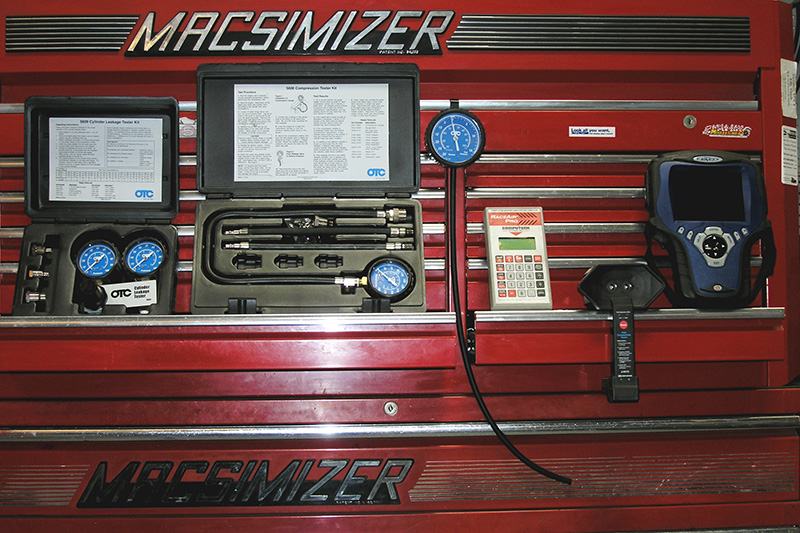
Having the right tools in your tool box makes it possible to unlock all the power and driveability that was built into the engine you are tuning.
One of the questions we always ponder: Is tuning an engine for maximum performance and/or fuel efficiency an art or a science? The answer appears to be that it is a combination of both. Back in the early days of hot rodding most of the fastest cars were set up by a highly-experienced tuner who could look at a spark plug to see if the air/fuel mixture was correct, and if the engine needed more spark advance.
But the changes in the formulation of today’s unleaded gasoline and the many advances in engine technology have made it almost impossible to come to any meaningful conclusion from reading a spark plug, unless the air/fuel mixture or the ignition spark advance is way out of whack. This may seem like bad news, but the computer age has made tuning tools, formerly only used by factory engineers, now relatively affordable for virtually anyone with the need for speed and performance.
The basic tools that every tuner should have in his tool box include:
- compression gauge
- cylinder leak-down tester
- fuel pressure gauge
- vacuum gauge
- manual vacuum pump
- volt meter.
These allow you to check the condition of the engine and be sure there is enough fuel pressure and fuel volume, and to verify that the operating voltage is correct for any electrical systems in the vehicle you are testing. You will also need a few specialty tools that can make it possible for almost any motorhead to become a tuning hero. These include:
- Ignition scopes and timing lights
- Gasoline test equipment
- Tools for checking the air/fuel mixture
- Exhaust gas analyzers
- Digital air/fuel meters
- Tools for checking ambient conditions
Ignition Scopes and Timing Lights
An ignition scope can be very valuable in diagnosing the ignition system. It allows you to check the electrical output of the ignition system, look for open plug wires, or fouled spark plugs, plus it provides secondary pattern diagnosis. This is one key to analyzing air/fuel ratios, stuck or burned valves, and other mechanical conditions that can alter combustion. Many ignition scopes also have a cylinder-kill function that can allow the user to check cylinder balance to be sure all cylinders are functioning equally.
