Working with this light metal in collision repair isn’t really more difficult than working with steel. It’s just different. Learn how to deal with those differences in a professional manner and you’ll be ready when an aluminum-intensive Mercedes-Benz rolls into your shop.
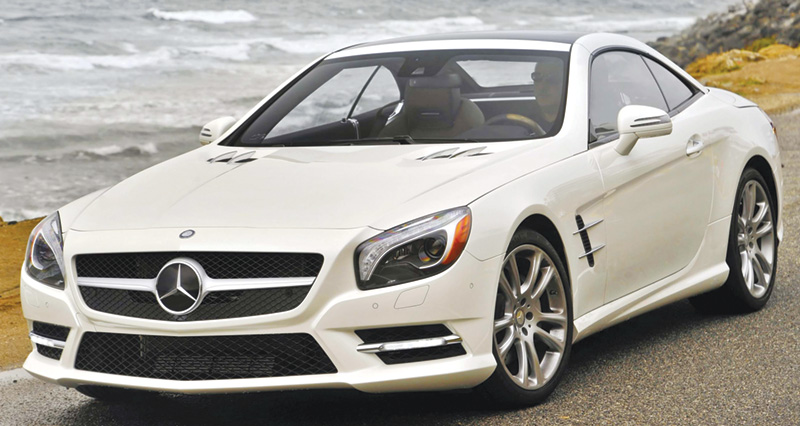
The first Mercedes-Benz SL in 1952 combined a lightweight aluminum body, an innovative tubular space frame, and an engine with direct gasoline injection. It won LeMans and the admiration of the entire racing world in its first season. The 2013 SL550 continues the tradition with an all-aluminum structure, innovative engineering, and flowing lines that exude power and grace at the same time.
Made from plentiful bauxite ore, aluminum weighs approximately one-third as much as steel, but can be combined with other elements to create alloys with strength equal to some High Strength Steels. Ongoing pressure on vehicle manufacturers to increase fuel economy guarantees that body shop technicians will each year for quite some time face a growing need for aluminum repair skills, tools, and equipment.
Current aluminum-intensive vehicles tend to be high-performance or luxury models such as the 2013 Mercedes-Benz SL.
Use of aluminum in some automotive parts however, including doors, hoods, roof, structural components, bumpers, and other body parts, has spread to mid- and even entry-market vehicles, and is increasing at a faster rate each year. When collision damage affects these aluminum components, special repair tools, materials, and techniques are required.
Don’t Touch Me, I’m Aluminum
If aluminum is in direct contact with other metals, it needs only a little moisture from the air to create electrolytic action – essentially a battery – in which electrons are exchanged between the two metals. The result is what looks like rust, or, if it is under paint, bubbles that will pop through the finish and ruin your repair.
This is more than just a cosmetic issue. Remember in the old days seeing chrome bumpers with one of the bolts corroded through and the bumper sagging on that side? That was galvanic corrosion in action.
At the factory, Mercedes-Benz prevents galvanic corrosion by placing a non-conducting barrier between two dissimilar metals. O.E. repair instructions will tell you how to duplicate this in the repair shop.
For example, the Mercedes-Benz recommended bonding adhesive may also function as an anti-corrosion coating. A fastener may have a coating that prevents galvanic corrosion. Pay attention to the installation instructions, as the coating is likely to make this a “one-time use†fastener.
Removing this type of fastener strips off some of the coating and reduces its ability to prevent galvanic corrosion. This weakens the repair, which may have safety implications for the customer, and definitely can harm a shop’s reputation.
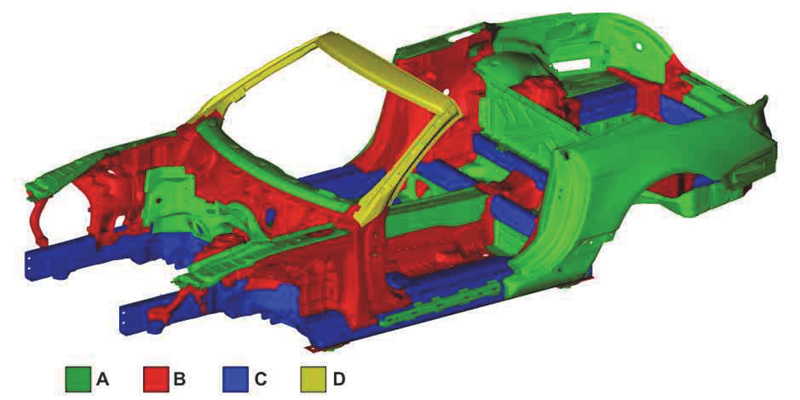
The only structural component in the Mercedes-Benz 2013 SL550 that is not aluminum is the windshield frame. The SL550 includes aluminum sheet metal (A), cast aluminum parts (B), extruded aluminum parts (C), and sheet steel (D) in the windshield frame.Â
I Want a Room of My Own
Unfortunately, this galvanic corrosion can also occur even if only a small amount of steel dust comes in contact with an aluminum surface. You need a space dedicated to aluminum work in order to minimize galvanic corrosion potential in a field repair environment.
It should have floor-to-ceiling curtains that close the space off from surrounding bays. This will keep steel dust from other vehicle repairs in the shop from settling on and contaminating your aluminum repair surfaces.
Your “clean room†needs its own air management system, a vacuum evacuation system to remove contaminants from the air and from work surfaces, and separate compressed air lines. A vacuum system offers another important benefit: It removes aluminum dust, which is harmful to breathe and (surprise) explosive in high concentrations, from the air.
You’ll need picks, locking pliers, and clamps that are made for working on aluminum. Hammers and dollies should have surfaces that are highly polished so they do not chip or flake easily, or are covered with a non-conductive material such as leather. Wood, plastic, or rubber mallets are good for working out minor dents in aluminum.
