EVAP emissions sources are tricky to find. Here are a few tips to try before connecting that smoke machine.
Vehicle-related environmental regulations focus on reducing three types of harmful emissions: unburned hydrocarbons (HC), carbon monoxide (CO) and oxides of nitrogen (NO2, or NOx). Mercedes-Benz engineers have brought powerful new technologies to the fight, including more efficient combustion chambers, low-friction engine components, higher-precision ignition timing, direct fuel injection systems, variable valve timing, and closer engine tolerances.
In addition to those new technologies that make engines more efficient, key systems directly reduce the targeted harmful emission categories. CO emissions are limited by the positive crankcase ventilation (PCV) system, the secondary air injection (SAI) system, and the catalytic converter. NOx emissions are reduced by the exhaust gas recirculation (EGR) system and the catalytic converter. For HC emissions, the first line of defense is the evaporative emissions system, with additional help from the PCV, secondary air, and catalytic converter (aftertreatment) systems.
Leaks are by far the leading cause of EVAP system trouble codes being set. However, seeing a leak-related trouble code and solving an EVAP system problem can be two very different things. Diagnosis can be complicated by the fact that some leak trouble codes can be caused by problems other than a cracked hose or leaking fitting. In a system with only one psi of pressure, finding the typical small leak can be time-consuming at best. Key system components may be hidden from easy visual inspection. Even when you can see the relevant valves, lines and fittings, the leak opening is often too small for the unaided eye to see. An EVAP smoke machine is essential.
What appears to be a leak may actually be a stuck valve not allowing vacuum to flow where and when it should, or an electrical problem preventing a component from responding appropriately to actuation commands from the PCM (Powertrain Control Module, SAE’s term, but you may be used to ME for Motor Electronics). A small leak will eventually become a large leak that can come back to bite you, so despite the diagnostic headaches, you have to find and repair it.
Reach first for your scan tool
Even with a Mercedes-Benz-approved EVAP smoke machine, the process of moving things around may alter the conditions that caused a trouble code to set, making it difficult to verify and repair the original problem. For ex-ample, it could shake loose the piece of debris that was causing a valve to stick open, push a vacuum hose back on its fitting, and, in essence, tem-porarily eliminate the problem that caused the customer’s complaint.
Before setting up the smoke machine or checking to make sure the gas cap is tightly closed, conduct an EVAP leak test using the Mercedes-Benz XENTRY or previous Star Diagnosis tool. Because you connect under the dash, you won’t likely have altered one or more of the conditions that could be a primary leak source. Also, if the vehicle fails the leak test, you’ll have verified that the fault code is not due to an intermittent problem or ME control unit issue.
Mercedes-Benz structures its test to look for three leak levels: gross leak (equal to or greater than 3 mm in diameter), fine (equal to or greater than 1 mm), and very fine leak (equal to or greater than 0.5 mm diameter). It tests first for the largest leak first, and works its way down.
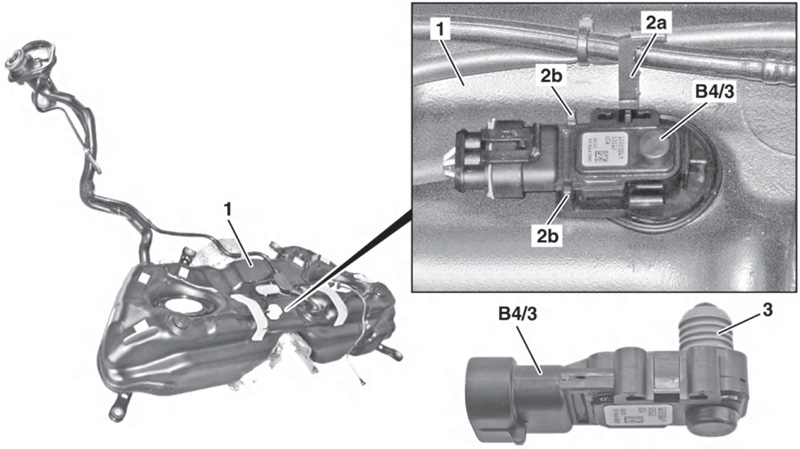
The fuel tank pressure sensor seal (3) could be deteriorated, or the sensor (B4/3) may have become stuck, and is sending a false positive signal to the ME control unit. Take care to not turn or tilt it when removing the faulty FTP sensor, as this may damage the locking tab (2b), which is needed to secure the replacement sensor.
Using your Mercedes-Benz scan tool or an aftermarket substitute hooked up to the diagnostic connector under the dash, close the vent solenoid and open the purge valve. Vacuum should reach approximately -6 mbar within 12 seconds in the fuel tank on a typical E350. See your Mercedes-Benz service information for fuel tank test and adjustment values for the vehicle you are working on. If no vacuum builds up in the fuel tank, there is a major leak. A trouble code will set, the warning light will flash in the instrument cluster, and the message “Check Filler Cap†will appear in the multifunction display.