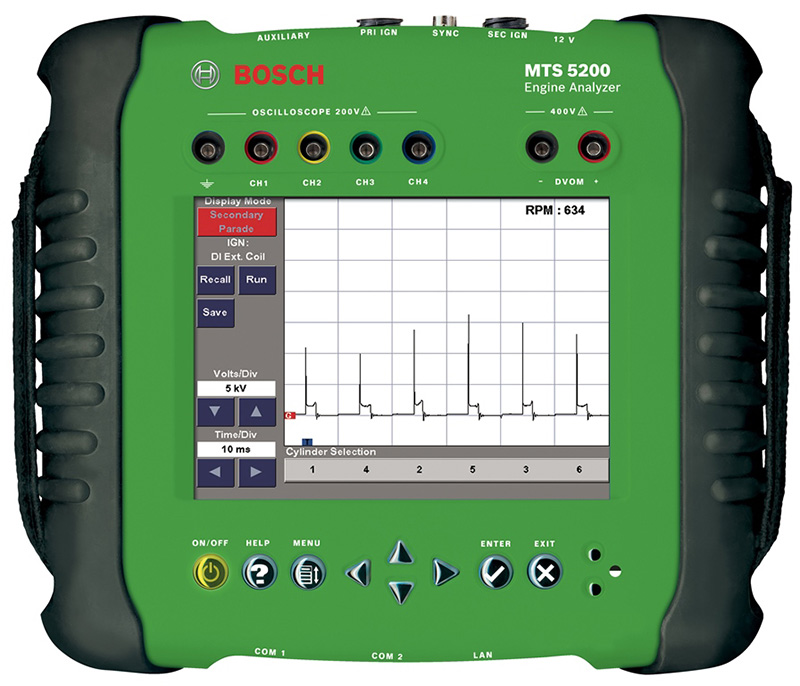
The Robert Bosch MTS 5200 Analyzer is a high-quality ignition scope, plus it can also allow the user to diagnose the health of an engine by looking at the vacuum signal created by each cylinder.
In an ideal world, every shop would have a distributor machine, and every engine would have a degreed harmonic balancer. But distributor machines are not as common as they once were, and most engines don’t have degreed balancers. It would be best to check the distributor mechanical and vacuum advance curves in a distributor test stand, but a dial-back timing light is a good second choice. It allows you to determine how much total advance an engine has so you can be sure its spark advance curve is correct.
Reformulated Gasoline and Gasoline Test Equipment
Gasoline quality is a real concern when you are diagnosing drivability problems, especially now that most of the gasoline sold in the United States contains ethanol. The addition of ethanol is causing corrosion and swelling problems with many fuel system components of carburetor-equipped vehicles not designed with ethanol in mind. Ethanol can act as a solvent that will attack any component made with plastic or rubber compounds, such as fuel hoses. It can also attack components made from brass, copper, and aluminum that can become corroded over time if they are not given proper surface treatments.
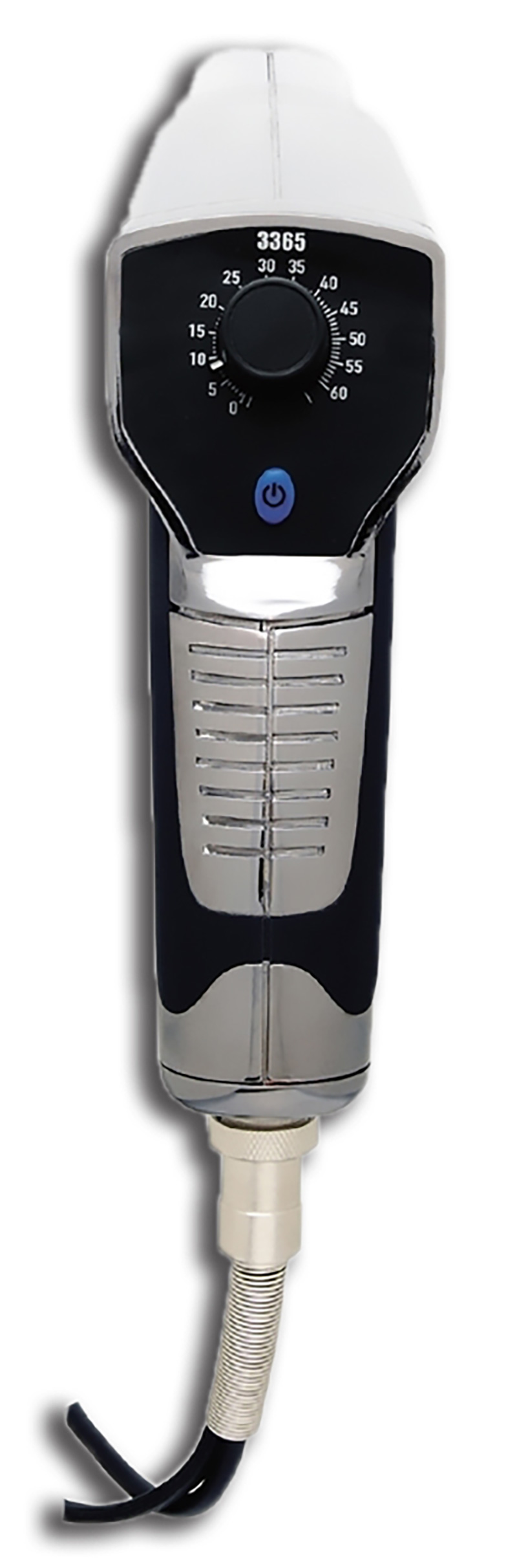
…but a dial-back timing light can also be used to get a profile of both the mechanical and vacuum advance systems’ curves.
