A major hybrid automobile and truck innovator just after the turn of the 20th Century, Mercedes-Benz has engineered advanced versions of the concept that are not only highly economical, but also have a big “Wow†factor.
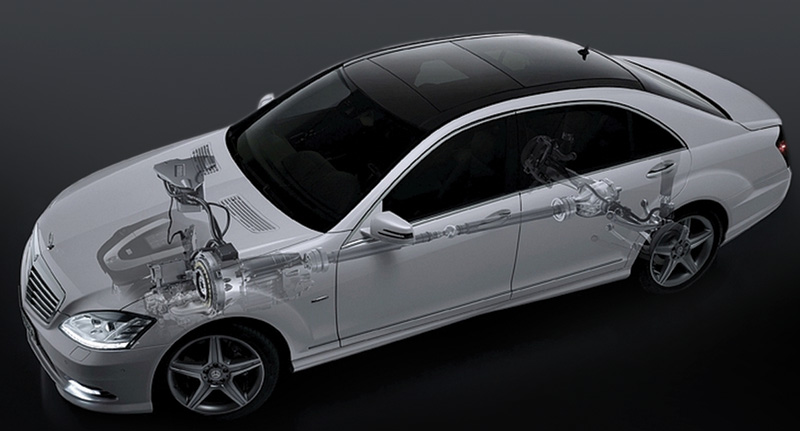
Svelte, capable Mercedes-Benz hybrids combine robust internal-combustion power with supplemental assistance from the electric motor.
Turn your clock back to those heady days near the turn of the 20th century. As we all know, Karl Benz designed and produced the first real automobile in 1886, and followed this with rapid advancements in his fledgling gasoline-powered vehicles plying the rudimentary roads of the time. Meanwhile, Gottlieb Daimler was doing much the same. Early internal-combustion engines were quite unreliable and cantankerous, however, and they were vying with more-dependable electric cars at the very beginnings of the automobile era.
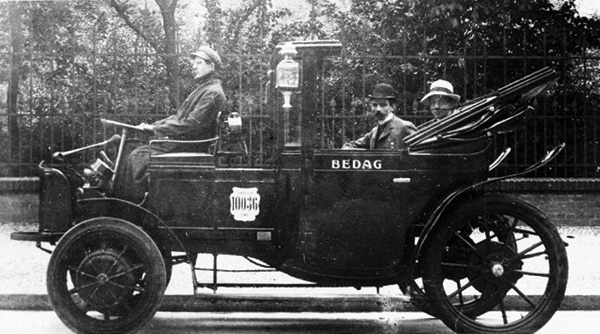
In 1907, the Austrian affiliate of Daimler-Motoren-Gesellschaft introduced the Mixte, a hybrid (Benzine over electric) that saw service mostly as taxis and work vehicles.
Seeing the potential advantages of combining the two options, Daimler-Benz developed hybrid-powered vehicles to complement its gasoline-only vehicles. The firm successfully marketed hybrid automobiles and trucks for several years as the 20th Century began, even winning road races with them. But, in Europe as in this country, steady advancements in the power and reliability of internal-combustion engines, the availability of cheap gasoline, and the avoidance of the need for periodic recharging eventually relegated both hybrids and pure electrics to the back burner, then almost completely out of sight.
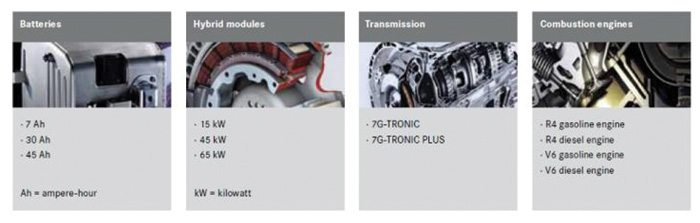
Mercedes-Benz seamlessly combines these elements so that the driver doesn’t need to take any notice that the vehicle is a hybrid.
