Great stopping power, pleasant pedal feel, no noise or pulsation, and long life are all good reasons to buy friction components and everything that goes with them from your local M-B dealer’s parts department. Your customers recognize quality and value or they wouldn’t be driving Mercedes-Benz vehicles in the first place, so explaining the following points to them should make them happy that they are choosing the best in brake parts – and a shop that’s offering only that.
Where safety is concerned, Mercedes-Benz engineers represent a paradox: They’re both forward-thinking and conservative at the same time. Certainly, they investigate and develop any new concept that might help keep Mercedes-Benz drivers and passengers from bodily harm, but nothing gets put into production until it’s been tested and proven to an extent you might find hard to believe. This is true not only of systems designs, but also of the materials and manufacturing processes used to produce the components. Therefore, the only way to feel confident that those systems will continue to function as designed is to use genuine O.E. replacement parts. This is especially so with brakes, as we shall see.
Big Business
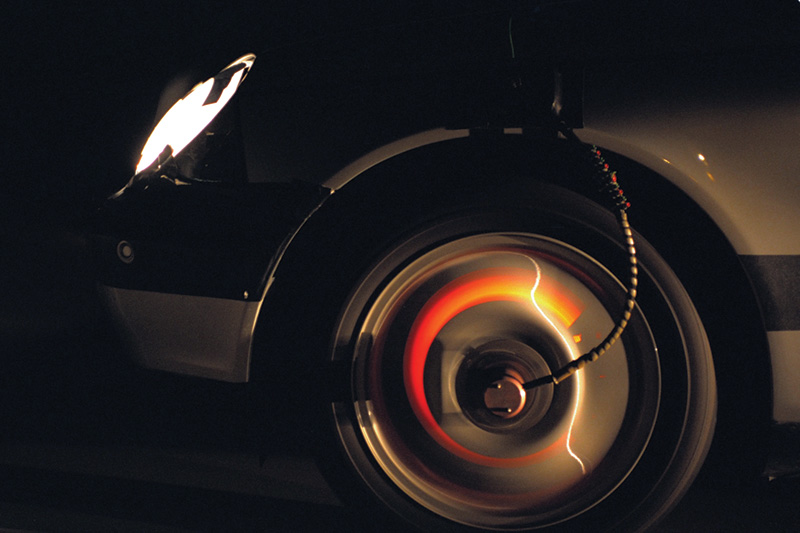
Nobody does more exhaustive testing than Mercedes-Benz engineers. We hope your customers never get their brakes this hot, but even if they do they’re covered – providing they’ve opted for genuine M-B friction components. It’s your job to advise them to do so.
Although many other areas of automotive service are shrinking as cars continue to get better and better, brakes are an exception. No matter how modern and well-made they may be, it’s in the nature of brake friction components to be sacrificial – you might call them consumables. Given that people are driving more than they did in years past, and in ever-increasing stop-and-go traffic, the market for brake work is actually growing. Another factor is the addition of high-tech on-board braking enhancements from ABS to Mercedes-Benz’s exclusive BAS (Brake Assist System) and SBC (Sensotronic Brake Control). In the long life expected of that company’s vehicles, there’s always a chance that these systems will need repair. So, it’s a pretty sure thing that this area of service represents a very large chunk of your business income. That’s one reason why it’s important that you manage it properly. Not only in terms of customer relations, but also by making wise parts-purchasing decisions. Think quality and value, not just price, and you’ll reap benefits in not only profitability, but also in freedom from frustration and worry. Let’s put it this way: How much is peace of mind worth to you?
