Except maybe for some impractical exotics, nothing has more powerful, fade-resistant brakes than a BMW. As one “Bremsen†(brakes auf Deutsch) engineer once said to us, “They’ll stop on a dime and give you nine cents change.â€Â We’ve always called them “Autobahn brakes,†referring to the German highways that have no speed limits and require serious vehicular control if your survival is of any importance to you.
A necessary consequence of this sophistication in stopping and BMW’s focus on maximum all-around performance is that the company’s rotors aren’t the heaviest out there. There’s the matter of reducing unsprung weight to improve handling, but another factor is keeping the mass down to aid heat dissipation and cut the potential for fade. Also, to enhance cooling the air passages have been opened up with the result that the wear surfaces are a bit thinner than they are on mundane vehicles. In most cases, BMW only allows 0.064 in. (1.6mm) of wear before the discard thickness is reached, whereas other carmakers might permit 0.100 in. (2.5mm).
Eyeballing
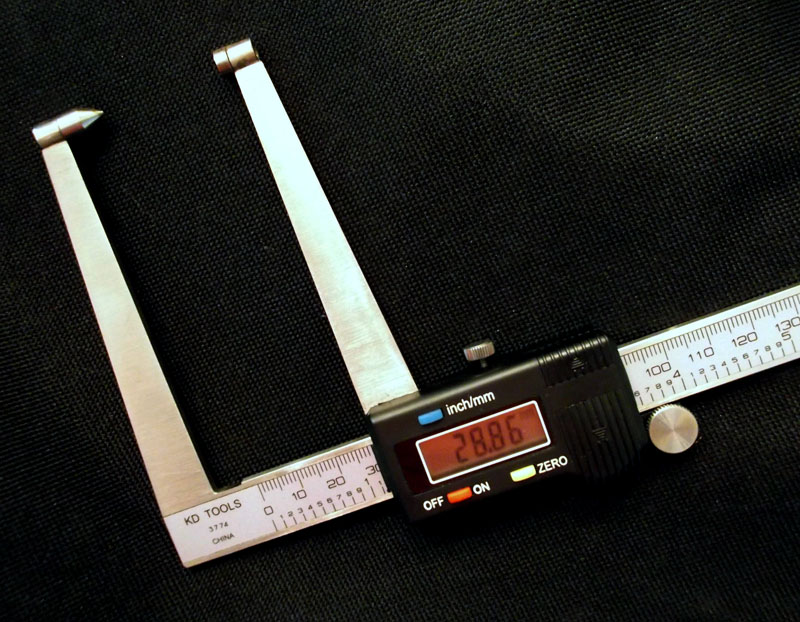
It may not be as accurate or rugged as a mechanical disc micrometer, but since our eyes aren’t what they once were we’ve come to love our digital rotor caliper.
We remember years ago removing a wheel from a BMW with maybe 39K on the odometer and being able to see with the naked eye the excessive rotor wear that was going to make replacement necessary. We’re not talking grooves. We mean a visible wide depression made by pad contact. But it turned out that this was on a car that had high-performance modifications and was presumably driven aggressively, so such a situation shouldn’t form the basis of your decisions where the majority of these cars are concerned.
So, disc service and replacement policies become a delicate balance on a high-performance car such as a BMW. Some frugal techs say you can usually hang pads twice before installing new rotors, but more and more have come to believe that new-on-new is the only way to insure excellence in stopping characteristics and safety.
Almost nobody turns BMW discs anymore. As one successful upscale Euro specialists says, “We threw our brake lathe in the trash.â€Â That’s a big change from traditional American brake service, and something your patrons may give you an argument about since they’ve probably been hearing about brake rotor machining ever since they bought their first car (a ponderous domestic with 40-lb. discs, perhaps?). Well, this is a BMW. If you want the cheapest thing to drive and the least expensive to service, choose some old-fashioned slug of a vehicle. Besides, when you subtract the labor of turning rotors in a workmanlike manner on a well-maintained lathe, then cleaning them thoroughly (the avoidance of which task is a common cause of squeak and squeal), the difference between that alternative and installing new isn’t so great after all. In the case of cross-drilled discs, machining is not allowed, period.