Today, of course, the driving constraints of environmental concerns and unpredictable fuel prices have made the pursuit of motorized-vehicle efficiency one of the primary concerns of any auto manufacturer. Always in the forefront of innovation, Mercedes-Benz is addressing the needs of many of today’s motorists with hybrid vehicles offering substantial fuel economy gains combined with environmental responsibility, reliability, and enjoyable performance.
A driver can get behind the wheel of a Mercedes-Benz hybrid, start the car, and go on his or her way without a thought about it being just that: a hybrid. The company’s hybrids mesh internal combustion power with a supplemental electrical motor smoothly and virtually unnoticably to deliver highly-economical driving with strong vehicle performance. The only tipoff to the driver is the dashboard display indicating the status of the vehicle’s supplementary electrical-propulsion system.
Mercedes-Benz hybrids accomplish this with a combination of several components working in complete synergy, including:
- A conventional, though highly-sophisticated, gasoline or diesel engine
- A high-voltage lithium ion battery
- The “electric machine†– a robust electric motor inside the transmission incorporating a wet clutch
- A regenerative braking system (RBS) control unit
“Sailing†generates significant fuel economy improvement
Mercedes-Benz hybrid vehicles are renowned for their ability to reduce fuel consumption dramatically by “sailing†– cruising along with the gentle power of the electric motor to maintain speed with the conventional engine shut off when conditions are right, such as coasting on a freeway or driving downhill. In this mode, the central Engine control unit ensures that the battery charge is sufficient to utilize the electric motor, activates the wet clutch to decouple the engine, shuts the engine down by deactivating the fuel injectors, and tells the electric motor to supply power to propel the vehicle.
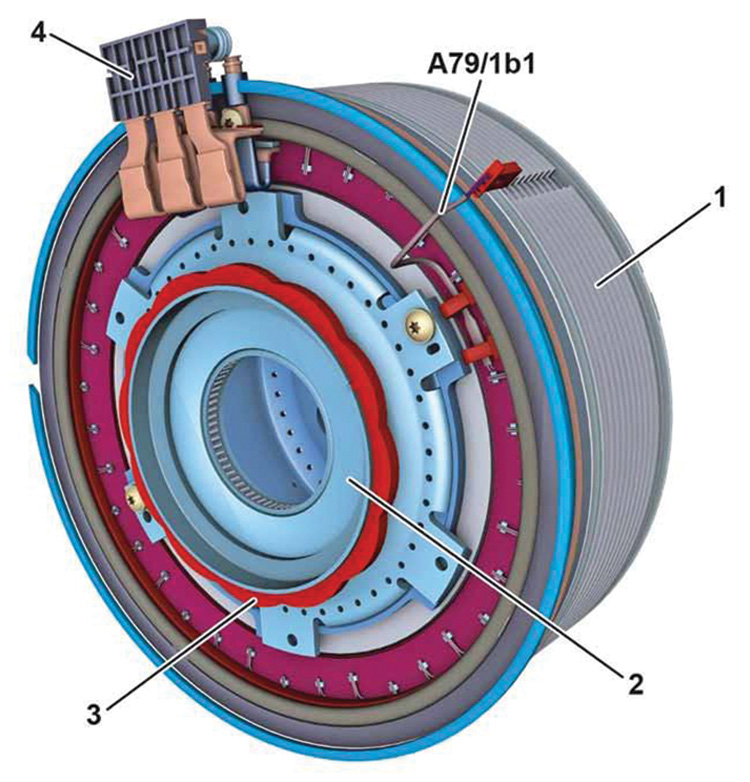
The “electric machine,†or electric motor, augments propulsion from the primary internal-combustion engine, and allows the vehicle to “sail†under the right conditions using little or even no fuel.
