In the past two installments we discussed how the dimensions of a car and its overall weight distribution can affect cornering and handling. Let’s see how we can utilize this information and begin to upgrade the suspension.
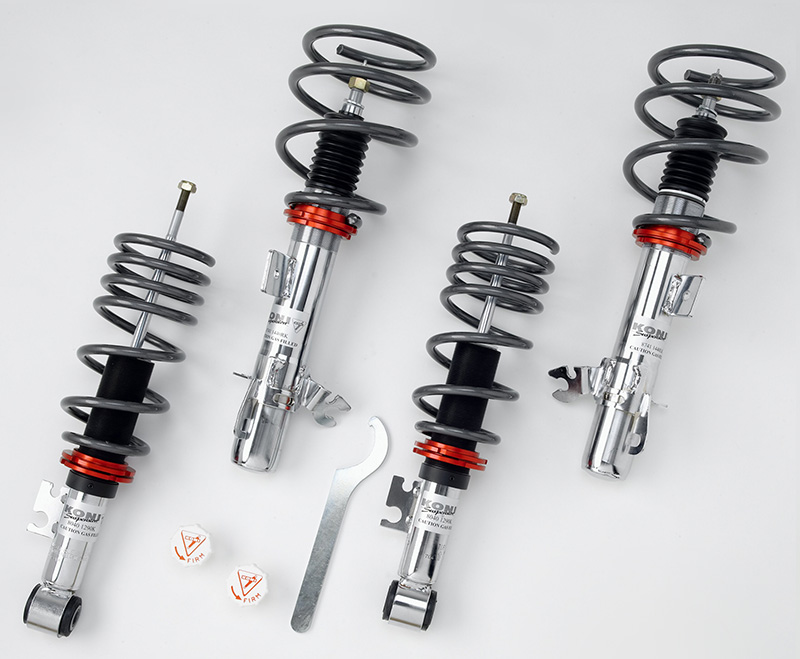
These high-quality fully-adjustable coil-overs will give you all the options you need to tailor your suspension to your liking (courtesy Koni).
The weight of any car is obviously an important factor in cornering and handling, as well as outright performance. When accelerating, the less the car weighs the better. When braking, the less mass of the vehicle the shorter the stopping distances. As a lighter car corners, the suspension system has to handle less mass as it keeps the wheels in contact with the road, especially over rough road surfaces. Less stress on the suspension will allow the shock units to maintain a consistent dampening rate over the course of a race.
Weight distribution can have a great effect on how a car corners and handles. A vehicle with more than 50% of its weight on the front end of the car will overload the front tires at their traction limit under both braking and cornering, and cause the front end to “push†or slide away from the apex of the corner when the car is turning in a phenomenon called “understeer.”
If the weight is biased toward the rear of the car, the back tires will tend to “oversteer,†or slide out while cornering when they are at the limit of traction. Depending on the type of racing you do, you may want to move components around to tailor the weight distribution to match your needs as best you can, if the race rules allow.
Side-to-side weight distribution is just as important — a road racing car, needing to make left and right hand turns throughout the race — will want close to even, or “neutral,†weight distribution for more stable cornering in both directions. On a rear-wheel-drive oval-track car turning left only, the driver would usually want more weight on the left side of the car. Under acceleration, the pinion gear in the rear axle slams the ring gear upward, raising the left rear of the car. If it is severe enough it will cause a loss of traction at the left rear wheel. By adding more weight to the left rear we can offset this torque reaction, promoting even contact patches and more uniform traction from both rear wheels.
A Brief Review
On oval tracks when cornering left, the weight of the car will be transferred from the left side of the car to the right side, providing an even “footprint†for each corner of the car. This “static†weight distribution is a good place to start, but you can also change the weight by adjusting the height of the suspension at an individual corner. This is known as “preloading†the suspension.
If you make the suspension unit at one of the corners longer, that corner and the diagonal opposite corner will carry more of the weight of the car. We have already learned this is known as “wedge.†If the wedge is 50%, the cars handling would be considered neutral, all other things being equal.
Adding more weight to the right front or left rear wheels would be considered positive or +50% wedge. If the weight were directed to the left rear or right rear wheels, this would be considered a negative or -50% wedge. Wedge is used to fix problems with oval track cars and drag racers that can take advantage of only turning in one direction, or going straight and reacting to torque loads. Road racing cars may only benefit from a slight wedge if the course favors more left-hand turns than CART or IRL cars normally experience, driving counter-clockwise on a race track. It was widely reported that Formula 1 race car driver Jacques Villeneuve was recruited by the Williams Formula 1 team because of his ability to set up a car with some wedge for tracks that favored either more left- or more right-hand turns, even though they were road courses.
