Transitioning to waterborne paint systems will enhance a collision shop’s quality, performance and profitability.
In mid-2009, Volkswagen of America Inc. (VWoA) introduced its VW Certified Collision Repair Facility (CCRF) program for U.S. dealer-affiliated and qualifying independent body shops. The CCRF program assures VW vehicle owners that collision repair facilities performing repairs do so in accordance with Volkswagen recommendations.
Among other tenets, facilities and collision professionals must meet certain VWoA training requirements provided by Inter-industry Conference on Auto Collision Repair (I-CAR). In addition, with respect to painting, VWoA also recommends that body shops and personnel use waterborne paint and associated equipment, tools, systems, and procedures.
“We don’t require waterborne coatings at this time, but it’s recommended,†explains Alain Bleau, GM Wholesale Parts Management. “Collision facilities must be sure to use paints which comply with state and federal VOC regulations. In many states this means that they are obligated to use waterborne base coat.â€
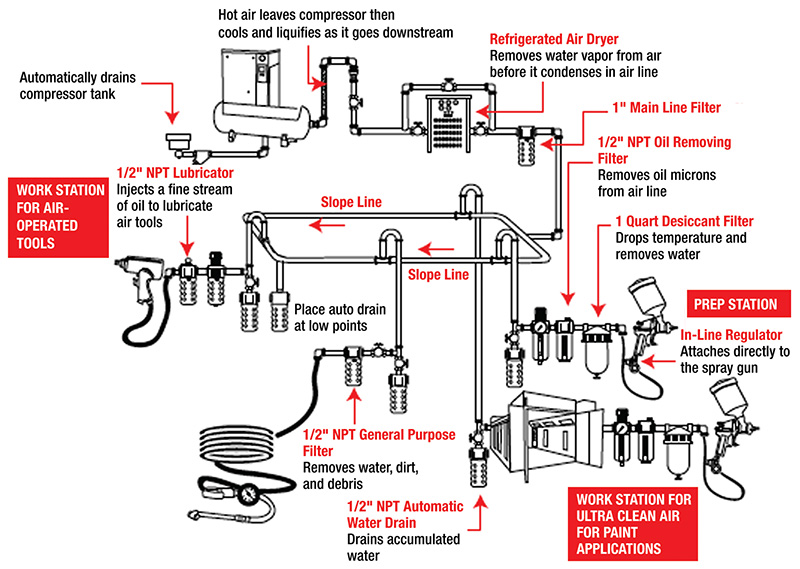
It’s the law in many places; waterborne is also safer, faster, and cheaper
Regulatory pressures, economics, a shift by automakers into using waterborne paint systems and a desire to be both eco-conscious and safer are driving the transition to waterborne paint. Experience has shown that the transition from solvent-borne to waterborne can be seamless, efficient and profitable — provided the right choices are made regarding technology, equipment, support, training and preparation.
Waterborne paints meet the requirements of the U.S. Environmental Protection Agency’s (EPA) National Emissions Standard for Hazardous Air Pollutants rule (EPA Rule 40 CFR Part 6H). The rule was published in January 2009; collision facilities were required to be in compliance by March 11, 2011. Facilities should also check with their state and regional authorities in regards to other requirements.
“Environmental issues are very important to our customers in the Colorado Rocky mountain region, as they are worldwide,†says Jim Frost, manager of the Prestige Imports Collision Repair Center, a VW/Audi CCRF located in Lakewood, Colo. “Switching to a waterborne paint system and procedures has allowed us to deliver eco-friendly collision repair solutions without compromising high quality service to our customers. Our paint technicians agree that waterborne basecoats color match, metallic control, and ability to blend not only meet, but exceed solvent-borne basecoats.â€
Plan for a successful transition
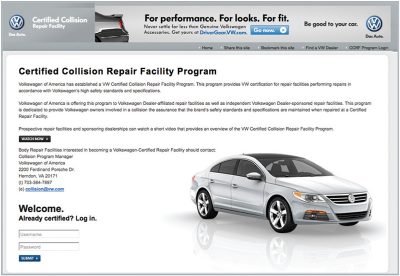
Waterborne paints are latex and provide collision facilities with a safer and more efficient alternative to traditional solvent-based paints. Made of synthetic resins and pigments that are kept dispersed in water by surfactants, waterborne paints contain less coalescing solvents than solvent-borne paints.
This is because the coating material in waterborne paint is suspended in the water instead of being dissolved in solvents.