All Mercedes hybrids utilize 7, 30, or 45 amp batteries, 15kW, 45kW or 65kW hybrid modules, R4 or R6 gasoline or diesel engines, and 7G-TRONIC or 7G-TRONIC PLUS automatic transmissions. In operation, the systems operate in either conventional, hybrid, or all-electric modes:
- When driving solely with the conventional engine, power flows directly to the rear axle, while also driving the electric motor in its generator mode to produce AC voltage that is converted by the power electronics control unit into DC voltage and stored in the high-voltage main battery.
- When operating as a hybrid in “boost†mode, conventional engine power is supplemented by the electric motor, which is directed to generate torque to support the conventional engine, enhancing performance. The electric motor is powered by AC voltage suppled from the battery after being converted from DC voltage by the power electronic control unit.
- During braking in regenerative mode, power from the rear axle flows into the electric motor acting as a generator, and is converted to electrical energy to charge the battery. This also relieves some of the load from the service brakes.
- The system allows propulsion of the vehicle for a brief time as a pure-electric using energy stored in the battery driving the electric motor in the transmission, with internal-combustion power entirely off.
The major domo of the hybrid system
The primary manager of the hybrid system is the Engine control module, along with the power electronic control module, which determines which mode the vehicle utilizes and directs all power from the appropriate source. They are integrated and installed with a heat shield on the combustion engine.
The “electric machine,†a three-phase synchronous electric motor, is installed as part of the automatic transmission and housed in the bell housing. It utilizes electrical energy from the battery to add torque support to conventional power, operates as primary power, or generates electricity in braking regenerative mode. It also can act as the starter for the conventional engine.
When is the vehicle in conventional power mode, hybrid mode, and even all-electric? Basically, the determining factors are:
- The power request from the driver – how far down is the driver pushing the accelerator?
- What is the road surface inclination?
- What is the available high-voltage battery charge?
- What are the demands from air conditioning, power steering, 12V onboard electric system, and what are other auxiliary needs?
If the driver is going uphill with his or her foot hard into the accelerator, the air conditioning on, and electric power steering working hard to conquer a serpentine road, the conventional engine must power the vehicle to the limits of its torque capacity and, if necessary, utilize assistance from the electric motor. But if the driver is cruising on relatively level roads under mild power demands, assistance from the electric motor comes into play and can dramatically increase fuel economy by lessening the load on the conventional engine – this is when a hybrid vehicle really shines.
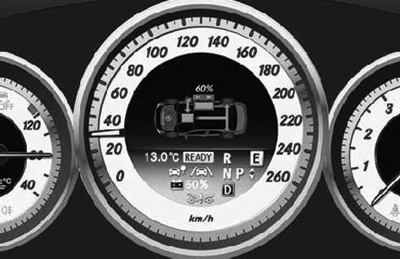
The “electric machine,†or electric motor, augments propulsion from the primary internal-combustion engine, and allows the vehicle to “sail†under the right conditions using little or even no fuel.
The hybrid is managed by the Engine control unit to designate either conventional engine power, hybrid combination of conventional engine with electric motor assistance in the ’boost’ mode — usually utilized during acceleration — or in all-electric mode with the electric motor alone powering the vehicle for a short time (when the battery has sufficient charge).
The Engine control unit manages the mode the vehicle operates in and continuously coordinates the source of energy to meet power requirements. The objective is to generate the best fuel economy with satisfactory performance, and a wet clutch is activated when appropriate to equalize the rotational speeds of the conventional engine and the electric motor.
Regenerative braking
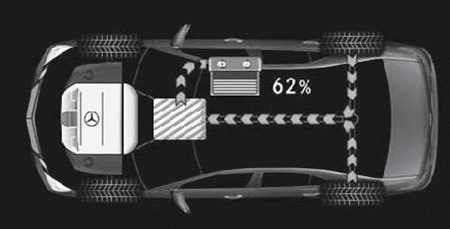
Regenerative braking utilizes the electric motor to slow the vehicle and turns the kinetic energy from the rear wheels into battery charging voltage.
