Where safety is concerned, what’s more important than brakes? And now, of course, lots of sophisticated electronics are involved in stopping a vehicle. We need to keep up to speed on the systems that help cars slow down, yet not lose sight of the basics.
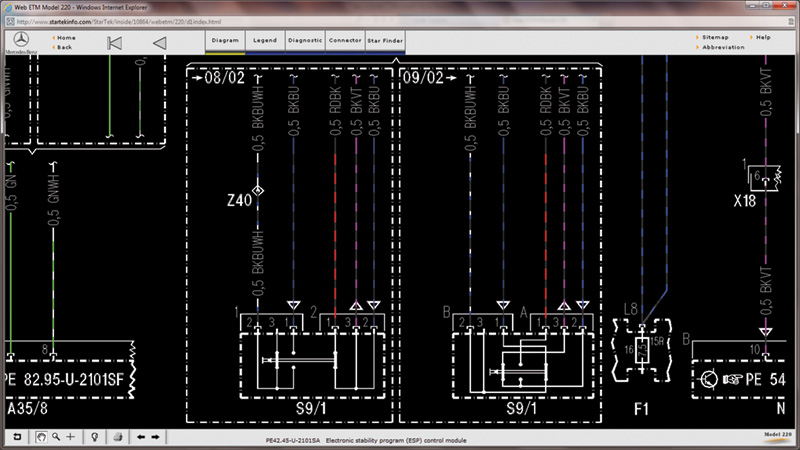
The brake switch is a major input. Mercedes-Benz uses a dual switch with opposite contacts. One switch is normally open (NO), and the second is normally closed (NC). Both of these switches change voltage readings when the brakes are applied, as you can see in this diagram.
One of the most common things we do for our customers is brake service. Brakes are probably the most important system on the car — aside from the powertrain that gets it rolling in the first place. Our customers are very sensitive to their brakes, so it behooves us to be very concerned with them, too. For years, much of their discomfort has been with noisy braking. They seemed to complain more about the squeal from a new set of pads than about any deficiency in how the vehicle actually stopped. But noise is just one of several potential problems in a modern braking system, and service is more than just relining.
Much better decel control
Many years ago before the advent of Anti-Lock Braking Systems (ABS), braking was a fairly simple operation. The driver would step on the pedal, which pushed a piston into a cylinder, which in turn generated hydraulic pressure that was routed to calipers that clamped friction material against rotors, thus converting rotating kinetic energy into heat energy and slowing the car. With such a rudimentary arrangement, panic stops may become a scary issue. If the braking force of any caliper exceeded the grip its tire had on the road, that wheel would lock up and the driver could be in danger of losing control. So, ABS qualifies as perhaps one of the greatest safety advances in automotive history. It, and further improvements in driver control, however, added complexities (especially the electrohydraulic variety) that we in the service business must understand before we can perform proper diagnoses.
ABS made electronic traction and stability control systems possible, and greatly improved the ability of even the best driver to deal with emergency stops and maneuvers, especially in conditions where traction is compromised. ABS took over braking during hard stops, Anti-Slip Reduction (ASR) applied the brakes to a wheel that has lost traction under acceleration (along with “relaxing†the throttle to reduce engine output), and the Electronic Stability Program (ESP) combined ABS and ASR (and in some models, systems that adjusted suspension stiffness, or even offered active suspension intervention) to orchestrate what some drivers have called “the hand of God†effect to help prevent accidents.
Of course, these systems add complexity, making diagnosis a high-tech enterprise when problems crop up. Over the past couple of decades, automotive technicians have had learn how to isolate the cause of a customer complaint: Is it mechanical, or electronic? Self-diagnostics have helped, but the electronic control unit must be able to see the problem for the program to work. Take, for example, a complaint that is familiar to all of us: low-speed ABS activation when traction conditions are normal.
Faulty signal
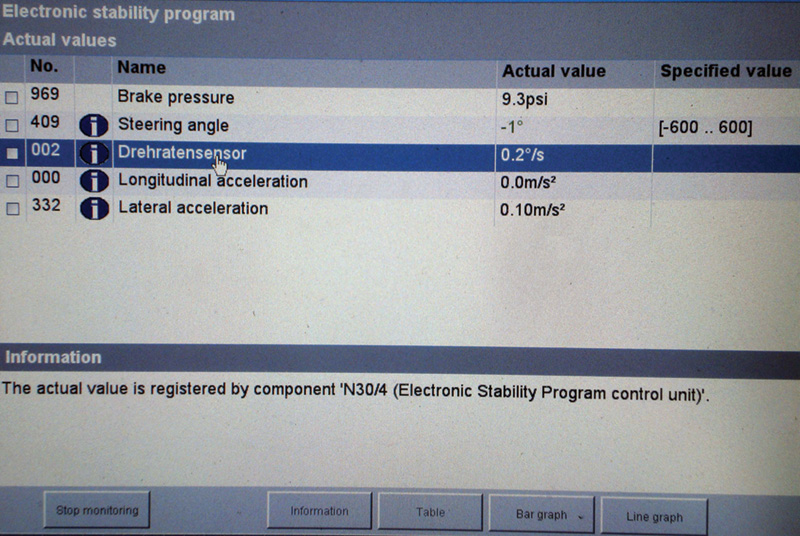
You can use your SDS/XENTRY to monitor many inputs, including that for brake pressure. You should know what options the vehicle came with so you can look into the correct control unit. Here we have the brake pressure at 9.3Bar on a vehicle with ESP, so we are looking in the ESP control unit.