The most common gasoline quality problems we test for are phase separation, high ethanol content, and low volatility. Phase separation can happen if the ethanol in the gasoline is exposed to enough moisture to cause it to separate from the fuel. This phase-separated ethanol and water mixture is very corrosive to most of the components in a carburetor-equipped vehicle’s fuel system. Both Driven Racing Oil and Sta-Bil offer fuel additives that will help extend the life of gasoline and prevent the corrosion problems that can happen using gasoline that contains ethanol. The OTC #7670 Gasoline Quality test kit can be used to test for water in the gasoline, fuel vapor pressure, and ethanol content. The Kent Moore/OTC #J-44175-A Flexible Fuel Tester provides a digital reading of gasoline’s ethanol content.
Tools for Checking the Air/Fuel Mixture
The biggest advancement in tuning tools has been in those that read an engine’s air/fuel mixture. The digital age has reduced the size and price of five-gas exhaust analyzers, and brought us very affordable digital air/fuel meter systems. The readings from a five-gas gas analyzer are comprehensive and accurate, and the readings can help determine what air/fuel mixture the engine needs for maximum efficiency. The reaction time is slow, however — six to 10 seconds. The readings from a wide-band oxygen sensor-based digital air/fuel meter are basically in real time, but users need to know what air/fuel mixture readings they are tuning for, and the unit can give false readings caused by an exhaust leak or engine misfire problems.
Exhaust Gas Analyzers
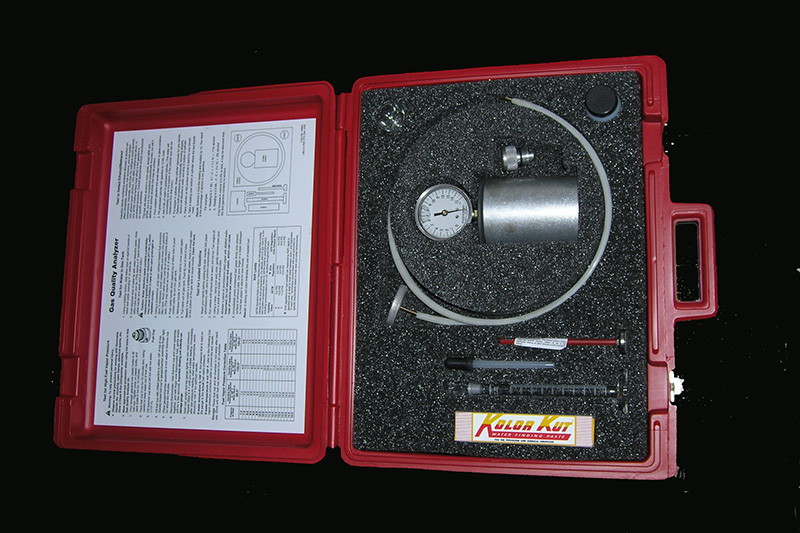
This gasoline quality test kit from OTC is used to check for water in the gasoline, the fuel vapor pressure, and the ethanol content.
