Sound planning is the key to efficient, complete and safe collision repair
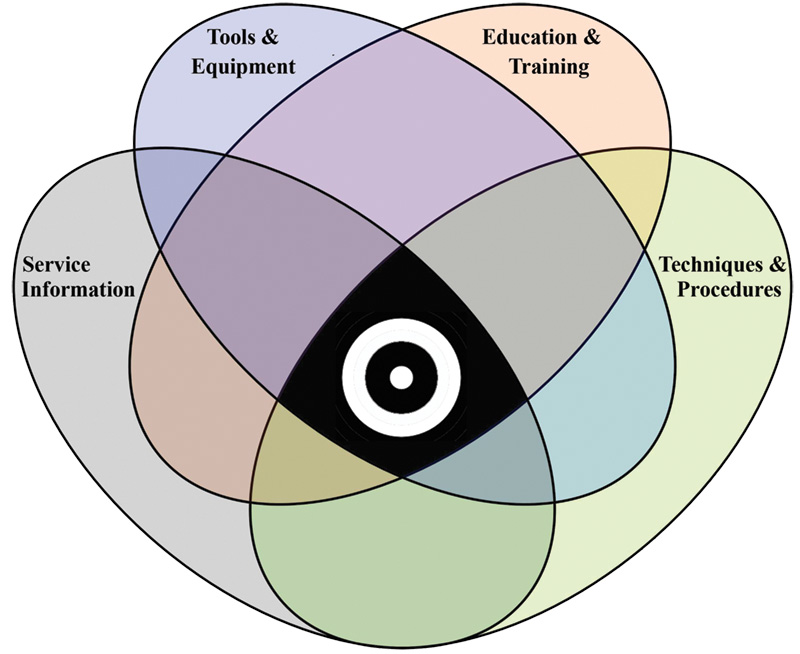
Blueprinting is the process of bringing all the necessary resources together to build a complete collision repair plan that minimizes wasted time and resources that would otherwise result (ManicMedia LLC).
If you added up all the efficiencies the application of lean, up-to-date procedures and associated efficient products in a body shop operation promise, vehicles would be fixed seemingly before you even put in any effort. Unlike that fantasy, the reality is that there is no perfect process or repair facility.
In these fast-changing times in the collision repair world, the technological curve is shifting ever forward and upward, led by automakers such as Mercedes-Benz (MBUSA). To survive and flourish, breaking from long-held collision repair paradigms and practices is no longer optional. Developing a good repair plan before ever starting the repair — a practice know as blueprinting — is essential to performing a safe, complete, and efficient repair.
Design a complete and thorough repair plan methodology
In the past, estimates drove the collision repair process. That is no longer the case today; Increasing complexity is the new norm. Body shops must be aware of inbound change and develop the capability of handling innovative materials used in the mix to manufacture vehicles, as well as the associated repair procedures and emerging interactive electronic systems — such as integrated safety systems, electronic steering and suspensions, and body controls sensors — that are often located in impact crush zones. In addition to cognizance, access to the resources necessary for modern collision repair is required before ever touching a vehicle.
Ongoing change is reflected in ever-evolving service/repair information, developments in repair procedures, and requirements for new, often specialized tools and equipment — sometimes more than once for vehicles in any model year. Think of blueprinting collision repair as a systematic approach to continually identifying and removing the waste from the system, be it time, money, or other resources.
Whereas estimating focused on determining damage, blueprinting is more encompassing; it is about building a thorough and complete repair plan from the get-go, before technicians begin their work. Similar to building a house, a quality and mistake-free collision repair blueprint is essential. Preparing that blueprint requires the completion of a number of key steps before repair actually begins.
These include:
- Understanding collision repair theory for older and newer M-B models — Whoever inspects the vehicle and prepares the collision repair blueprint must have an expert understanding of past, current, and incoming M-B vehicles. This professional must also be cognizant of the material mix and technologies within the vehicle, and be able to access service/repair information and other resources to perform a complete repair. Today, more than ever, experience matters. Have a skilled repair-planning technician enter relevant info directly into a repair plan, then make sure that someone verifies that this plan meets the requirements of your insurer.