Recipe for Success
Horror StoriesHistorically, Mercedes-Benz has done a better job formulating, producing, and testing its friction materials than some other car makers we can think of. We particularly remember many thoroughly-unpleasant, even frightening, examples of ill-conceived brake lining materials and shoddily-made pads from both O.E. and aftermarket companies. First, there was a domestic car from the early semi-met era. The original linings were so hard and abrasive that on the first brake check you’d find that the pads were still thick, but the rotors were worn down past their throw-away spec. Or, how about a powerful sports car whose brakes felt as if you were pushing cinder blocks against the discs? It made you cringe and avoid stopping at all costs. Then there was the time we road tested a domestic minivan right after the installation of O.E. pads at a dealership and ended up rolling through a red light into the middle of an intersection even though we were pressing on the pedal with both feet. Another example was a car in which the new aftermarket brakes would fade out completely on the first stop after any drive (the transmission and the parking brake were the inadequate, but only, means of dicey deceleration). It turns out that the aftermarket linings were made way too thick, so even with the caliper pistons bottomed they dragged continuously against the rotor and overheated. Some of those cases are from long ago, others not so much. Although things have generally improved throughout the industry, we don’t think using anything but genuine M-B O.E. linings is worth the risk. After all, they have an unsurpassed track record. |
Linings are the first thing that comes to mind when you hear the term “brake job.â€Â They bear the brunt of converting kinetic energy into heat energy, and are consumed in the process. How well they do that, how much noise and dust they make while they’re at it, pedal feel, and how long they last are all dependent on what’s known as the “recipe†of the friction material. For generations, there was just one ingredient, that dangerous, thready mineral asbestos. It was phased out almost completely three decades ago not only because of health concerns, but also because formulations with better performance characteristics were needed anyway.
The wholesale conversion to semi-mets, non-asbestos-organics (NAOs), and ceramics amounted to a major teething process throughout the industry, with one notable exception: Mercedes-Benz. Its lining formulas/recipes were always much less apt to cause squeal, eat rotors, or make dust than those of other manufacturers, or of aftermarket brands. That was because cost wasn’t the primary factor in deciding what would go into those pads; performance was.
That is still the case. When you buy genuine O.E. Mercedes-Benz pads from your local dealer’s parts department, you can be sure you’re getting the same formulation that the engineers hit upon while designing the brake system for that particular model. They won’t be something that will merely fit physically, but lack the proper performance characteristics.
Discorama
The other half of the energy-conversion device we call a disc brake is, of course, the rotor. There’s so much to this subject that it would easily justify a whole StarTuned feature, so we’ll just hit the high points here.
First, almost nobody turns Mercedes-Benz discs anymore. As one successful M-B service manager told us some years ago, “We threw our brake lathe in the trash.â€Â That’s a big change from traditional American brake service, and something your patrons may give you an argument about since they’ve probably been hearing about brake rotor machining ever since they bought their first car.
There are lots of good reasons to choose replacement over the lathe, however. First, although the machining of M-B rotors was regularly done in independent shops for decades, the company doesn’t approve of this operation because the O.E. tolerances aren’t reproducible in the field. Next, when you subtract the labor of turning rotors in a workmanlike manner on a well-maintained lathe, then cleaning them thoroughly (the avoidance of which task is a common cause of squeak and squeal), the difference between that alternative and installing new isn’t so great after all. In the case of cross-drilled discs, machining is not allowed, period.
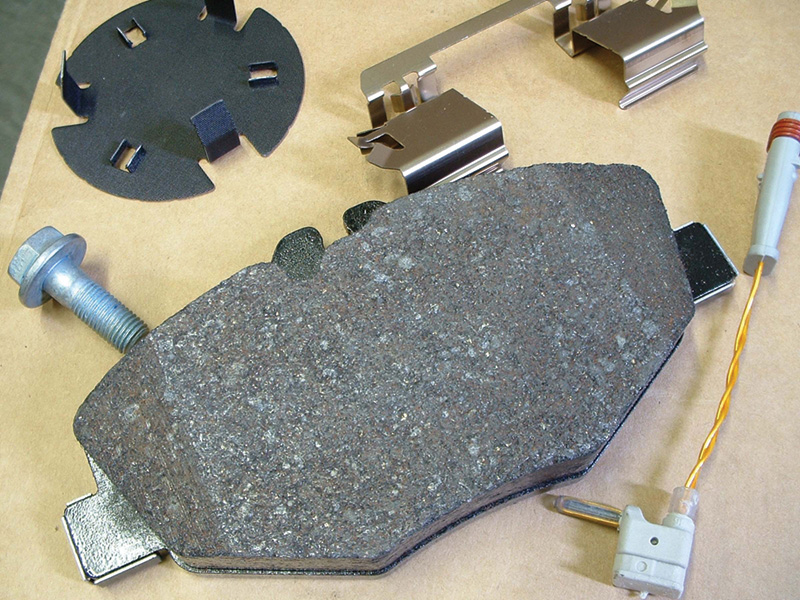
Another advantage to buying pads from your local Mercedes-Benz dealer’s parts department is that you get everything you need for the job in the package.
