It’s been 13 years since Volkswagen first put Fuel Stratified Injection (FSI) into production. Generically called Gasoline Direct Injection, this efficiency-improving system is getting ever more sophisticated. Here’s what you need to know as a basis for diagnosis and to help your customers.
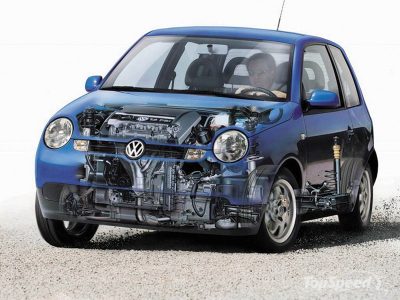
The concept of injecting gasoline directly into the cylinders of an internal-combustion engine originated in Europe in 1902 for use in very early aircraft, believe it or not. The logic was compelling, but without the benefit of sophisticated combustion science and the precision of electronic controls, it was just too inaccurate and unwieldy to be successful.
Back in the 1970s, two critical forces revived interest in the venerable idea: Fuel supply and price crises, and concerns over air pollution, characterized by Earth Day and the Clean Air Act. Various “programmed combustion†designs were tried by different automakers, the basic goal being to get extremely lean air/fuel mixtures to fire dependably by having a reasonably rich plume present around the spark, but technology still had not evolved to the point that they were practical enough for commercial production.
The potential for a 15% increase in fuel efficiency (or, to look at it another way, that same percentage less CO2 emission) and overall cleaner running kept Volkswagen’s engineers at it, however. The company introduced a 1.4L four with Fuel Stratified Injection (FSI) for overseas markets in 2000, and has been refining the system and using it on more and more engines, turbocharged (TSI) and otherwise, ever since. VW’s main collaborator and supplier in this effort has been, naturally, Robert Bosch GmbH of Germany, which recently celebrated the production of its 50 millionth GDI injector, and 10 millionth high-pressure pump.
Worth the trouble?
You might wonder why they’ve bothered to develop this complex technology when regular low-pressure sequential port electronic fuel injection seems to work so well. Certainly, systems from L-Jetronic through Motronic have served us admirably for decades, but they have some inherent drawbacks that just can’t be engineered away. First, timing precision ultimately depends on when the intake valve opens, not necessarily on the millisecond when the injector is pulsed. Besides being relatively crude in its essence, it also means that only one injection event is possible (more on this later), and that only during the intake stroke. Further, spraying gasoline into the ports and at the backs of the valves provides an opportunity for a portion of it to condense on the metal surfaces, thus falling out of atomization to perhaps be pumped raw out of the cylinders.
“Paradymn shift†has become a cliché, but it really does apply here. Not only do we get the benefits of stratified charge and controlled swirl that allow incredibly lean mixtures during certain modes, but there’s also no quenching, and timing is determined by the light-speed of the electronics, not the ponderous movement of heavy steel valves as operated by camshafts. Fast heating of the catalytic converter is made possible, too, as we’ll explain.
Broadly, GDI is quite similar to a common-rail diesel injection system, albeit at only a fraction of the pressure (in case you’ve never heard, some “EFI†diesel pumps generate up to 30K psi (2,000 Bar!). Volume through the injectors changes, however, not only according to the open time the ECM commands as determined by electronic logic based on sensor input, but also by varying the pressure in the rail.
Biz End
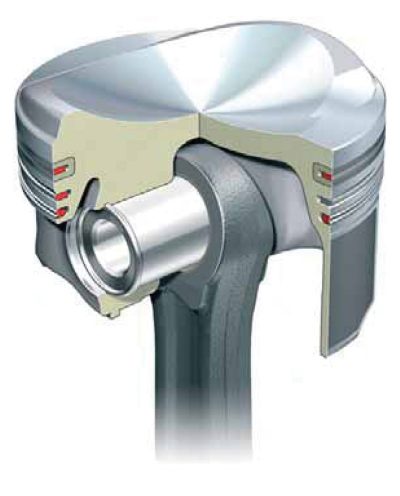
Since what happens in the combustion chamber is where the real subtleties lie, we’ll concentrate on a description of that.
Just as the shape of the piston top has a great deal to do with the dynamics of the burn in a D.I. diesel, so it is with GDI. The plume of atomized gasoline is made to swirl and take shape as it strikes this sculpted area, and the engineering of this required the most technical study imaginable to determine the optimal airflow characteristics and define the shape of the piston. Something called “Doppler Global Velocimetry,†which makes it possible to evaluate airflow characteristics and mixture formation while the engine is running, was employed in this research.
The goals here are to avoid both detonation and quench by having the fuel burn in a controlled “programmed†manner, rather than just randomly. The plume is shaped so that the mixture is rich enough to fire right at the plug gap, but very lean elsewhere. Once initial ignition is achieved, the flame front keeps burning and consumes every trace of fuel.