A five-gas exhaust gas analyzer provides readings that give information needed to determine the air/fuel ratio, misfire rate, and combustion efficiency. Plus, the readings can be used to see if the engine has any detonation issues. These readings can allow an experienced tuner to determine what air/fuel mixture an engine needs for maximum engine efficiency, and can help in the tuning of the ignition spark advance systems. The exhaust gas analyzer looks at:
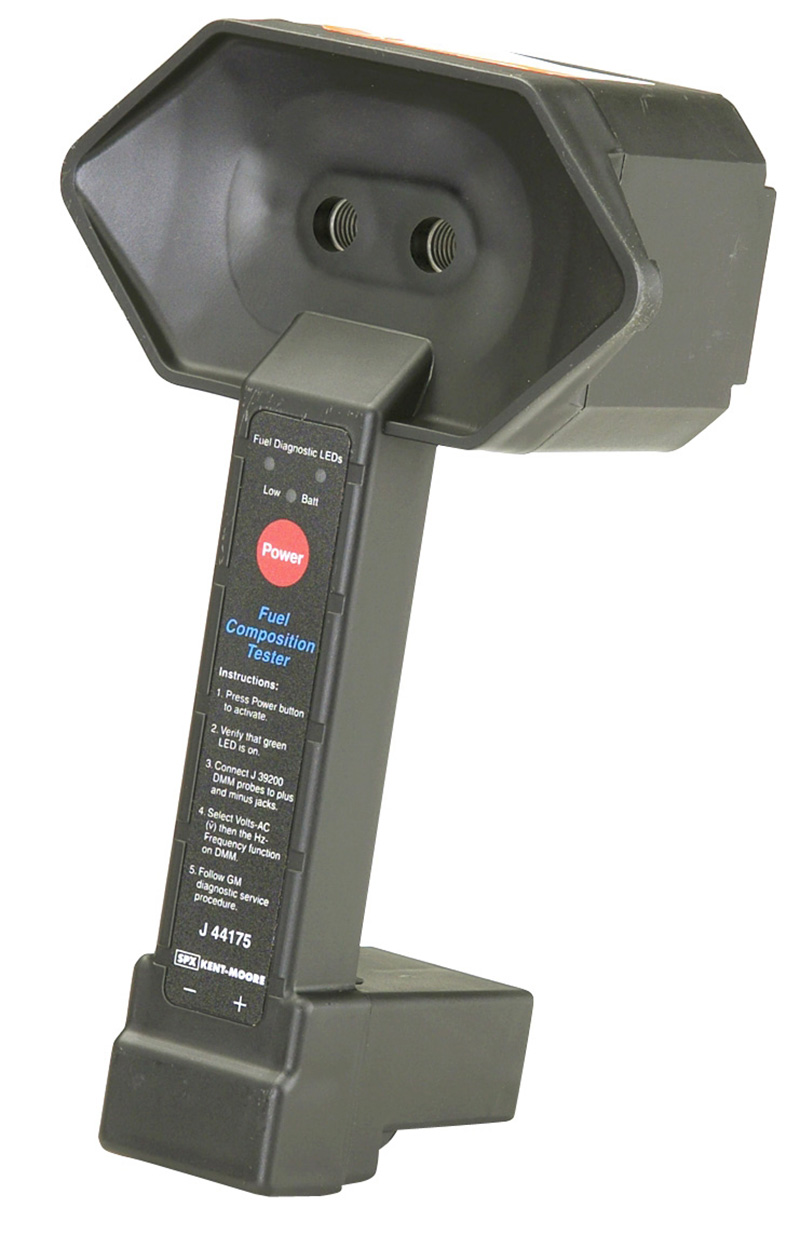
This Kent-Moore Fuel Composition Tester gives you an electronic readout of the ethanol content of a gasoline sample.
- The CO (carbon monoxide) reading is determined by the air/fuel ratio. A low reading indicates a lean air/fuel mixture and a high reading indicate a rich air/fuel mixture.
- The HC (hydrocarbons) reading shows the amount of unburned fuel in the exhaust, normally caused as the engine misfires. The ideal air/fuel mixture and the ideal spark advance setting will provide the lowest HC reading, as long as the fuel is fully vaporized
- CO2 (carbon dioxide) is a product of complete combustion. The best air/fuel mixture and the best spark advance setting will give the highest CO2 reading.
