Unstable fossil-fuel markets, customer environmental awareness, and government regulations have all contributed to automobile manufacturers searching for the silver bullet for mpg. Mercedes-Benz has looked to its long diesel engine history, and added a huge dose of new technology.
Ask powertrain engineers and they will all tell you their ultimate goal is “the free lunch.†Of course, like the physicists’ Absolute Zero, that’s not really attainable, but it at least provides a clear direction. The goal of an engineer is to optimize an internal combustion engine’s output in order to produce maximum power while using the minimum amount of fuel. Approaches such as turbocharging, variable valve timing and lift, direct fuel injection, etc. all contribute to this main objective.)
There’s a concept that goes even further, however: compression ignition. Diesels have always squeezed more useful work out of a gallon of fuel than gasoline-burning engines, and with Mercedes-Benz’s application of advanced technology their inherent drawbacks in terms of noise, smell, emissions, cold starting, and lackluster performance have all been pretty much eliminated. This article is intended to help you keep up with this technology so that you’ll have a better understanding of the service requirements involved.
Since 1936

It was 77 years ago when Mercedes-Benz introduced the world’s first diesel-powered passenger car, the 260D.
Mercedes-Benz has always felt that the diesel engine has tremendous advantages when it comes to increasing fuel economy and reducing harmful emissions, although only the former was germane in 1936 when the company introduced the 260D, the world’s first diesel passenger car. It has successfully sold diesels to the American public for decades. With the modern push for fuel efficiency and clean exhaust, Mercedes-Benz has practically reinvented the compression ignition engine. Electronically-controlled high-pressure direct injection and an after-combustion catalytic system are just two of its prominent advances.
But revolutionary engineering improvements rarely come without additional levels of technical complexity, which makes our job of keeping everything operating properly challenging. We believe, however, that you will find that your experience with the electronic management systems of gasoline-burning engines will be very helpful.
Major psi
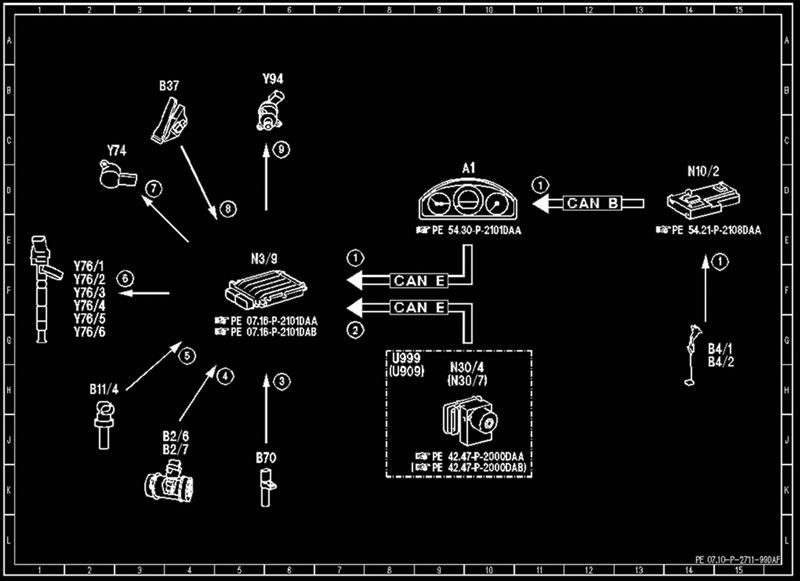
With a paid subscription to www.startekinfo.com, you can access function diagrams in the ETM section. These let you know what sensors and control units are involved in the system you are working on. This is a function diagram of the smooth-running system on the 642 diesel engine. The CDI control unit looks at all of these components to mitigate crankshaft fluctuations through individual cylinder injection control.
The Mercedes-Benz CDI (Common rail Direct Injection) system has an electric fuel pump that supplies relatively low pressure, but high volume, to the mechanical high-pressure pump that’s driven by a camshaft. The 5,000 to 30,000 psi (!) generated is routed through a common rail that branches to the individual injectors, so it’s similar to a typical port-type gasoline EFI albeit at up to 600 times the pressure. The injectors are opened when the CDI control unit sees fit, again similar to EFI.
As in any modern engine, the control unit gets signals from both crankshaft and camshaft position sensors to determine where the engine is in its four-stroke cycle (many other inputs are involved in the grand scheme of things, too, of course), thus when to fire each injector, but it’s relieved of the duty of controlling an ignition system. The serious pressure in this system not only greatly enhances fuel atomization, it also makes the efficient direct injection feature work better.