If no fault codes are present, why is the ABS causing this pulsation? A likely scenario is that as the vehicle slows to a stop, a faulty signal from a wheel speed sensor (possible causes include high resistance in the sensor or wiring, debris interfering with the magnetic field from the tone ring, etc.) tells the control unit that a wheel is locking up even though it’s actually turning normally. Taking the speed signals from the other wheels into account, the control unit merely does what it was designed to do, and takes over the braking of the wheel with the weak signal. No code is flagged because this looks like normal intervention to the electronics.
So, it is our job to find out which signal(s) is/are the problem. Luckily for us, Mercedes-Benz has incorporated one of the most comprehensive diagnostic systems in the industry. With an SDS/XENTRY system, can access DTCs, live data and activations. Something to keep in mind is that ABS, ASR, and ESP are all shut down while in the self-diagnostic mode. So, if you road test the vehicle, do it in a safe place. Remember that it is much safer to have someone else drive while you watch the scan tool. Monitoring the wheel speed sensor readings as interpreted by the ABS/ESP control unit should identify the problem.
All of these electronic controls depend on two other systems operating properly: the friction-producing mechanical components, and the hydraulics that empower them. Some of us technicians (present company included) jump right to the scan tool to look for codes. While this is not a terrible idea, if no codes are present we need to have a diagnostic strategy that will give us the results we want in a cost-effective manner. To be able to diagnose a braking complaint, you should have a complete understanding of the systems involved. Of course, this will depend on the particular systems the vehicle you are working on includes. Most vehicles brought to the United States have the high-end options, but with so many possible combinations you are going to need to know the differences. Going back to the early ‘90s, the possibilities are:
- ABS (Anti-Lock Brake System),
- ASR (Acceleration Slip Reduction),
- ETS (Electronic Traction System),
- ESP (Electronic Stability Program),
- BAS (Brake Assist System),
- 4ETS (4Matic + ETS),
- SBC (Sensotronic Brake Control)
This is not to mention earlier systems, such as ASD (Automatic Locking Differential).
Sound foundation?
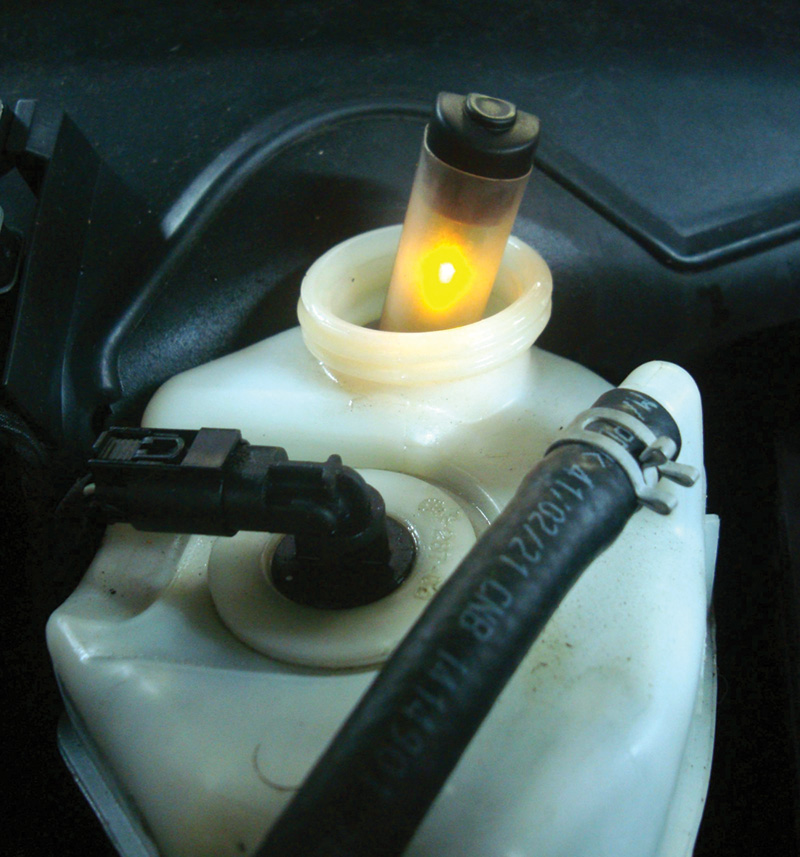
There are tools available that test the water content in the brake fluid. Here, the amber light indicates the presence of excessive water in the master cylinder reservoir. Mercedes-Benz recommends that you flush the brake fluid every two to three years as important basic maintenance. This will keep the fluid boiling point high to help insure consistent performance under heavy braking, and go a long way in preventing corrosion.