- A high O2 (oxygen) reading — excess oxygen in the exhaust — indicates a lean mixture, an exhaust leak, an engine misfire problem, or an engine with a high-overlap camshaft at low engine speeds.
- NOx (oxides of nitrogen) is created by excessive combustion chamber heat. In many cases, a high reading may be related to excessive ignition timing advance, creating detonation, or an engine with an insufficient cooling system, and can result in engine damage
Digital Air/Fuel Meters
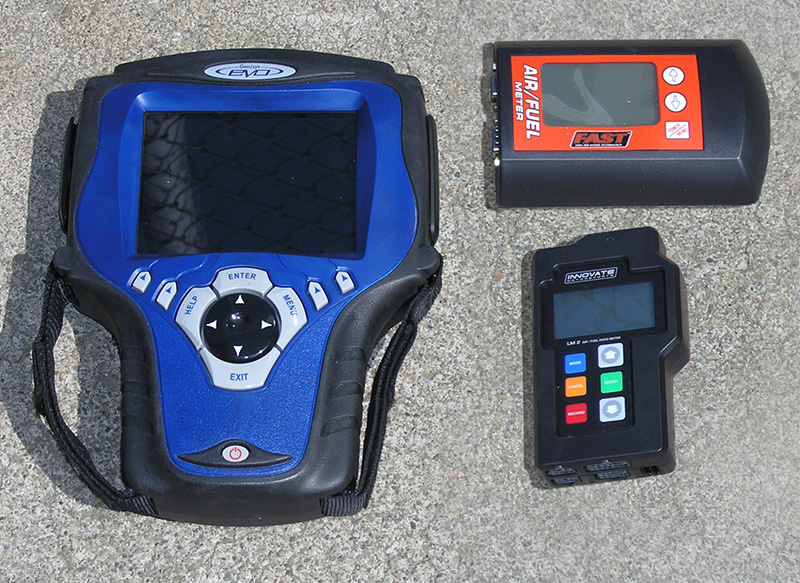
The digital age has reduced the size and price of five-gas exhaust analyzers, and has ushered in an age of very affordable digital air/fuel meter systems.
A wide-band oxygen or AFR (air/fuel ratio) sensor-based digital air/fuel meter can allow a technician to accurately read the mixture in real time, but the engine needs to be running efficiently if the readings are to be accurate. This type of meter uses a wide band oxygen sensor mounted in the exhaust system that tries to maintain a stoichiometric (14.6:1 by weight) air/fuel ratio in the sensor’s detection chamber by sampling the engine’s exhaust and by pumping oxygen in or out of the detection chamber. The sensor emits voltage that indicates relative oxygen content — or lack of it — in the detection chamber. It “looks†at the value of the pumping current the wide-band sensor requires to achieve a stoichiometric mixture, and compares this with the actual air/fuel mixture readings in real time.
The readings from such a meter are very accurate as long as the engine is properly burning the fully-vaporized air/fuel mixture in each cylinder. The readings will not be accurate if the sensor is exposed to a high level of unburned combustibles from an ignition or mechanical problem that would cause the mixture to not fully burn in each cylinder, or if the sensor is exposed to outside air from an exhaust leak. Any time the air/fuel mixture readings indicate that a major tuning change is needed, it would be wise to confirm the readings with an exhaust gas analyzer before major changes are made — the oxygen sensor can easily misread the exhaust and supply false lean readings.
An example of a situation that could cause false readings from a digital air/fuel meter are incorrect ignition timing, the fuel not being fully vaporized (only vaporized fuel will burn), fouled spark plugs, a cylinder that is misfiring, or an engine with a high-overlap camshaft at low engine speeds. The sensor will “read†the unburned oxygen that is in the exhaust from the cylinders that misfired and assume that the oxygen is there because the air/fuel mixture is too lean, and will supply a false lean reading.