- Performing a visual inspection for apparent and suspected hidden damage — New vehicles behave differently from their predecessors in a collision. A visual inspection might only show some tell-tale signs of damage. Using a knowledgeable, seasoned technician here can be critical to identifying suspect areas of hidden damage. Many of the new materials used in late-model M-B vehicle construction don’t behave as materials of the past did. Even in a close visual inspection, damage can be missed. Traditional gap analysis (e.g. door to fender, door to hood, door to quarter) might only show some minor signs, but not reveal the full extent of the damage. For example, rear-end damage may result from a front-end collision that transferred much of the impact forces around the central cabin structure to the rear rails. In other cases, shifts of the advanced construction materials may not even be discernable to the eye.
- Measuring to identify and document damage, including hidden damage — You simply don’t see damage the way you used to. Nor does damage from an impact in one area show up where it used to. Methodically disassemble the vehicle and measure along the way to arrive at a complete understanding of the damage before writing the estimate. Measure the vehicle front-to-back, side-to-side, top-to-bottom, even when damage appears limited to one side or end. Use M-B-approved equipment and tools that provide a range of electronic measuring options. Stay current with cost-effective innovations that can both help identify hidden damage and verify repairs. But like any new tool or piece of equipment, it isn’t enough to purchase it. Ensure your supplier provides training in the tool’s or equipment’s use. Proper measurement not only makes the identification of damage possible, it also facilitates documentation and eases approval for recommended repairs from your customers, whether insurers or car owners.
- Referring to M-B service/repair information for vehicle data, as well as recommended repair and replace guidelines and procedures — The failure to consider MBUSA service/repair information before preparing a collision repair plan can doom the repair to failure downstream, or costly reworks. More on this later.
- Conducting a damage analysis to identify and describe all damage — Once the vehicle has been measured, prepare a thoroughly-documented damage analysis. This is more than a structural assessment. Insurance covers both structural and mechanical damage sustained in an accident that needs repairs. Blueprint for both structural and mechanical repairs. For instance, involve your paint specialist at this stage to be fully aware of whether certain fillers, paints, blending, or other procedures will be necessary. Other examples include a part that isn’t there in time, a missing one-time fastener like a fender bolt or clip, or finding something on the tail-end of a repair that was not identified in the measuring process. Clearly, the lack of a complete damage analysis can interrupt your shop flow, increase vehicle “touch†time downstream and create unnecessary waste.
- Writing a repair plan that identifies all steps in the repair process — Eliminating potential bottlenecks once repairs begin should be paramount in writing up the repair plan for a vehicle. Know and document how the vehicle needs to be set up to properly pull where necessary. Have a full description for all the parts needed (e.g. specialized one-time clips or rivets required) to help eliminate omissions when ordering parts. If specialized welds or other procedures are required, document those as well. In essence, avoid ambiguity because it leads to omissions.
- Getting customer approval (be it the insurer or owner) — Ignorance or lack of foresight are not excuses an insurer or car owner will accept. Think of waste as anything that a customer is not prepared to pay for, be it an insurer or a car owner. Examples include time, materials, and more. Think of these as items that add cost, but not value to a repair. When seeking approval to proceed, “no surprises†should be your goal. For instance, documentation should note suspect areas and account for the possibility of supplements. Identifying the full extent of damage before getting insurer approval, rather than piece-mealing post-estimate discoveries later, solidifies relationships with both insurers and car owners.
- Ordering structural and mechanical parts and supplies — Once the repair plan is approved, order the necessary parts and supplies. Ensure all the parts are present before you begin work on the vehicle, or know with certainty that if you start sooner with structural parts, required rebuild parts (such as taillights, radar sensors, and cameras) will arrive before being needed. In addition, use carts and keep the necessary replacement parts organized in a consistent manner so that repair technicians can focus on repairs rather than on searching for elusive pieces.
- Scheduling the vehicle for repair — It’s all about creating a good repair flow. Good repair planning ensures that technicians do not have any gaps in their time working on a vehicle — no stoppages, delays, or reworks occur once a vehicle repair is started. Some shops only have one frame rack. If a shop has more than one, be sure to designate the right machine for the vehicle. In addition, a sound repair plan will ensure no delays occur once a vehicle is mounted on a rack. Likewise, blueprinting properly will ensure time and resources in a paint booth aren’t wasted.