Before you jump into any deep diagnostic work, you first should have a look at the basics involved. These include some systems that you might not think of when evaluating a braking problem. Certainly, you should perform a visual inspection of the brake system hydraulic and mechanical components. The master cylinder must supply the necessary fluid pressure (except in the SBC system) through the brake lines to the calipers. The calipers must move freely on their guide sleeves in a floating caliper design. With fixed calipers, the pistons need to move freely or uneven brake pad wear will result, as well as uneven braking at each wheel. These factors are obviously related to braking, but others are not so obvious. As with any other computer-controlled system, stable voltage supply and ground are requirements. This is why you cannot overlook the charging system and battery, although more than likely a control unit will flag DTCs if there’s a problem.
One major service procedure (and opportunity!) that is too often overlooked is flushing out the hydraulic system and replacing the brake fluid. Mercedes-Benz maintenance schedules state that this should be done every two years, or 20,000 miles. Brake fluid is hygroscopic, which means it absorbs moisture from the air at any opportunity, particularly in the master cylinder reservoir. A very important characteristic of brake fluid is its ability to handle the heat generated during braking. If there is water in the brake fluid, it will boil at a much lower temperature than the brake fluid itself. While fluids aren’t compressible, the steam created in this situation is. So, the driver depresses the pedal, the gas vapors compress, and the pedal hits the floor. Vigorous pumping may be necessary to get enough psi to the calipers to stop the vehicle. Many people would not even know enough to do that, and a very dangerous state of affairs arises.
Also, as the seals within the hydraulic braking system wear, debris can become suspended in the brake fluid, or accumulate within areas of the hydraulic circuit. This can cause pistons or valves within the ABS/ESP system to stick or jam. A brake fluid flush removes most of these contaminants, so amounts to cheap insurance against expensive repairs.
While over the long history of hydraulic brakes numerous means of flushing and bleeding the system have been used, with a conventional brake system (master cylinder, ABS/ASR control unit, and calipers), the only procedure approved by Mercedes-Benz is the use of a pressure bleeding unit installed on the master cylinder reservoir, which keeps the reservoir full while the bleeders are opened.
Unconventional Sensotronic
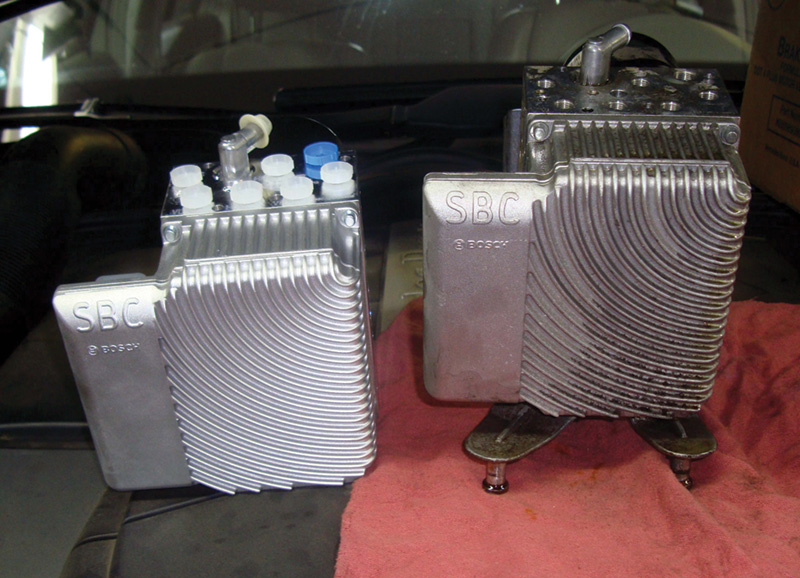
The SBC control unit contains the charge pump and accumulator that generate and store the brake fluid pressure used to stop the vehicle. When servicing this unit, or any other component in the brake system, you need to deactivate SBC. This brings fluid pressure low enough so you can open the hydraulics, or simply change the brake pads.
