It’s been a couple of decades since BMW introduced its first full-time electronically-adjustable suspension system. Dubbed EDC (Electronic Damping Control), it appeared on the 7 Series and did exactly what its name implies — changed the stiffness of the shock/strut units according to how the car was being driven by means of a valve that altered the size of the hydraulic orifices.
Fine, but today BMWs employ additional inputs to determine damping commands, which presents us with another whole level of sophistication and complication. So, when a customer comes to you complaining of a harsh ride, you’d better understand what you’re dealing with.
What’s what
First off, EDC is different from EHC (Electronic Height Control), which only addresses vehicle level as additional weight is carried. The tip-off to the presence of EHC is the large reservoir on the power-steering pump and the hydraulic lines running to the shocks/struts. As we said, EDC handles suspension stiffness, and offers the driver manual choices for either a soft, compliant ride, or a sportier, stiffer suspension feel. Through the years, this system has evolved to provide an increased range of comfort and additional vehicle control under various road conditions.
BMW has offered computer-controlled suspension systems as options on various models. EDC-K followed EDC I, II, and III. The K system is truly active, reading road conditions and reacting accordingly. BMW uses conventional gas-charged shock absorbers even in its computerized systems, but they have the addition of adjustable hydraulic restriction to control compression and rebound dampening. EDC logic commands internal valves that control the flow of hydraulic fluid from one chamber of the shock to another. When the valves are wide open, the fluid passes easily providing a softer, more comfortable ride. When the valves close down, flow is restricted increasing compression and rebound dampening. This makes for a stiffer ride and sporty, more precise control of the vehicle.
As with every other make, the hydraulic fluid level is not serviceable, so if a serious leak occurs unit replacement is required.
When Computers Take Over
The EDC control unit is continuously in charge of shock absorber compression and rebound dampening, and the shocks are infinitely adjustable from full-firm to full-soft. If there is a failure such as the loss of voltage supply, the shocks default to maximum compression and rebound dampening. In other words, the internal valves are in their most-closed position when they do not have electrical power. Again, don’t confuse this with EHC — when that fails, the suspension can drop the chassis to the ground. With EDC, on the other hand, a problem will only change the ride characteristics. Your customer may notice a very stiff ride and severe jolts over large bumps, as well as the EDC warning light coming on, indicating that the self-diagnostic system picked up a fault.
The EDC control unit has only one function: adjusting the dampening characteristics of the individual shock/strut assemblies. It receives signals from three sensors that indicate body direction and speed, which are called acceleration sensors. They are placed in only three corners of the vehicle because the direction and speed of the fourth corner can be determined by the readings of the other three. Locations can vary according to year, make, and model. For example, on a 2007 M5 the two front sensors are mounted in the rear of the front wheel houses and on the passenger’s side of the trunk, or the right-rear corner. They are all three-wire sensors with a 5V reference, ground, and signal wire. The signal voltage should be very close to 2.5V for each sensor while the car is parked on a flat surface. The signal voltage on each sensor will rise from 2.5V in one direction of travel, and drop below 2.5V in the other direction. It is important that these sensors are installed properly, especially after accident damage.
So Who Pulls Whose Chain?
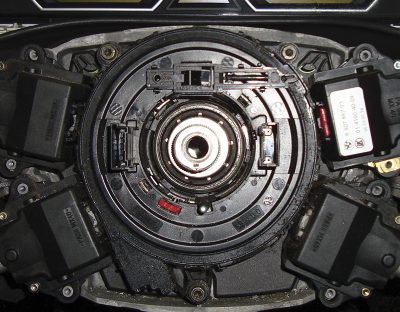
The driver is in control of the overall setting of the suspension. EDC-K has two settings, Comfort and Sport. This driver input goes directly to the Controller (Con) through the K-CAN and can be seen in the on-screen display. From here, messages are passed on to the Gateway (ZGM), and then on to the EDC control unit on the Powertrain (PT) CAN. This is not the only input coming in from the Gateway. The Steering Angle Sensor (LWS) sends a “Byteflight†fiber-optic signal (used to increase the speed of the steering angle input) to the Gateway control unit as well. This information tells the EDC control unit how much steering input is occurring so it can make the necessary adjustments to the suspension valves using pre-determined maps. Other inputs come in directly on the PT-CAN. The Dynamic Stability Control (DSC) unit has some say in how the EDC should react. Here, the relative speeds of the two front wheels are used to calculate the optimal suspension adjustment.
The EDC control unit provides power and ground for the valves in the shock/strut assembly. It is a relatively low voltage supply because high currents are called for (more on this later). Remember, the shocks are normally in the firmest setting without power. Small amounts of current to the valves keep the suspension firm. The more current that is applied, the softer the suspension is going to be. That is limited to two amps to prevent damage to the solenoid and/or the driver in the EDC.
