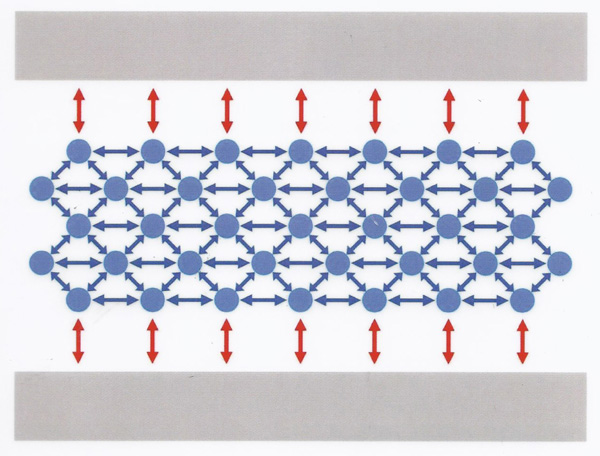
Adhesion and cohesion are the two fundamental properties of adhesives. Adhesion is the attraction between the materials being bonded and the adhesive (red arrows). Cohesion is the attraction between the molecules of the adhesive itself, which occurs as the adhesive cures (blue arrows). To ensure proper adhesion and cohesion, the mixing ratio of the chemically-hardening adhesive used is crucial. In addition, dirt, fingerprints, and other contaminants cannot be allowed between the adhesive and the materials (courtesy BMWNA).
Modern automotive structural adhesives are made from chemicals called epoxies, which typically come with two parts — a resin and a catalyst — that are kept separate until use.
Applying adhesive is no longer a process of just slathering on some glue and clamping the parts together. The surfaces to be bonded require a thorough cleaning, and sometimes, such as with aluminum, primers are also necessary. Once combined, the catalyst initiates curing, a chemical reaction in the resin. Expect to feel the bonded parts heating up as the resin develops its bonding properties.
The curing ability built into an adhesive requires extensive testing and some impressive chemistry to meet BMW specifications. Curing time can range from minutes to days. In some cases, curing may be aided by baking or some other recommended procedure involving applied heat. For example, some epoxies cure when exposed to ultraviolet light.
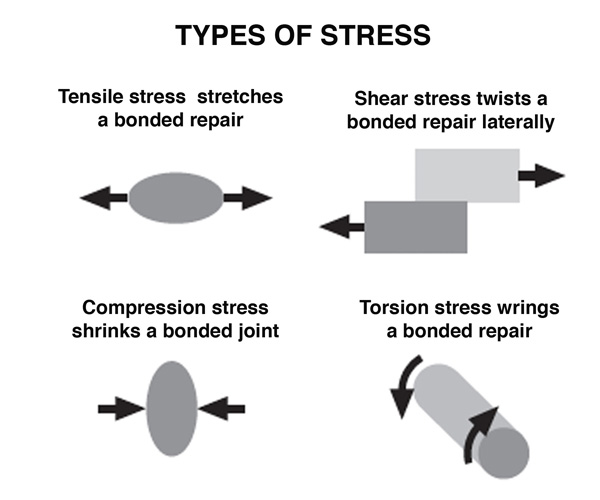
Chemical bonding can often better handle various types of stress than other joining technologies. The diagram above illustrates the major forces involved (courtesy BMWNA).
Automakers know their vehicles best, so following BMW-recommended collision repair procedures and using the approved resources ensures that technicians have adequate working time to effect a safe, complete repair. Refer to www.bmwtechinfo.com. It provides key BMW resources, including collision and mechanical service information, tools, procedures, training, and more.
BMWNA’s recommends five chemically-hardening adhesive formulations. Each has its own storage requirements, shelf life, surface preparation, application, hardening, disposal, and other properties. They also have advanced special polymers, epoxy resins, adhesion promoters, and other additives that improve bonding, manage stress more effectively, provide better mechanical properties, and resist corrosion better than alternative joining technologies. These enhancements enable the adhesives to:
- Provide more durable and stronger repairs with less corrosion risk than convention welds. As carbon fiber composites are increasingly used for roof panels and other components, adhesives will have to be used to bond them, as they cannot be welded together.
- Reduce the number of welds that would have otherwise been required. For example, BMW rivets and approved structural adhesives may be specified in areas that squeeze-type resistance spot welding arms cannot access, or when replacing boron components. Adhesive bonding also helps resolve problems with cracks around spot welds occurring as a result of fatigue loads.
- Better manage the various stresses during vehicle operation or a collision by more evenly distributing them across a region than would be possible with welding or riveting. This enables the flow of forces during an accident to remain truer to BMW’s designed intent.
- Facilitate the down-gauging of metals (e.g. thinner and lighter body panels, less steel reinforcement) for lightweight, optimized vehicle construction.
- Replace other inferior sealant materials. These adhesives not only seal out water better, they also improve noise, vibration, and harshness control by dampening noise distribution and minimizing body vibrations.
- Allow the introduction of lighter weight materials, such as carbon fiber roofs and other non-steel and non-alloy components without compromising strength, safety or durability.
- Enable hybrid sandwich construction to be employed in manufacturing, using different grades of steel and alloys. For instance, carbon fiber and other advanced thermoplastics can be sandwiched between aluminum sheets for the front flexural and supporting structures.