Once diesel combustion has taken place and the last possible ounce of power has been extracted from the air/fuel charge, Mercedes-Benz made sure the exhaust comes out squeaky clean by means of the Selective Catalyst Reduction system (SCR) that aids in the continued combustion of any excess fuel that did not burn in the combustion chamber. This utilizes urea injection — a chemical additive, commercially called AdBlue® Diesel Exhaust Fluid (DEF), is sprayed into the SCR system. This type of system has been around for years in the European trucking industry, so is not a new, untried concept. It’s needed to make the engine emissions-compliant, and be fully functional in order for the engine to be allowed to run.
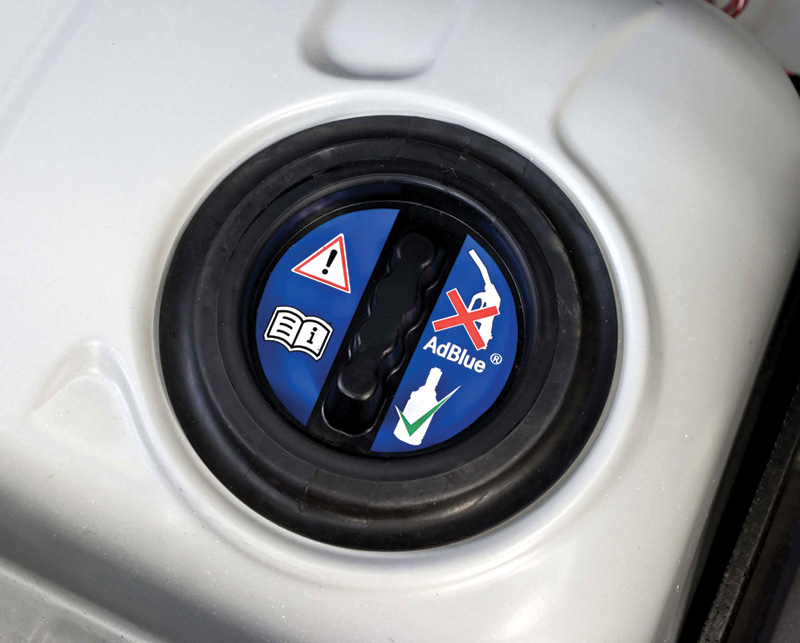
Here’s what the ADBlue® DEF tank filler cap looks like. The fluid level is continuously monitored to make sure there is enough. When it gets low, a message will appear in the instrument cluster, then there will be a warning gong.
An easily-accessible AdBlue® DEF tank is mounted in the vehicle, and each gallon lasts at least 2,500 miles. A level sensor lets the control unit know how much fluid is in the tank. If the fluid drops below a specified level, a message will appear in the instrument cluster (“Check AdBlue®/Check Diesel Exhaust Fluid (DEF)â€). If the vehicle is driven for a certain amount of time with the warning illuminated, a gong will be sounded. The number of gongs sounded starts at something like 21, depending on the model. If the level is allowed to drop even further, the number of gongs will go down also reflecting the number of engine starts permitted. Once it reaches zero, the control unit will either put the engine into idle mode, or prevent it from starting, depending on the model. Adding a gallon of AdBlue® will get things going again.
The players
We already know the CDI control unit completes the circuit to the fuel injectors. We also know that the control unit receives crank and cam position sensor signals so it can determine when to fire the injectors. But, as mentioned above, there are many other sensors and solenoids that help manage all that fuel pressure. Since time is of the essence in a high-pressure direct fuel injection system, more is needed than just increased injector on-time to add enough fuel under acceleration. The pressure itself is increased in order to get more fuel into the combustion chamber under high demand. This is one instance where diesel engines differ from their gasoline counterparts. With gasoline fuel injection, injector pulse width is increased to meet the demands of acceleration, but system pressure stays pretty much constant.
CDI controls the amount of pressure in the fuel system with a combination of a Quantity Control valve (mounted on the high-pressure pump) and the Pressure Control valve mounted on the fuel rail. Both receive pulse-width modulated signals from the CDI unit.
The CDI control unit needs to be aware of the actual pressure in the fuel rail (also called a “manifoldâ€) in order to calculate pulse width and pressure requirements. It gets this information via a high-pressure sensor mounted on the rail. As with any other diesel, the high compression generated by the engine starts the combustion process. On very cold days, it is sometimes difficult to get the fire started. In older designs, there was a pre-chamber with a glow plug installed. When the ignition key was turned on, the glow plug heating element was supplied with electric current. This would heat the fuel as it entered the chamber, making it easier to ignite. With CDI, pencil-type glow plugs are mounted directly inside the combustion chamber for pre-heating. A separate glow plug control unit supplies the necessary amperage with the ignition key on and during the warm-up phase to increase efficiency. The glow plug control unit takes its orders from the CDI control unit.
