An in-depth understanding of fluid mechanics requires a background in mathematics and physics that most of us have either never had or have forgotten over time. The “languages†of science and engineering, math and physics, like a spoken language, fade without constant use and practice. This fact does not mean that common sense and mechanical aptitude can’t make this complex topic understandable. Before we take a quick look at some of the fluid and air flow characteristics that we use to mix fuel and air together in our carburetor, let’s go over a few basic definitions so we’re all on the same page.
States or Phases
Matter exists in three major phases or states: as a gas, a liquid, or a solid. There ARE other states of matter like plasmas and mesophases (intermediate phases between the major phases — think Jello, for example) that are useful to us at times, and to be absolutely thorough in this discussion, there are even complex lab-induced phases like Bose-Einstein condensates; very specific, low-temperature, low-density states used by the long-haired lab types to study experimental and fundamental physics and quantum mechanics. For us, our focus is on solid, liquid, and gas, with an occasional foray into plasmas and mesophases.
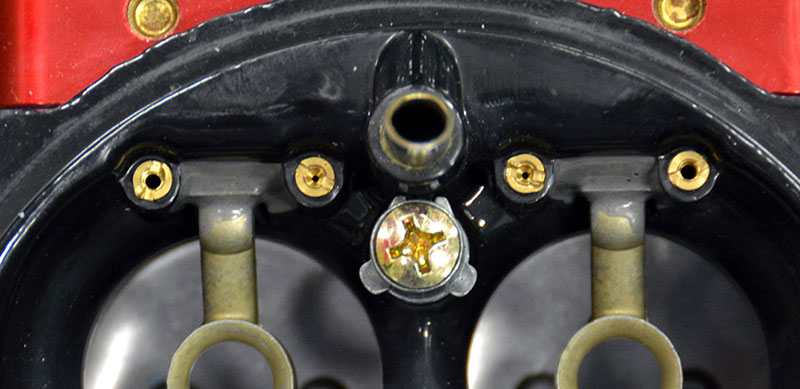
Fluids, Liquids, Gases and Solids
A fluid is defined as a substance that is capable of flow and changes shape at a constant rate when acted on by an external force, a substance that cannot resist an applied shear force. A fluid can be either a liquid or a gas. Our little fuel mixer is a fluid handler in every sense of the word.
Gases are compressible, and as they are compressed their volume decreases, pressure increases, and temperature increases as the act of compression occurs. Air is a mixture of gases including nitrogen, oxygen, and water along with several trace gases.
Temperature is a reflection of molecular movement or energy, and as you shrink the volume of a gas you concentrate the energy contained in the original volume so there is a natural, temporary temperature rise caused by the concentrating effect of compression. Also, because compressing a gas requires energy, you see that added energy as an additional increase in temperature over and above the rise attributable to volume reduction. The heat of compression can be useful; for example, we use it to vaporize fuel in the cylinder of an engine.
Once the action of compression is complete, the increased temperature of the compressed volume will normalize slowly with ambient temperature and the pressure inside the vessel will reflect this by dropping slightly as the compressed volume cools. We sometimes use artificial means to cool compressed gas volumes, using devices like intercoolers on turbocharged or supercharged cars, or air compressors because extracting the heat of compression increases the density of the compressed output improving an air compressors’ efficiency, or because cooling the incoming air on a supercharged engine improves charge density resulting in more oxygen per cubic foot to react with the fuel.
Liquids are non-compressible. A liquid will only compress roughly ½ of 1% by volume. We mechanics know this because we use the non-compressibility of a liquid to control brakes, power steering, and automatic transmission operation. It’s the same non-compressibility that allows engine oil to act like a solid when it’s in the confines of the bearing clearance, or a hydraulic lifter. Nothing we do inside an engine will work without knowing or utilizing the compressibility of a gas or the incompressibility of a liquid.
Elements, Compounds, Mixtures and Emulsions
An element is a pure substance that cannot be chemically broken down into any simpler form. Each element is a primary constituent of all known matter, either in its pure state or in combination with other elements.
A mixture consists of two or more elements or compounds that are combined, but retain their distinct chemical identities. They come in two forms, heterogeneous (not uniform when sampled — a load of gravel mix, for example) and homogeneous (uniform when sampled and consistent in phase and composition throughout the sample — like air). Examples of mixtures would be a mixture of flour and sugar, sugar and water, or smoke, which is a mixture of solids and gases.
A compound is a mixture of any two or more elements that are chemically joined so that they cannot be separated by mechanical means, and good examples of this abound in our choice of fuels for our cars — gasoline, which is both a mixture and a compound in that it is uniform when sampled, but contains a number of different compounds made up of carbon and hydrogen. Other fuels like methanol are made up of carbon, hydrogen, and oxygen (CH3OH). Or, nitromethane, chemical formula CH3NO2, a compound containing carbon, hydrogen, nitrogen, and oxygen.
