Unibody repair requires thorough discovery of the extent of damage, identification of the materials that damaged components are made of, understanding of the importance that material construction has on the choice of repair procedures, and use of the appropriate tools and equipment. Read on for examples of how Mercedes-Benz repair information helps bring factory precision to the real world environment of a collision repair facility.
Unibody automobile construction is designed to manage collision energy to minimize the impact on passengers. Mercedes-Benz unibody design combines advanced high-strength steels and other materials to reinforce the safety of the central body of the vehicle, plus front and rear crush zones that are engineered to collapse in a specific way that diverts collision energy away from the passenger compartment.
This is wonderful for occupant safety, but very challenging for you as a collision repair technician. When cars were mostly mild steel, the same straightening and welding techniques worked on a wide variety of components and vehicles.
A huge variety of decisions
Advanced high-strength steels, light and strong aluminum alloys, magnesium, plastic and composites, carbon fiber and other exotic materials are challenging us to learn new repair methods and make different decisions about what can or cannot be repaired. There are application-specific components and procedures in almost every area of collision repair.
Today, some advanced high-strength steels (AHSS) are weakened by levels of heat that were fine for mild steel. Others are work-hardened beyond desirable limits simply by pulling. Minor dents in aluminum alloys can be straightened, but pulling major damage will likely result in fracturing the more brittle material, perhaps invisibly.
Structural components may contain internal reinforcements made of advanced materials that cannot be straightened, even though the outer component could. Some joints that were welded when factory-new must be adhesive bonded and riveted to minimize heat damage in a post-collision repair.
New laser welding techniques create weld bonds that go to the exact required depth in a multi-layer joint that may contain different types of metal, or different thicknesses. The precision required to weld without damaging the layers of thin, ultralight steel in a joint cannot be duplicated outside of the computerized, robotic environment of the OEM factory.
Joints that combine AHSS with aluminum, magnesium, or new composite materials require different welding or bonding methods to avoid heat damage, protect against corrosion, and maintain long-term durability. Different adhesives require specific pretreatment of the surfaces to be joined. Different materials call for special rivets that are matched to the strength requirements of the joint.
As collision repair technicians, you are faced with a huge variety of decisions for even the most routine post-accident restoration situation. Straighten or replace, section or complete component replacement, MIG weld, braze, or adhesive bond and rivet, what type of rivet? The decisions you have to make are many.
Destructive testing
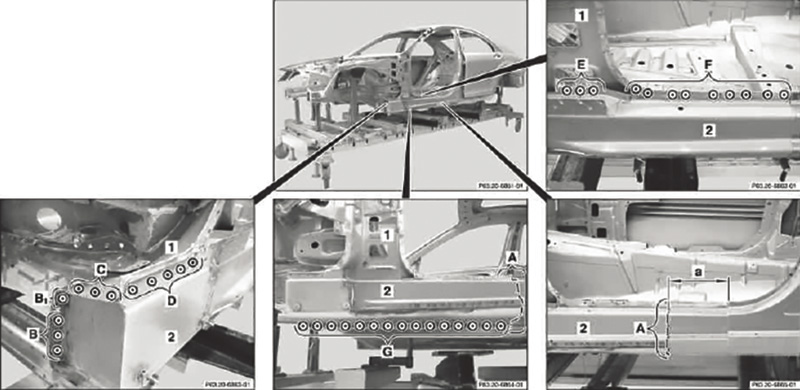
The Mercedes-Benz instructions for removing the A-pillar with side longitudinal member (rocker panel) on an S 500 4MATIC show in great detail the variety of repair methods used in one procedure. For example, cut out spot welds in areas B and B1 on outer longitudinal member (2) using a ball cutter, but in area C, use a Vario Drill spot weld removing tool, and in areas D, E, F and G use an 8×44 mm diameter BTR Usibor milling cutter.
Your best ally is information from the carmaker. Mercedes-Benz has long been a leader in the development of occupant safety and, more recently, accident avoidance technologies for its new vehicles. Because its customers love and keep their Mercedes-Benz vehicles in service far longer than the industry average, the company has also invested a lot in crash-testing and studying how to repair or rebuild the vehicle after it has been in a collision.