- Verify continued safety — Mercedes-Benz spends a great deal of time and money crash testing recommended repairs. So, your blueprint should include verifying that your work fits all the criteria needed for the safety of the vehicle in possible future collisions.
To help the industry understand and implement blueprinting, I-CAR (the Inter-Industry Conference on Auto Collision Repair) has developed a brand-new Blueprinting Process and Damage Discovery course, which was debuted in October, 2012. “The course provides dealer and independent collisions professionals with an understanding of the definition of the blueprinting process and how it can help improve repair quality through a standardized approach to collision repair planning,†said Jason Bartanen, technical training director for I-CAR.
Classroom time is limited, so that more interactive training is provided on a shop’s floor — including a number of demonstrations, quick checks and blueprinting implementation tips — which leads participants beyond the disassembly of damaged parts to help them uncover hidden damage that can impact the repair process. “What makes this new blueprinting course relevant and authentic is I-CAR’s ability to deliver the training at any collision facility,†Bartenan continued.
“For example, we could deliver the course at a Mercedes-Benz dealer-owned collision repair or sponsored facility. Using StarTekInfo.com service information, as well as MBUSA-approved equipment, tools, supplies and other resources, the course will help train participants in blueprinting by providing the knowledge and a number of live demonstrations on actual Mercedes-Benz vehicles provided by the host facility.â€
Employ the power of MBUSA service information
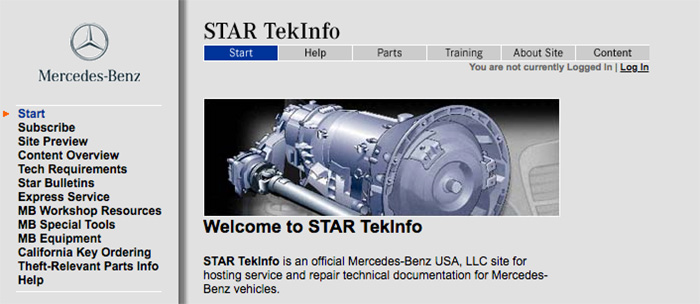
Models can change year-to-year, and even mid-year. Make access to genuine and current MBUSA service information a mandatory early step
(www.startekinfo.com). It will help identify the types and location of various metals, whether there are reinforcing, but different, metals behind structures, and whether specialized adhesives or other new materials (e.g. carbon fiber) are present. In addition, specific repair procedures, lists of required parts, required welding procedures, and other information will help ensure a complete repair plan is used (courtesy MBUSA).
If you’re not looking up OEM information and repair procedures for every vehicle when preparing a collision repair plan, you’re probably already making mistakes. Given the ever-increasing complexity of modern vehicles, service/repair information changes often. This cannot be stressed enough. That’s why you need repair information online, rather than a quarterly CD or software updates you have to seek out.
Whether your facility provides both collision and associated mechanical repairs, or it sublets mechanical repairs to a dealership or an independent shop, genuine and current MBUSA service/repair information is not only essential, it must be reviewed up front for all repairs associated with a collision and incorporated into the plan.
Everyone in your shop — from the shop manager to the estimator to the technician — should have easy access to and be able to utilize the MBUSA service information website, notably WIS (Workshop Information System) where the real meat is available. From the beginning to the end of the repair process, including finished product quality assurance checks, each person involved in a vehicle’s restoration to pre-collision status should be proficient in using WIS.
Some may question the need for everyone to employ service information, but consider just how much more efficient your team could be when, before they begin their tasks, they review a vehicle’s structural composition and components, pertinent technical service bulletins and recalls, technical safety information, required tools and equipment, and other important repair information.
This strategy might cost a little implementation time, but as your team gains confidence using the service information system, the gains realized will be well worth the investment. Once proficient, a facility’s staff should be able to:
- Minimize costly vehicle defects and returns.
- Prepare more accurate estimates with fewer supplements.
- Document and verify proof of repair for insurers and car owners.
- Increase employee safety.
- Decrease production time with the foreknowledge of required parts, materials, techniques, equipment and tools.
- Improve management of liability issues.