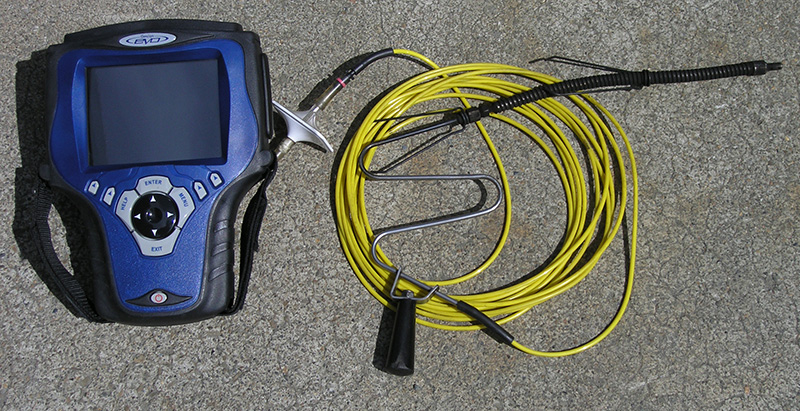
The OTC/SPX performance exhaust gas analyzer module mounts on the back of the company’s Genisys scan tool.
The Best of Both Worlds
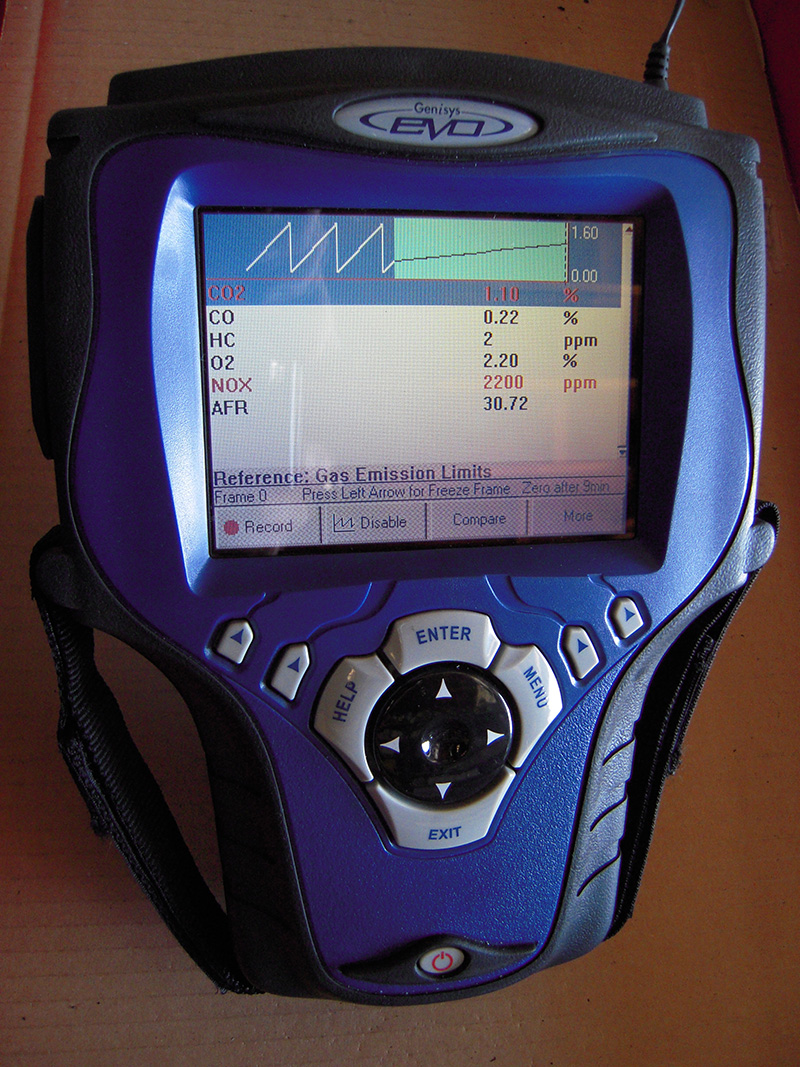
A five-gas exhaust analyzer samples the gases at the tailpipe to provide information on the air/fuel ratio, misfire rate, engine efficiency, and more.