Besides being fast, rotor replacement amounts to a profitable parts sale for the shop. But how do you choose among the available options? Do you try to save the customer a few dollars, or would you rather feel confident that the job won’t come back to haunt you?
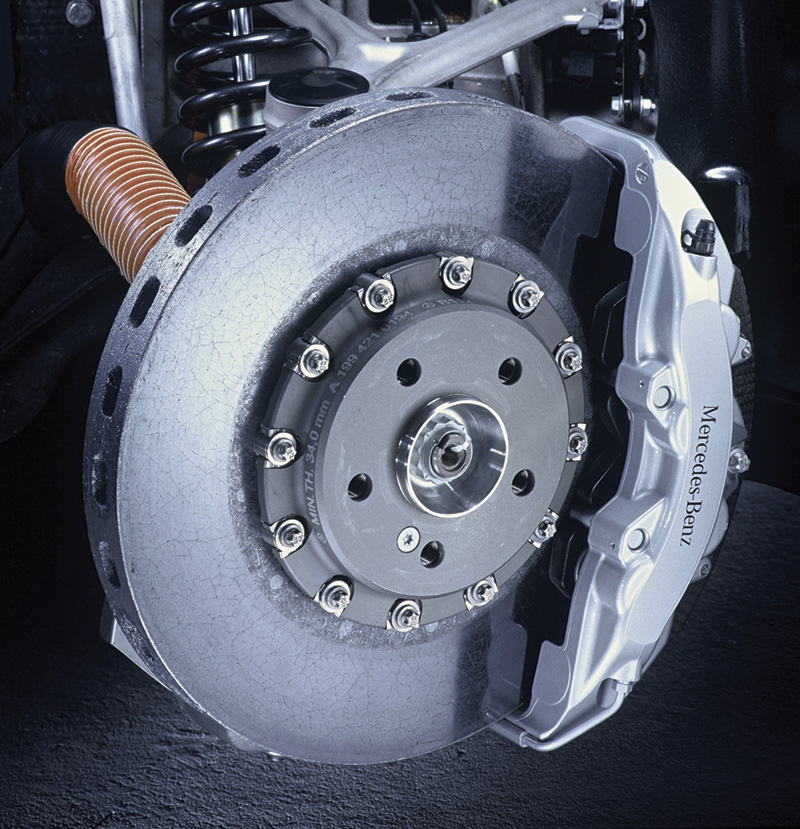
It’s not likely that you’ll ever have one of these super-high-performance McClarens in your shop with their fiber-reinforced ceramic-composite discs, but they show that Mercedes-Benz is on the cutting edge. Of course, machining is not an option here.
An independent shop owner tells us, “We’ve tried premium aftermarket rotors from one of the biggest disc manufacturers in the world, but we got warpage and comebacks. So, we did a little research and found that these parts weighed about two lbs. less than the original equipment discs. When we told the manufacturer about this, they said, essentially, ‘take it or leave it.’ We left it, and now we use only O.E. rotors.â€
A delicate diplomatic situation may come up that complicates your used disc/new disc decision. Suppose you replaced a regular customer’s rotors with the proper O.E. units at the last reline. Now, he or she’s been driving a lot and has worn out the pads in a relatively short period of time. You’ve wisely adopted the no-cut policy, but there’s still plenty of meat left on the existing discs to assure they won’t wear past the throwaway-thickness in the next cycle. You can’t help but feel that selling this loyal patron another new set of rotors after just, say, 30,000 miles might be perceived as excessive, even if he or she trusts you enough to bite the bullet. That, of course, puts an even heavier responsibility on you to do the right thing in this particular case. So, if there’s no evidence of pulsation, you might opt to just install new linings. While the notion of “hanging pads†might be offensive to your sense of craftsmanship, there are cases where it’s the only reasonable route. Just make sure you do it right so that you don’t generate a comeback.