- Realize better customer satisfaction index scores (CSI) scores by providing on-time and complete repairs.
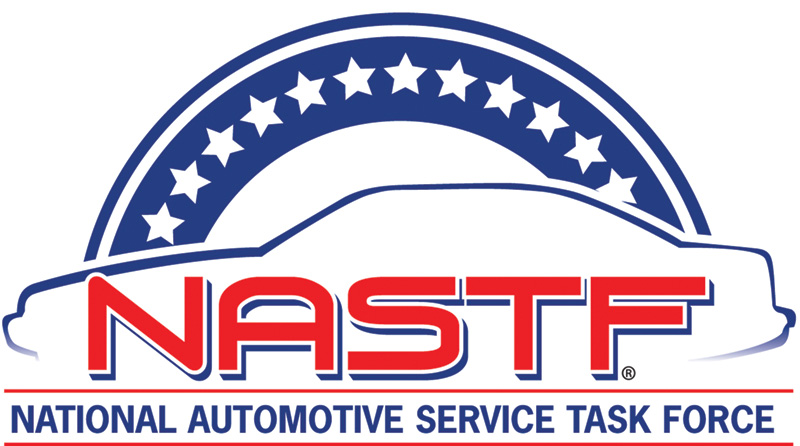
Many collision facilities are not aware that when authentic service information gaps are identified, it is imperative to contact MBUSA. Not only can your team obtain the necessary information, the gap can be corrected for future use by everyone. Another avenue that independent and dealer-owned collision shops can use to resolve information gaps is to file a “Service Information Request†with the NASTF. To do so, copy www.nastf.org/i4a/pages/index.cfm?pageid=3290 into your Web browser (courtesy NASTF).
Granted, not every service information system is perfect. There are bound to be bona fide information gaps — times when a team member will be unable to locate the necessary data to complete work. However, when everyone on the repair team is using this critical tool proficiently, what appears to be a gap sometimes can be merely a few more clicks away, demonstrated by a co-worker or manager who has previously encountered a similar situation.
When authentic gaps are identified in M-B service information, it’s imperative to contact MBUSA. Not only can your team obtain the necessary information, the gap will be corrected for future use by everyone. Another avenue that independent and dealer-owned collision shops can use to resolve information gaps is to file a “Service Information Request†with the National Automotive Service Task Force (NASTF) at www.nastf.org.
Implementing blueprinting requires a determined, open-minded resolve
Having a plan is one thing; implementing it is another. Optimizing a vehicle’s flow through a body shop’s repair process requires planning to minimize, if not eliminate, bottlenecks. On a larger scale, consider whether your shop layout creates bottlenecks. Are their changes you can make that would facilitate a smooth flow of vehicles through the repair process? If so, make the ones you can afford to now, and work toward making others that improve shop flow over time.
Then look at specific areas of the work environment with an open eye to removing waste from shop processes and procedures. Are there ways to streamline and reduce waste? While not every inefficient or unpleasant task can be removed during a repair, unnecessary wastes of time and resources not only cut into the shop’s profitability, but create a more stressful and frustrating work environment for everyone.
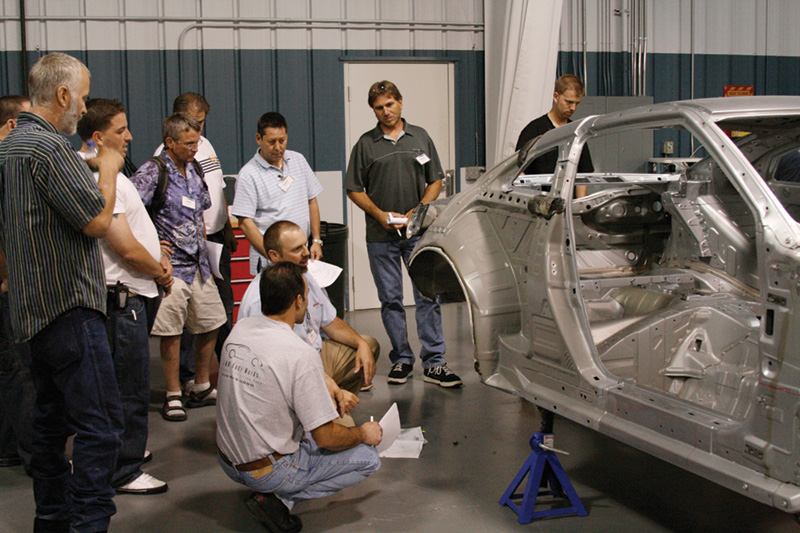
Copy www.youtube.com/watch?v=NtMdhlHEx28&feature=g-all-u into your computer’s Web browser to see what shop owners, technicians, and other staff have to say about blueprinting. For more information, visit the I-CAR website: www.i-car.com (courtesy I-CAR).