Since both the five-gas analyzer and the digital air/fuel meter tuning methods have their advantages, we use the five-gas to tune both the air/fuel mixture and the ignition system, then we use the digital air/fuel meter for more advanced tuning during real-world operating conditions. If you’re lucky enough to have a chassis or engine dynamometer available, use it to determine what air/fuel mixture the engine wants to make maximum power, then check to be sure the engine is getting the same air/fuel mixture readings when you are driving it on the road.
If the readings are different, check to ensure that the fuel pressure and fuel volume are adequate for the needs of the engine, and be sure that the fuel tank vent system is operating properly — you can only pump fuel from the fuel tank as quickly as the vent system allows air into the tank to replace the fuel being pumped out.
Air/Fuel Mixture Targets
If you are tuning a new or rebuilt engine, it would be wise to ask the engine builder what air/fuel mixtures you should be tuning for, as well as what ignition advance curve he or she suggests. If this data is not available, a good starting point for the air/fuel mixtures on a generic engine would be:
- An idle and cruise mixture of 14.1 to 13.4 to 1 air/fuel mixture (1% to 3% CO).
- A power mixture of about 12.0 to 1 (6.6% CO) with most early vintage carburetor-equipped engines, but if the engine is equipped with newer fast-burn cylinder heads it may use a slightly leaner power mixture of 13.0 to 1 (4% CO).
- The thing you need to know is that both the five-gas exhaust gas analyzer and the digital air/fuel meters supply the user with the average air/fuel mixture of all the cylinders that the tool is analyzing. It’s more than likely that the air/fuel mixture will vary from cylinder to cylinder.
Many of the best performance tuners and engine builders use the data they get from multiple wide-band oxygen sensors, placed in the exhaust header tube of each cylinder, to determine the exact mixture of each cylinder so they can be sure each has the ideal blend for maximum power. This same tuning method can also be used to observe any fuel mixture changes that are caused by the G-forces that are seen during race conditions.
One example of this tuning method being used in actual race conditions is in NHRA Pro Stock. The data allows tuners to observe how much the air/fuel readings on the track changed from the readings they got when they were tuning the engine on the dynamometer. Many of the top carburetor-equipped engine race teams in both drag and oval track racing use these air/fuel mixture distribution readings as a guide when they are designing their intake manifolds so they can get maximum power.
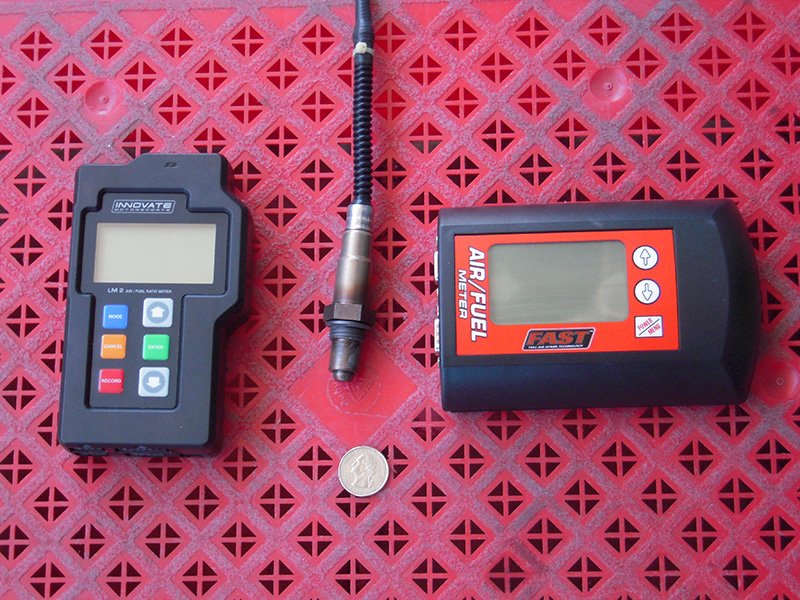
Don’t let the small size fool you; a wide-band “oxygen†sensor based air/fuel meter is an essential tool that should be in your tool box.