Hearsay
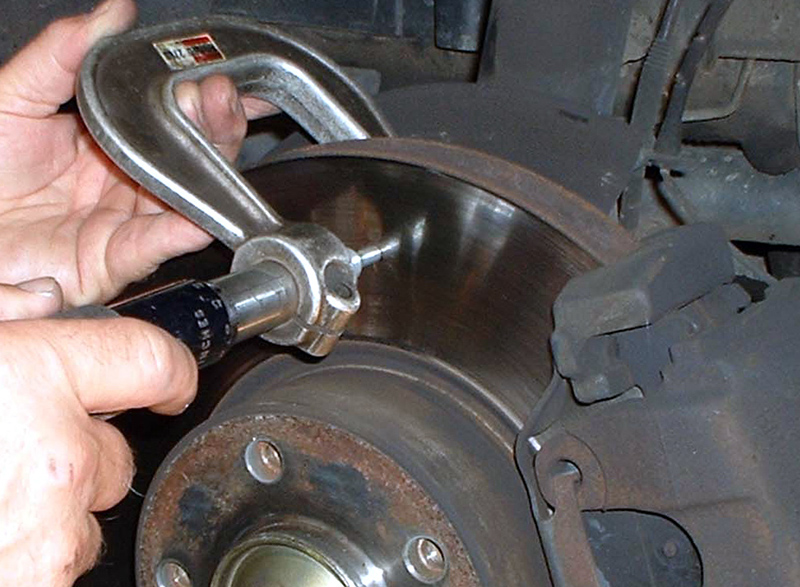
Even if they’re not down to the discard thickness yet, how much iron was lost during the last wear cycle? If that same amount will take a used disc below the throw-away spec, you should have a talk with the customer about “rotor forecasting.
Given the rumors circulating out there in the trenches of independent auto repair, we decided to submit some straightforward questions to the service engineers of BMW North America to be sure we weren’t saying anything outrageous in the pages of The Bimmer Pub, and they graciously responded through the company’s excellent P.R. department in Montvale, NJ. To wit:
Q. There’s a rumor out there that in order to provide the best possible stopping power, BMW uses relatively soft rotors, and that’s why they tend to wear faster than they do on lesser vehicles. Some technicians even claim that the discs and linings are designed to wear out at the same rate. What’s the truth about BMW rotor metallurgy?
Not true. Generally speaking, BMW brake rotors are designed to support more than one set of brake pads during their normal service life. As you can imagine, the life of any brake system component is subject to the customer driving profile. When brake system components are subject to high heat loads with insufficient cooling time, accelerated wear can occur. BMW brake systems are designed to match the overall performance nature of the vehicle, having the ability to provide braking as superior as the acceleration and handling to complete the whole package.
Are there any circumstances in which you would recommend that BMW rotors be machined?
Yes, when irregular wear, brake pulsations or vibrations are present before the brakes are to be serviced and there is enough material thickness remaining to support machining (not below minimal wear tolerance). BMW brake rotors are similar to any other manufacturer’s rotors and can be machined, with the exception of the cross-drilled rotors used on M models and other performance vehicles. When the frictional surface of a cross-drilled rotor is questionable, BMW recommends the replacement of the rotor.
If no pulsation is present, grooving is minimal, and there is enough thickness left so that the next wear cycle will not bring the discs down below the “throw-away†spec, is it ever acceptable to simply “hang pads†(as techs call it)? In other words, put new linings on worn rotors.
Yes, absolutely. Provided there is no obvious “irregular†wear, BMW brake pads will conform to the friction surface of the rotor within the normal ‘bedding-in’ period (300-400 miles).
Reasonable responses, indeed. It would be foolish to disagree with any of them, but there is a little more to the story.
What’s the forecast?