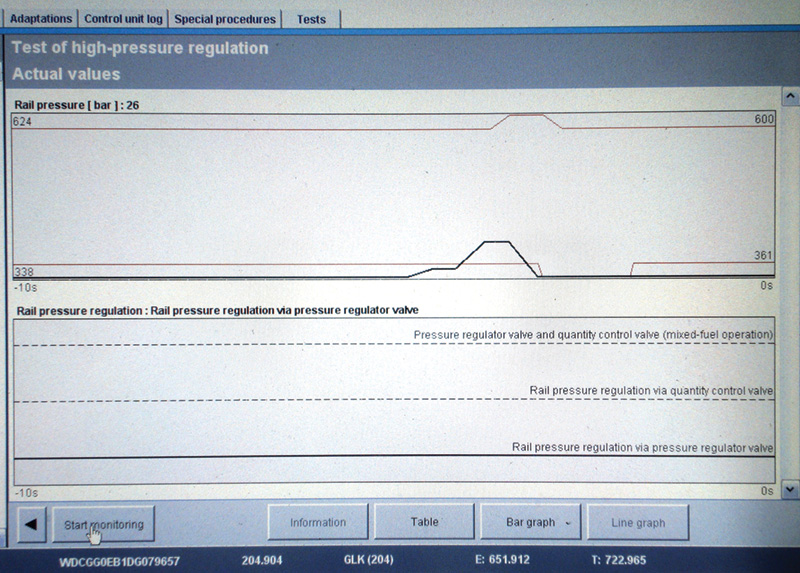
With a XENTRY system you can graphically display the fuel rail pressure as picked up by the fuel rail high pressure sensor. Here, we see the thick black line indicating the increase in psi as the engine is cranked and started (then immediately shut off). This can help in the diagnosis of a no- or hard-start condition.
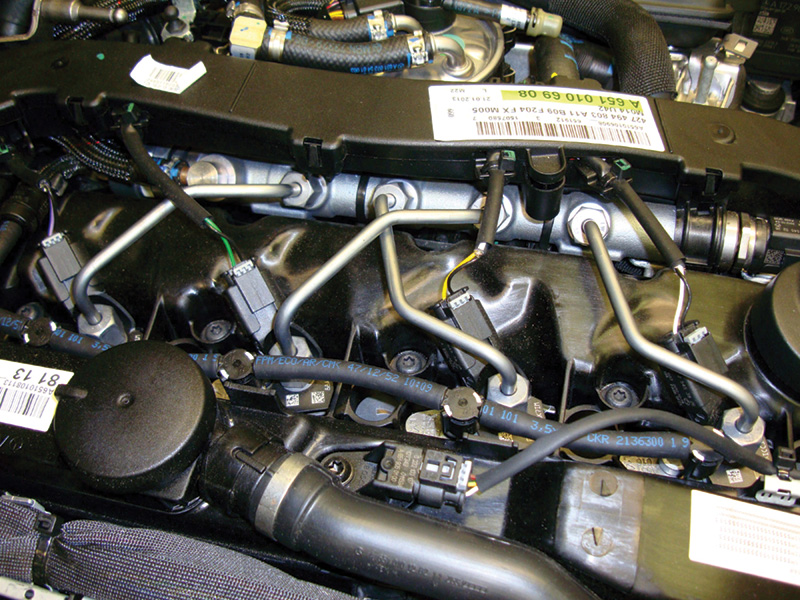
Here’s the fuel rail of the new four-cylinder Mercedes-Benz diesel engine that’s gaining so much notoriety. Metal lines carry the pressurized fuel to the individual injectors. The fuel volume is very small, so even a small leak will not allow pressure to build. This can lead to a hard- or no-start condition.
Injection actualities
When we think of traditional gasoline EFI, we think of a computer energizing a solenoid that allows pressurized gasoline to pass through a nozzle. With a high-pressure diesel fuel system capable of producing 30,000 psi or more, it may seem that it would be virtually impossible to electrically open an injector whose pintle has that much force bearing on it. Engineering injectors that could do just that dependably was one of CDI’s breakthroughs. Depending on the year, model, and country of sale, either the Piezo type or electric solenoid type has been used. Regardless, the traditional diesel’s rattle and knock are practically eliminated by up to seven injection events occurring for each power stroke. It’s not just one big blast anymore, but a relatively slow, controlled burn.