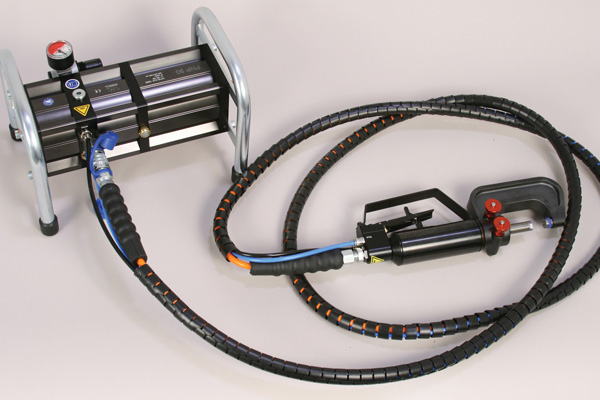
Rivet-bonding is on the Rise
In cases where neither welding nor bonding will restore the integrity of a vehicle, BMWNA may specify a different repair procedure. In rivet-bonding, there are several key considerations that will help conserve limited working time and perform a complete, safe repair:
•Technicians must know the composition of what they are going to cut into beforehand.
•Application instructions and repair procedures must be understood before using an adhesive.
•The use of approved parts, tools, fasteners, and adhesives is essential. In particular, this new method requires the use of a punch riveting tool.
•Avoiding cross contamination by working on the separate metals in different areas and with different tools may be necessary.
•Clean surfaces are required for proper bonding. It is also important that bare metal be bonded to bare metal and not painted surfaces.
•When rivet-bonding , be sure to bevel the drill holes so that panels can be compressed snugly together.
•During the final assembly, ensure that the new panel aligns properly to where it will be attached and check for gaps. The use of a reinforcement plate may be specified.
Don’t let adhesive bonding be the weakest link. Like the shift from mild steel to higher strength steels and alloys, the introduction of new composite and plastic materials requires that repairers learn and use BMWNA-approved repair procedures, supplies, tools, equipment and training. To provide acceptable elasticity and flexibility (in addition to better tensile and shear stress strength than the materials being bonded), professionals must be cognizant that BMW specifies certain adhesives that are matched to the repair. Otherwise, a repair that looks fine cosmetically may in fact stick the car owner with durability- and corrosion-related concerns, as well as compromised occupant safety should another accident occur. Being responsible for a substandard repair before that second collision could be devastating, especially if BMW recommendations were not followed in the previous repair.
BMW provides industry-leading collision training
In April, we attended ToolTech Week 2012, an annual conference hosted by the Equipment and Tool Institute. The event is a gathering of automakers, aftermarket tool and equipment manufacturers, insurers, educators, and repair associations and facilities. One afternoon during the conference was focused on the topic, “Collision Repair in the Aftermarket.†The panel discussed new materials, required joining technologies, and training. After this session, we met with some of the presenters to discuss BMW training.
BMW Information Resources
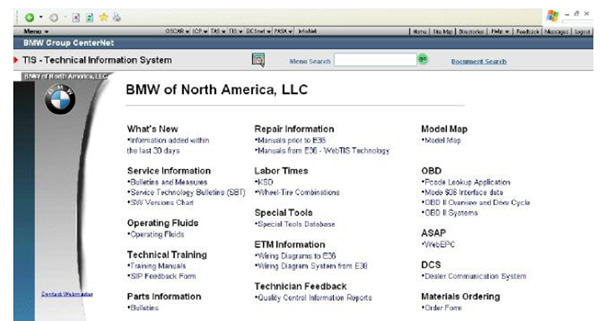
BMW Information Resources
BMWNA has dedicated much effort to creating a secure, single website, www.bmwtechinfo.com, where technicians can access needed collision and mechanical technical service information. Once logged in, reprogramming professionals can access a myriad of technical information including service and reprogramming data, repair instructions, special tools database, wiring diagrams, electronic troubleshooting manuals, technical training material, and more. If you are unable to view or log-in to the website, visit http://www.nastf.org/i4a/pages/index.cfm?pageid=3456 for answers to FAQs and a list of computer system requirements (courtesy BMWNA).
First, we spoke with Tom Brizuela, BMWNA’s Body and Paint Technical team leader at its technical training center in California. In addition to directing curriculum development for BMW’s Body & Paint Service Technician Education Program (STEP), his other duties include training development, insurance company technical presentations, and industry relations. We asked him to share what distinguishes BMWNA training from the rest of the industry.
“New lightweight, thinner, yet stronger materials are increasingly part of new BMW vehicle model builds,†says Brizuela. “Similar to the STEP program for mechanical service, BMWNA has developed a collision-focused STEP training program as well. This training is provided to both dealer-owned collision facility technicians and dealer-sponsored independent collision shop technicians at BMWNA’s four technical training centers in the United States. In addition, it is provided to aspiring and entry-level technicians at several leading educational facilities throughout the country.â€
“To provide a complete, safe repair of customers’ vehicles, collision professionals must be aware of and be able to properly identify and repair new high-strength steels and alloys, plastics, carbon fiber and other innovative materials,†adds Jason Bartanen, technical training director for the Inter-Industry Conference on Auto Collision Repair (I-CAR). “To do this, technicians must have access to genuine collision-related service information; automaker-approved tools and equipment; be capable of employing the correct methods and techniques; and maintain the currency of their repair knowledge and skills through ongoing training and education.â€
“Compared to other automakers, BMW collision training is second to none,†notes Bartanen. “While I-CAR works with all automakers, the BMW collision training model is one that other automakers would do well to emulate.â€
That kind of recognition doesn’t come easy. And it’s yours for the taking.
0 Comments