Checking the Weather
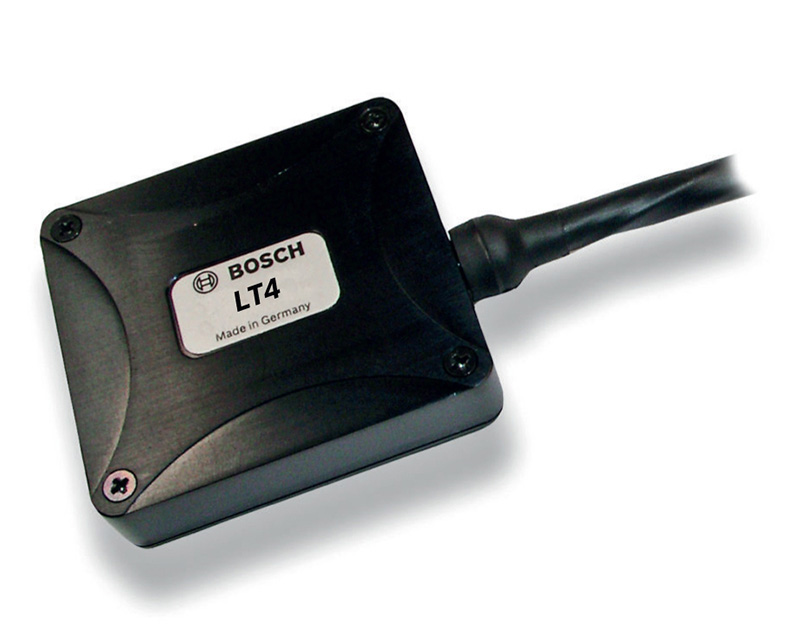
The Bosch Lambdatronic LT4 can tap into up to four AFR (air/fuel ratio) sensors at once. It’s the unit many of the top engine builders for NASCAR, including Hendrick Motorsports, use in their engine test cells and at the track for mapping and tuning their fuel injection systems.
The tuning you’ve done may be correct for the density and altitude of the air — this includes the air temperature, density, humidity, and barometric pressure — at the moment the tuning was done. But whenever the density/altitude of the air changes, you may need to re-tune the engine for these new conditions. The computer of a modern fuel-injected engine uses the readings it gets from its various sensors to determine the density of the incoming air as part of the calculations it does to determine what commands it should send to the fuel injectors and what the ignition spark timing should be.
The computer then fine-tunes the mixture and the ignition spark advance for maximum efficiency. If you are tuning an engine for maximum power, it would be wise to consider using a weather station such as Computech’s Race Air Pro so you can know what the weather conditions are and then tune the engine for ever-changing air density.
Burning the Fuel
Don’t forget that the fuel must be fully vaporized in order for the engine to convert it into power. Most production carburetor-equipped engines use an exhaust passage across the bottom of the intake manifold to use heat to turn any liquid fuel into vapor. It has become very popular to block the exhaust crossover in the intake manifold, or to use an “air-gap” style manifold to keep the incoming air/fuel mixture cool. This may work quite well in hot-weather areas, but it will cause power and drivability problems when the ambient air turns cold. If there’s not enough heat in the intake manifold to fully vaporize the fuel, the engine will often not idle properly, have poor throttle response, and may lack power at low rpm. So, with every part you buy, be sure it is designed to work properly with the expected driving conditions.
Getting It Right
Once you have spent the time to be sure the ignition system is doing its part to light the fire, and that the correct mixture of fully vaporized fuel is present, the engine you are tuning will provide all the power and fuel efficiency that was engineered into it.
…Happy Tuning!
by Henry P. Olsen
Â
This info may be useful to hot rodders. It is useless to experienced professionals. We already know this stuff.
This sentence irked me:
>An idle and cruise mixture of 14.1 to 13.4 to 1 air/fuel mixture (1% to 3% CO).
Any car built after 1975 needs to have a 1.2% or lower CO reading in order to pass emissions in my state. Also, pretty much any street legal car that’s spewing 3% CO at idle is in a poor state of tune.