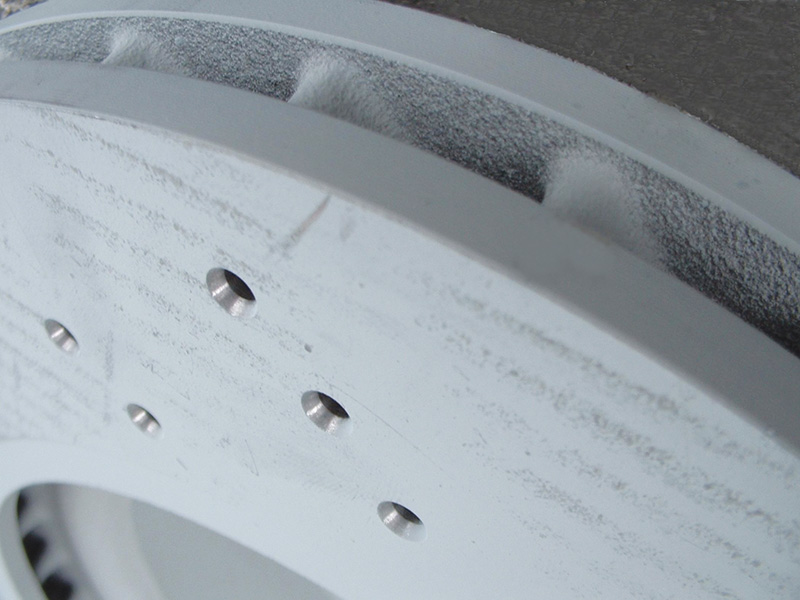
Perhaps you’ve been expending a lot of work cleaning that nice rust-preventative coating off a new rotor before putting it into service. You can stop now. It’s meant to stay on.
Crystal Ball
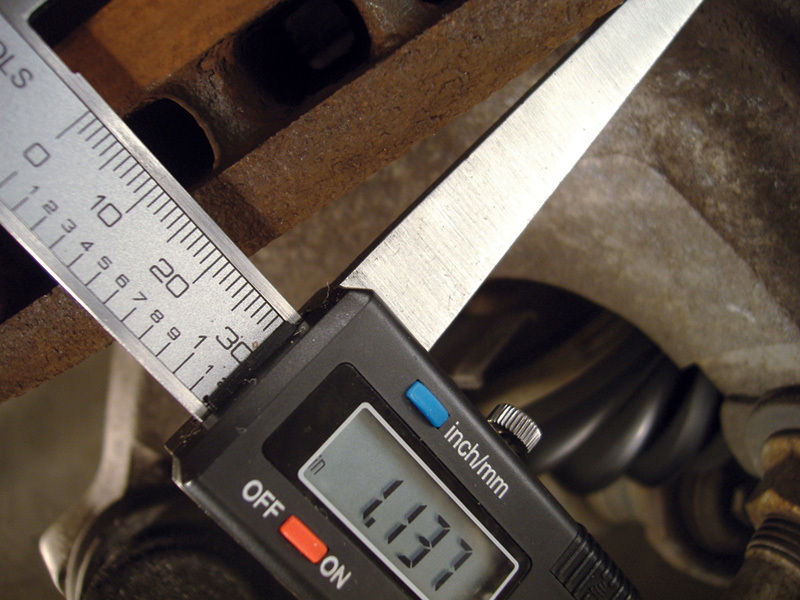
Our digital disc micrometer gives us fast readings, which we can use as a basis for rotor forecasting.
We should mention an excellent tool for the sale of new discs: rotor forecasting. Although you can find values for new and minimum thicknesses, and wear limits for maintenance, on WIS, the following method can transform hands-on measurements into a powerful justification for the replacement route. The idea is to take the original thickness of the disc (look it up, or measure an unworn area), then subtract the current thickness from that number, which will give you the amount of iron reduction the wearing out of one set of linings results in (or, if this is a second reline, two sets, and so on). Typically, this will be 0.032 to 0.040 in., or 0.8 to 1.0mm per cycle. If the rotor has more than that left, you can reuse the discs as-is and just hang those pads. On the other hand, if that subtraction puts you below throw-away, you’re leaving yourself open to both complaints and liability. It’s easy math to explain to your customers, and if you handle it right you should sell a lot more new rotors.