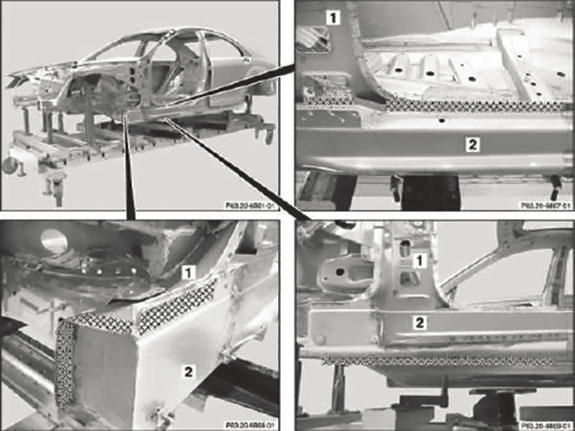
The cross-hatched areas (2) on the outer longitudinal member of an S 500 4MATIC must be loosened using a hot air gun prior to removal. Excess heat, or more destructive extraction methods would damage the adhesive bonding of underlying sheet metal in the rocker panel.
Using the findings from extensive and ongoing destructive testing, an army of Mercedes-Benz engineers, metallurgists, and technicians have developed repair-or-replace guidelines for structural and other vehicle components. They publish procedures that tell you whether to cut out just the immediate damage, cut at a factory seam, or replace an entire assembly. They recommend materials, tools, and equipment for working on Mercedes-Benz vehicles.
You can access this information via the Mercedes-Benz Workshop Information System (WIS) online database, available at StarTekInfo.com. Alternatively, your aftermarket repair information provider may partner with Mercedes-Benz to make that information available.
Replace at Factory Seam, or Sectioning?
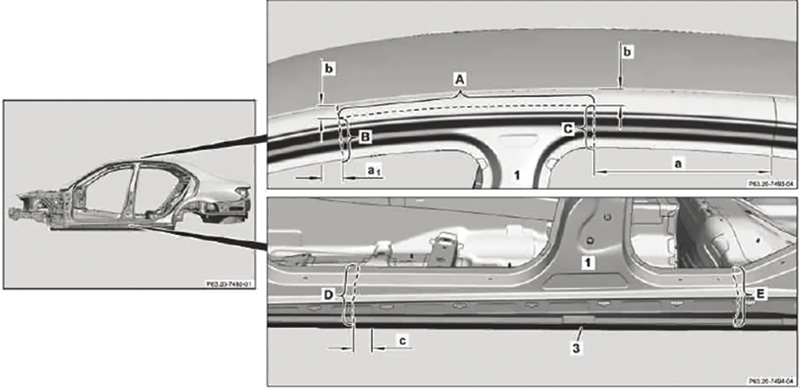
At the base of the B-pillar on an E 350 4MATIC, Mercedes-Benz allows cutting (at “Dâ€) within only an approximately 20 mm window from a notch (at “câ€) on the left side of the repair. The notch likely indicates a factory seam or the end of an internal reinforcement that, for safety in a possible future collision, should not be cut. The cut on the right side is determined by the length of the new part on that side, or by where the damage ends. At the top of the pillar, a cutting window is indicated on each side. The dimensions (approximately 265 mm at a, and 33 mm at a1), indicate areas within which you may cut without harming nearby internal reinforcements.
In sectioning, you create a cut line at a location where there was no factory seam. In part replacement, you are replacing part or all of a given component, but cutting and joining only at the factory seams. Go to WIS to see whether the component you will be working on is recommended for sectioning or for partial or complete replacement at factory seams.
For example, Mercedes-Benz allows sectioning when removing the B-pillar without the side longitudinal member, on the E 350 4MATIC. The step-by-step instructions say that the cut-points “can be determined according to the degree of damage.â€
Even when sectioning is allowed, it is often within a narrow area. The tolerance, or amount of area within which you have freedom to locate your cut can differ on one side of the repair versus the other, and from top to bottom. This is just one example of the importance of researching the Mercedes-Benz procedures and planning your repair in advance of your first cut.
Do not transfer the upper separating point on the B-pillar. The upper separating point is matched to the replacement part. Repositioning the upper separating point will damage the reinforcement for the adjustable seat belt mounting and reduce the durability of the B-pillar.