What’s Next
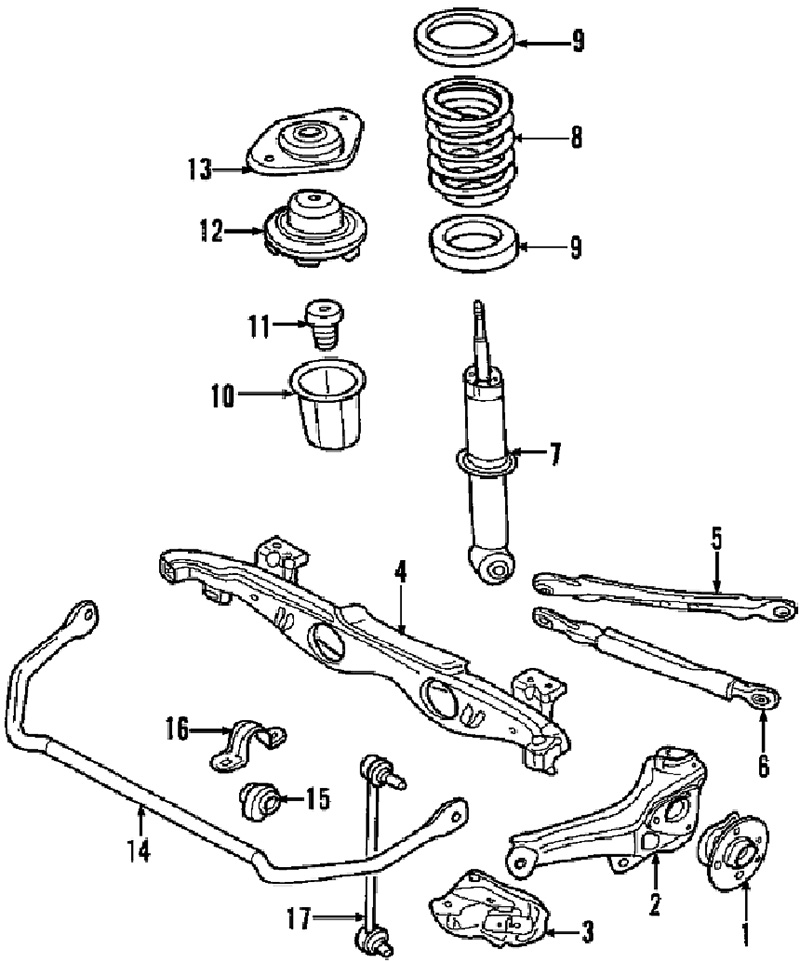
The Mini’s suspension is pretty simple and light, and the struts place the weight up high for better cornering dynamics. Note the long stabilizer bar link (courtesy BMW).
While weight distribution will change the way a car handles, it is static, and we should not make changes to weight distribution from race to race. Once in a season maybe, if a significant development occurred, but generally the car is the car. In fact, many believe that the more changes you make to a car the less reliable it may be. It is difficult for an engineer to determine how things like heat and vibration will affect newly mounted components.
So if the car is the car, how can you tailor it to the track?
Chassis preloading – often with performance coil-over-shock absorbers — will allow you to make the adjustment from road course to road course, and the one thing we must look for is adjustability! This will be the deciding factor in selecting a suspension coil-over-shock upgrade to give us the handling we seek. The key things to remember are:
- adjustable shock absorber length
- independent spring preload
- multiple adjustments for compression
- rebound dampening.
Not all coil-overs are created equal, so let’s talk about what’s out there.
An upgraded suspension will have no effect on the track width on the car — the only way we may modify that is with offset tire rims. Suspension height will have a much greater effect on lowering the center of gravity of the car, and if you are setting up a track car rather than a street car, you may not care as much about raising the ride height. The goal of our suspension tuning series, “Handling the Change, or Change the Handling,†is to remind the professional technician on the engineering goals of a race car.
Most of us will be modifying a production chassis, as it is the fastest way to get a sports car on a road course. We may cover some race chassis dimensions building techniques, but only to illustrate a point — chances are if you a building a chassis you’re probably not going to be referring to this series for advice.