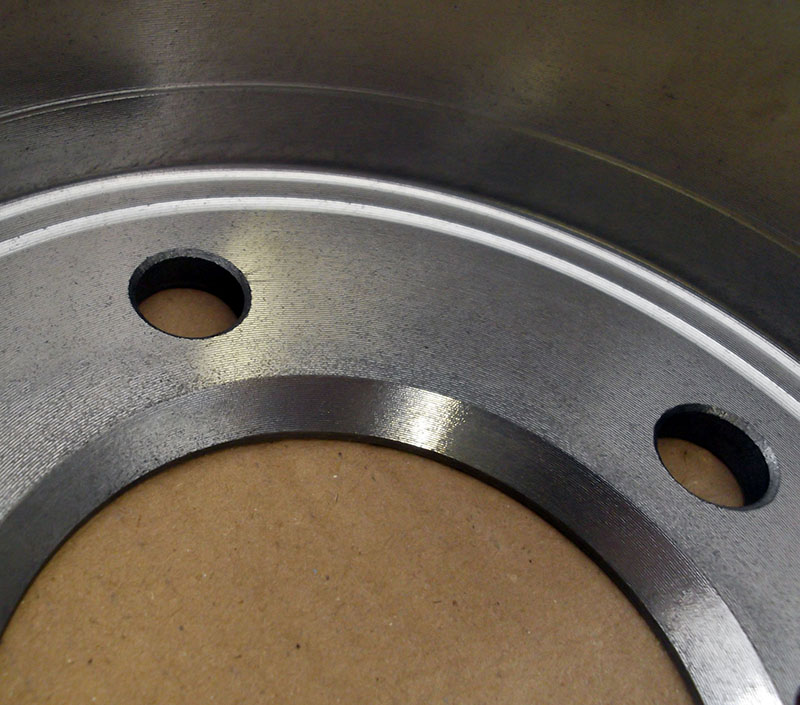
One subtlety most people don’t know about is the angle of the chamfer of the center hub hole. Is it identical to O.E. on that aftermarket replacement?
Take the subject of “rotor forecasting,†for instance. We first heard of this years ago, and it always made sense to us. The idea is to take the original thickness of the disc (look it up, or measure an unworn area), then subtract the current thickness from that number, which will give you the amount of iron reduction the wearing out of one set of linings results in (or, if this is a second reline, two sets, and so on). Typically, this will be 0.032 to 0.040 in., or 0.8 to 1.0mm per cycle. If the rotor has more than that left, and no machining is necessary, you can reuse the discs and just hang those pads. On the other hand, if that subtraction puts you below throw-away, you’re leaving yourself open to both complaints and liability. It’s easy math to explain to your customers, and if you handle it right you should sell a lot more new rotors.
Thoroughbred

Some guys like to compare the weight of aftermarket replacements to that of the originals, figuring the heavier, the better. But BMW wants good heat dissipation and reduced unsprung weight, not a massive, perhaps crude, casting, so your scale won’t really tell you anything about quality.
Whenever you’ve decided that replacement is the proper course of action, you’re faced with another big question: O.E., or aftermarket? While people who work on domestics and run-of-the-mill imports generally opt for the latter to save money, what should you be doing? After all, you’ve chosen to pursue the servicing of thoroughbred vehicles. Is the cheapest route appropriate?
Probably not. In the first place, while that aftermarket rotor may claim to meet factory specs, that might just mean that it shares the same dimensions and will fit physically. While the original might have an aluminum “hat,†or be of the floating variety that both saves weight and optimizes airflow, what you get from your local jobber will often just be a plain, relatively crude iron casting. We’ve seen pictures of discs sawn in half to reveal the configuration of the cooling fins in the air gap, which is an engineered feature. Do the makers of cheap parts follow that exactly, or just do what’s easiest?
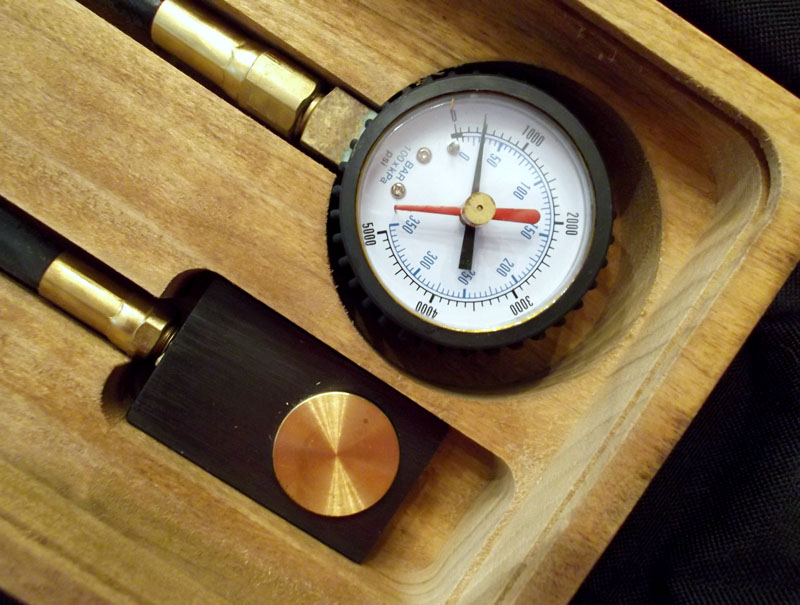
Is that brake pull being caused by a hydraulics issue, or did somebody do something strange like mixing brands of linings? Comparing the squeeze of each side will tell you.