Label these tools so they are used only on aluminum, and store them in a dedicated toolbox so they don’t get mixed in with or pick up steel dust from other tools (or from the box).
Because access to the back side of many aluminum parts is restricted, you’ll need a weld-on-tab type dent puller. Expect to pay more. Dent pullers made for aluminum must produce more amperage than pullers designed for steel because of the way aluminum conducts current.
You’ll need many other tools, including an aluminum welder, spool gun, self-piercing rivet guns, fixture benches, and more. Mercedes-Benz requires specific models of welders that meet Mercedes-Benz requirement and training in aluminum welding procedures and equipment in order to be included in its certified aluminum repair provider network.
Extruded, Cast, or Stamped?
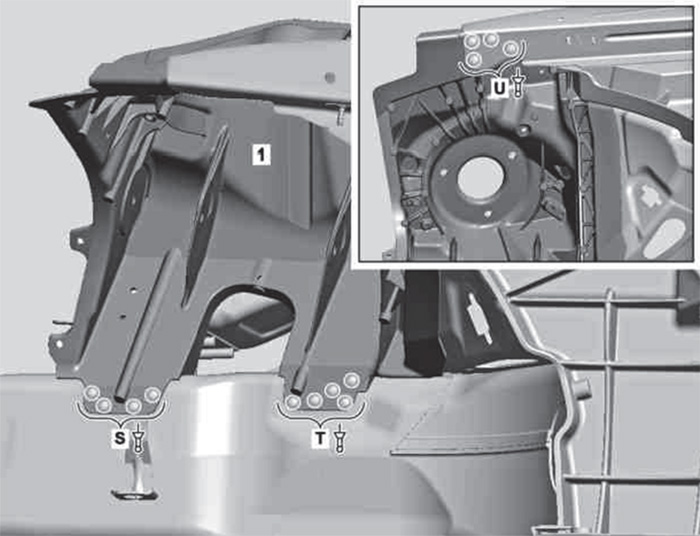
Mercedes-Benz instructions in WIS recommend replacement of a damaged Suspension Strut Tower – a cast aluminum component – using rivets and two-component adhesive in locations “S†and “Uâ€.
Aluminum automotive components are made in one of three ways: extruding, casting, or stamping. Frame rails once were built by welding inner sections together to create a stronger component. Today, they are made stronger by extrusion — pressing heated aluminum through complex dies to form multi-celled shapes. Ability to straighten extrusions is extremely limited due to the strength created by their complex internal sections.
Castings are created by pouring molten aluminum into a mold. Strut towers and pillars are made lighter and stronger through casting. Damaged castings MUST be replaced.
Stamped metal parts can include doors, hoods, and fenders. On aluminum-intensive vehicles such as the Mercedes-Benz SL, stampings can also include structural components such as rails, pillars, and crossmembers. Due to their relatively uniform thickness and simpler, non-sectioned design, stamped parts tend to be more readily workable for repair than extrusions or castings.
With This Rivet, I Thee Wed
For extruded or cast components that must be replaced rather than repaired, re-attachment can require bolts, rivets, rivet bonding, or possibly welding. Refer to WIS for recommended replacement procedures. Of course, bolts and rivets must be either aluminum or coated to prevent galvanic corrosion. If the component is mated to a non-aluminum part, instructions will specify parts that include a non-metallic material or coating between the two to help prevent galvanic corrosion.
Use a torque wrench to install threaded fasteners to the recommended torque specification. Stripping threads when installing fasteners on an aluminum part will ruin your day.
Humpty-Dumpty
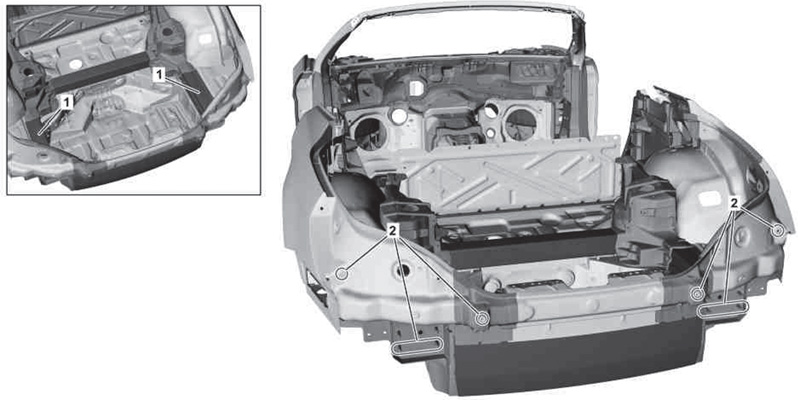
The floor in the area of the rear longitudinal member (1) is one of the few aluminum structural components on the SL550 for which Mercedes-Benz permits straightening, but only if the deviation from measuring points at “2†in the diagram does not exceed 3 mm.
Aluminum is not more difficult to repair than steel, but it requires different skills, tools, and equipment. Depending on the alloy, aluminum is more heat sensitive and less workable than steel. Technicians therefore have to become very good at judging in advance what can be heat-treated or pulled, and what should be replaced.
Refer to the Mercedes-Benz Workshop Information System (WIS) for the proper repair procedures. The company provides a wealth of information about where the different types of aluminum components are on the vehicle, and what tools and procedures are required to properly repair or replace a given component.
Jump in. Master the skills required for aluminum repair before your competitors get in the game. You’ll be a leader in your market, and keep your bays full with referrals from your customers (and from other shops).
Become a Mercedes-Benz certified aluminum repair facility. You’ll get extensive aluminum repair training, plus referral business from area Mercedes-Benz dealers that have no in-house collision repair capability. It’s a win-win.
0 Comments