A highly-important aspect of the hybrid system is regenerative braking, which helps keep the lithium-ion battery charged whenever the vehicle is braked. Run by the regenerative braking system (RBS) component of the Engine control module, the electric motor acts as a generator and actually brakes the vehicle with magnetic drag in most normal deceleration activity above six mph, unless more braking force is needed and the traditional hydraulic brakes must be actuated. The three-phase AC voltage generated by the electric motor during braking is converted to high-voltage DC energy and fed into the main battery, recharging it for future use.
In operation, the brake pedal uses part of its free travel to activate regenerative braking, with that travel growing shorter once regenerative braking is engaged — pushing the brake pedal past this actuates the traditional hydraulic brakes. Regenerative braking cannot occur below two mph, and if an automatic braking system (ABS) event occurs, regenerative braking is shut down and all deceleration is handled by the hydraulic brakes.
If the battery is fully charged, regenerative braking cannot occur, and hydraulic braking takes over entirely.
The lithium-ion battery is highly efficient, but needs temperature control
The lithium-ion main storage battery, crucial to the success of the hybrid concept, is charged by regenerated braking forces and by the conventional engine. It provides 33% more storage and 50% greater power/weight than a conventional lead-acid battery. Controlled by the high-voltage battery module, this highly-efficient battery powers the electric motor to provide torque to supplement the conventional engine, or even operates as solely-electric power for short periods of time.
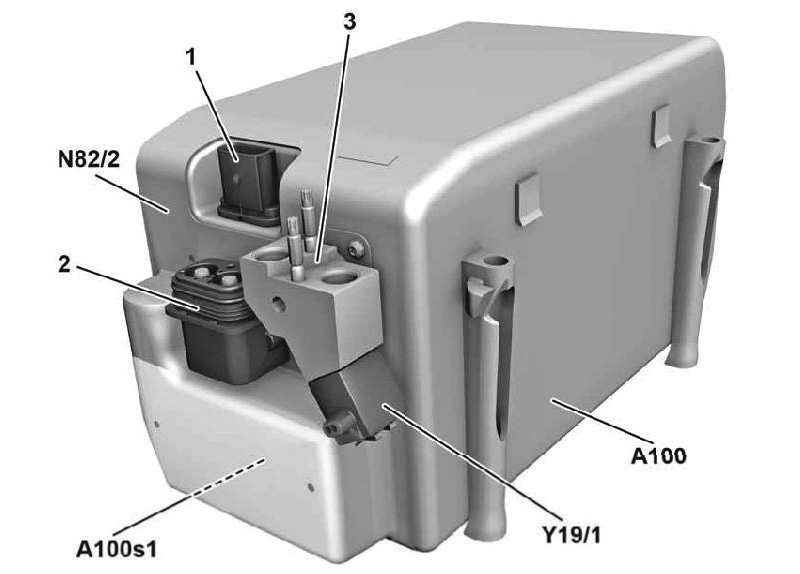
The high-voltage lithium-ion battery provides the power to the electric motor to boost internal combustion engine performance, or can function alone to power the vehicle for limited driving.
Highly temperature-sensitive, this battery should be maintained at 50% to 75% optimum charge to deliver greatest output, dependability, and long life. The vehicle’s battery maintenance system (BMS) control unit monitors battery temperature, and if cooling is needed transmits this information to the Engine control unit and then to the electric refrigerant compressor to maintain optimum battery temperature.
If the vehicle sits unused for a lengthy period, exhaustive discharge can damage the high-voltage battery. It is best to operate the vehicle for a few minutes at least every four weeks with all unnecessary electrical units turned off to charge the battery. If the battery is discharged and does not provide power to start the car, the vehicle should be jump started.
The high-voltage battery should be charged in the “charging while stationary†mode, and battery chargers should not be connected to the high-voltage battery for personal safety and to avoid damaging the vehicle’s high-voltage electrical system. Charge the battery to at least 60% if it has been discharged significantly.