Besides metallurgy and structure, there’s a factor that might cause serious problems with aftermarket rotors that most people aren’t aware of: hub chamfer. If the angle doesn’t match the hub exactly, the disc won’t seat right, leading to big trouble with runout and heat dissipation, yet some cheap items just use, say, 45 deg. as a one-size-fits-all manufacturing convenience.
We’ve never seen a cracked BMW rotor, but according to expensive and extensive research by some European brake parts makers who supply O.E. and genuine replacement parts, Asian discs are much more prone to this failure than theirs are. We don’t find that hard to believe.
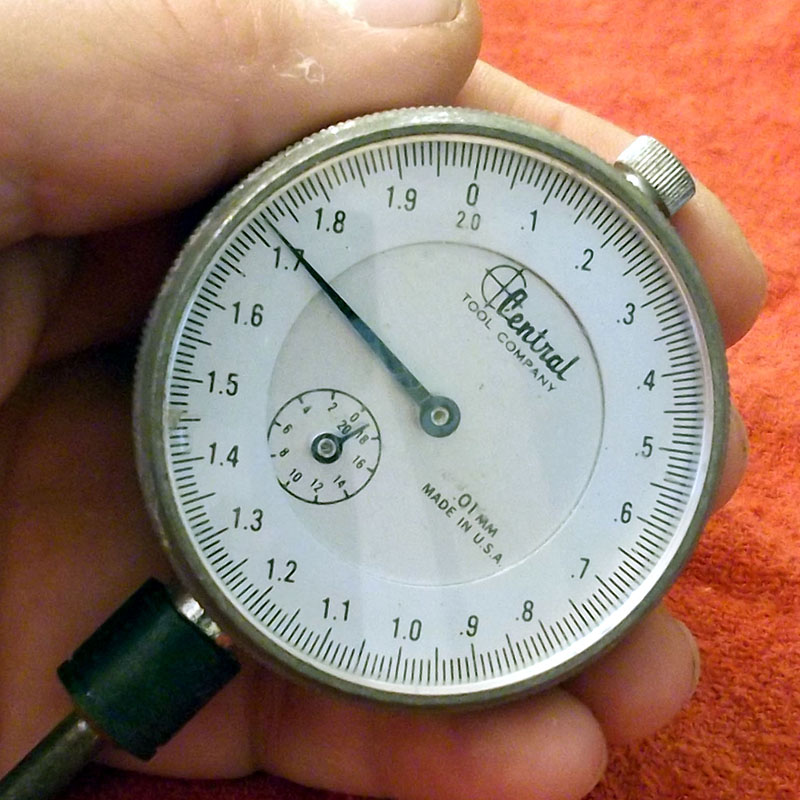
“Wobble†is commonly the underlying cause of DTV (Disc Thickness Variation), which in turn results in pedal pulsation. Use that dial indicator to head off comebacks.
At BMW, it’s corporate policy not to disclose suppliers, so it would be poor form for us to tell you what companies actually manufacture its O.E. and replacement rotors (except, of course, for the high-profile Brembos on models such as the M3 GTS that can go from 100 to zero kph in a mere 32.6 meters). Suffice it to say that they’re long-established European companies with impeccable reputations for research, testing, and manufacturing quality. And there’s no difference between what they supply for BMW assembly lines and what your local dealer sells. Opting for them will pretty much eliminate comebacks, keep your customers happy with your work, and allow you to sleep well.