Several different failures can occur, but there are only two fail-safe modes. With minor faults, the system enters a “partial fail-safe,†which keeps a static current to the solenoids for medium ride quality. Total failure defaults to the firmest settings as mentioned earlier. The solenoids are current-controlled, but BMW uses a pulse-width modulated (PWM) signal to average the amount of current the solenoids receive.
A Current Divided
The control unit can adjust each individual corner of the vehicle, but it has a unique way of controlling each pair of shocks on one axle. The EDC provides a 12V power supply to one of the front solenoids. In the case of the 2007 M5, this goes to the left solenoid, and the ground control of the left solenoid becomes the power supply to the right solenoid. This way, current is evenly split between the two solenoids on one axle. As mentioned earlier, the EDC controls the ground voltages at about 2.5V and maintains the overall current flow with PWM. You can use an oscilloscope to monitor these signals, but you will have to drive the vehicle. Current control of the solenoids stops below three mph.
Using your iComm/ISTA tool, you can diagnose problems with the system. The EDC control unit only sets faults for axles, so you have to individually test each shock. You are going to need a special tool available from your local BMW dealer’s parts department, Part #90 88 6 372 050, to use Testplan to isolate which shock is at fault. If one is replaced, the “running time memory†in the EDC control unit must be reset. To put it another way, the EDC keeps tabs on the wear characteristics of each shock, so this learned pattern needs to be erased.
With a little knowledge of the system, a paid subscription to www.bmwtechinfo.com, and a good relationship with your BMW dealer’s parts department, you should be able to provide your customers with the type of service they have come to expect. An accurate diagnosis, timely repair, and the use of genuine BMW parts ensures that your customers will keep coming back. Now that’s a good business plan.
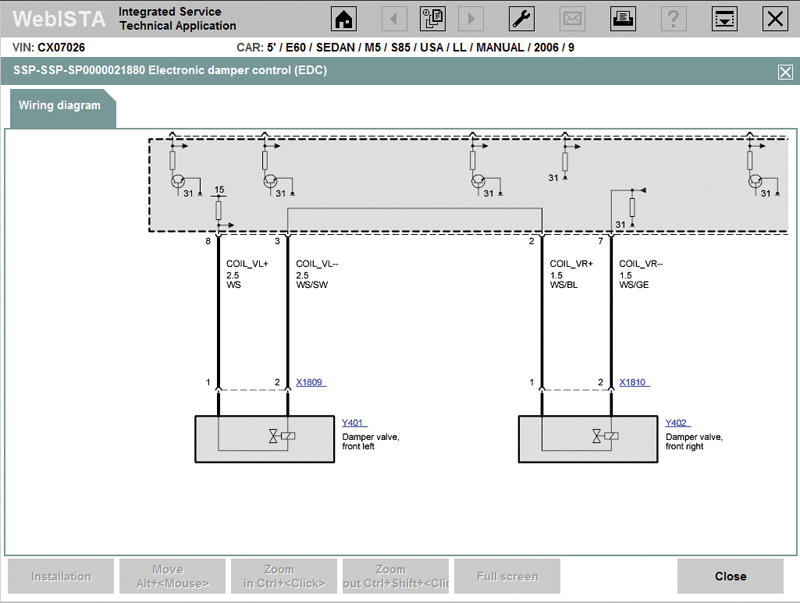
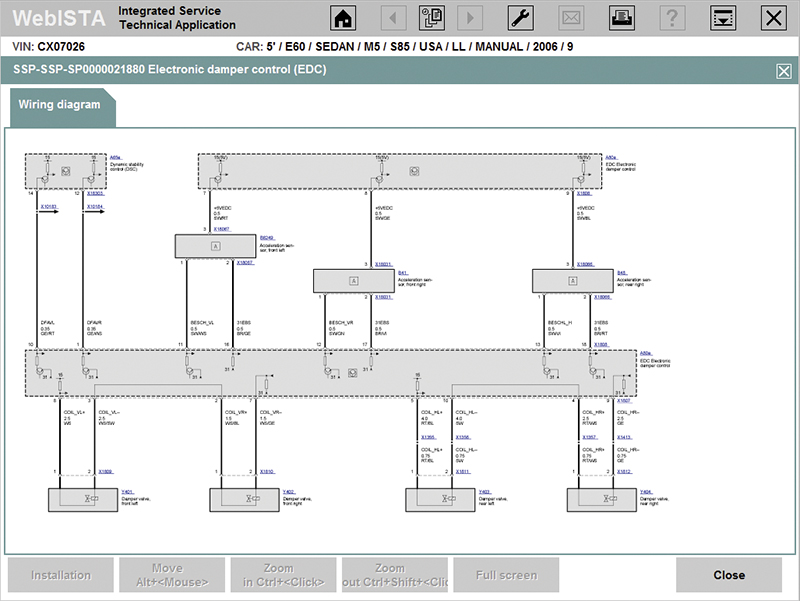
0 Comments