Consequently, waterborne paint has significantly lower volatile organic compounds (VOCs) emissions than solvent-borne paint. VOCs are harmful to people because they contain chronically hazardous pollutants; for example, they build smog. Although less harmful to the environment, collision facilities should note that waterborne coatings do require different handling; for instance, shop cleanliness.
In brief, the EPA rule incorporates the need for hygiene, lowers the VOC limits allowed in coatings, and mandates the use of waterborne refinish coatings. The rule requires collision facilities to implement equipment and management practices in compliance with the new standards, which help reduce toxic material consumption and produce savings for the facility.
Essentially, compliance is required in the following areas:
- Training – Paint technicians will find waterborne basecoat easy to spray, but spray techniques differ slightly from applying solvent-borne. All painters must train and certify on spray gun equipment selection, spray techniques, maintenance and environmental compliance. Note that major paint suppliers, such as PPG and BASF, provide training in using waterborne paints, associated equipment, tools, and more.
- Spray Booths – Open-air spraying is no longer allowed in any collision repair shop. Coatings containing a targeted hazardous air pollutant (HAP) must be sprayed in booths outfitted with an exhaust filter that has a VOC capture efficiency of 98%, or greater. Work with your spray booth manufacturer or filter supplier to select the right filter for your shop’s needs.
- Spray Gun Requirements – Spray guns used to apply coatings must employ high-volume, low-pressure (HVLP), or an equivalent EPA-approved technology. In addition, spray gun cleaning operations must prevent atomized mist, or avoid spraying cleaning solvent and paint residue outside of a container used to collect waste solvent.
- Record keeping – Collision facilities must provide notice of compliance to the EPA; newly-built facilities are required to comply before opening for business. In addition, all facilities must notify the agency each calendar year of any reportable changes that occurred and keep copies on file of all EPA-required documents (e.g. employee training certifications, equipment documentation and corrective compliance actions taken).
Partner with quality suppliers
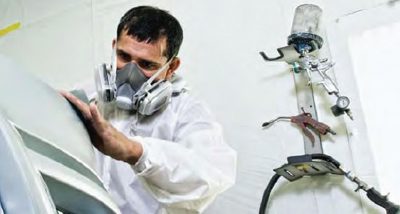
Choosing quality paint and equipment suppliers that provide training, technical support, and other services required to make a smooth transition to waterborne is essential. Besides providing reliable and durable products, they should also have a clear and practical understanding of how to get the very best out of your new waterborne basecoat system. PPG and BASF are just two of the reputable suppliers with established training and support. You might also want to check with your industry networks for positive experiences.
PPG and BASF are both VWoA-approved waterborne system vendors. Not only is each a reputable supplier of waterborne coatings and systems, they both provide on- and off-site training as well as other support during conversions. Approved equipment vendors include Global Finishing Solutions LLC for spray booths, Kaeser Compressors Inc. for a clean air supply, SATA GmbH for spray guns, Becca Inc. for cleaning systems, and others.
Support can help you design and equip your waterborne system based on your facility, car flow, health and safety issues, and other factors. Training can cover an overview of your waterborne system, application techniques, color adjustments, spot repair, blending, waste management, maintenance, and more.
Note that these approved suppliers offer a variety of classroom and hands-on training before, during, and after converting to waterborne – some online, some onsite, some offsite, and some a combination of these. For example, in addition to onsite training prior to and during conversion, PPG offers MVP Green Belt Training to waterborne system customers. This program helps collision facilities and staff to continuously improve after conversion via follow-up classroom training that also incorporates visits to other body shops to see the new learning being put into real-life practice.
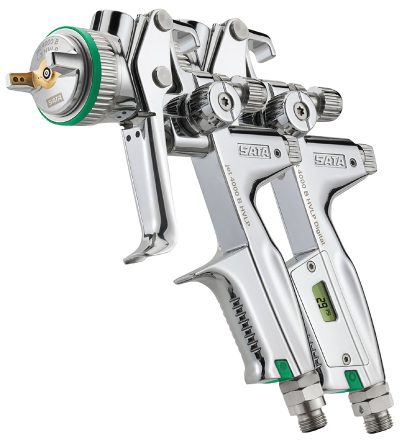
Consider your staff’s learning styles, then check to see what prospective suppliers offer to meet your training needs. For example, besides training at your supplier’s facility, negotiate having your supplier’s conversion and training team provide on-site training at your facility during the actual waterborne conversion period (typically one to three days). Working with your technicians on your site with your equipment – while covering application training, computer training, waste stream training, and color tool training – could go a long way to making the smoothest transition possible. You might also want to check within your industry networks and draw from their positive experiences.