All parts that are in direct contact with fuel use designs and materials that allow dependable operation on any available gasoline grade or quality without fear of undue corrosion or wear. The requirements in terms of manufacturing tolerances and material durability are much more stringent for compressing a thin liquid like gasoline to very high psi than for doing the same with relatively slippery and viscous diesel fuel, but VW and Bosch engineers have addressed this in admirable fashion.
On later models, each injector has six individual openings, providing optimum mixture preparation, reduced HC emissions, particulate matter formation, and avoids oil dilution.
Plenty of PSI
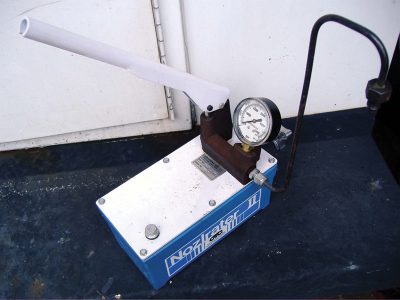
The high-pressure piston pump is driven by a two- or four-lobed cam (depending on the model and year) on the end of the intake camshaft through a roller, which reduces friction as well as the forces on the cam chain. The use of the four-lobe cam of later versions allows a shorter piston stroke. This, in turn, results in reduced pressure fluctuations. The metering precision of the injectors is also improved, as there is now one feed stroke per injection. This provides improved oxygen sensor control and fuel efficiency.
In a typical Volkswagen, the high-pressure pump is capable of generating a maximum of 2,175 psi (145 Bar). The fuel pressure requested by the engine control module is adjusted by the Fuel Pressure Regulator Valve N276, which keeps it between 725 psi (50 bar) and maximum, depending on requirements.
Later versions of the high-pressure pump have their own pressure-limiting valve. It opens at approximately 2,900 psi (200 bar) and admits pressure into the pump chamber. Previously, pressure was discharged into the low-pressure circuit. Excessively-high pressures can build up in overrun, or when the engine heat soaks after shut-off. Pressure pulsations in the low-pressure circuit are reduced by a damping element integrated into the pump.
After the pump’s intake valve closes, electrical power to the solenoid valve is shut off. This valve is kept closed by the pressure in the pump until the piston feed stroke is complete and the intake stroke begins.
Hot Cat Fast
Volkswagen FSI and TSI systems were designed from the ground up with emissions control in mind. The “homogenous†split catalytic converter heating process makes a good example.
This process brings the catalytic converter to operating temperature quickly after a cold start by using two injection events for each combustion cycle. The first takes place during the intake stroke and achieves an even distribution of the air/fuel mixture. In the second, a small amount of additional fuel is injected shortly before Top Dead Center (TDC) of the compression stroke. This late injection increases exhaust gas temperature, which heats up the catalytic converter so that it can start doing its job sooner.
Deposits and Service Notes
Just as with any other big-departure technology, FSI/GDI had some teething problems early on. They couldn’t be blamed on the design or materials, though. For example, since the backs of the intake valves aren’t continually bathed in gasoline and its detergent additives, anything that happens to stick to them won’t be washed off.
That is, Positive Crankcase Ventilation (PCV) gases and the exhaust that’s allowed into the intake for the purpose of internal Exhaust Gas Recycling (EGR). Even though VW PCV systems filter these more thoroughly than any other we’ve seen, they are by their very nature made up of many, many hydrocarbon compounds, some of which are sticky and tend to cause deposits. And even after the most efficient combustion possible, the waste gases are still not perfectly clean.
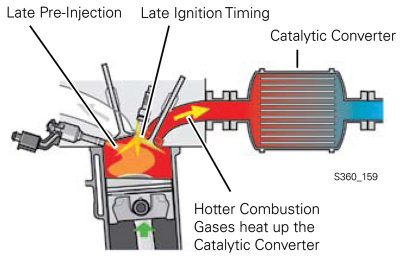
Volkswagen’s tech site, www.erWin.com, is the place to find out the best means of combatting and eliminating these deposits, thus keeping your customers happy with your level of service. All we’ll say here is that you should use only the highest quality motor oil in their engines, and advise them to fill up with “Top Tier†gasoline.
Speaking of service, we’ll conclude with some important notes:
- Always follow the official cautions and warnings when opening the high-pressure fuel system lines. Serious injury can result if proper procedures are not observed — the pressure is high enough to force gasoline through your skin, sending you to the hospital, or worse. “When servicing direct injection systems, the high fuel pressures that GDI systems utilize should always be in the minds of technicians. Bleeding down the fuel system properly is an important facet of service,†says Bob Pattengale, Director of Training for Bosch.Â
- Pattengale also warns us about possible electrical danger. “GDI injectors often actuate at approximately 70 volts and 10 amps, with the capability to rise to over 120 volts,†he says.
- When it comes to testing, be aware that applying continuous voltage to Fuel Pressure Regulator Valve N276 for longer than one second will damage it.
- On V6s, in order to install the camshaft roller chain, the High-Pressure Fuel Pump pinion must be locked with special tool T10332.Â
0 Comments