The Mitigating Factor
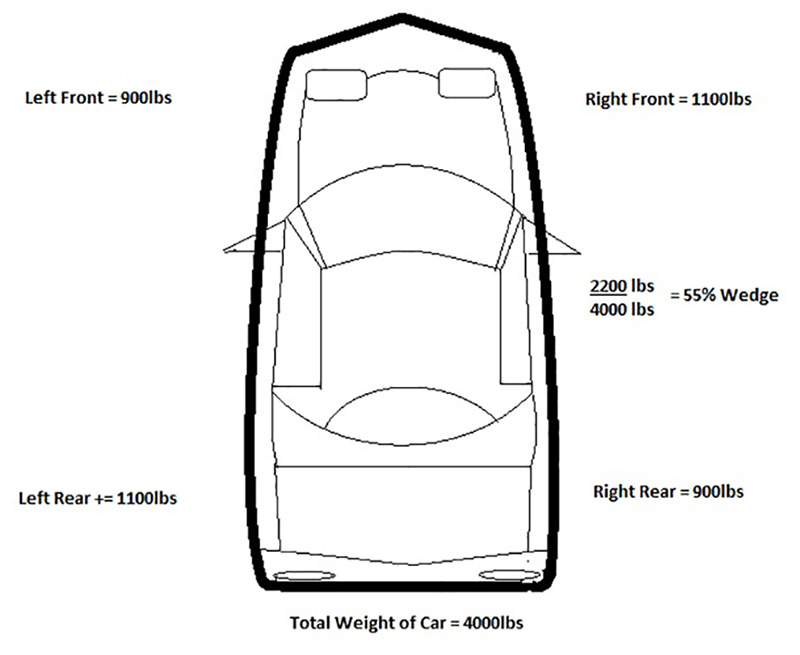
We’ve used this drawing in a previous installment of this series to illustrate “wedge.” That is, on road-race cars with over 50% cross-weight, weight bias or running a wedge will understeer or “push†in a turn, but will have good traction coming out of corners because the set-up favors the two tires that have the optimal weight on them while under high torque and high acceleration. You or your driver must decide if wedge or reverse-wedge is helping you go faster.
Adjustability is the most important factor in our decision to upgrade with performance-type coil-over-shock absorbers, and we need to understand the full purpose of a coil-over suspension. Obviously, suspension springs support the weight of the car and while the car is traveling over road irregularities – or cornering — the springs absorb the initial shock of the car hitting a bump, or absorbing weight transfer. As we know, a spring while coiled up has absorbed energy and wants to return to its normal position as soon as it can. The stiffer the spring, the stronger the reaction to being compressed and desire to return to normal length. In theory, inertia will cause a spring to expand to more than its normal size, and shock absorbers can and do offer compression dampening to assist the spring. But their main job is to control the rate of return of the spring to its normal position, and slow down that return.
The coil-over-shock absorber is a compact design that saves space and precious weight. Luckily for us, most manufacturers of the small sports cars we modify for some racing fun have migrated to the MacPherson strut, comprising a coil spring over a strut that contains the shock absorber unit. This usually makes the upgrade to more race-ready coil-overs much easier. One thing to note, though, is that a MacPherson strut design only has one pivot point for the lower control arm. Depending on the design, this may allow a significant amount of bump steer and change the camber angle as the suspension compresses.
Bump steer is the change in steering angle or toe as the suspension moves through its travel. If the steering angle changes as the suspension compresses, the driver will have to contend with subtle changes in steering as the car negotiates a bumpy turn, and it may make the front end feel unstable. Bump steer can occur on rear suspension systems, too, but can be controlled since there are no steering inputs.
Decisions . . .
This is one reason why wheel alignment adjustments are critical as we set up the suspension, but we will go into wheel alignment in more depth in future installments. For now, we’re looking to purchase and install some performance coil-overs. As we noted in the discussion of ride height, we want a coil-over that will allow us to adjust the overall height of the assembly, and we want to be able to adjust the length of the shock absorber without affecting spring tension.
You can install lowering springs instead of full coil-overs — maybe your cheapest option — but you will not have the adjustability.
There are less expensive coil-overs that do not allow adjusting the length of the shock absorber. With these units, you control ride height by moving the lower spring perches up and down, allowing ride height adjustment, but not suspension preload.
To create a fully-adjustable suspension system capable of being tuned to different tracks, make sure the shock absorber length is independently adjustable from both upper and lower spring perches. This will allow changing the spring preload at each corner of the car, or at least the front, and provide more control over corner weights. These static changes will allow tailoring handling to different situations.
Of course, coil-overs are more than just mounts for your springs. Part of the weight-saving package is the shock absorber itself. A quality coil-over will have fully adjustable compression and rebound dampening settings. Depending on how serious you are about racing, you can also purchase springs with different rates — but with spring preload being adjustable, you will probably not need to. There are differences in construction of even high-quality coil-overs.
The Detail Devil
This is probably overkill, but a dual-tube shock absorber will manage the heat generated as the shock plunges up and down hundreds of times during a lap. Most of us running in club events and track days will probably not overwork the shock absorber, since our events have short distances to cover; a mono-tube design will probably give us all the benefits without the added expense. Usually, the coil-overs will be offered with either a streetable spring that is not so stiff, or a racing spring that is much stiffer.
This may not be a problem for most tuner cars, but early-2000s Mini Coopers may be the exception. The stock vehicle does have a small problem with front strut towers flexing when the suspension bottoms out. Stiff racing type springs will put added stress on the strut towers as the car is being driven, so keep that in mind while making your purchase for your application. In our next installment we will go over compression and rebound dampening, and what they mean to us.
Â
0 Comments