“We were told by our supplier that waterborne is unforgiving in regards to cleanliness, so it was imperative that we start with a clean slate,†says Tom Gillespie, manager of Bodyworks by Concours, a VWoA CCRF located in Milwaukee, Wis. “When our paint department underwent a complete renovation, the spray booths were retrofitted with corner air movers; the floors were blasted and epoxy coated afterward; and the whole department was commercially cleaned from girders to floor.â€
Equip for success
Converting from solvent to water won’t take much time at all – typically a month or less – especially when a bodyshop partners with quality suppliers and their dedicated teams of conversion and training specialists. Importantly, you won’t sacrifice your shop’s performance or quality.
When converting to waterborne, keep in mind the following four benchmarks that will enable a successful transition:
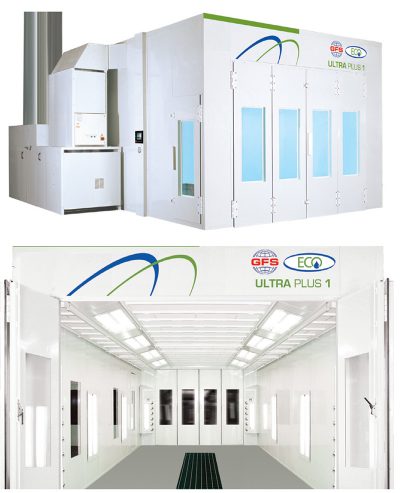
- Use spray guns designed for waterborne paint. Waterborne paints can rust plain steel and attack aluminum, so choose a gun that is constructed of a corrosion-resistant material such as #316 stainless steel with 1.2mm to 1.4mm fluid tips. To extend spray gun life, dedicate this spraying equipment for waterborne products only.
- Cleaning your dedicated waterborne spray guns to maintain top performance and durability. Check with your gun’s manufacturer for instructions on how to clean and maintain your specific equipment. Exercise caution here, as cleaners may not be suitable for both waterborne and solvent-borne spray guns.
- Be aware that the evaporation characteristics of waterborne coatings differ from those of solvent-borne. Notably, waterborne systems are very fast and can often outperform solvent-based coatings. But waterborne paint requires good airflow to quickly evaporate water from the coating. For efficient drying, increasing the cubic feet per minute (CFM) of air passing over the surface is key. Temperature and humidity also play a role in drying times. Generally, 200 CFM or more will lead to great results.
- Drying equipment can range from simple additions to existing equipment to installing specialized equipment specifically designed for use with waterborne automotive paint systems. Specialized waterborne downdraft spray booths use accelerated air make-up systems (e.g. fans that double their speed in flash mode) to decrease dry times and improve productivity at the flip of a switch. Systems can also be retrofitted with temperature/humidity controls, mounted blowers, and floor stands to increase airflow and quickly evaporate water after spraying waterborne.
Benefits worth switching for
While waterborne paints do not eliminate the need for safety equipment, their use lowers the exposure risk to those in collision operations who handle paint. Standard safety equipment is still required, but the harsh odors associated with using solvent-based paint throughout a facility can be eliminated. Waterborne paints can also reduce the amount of hazardous waste generated by a body shop.
The ease of use and ability of waterborne paints to match a vehicle’s finish, (whether or not the original paint was solvent-borne) is a critical advantage. Current waterborne paint technology and systems from leading suppliers allow refinish technicians to simply shake, pour, spray, and expect the same performance, accuracy, and durability of solvent-based systems. Facilities no longer need a mechanical mixing machine, because the toner pigments in acrylic waterborne latex resins are engineered with anti-settle technology.
Waterborne paints also dry and cure faster than solvent-borne paints, allowing vehicles to be ready for customers several days sooner. As with any type of paint, temperature, humidity, and airflow all play a role in curing speed. Fortunately, modern spray booths and accessory equipment can optimize these influences.
“Waterborne is a major technological advancement with no downside,†notes Rick Sloan, field operations manager of White Allen Volkswagen, located in Dayton, Ohio. “Our team has the I-CAR Gold Class designation and is certified to work on Volkswagen, Audi, and other brands. Our switch to waterborne basecoats has been a win-win situation — better for the environment, for the employees, and great color matches for our customers’ vehicles.â€
Now, more than ever before, the decisions you make today will have a long-lasting impact on the quality, productivity and profitability of your body service business. Like any new material or procedure, there’s a learning curve to go through. But with the right information, support, equipment, and training, collision repair facilities and their technicians can make a successful transition into waterborne finishes.
Download PDF
0 Comments