This evaluation should be a work-in-progress within the business, and it should include the entire staff. Unless everyone has a stake and a say in procedure and process changes, you have little chance of creating a sustainable environment of best practices. Here are seven areas that you and your employees should examine:
- Transportation — The moving of vehicles, tools, parts, and equipment within your work environment.
- Inventory — Parts and repair materials impact each person’s time available to work each day. How can you improve the flow of parts, as well as an inventory of employee time, expected versus actual?
- Motion — Similar to transportation, but it’s a closer examination of each person’s need to move and the necessity of these movements.
- Waiting — Downtime and non-productive time periods for any reason affect cycle time. Consider how you can optimize getting work approvals, tool and equipment sharing, and parts deliveries, handling incorrect or incomplete orders, etc.
- Over-processing — Avoid completing work ahead of schedule if it causes other projects on deadline to be sidelined.
- Over-production — Avoid completing work that is unauthorized, unsold, or unnecessary.
- Defects —Avoiding mistakes, miscommunications, substandard or incorrect work, and comebacks all fall into this category. Think about how this kind of waste can be reduced.
- Safety — A safe work environment is critical, but also consider losses caused by injuries that happen outside of the work day and injuries that occur over time as a result of the work (i.e., hearing loss, repetitive motion, exposure). For example, do technicians work at a comfortable level, or on the floor?
One-Stop Shop For Auto Body RepairEuropean Auto Tech is located in the Dallas-Fort Worth metroplex. The organization has several mechanical repair facilities and a central MBUSA Certified Collision Center that is equipped with current MBUSA-approved repair technology, and employs technicians who have been trained by MBUSA and I-CAR. “For owners of Mercedes-Benz vehicles, our auto body specialists can make collision mishaps a distant memory. We offer a lifetime warranty on all our auto body repairs. That means paint will be an identical match, body panels will be a perfect fit and the vehicle will be aligned the way it was before your accident. In addition, if a customer’s vehicle needs mechanical repair as a result of an accident, our staff of MBUSA-certified technicians provides a complete range of electronic diagnostics and services necessary to discover and remedy any issues.†|
Blueprinting enables a collision facility to become a leaner, more efficient operation. Eliminating wastes within your work environment, as well as within the processes and procedures you employ, should be done uniformly and consistently by each team member. When you establish a common ground, resistance to change is more easily overcome by the entire staff.
One means of leveraging blueprinting to become a leaner work environment is to integrate principles known as the “5S’s†into your repair planning. These five principles are:
- Sort — Reduce clutter and unnecessary items in work areas. Rank each tool and piece of equipment by how often it is used.
- Set in order — Determine critical resources needed for a job and evaluate an appropriate location for each.
- Shine — Work areas, tools, equipment, and other resources need to be maintained. Clean each item regularly, noting service, repair, or replacement of resources when necessary.
- Standardize — Look for easy ways to create consistency, and create standard operating procedures.
- Sustain — Ensure all team members get the chance to provide input to changes in the work environment, processes, and procedures. Create a culture that encourages innovation within the workplace.
These may appear to be lofty goals, but if changes are developed with buy-in from the team and implemented incrementally over time, you have a better chance of sustaining these changes. It takes a great deal of hard work to overcome old habits. Remember to give your team the space and authority to incorporate change in a consistent manner across your entire operation, thus giving them the keys to attaining personal success.
One final note: You will encounter processes and procedures that can’t be altered, for whatever reason. Remember to accept them with grace, and turn your attention and energy to the items that you have control over.Â
0 Comments