The Sensotronic Brake Control (SBC) system is easy to identify. It does not have a booster to amplify the force of the driver’s leg to the master cylinder. Instead, it has a Brake Operating Unit (BOU). This houses the reservoir, the tandem master cylinder, and a brake pressure simulator. The master cylinder isn’t normally in operation, and is only present in case of total SBC failure. The pressure generated in the master cylinder is directed to the two front wheels only. The brake pressure simulator simply gives the driver the feel of a conventional brake pedal for an added level of comfort and familiarity.
Only during an SBC failure is there a limited direct mechanical/hydraulic connection between the brake pedal/master cylinder and the calipers. Normally, a Pedal Value Sensor sends the braking request to the SBC control module. This determines how to match braking request and apply the proper amount of brake pressure to the calipers. The SBC hydraulic unit has a charge pump and accumulator built in to generate and store its own pressure.
A self-check system engages each time the vehicle’s CAN systems are “woken-up.†This means when the door handle is touched, the ignition key is installed in the EIS, and/or the key is turned on. During the pre-drive check, pressure is applied to the calipers. If you activate the pre-drive check with the brake pads removed, the pistons may be forced out of the calipers. Therefore, before performing any service work on the brake system, you need to deactivate the SBC system. This can be done with your SDS/XENTRY. Once you have deactivated the SBC and finished the service work, you will need to activate the system (also done with the SDS/XENTRY).Â
Since SBC generates its own pressure, the bleeding procedure is not conventional. SDS/XENTRY software is required. Start at the right rear wheel, and continue clockwise to the right front wheel. The charge pump is activated throughout the procedure, so securely attach the special adapter to the bleed screw, or you’ll have a slippery puddle on the floor. You will be instructed when to open and close the bleeder screws. You will be replacing approximately 1.5 liters of fluid, so be sure the fluid level in the reservoir of the pressure bleeding unit remains adequate.
BAS muscle
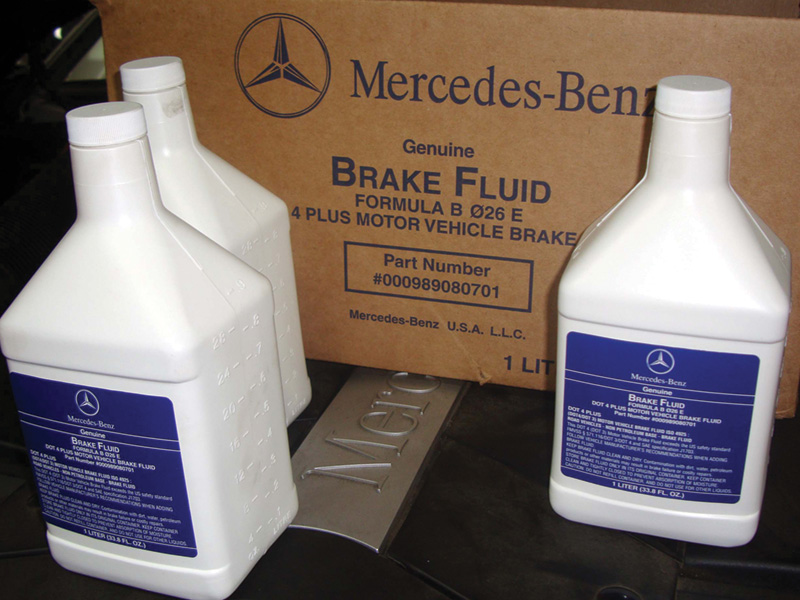
When flushing the brake fluid, you will be replacing over 1.5 liters with an SBC system, less with conventional brakes. Make sure to keep the reservoir fluid full while bleeding. The charge pump runs during the procedure, so make sure the bleeder hose is securely attached.
Conventional brake systems require a brake booster to amplify the force applied to the master cylinder. Mercedes-Benz developed BAS (Brake Assist System) to provide additional force during panic stops. In a normal brake booster, the amount of force depends on the volume of engine intake manifold vacuum it contains. For BAS, Mercedes-Benz uses a two-stage booster. With the engine off, barometric pressure bears on both sides of the diaphragm. With the engine running, both sides of the diaphragm are subjected to manifold vacuum. During normal braking, slightly more vacuum is held on the master cylinder side than on the brake pedal side. This difference in pressure applies force to the master cylinder. During a panic stop, manifold vacuum is still applied to the master cylinder side, but the BAS opens a solenoid releasing all the vacuum on the pedal side. This applies even more force to the master cylinder, thus generating greater brake fluid pressure throughout the system. ABS and ESP still monitor wheel lock-up and control the brake fluid pressure accordingly.
By having an in-depth understanding of how Mercedes-Benz systems operate and are integrated, you can provide the proper diagnostic and maintenance services that your customers have come to expect from you. Mercedes-Benz is a partner in this effort, recommending maintenance intervals, supplying accurate information on service procedures, and supplying genuine OEM parts to your local dealer. As a result of this partnership, everyone wins.Â
0 Comments