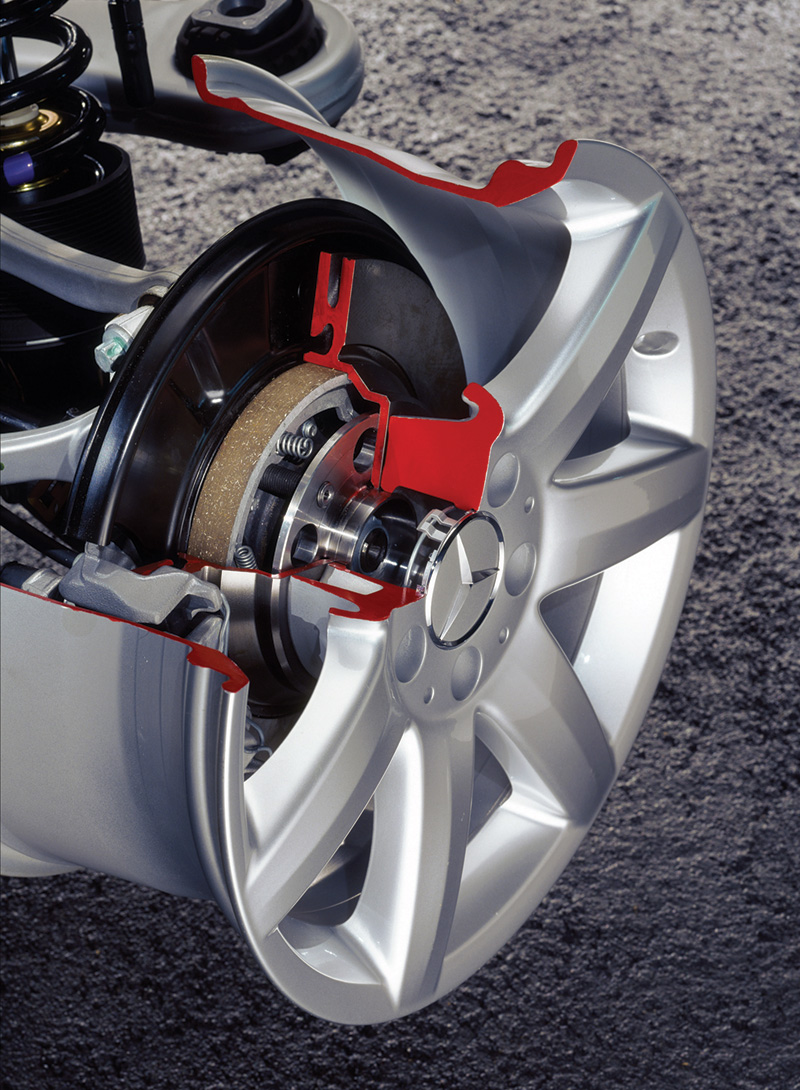
We’ve been talking about front brakes, but who wants squeaks or squeals in the rears? You’ve also got the little parking brake shoes and their mechanism to think about. No problem if you use genuine M-B parts.
We’ll conclude with some practical points:
- Genuine Mercedes-Benz replacement rotors come with an even, light-gray rust-preventative coating. You may have heard that this should be removed before installation, but that’s not true. The word from Europe is, “This highly effective surface protection enables installation without additional cleaning of the brake disc and full braking effect from the first braking movement is fully guaranteed.â€
- M-B has made special “cleaning pads†available to improve the wear surface of rotors that are to be reused without taking a lot of meat off. You drive no more than 300 meters at 30 kph (roughly 300 yards at 20 mph) while repeatedly applying the brakes moderately.
- Since Mercedes-Benz owners typically keep their cars for a very long time, you are probably still servicing older models with one-piece hubs and rotors. If you’re following the “no turn ‘em†philosophy, you should think about repacking wheel bearings and replacing the grease seal when a rotor is reused.
- There’s a factor that might cause problems with aftermarket rotors that most people aren’t aware of: hub chamfer. If the angle doesn’t match the hub exactly, the disc won’t seat right, leading to trouble with runout and heat dissipation, yet some cheap items just use, say, 45 deg. as a one-size-fits-all manufacturing convenience.
- The best-made rotors possible will tend to warp if you tighten the lugs with blasts from your thermonuclear impact wrench. Use a torque wrench in the star pattern.Â
0 Comments