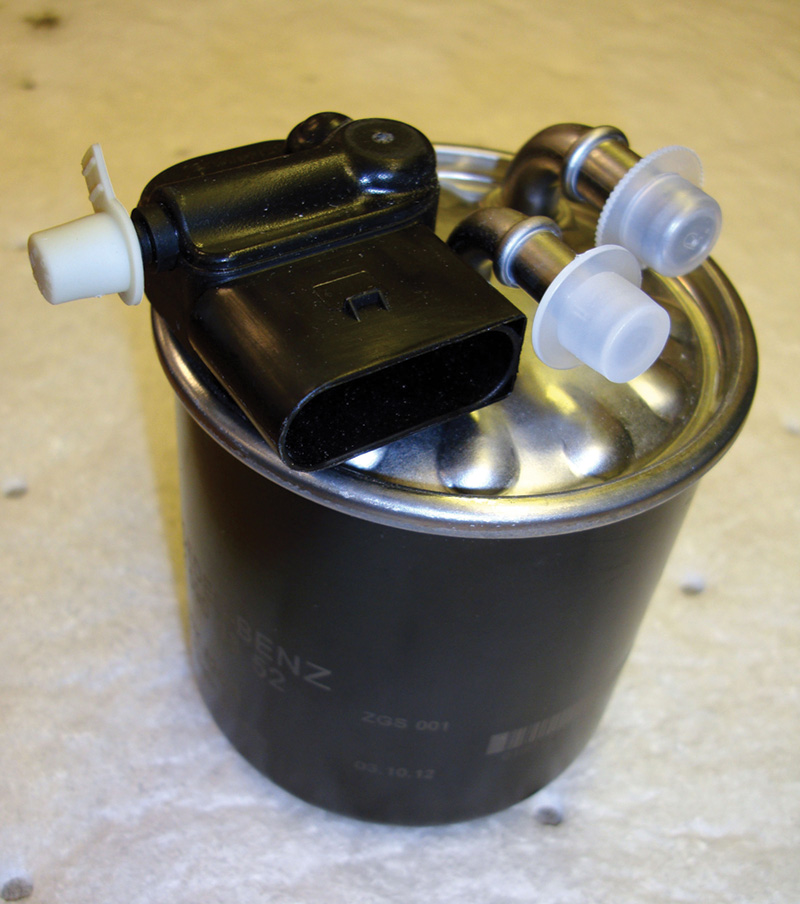
Between the fuel pump and the high-pressure pump, there is a fuel filter with a “water in fuel†sensor. When the filter’s water separator is more than half full of H2O, a warning light in the cluster will turn on. This filter needs to be replaced at the specific intervals outlined in the maintenance booklet, but may need to be replaced more often depending on the quality of the diesel fuel available to your customers.
Being a sequentially-fired injection system, CDI is prone to some of the same drivability issues usually associated with gasoline SEFI. Older diesel injection systems typically had a mechanically or electrically-controlled pump. A rack inside the injection pump would be moved to provide more or less fuel to all of the cylinders. If you had an individual cylinder misfire, or “nailing,†it was due to either the injector itself, or to an engine mechanical problem, such as a bad valve.
With common-rail, each cylinder is individually controlled. CDI has the sensitivity to continuously monitor and adjust injector flow rates to match the needs of individual cylinders. The CDI unit needs to know the flow rate of any injector that is being replaced. This information is entered into the CDI unit through the SDS/XENTRY software. As the injector wears, the flow rate may change over time. The CDI unit also monitors these changes and performs “adaptations†accordingly. These adaptations need to be cleared after replacing injectors or otherwise servicing the system so the CDI does not inject fuel using information from the old injectors. These adaptations can be viewed and reset with your SDS/XENTRY system.
We Need Feedback
Just like modern gasoline injection systems, there needs to be a sensor that monitors the effectiveness of fuel control. The CDI unit is always asking itself, “Am I injecting too much or too little fuel for complete combustion?†To get an accurate answer to that question, the CDI unit uses a wide-band oxygen sensor — the gasoline engine equivalent would be called an air/fuel ratio sensor. These sensors have a six-pin connector and use a milliamp signal to indicate a rich or lean mixture to the CDI control unit. They are capable of measuring a wider range of mixture ratios than could a traditional zirconium oxygen sensor. Having a good understanding of modern Mercedes-Benz diesel fuel injection systems will allow you to perform proper maintenance and more accurate diagnosis of any complaints. Your local Mercedes-Benz dealer’s parts department is a partner in this process, and will support you in making sure you have the knowledge and the quality parts needed to serve your customers in the most professional manner possible.Â
0 Comments