Bracketing impact damage
Impact damage travels through the unibody down load paths intentionally designed by Mercedes-Benz to divert collision energy away from passengers. These load paths differ not just from those of other vehicle makes, but due to the specific size, weight, and body materials used in a given model, are also engineered differently for many vehicle models within the Mercedes-Benz family.
Finding and correcting all current structural damage, which is mandatory in order to restore the vehicle to a crash-worthy state in case of a future collision, requires that you know the position of reference points at all four corners and in other key locations throughout the vehicle.
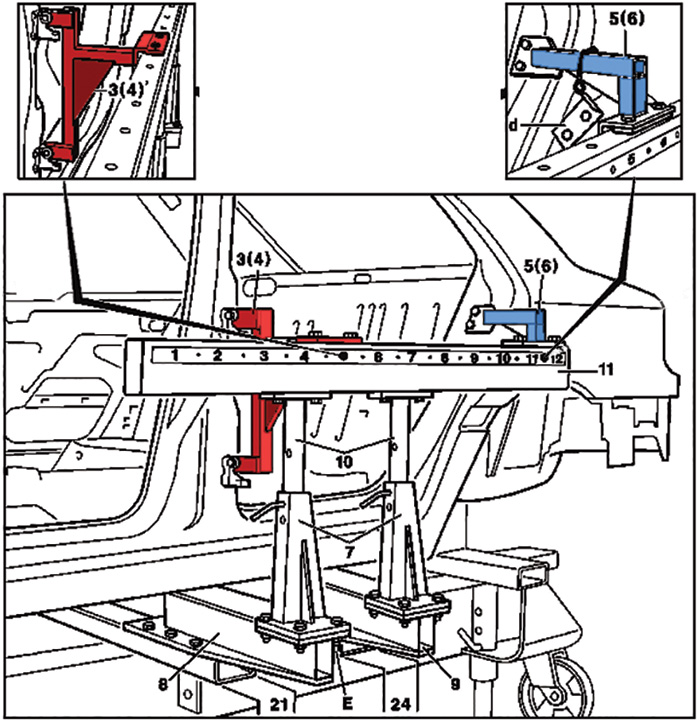
A dedicated Mercedes-Benz fixture bench provides for correct placement of the vehicle body. The above image shows modular brackets attached to the bench and to key locating points on the B and C-pillars.
A Mercedes-Benz dedicated fixture bench works with straightening brackets that attach to the bench and point to where these fixed mounting (reference) points would be on a factory-new vehicle. A collision-damaged vehicle is then mounted on the bench at points not affected by the accident. Wherever reference points on the vehicle do not match the bench bracket locations, components can be replaced or straightened to the proper placement of the body. New body parts can be located over the straightening bracket for welding in the precise, factory-engineered position. A Mercedes-Benz dedicated fixture bench eliminates concerns about measurement errors.
Lookup the Standard Service Equipment Program (SSEP) catalog on StarTekInfo.com, or contact your equipment provider for more information about the new, Extended Range Mercedes-Benz-approved dedicated fixture bench for working on commercial and long-wheelbase vehicles.
Application-specific Rivets
Adhesive bonding and riveting are recommended for joining advanced high-strength steels and aluminum panels. Mercedes-Benz has flow form rivets that compress and create a lip on both sides of the joined panels, for a stronger, more durable joint. The rivet head features the outline of the Mercedes-Benz star logo. When properly installed, the Mercedes-Benz logo remains visible on the rivet after the repair is complete.
Sealing out moisture
Sealing all bare metal with primer helps prevent corrosion, including the galvanic reaction that occurs when dissimilar metals such as steel and aluminum are joined together on an automobile. Mercedes-Benz recommends applying zinc dust paint as a weld-through primer to all bare metal, including the edges of pre-drilled rivet openings. Documentation in WIS will tell you that zinc dust paint can handle the lower heat of resistance spot welded joints, but is not for use when MIG welding, or on magnesium components.
Mercedes-Benz has developed rigorous standards for every aspect of the collision restoration process. Identifying and measuring damage, and determining what types of materials each damaged component is made of and if or how it can best be repaired, what replacement parts and procedures are approved by Mercedes-Benz, and what tools and equipment to use will make you more efficient and protect you from liability in a future mishap. All of this is made possible by having the correct information.
0 Comments