Electric motor and special automatic transmission make the vehicle a hybrid
The “electric machine,†or electric motor, turns the otherwise-conventional sedan into a hybrid. Housed in the automatic transmission bell housing, the motor is a three-phase synchronous unit excited by a permanent magnet and is connected to the wet clutch, and, through the clutch, connected to the combustion engine. The motor:
- Works in boost mode to supplement the combustion engine.
- Provides power to actually propel the vehicle by itself for about 15 miles if acting alone and the combustion engine is shut down.
- Operates in generating mode to provide electricity to charge the battery, either regenerated from braking, or generated by the internal combustion engine when it is powering the vehicle.
- Acts as a starter for the internal combustion engine.
Switching between electric power mode and generator mode is handled by the power electronics control unit, and when the power mode is selected utilizes a rotational movement with actuation of the wet clutch to engage the internal combustion engine and either help drive the vehicle, or start the engine.
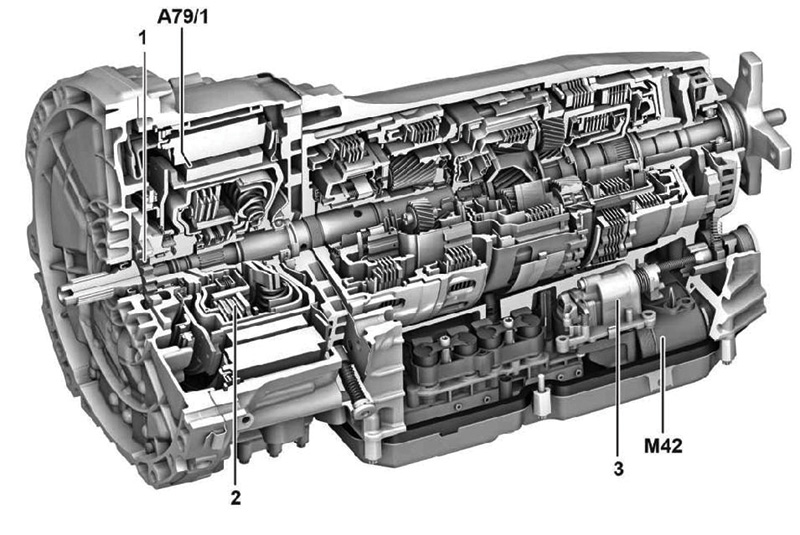
The special automatic transmission adapted for hybrids houses the electric motor and wet clutch in the bell housing, ready to take electric power to the road.
If the electric motor is capable due to sufficient battery charge to either power the vehicle by itself or to restart the engine, the engine is shut down with an automatic stop by switching off the fuel injectors without turning off the ignition while the transmission is either in “D†or “N.†The electric transmission oil pump is immediately activated when the engine is shut down.
When the electric motor can no longer solely provide propulsion, the CDI unit calls for an automatic engine start, actuates the wet clutch to connect the engine to the transmission, then actuates either the vehicle starter or the electric motor to start the engine. If the vehicle is already in driving operation, the starter is utilized to crank the combustion engine – the electric motor can only start the vehicle when it is at a standstill, with the hood closed.
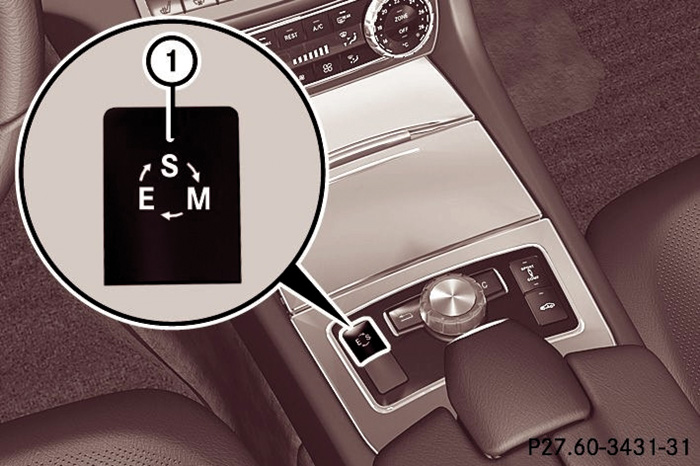
Select “E†for economical driving, utilizing electric drive whenever possible. Want sport? Select “S†for sporty driving with boost mode. Choose “M†for manual gear selection, strictly for internal combustion engine driving.