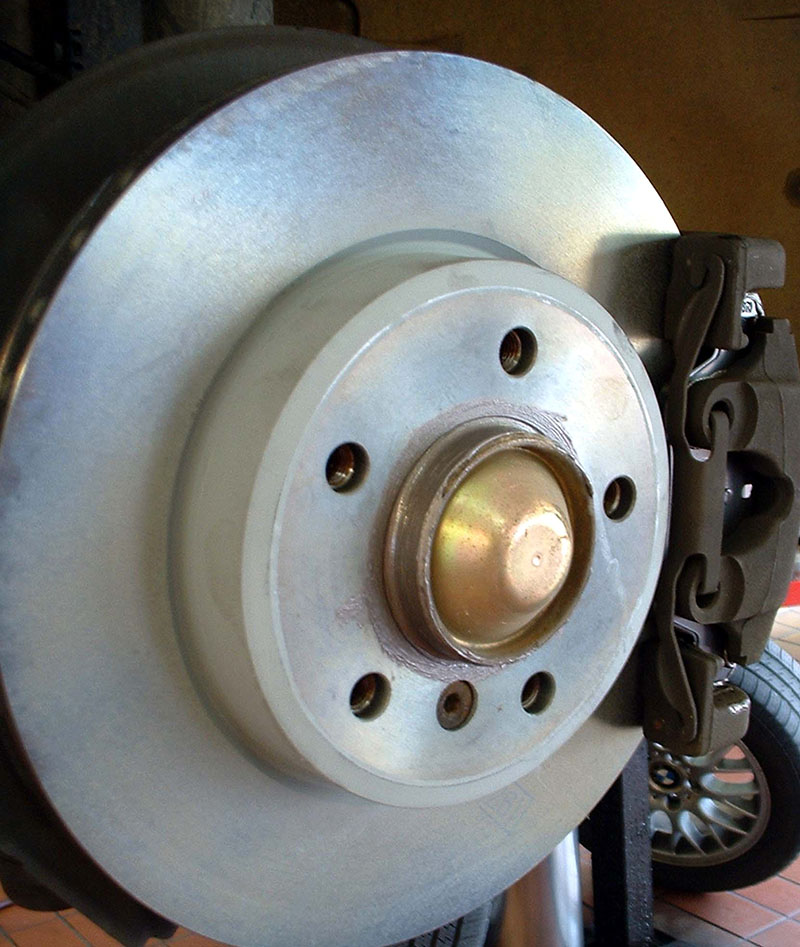
Perhaps you’ve been expending a lot of work cleaning that nice rust-preventative coating off a new rotor before putting it into service. You can stop now. It’s meant to stay on and actually helps the bedding-in process to prevent squeaks and squeals.
We’ll conclude with a few practical points:
- Brake pull can be the result of a restriction in the hydraulics, or a discrepancy in the characteristics of the friction components from one side to the other. Using a set of load-cell pressure testers will tell you if you’ve got equal squeeze left and right. If so, a reline is called for.
- Runout per se doesn’t cause pedal pulsation, but it’s still often at the root of the problem. What happens is that the disc surface strikes the pads just in certain areas as it rotates, which wears them unevenly and produces DTC (Disc Thickness Variation, once known as “lack of parallelismâ€), the true culprit. During a stop, each time the thicker parts of the disc pass between the pads, the hydraulic column gets a kick, which the driver feels. A common maximum spec for DTV is 0.0002 in., yet one lathe manufacturer tells us that 0.002 in. of runout will cause about .0004 in. of DTV in 3,000 to 5,000 miles.
-
You’d be hard pressed to find such a premium coating on an aftermarket replacement, such as this no-name Asian specimen.
So, get rid of runout or installing even the best new discs won’t protect you from a repeat “bumpy braking†complaint.
- Speaking of runout, disc mounting errors are a common cause. That is, any rust or dirt between the hub and the inner hat of the rotor that keeps them apart, even ever so slightly — the effect is magnified out from the center. Fortunately, BMWs use lug bolts instead of studs and nuts so it’s a lot easier to make sure that surface is perfectly clean than it would be if you had to go around all those studs.
- Genuine BMW replacement rotors commonly come with an even, light-gray rust-preventative coating. While you may have read that this should be removed before installation, the premium European disc manufacturers assure us that it should stay on. As one puts it, “This highly effective surface protection enables installation without additional cleaning of the brake disc and full braking effect from the first braking movement is fully guaranteed.â€
0 Comments