An emulsion is a combination of two fluids neither of which is soluble into the other. It’s formed by creating a fine dispersion of one fluid into the other, like the emulsion formed by oil and vinegar in a salad dressing.
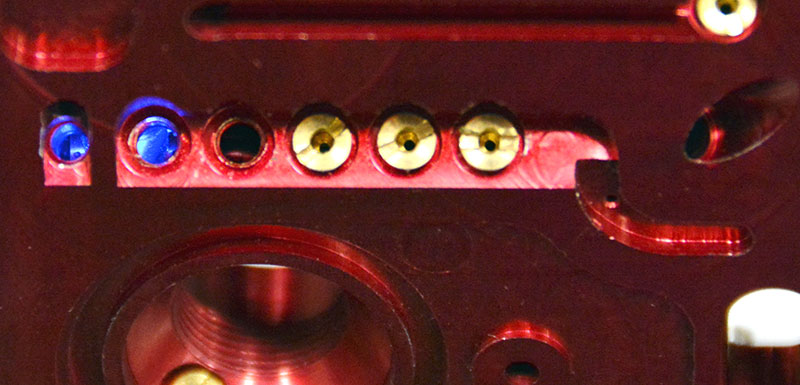
Application to Carb Circuits
In our next installment, we will start looking at the three main circuits of the Holley and as this discussion begins we need to have a good understanding of the air bleed and emulsion system.
There are two-circuit and three-circuit air bleed and emulsion systems, with the two-circuit used on the smaller main venturi systems and the three-circuit used on the larger-bodied carbs such as the 4500 Dominator series.
As we’ve previously defined it, an emulsion is a mixture of two fluids that aren’t soluble into the other, so they are only mixed temporarily, typically by some mechanical means of blending. Once the agitation stops, the emulsion falls apart.
Why do we need them? An increasing vacuum signal across a fixed orifice pulls an ever increasing amount of liquid through it and that quantity of fluid pulled isn’t directly proportional to the pressure differential across the orifice; the fuel curve tips upward as the pressure across the jet increases.
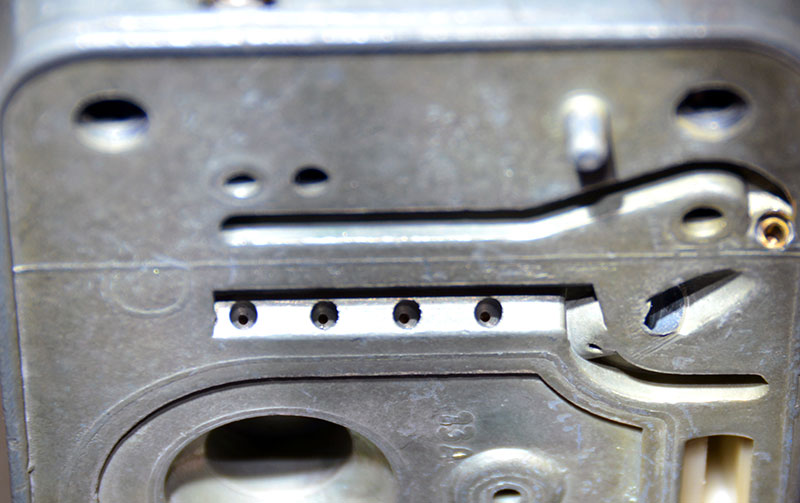
To combat this, we use an emulsion system to introduce air into the fuel, creating a froth or foamy mix, the volume of which changes as the amount of fuel in the main well system changes. The float level sets the main well level and that level sets the spill height, and we trim the mixture by introducing air into the fuel through the emulsion channels, adding more air as the fuel level in the main well falls due to the restriction of the jets, which uncovers more emulsion bleed points and tips the fuel curve downward creating a more linear fuel delivery rate across the entire operating range of the engine.
The emulsion system also acts to “pre-condition†the fuel, creating an air-fuel mix that is better prepared to vaporize since it’s already pre-mixed, and is readily ripped into finer droplets as it’s drawn into the low pressure flow created by the boost nozzles.
There are two points of calibration in the emulsion system: the air bleed in the air horn and the size and number of holes feeding the emulsion channel. The air bleeds are dual-purpose, trimming the fuel curve and serving as siphon breaks at shut down. Without them, fuel will siphon over until the bowl empties.
Some racers like to trim the air bleed to correct the mixture, but I’m not a fan. First of all, the old rule of thumb is .001 in. of bleed change results in the same correction as .002 in. of jet change isn’t necessarily correct. Second, because the air bleed change “bends†the air fuel curve, it may go richer or more lean than you’d like at some point in the operating range. You can change the air bleeds temporarily to see if you need to add fuel, but then you need to make the appropriate jet, power valve channel restrictor, idle or transfer fuel restrictor changes on the fuel side and go back to your original air bleed size to keep the fuel curve linear.
Stay tuned… more to follow
0 Comments