Rather than having the electric motor installed as a separate component, it is integral with the automatic transmission, where it engages the wet clutch to provide motive power when called on. The 7G-TRONIC seven-speed transmission is specially adapted to hybrid drive, and, in addition to the electric motor, houses the wet clutch and an electric transmission oil pump to provide the necessary oil pressure for transmission lubrication when the combustion engine is shut off and the vehicle is in electric drive mode.
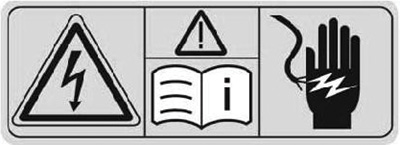
Help prevent a potentially fatal accident or damage to your health by avoiding all wiring and components labeled with a graphic warning sticker.
As we noted at the beginning of this article, all these actions are virtually seamless with nothing required of the driver, and normally occur without the driver even noticing – except when he or she realizes this Mercedes-Benz is providing perhaps 40 mpg on the open road.
High-voltage training for service, or you could be a fatality
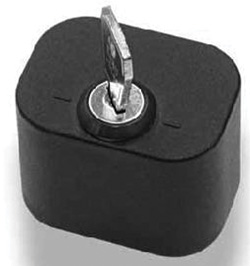
Once the electrical system has been deenergized, a special lock must be inserted and secured before any service can be conducted to avoid accidental re-energizing.
Technicians should only service hybrid vehicles with specific, appropriate training – there’s dangerously high voltage under the hood, and Mercedes-Benz requires that personnel performing diagnosis on hybrids must have completed a special qualifying course. Voltages greater than 60 volts DC and 30 volts AC are present on components of the on-board electrical systems, and touching these components can cause burns, spasms, damaged blood cells, or death.
NOTE: Please read the article in the Spring 2015 issue of StarTuned® online for a more complete discussion of hybrid service safety.
All electrical lines carrying high voltage are identified by an orange warning color and carry a graphic high voltage warning sticker. Anyone wearing electronic implants such as heart pacemakers should not work on high-voltage on-board electrical systems.
The high-voltage electrical system must be de-energized and protected against re-activation before any service operations involving high-voltage components can be performed on hybrid vehicles. The system is de-energized by disconnecting the positive and negative high-voltage battery terminals from the high-voltage on-board electrical system by unscrewing the plug connection on the high-voltage battery module and replacing it with a high-voltage activation lock. This prevents accidental reactivation of the electrical system and safeguards the health and survival of technicians servicing the vehicle.Â
Ready for 1200 miles on 20 gallons?What kind of mileage can a Mercedes-Benz hybrid driver expect? In extended highway driving, 35-45 mpg is fairly normal, less for stop and go. But what about a really long trip? British journalist Andrew Frankel recently drove with a co-driver in a Mercedes E 300 BlueTEC Hybrid equipped with a 21 gallon (80 liters) fuel tank from Tangier in Morocco, crossed through Spain and France and reached their destination in Goodwood in England after driving 1222 miles (1968 kilometers) for 27 hours – on one tank of fuel, which is about 60 mpg. After reaching his destination Frankel reported that the fuel gauge showed enough fuel left over for another 90-100 miles, which puts the potential range of this hybrid vehicle about 1300 miles on a 20 gallon tank of fuel. At this rate, one could drive from New York to Miami, about 1280 miles, in a Mercedes-Benz hybrid with a 20 gallon fuel tank without stopping for fuel – and have fuel left over. |
Â
0 Comments