No matter what the reason you are performing the purge cycle test, if there’s a leak of more than 3 mm, you will likely hear a loud hiss. If you can hear it, but the ME control unit does not see the leak and set a trouble code, replace the fuel tank pressure (FTP) sensor. The FTP sensor is likely stuck in a manner that sends a good (plausible) signal despite the leak.
If there is no large leak, proceed to check for a fine (1 mm) leak. Close the vent solenoid and open the purge valve long enough to build up approximately -6 mbar of vacuum in the fuel tank, then seal the purge solenoid. With the EVAP system sealed, measure the vacuum level for 30 seconds. If vacuum falls more than 0.3 to 0.5 mbar per second over a 30-second period, there is a fine leak, and the ME control unit will set a code. Note that this specification is dependent upon the fuel level in the tank, and will be taken into account by the ME control unit pass/fail algorithm as necessary.
If no fine leak is found, purging restarts until a vacuum of -6 mbar is built up again. Close the purge solenoid (the vent solenoid also remains closed), and watch for vacuum decay. If vacuum drops faster than 0.10 to 0.15 mbar per second (again, depending on fuel level), there is a very fine (micro) leak. Note that the ME control unit measures fuel outgassing shortly before checking the FTP sensor, and takes any outgassing into account for fault determination.
The Purge Solenoid
When the vehicle is being driven and certain conditions (speed, engine temperature, and others) are met, the ME control unit opens the purge valve to apply vacuum and pull measured amounts of fuel vapor from the EVAP canister into the engine to be burned.
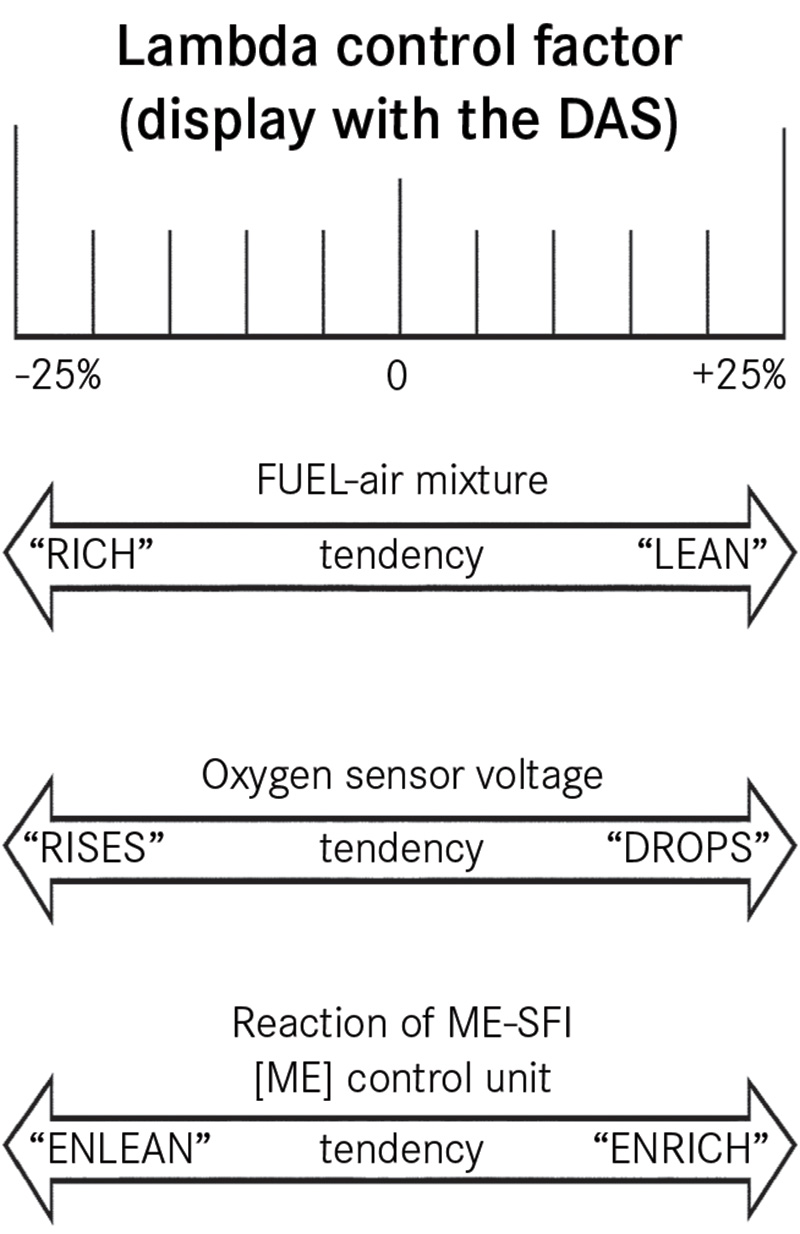
A faulty FTP sensor or defective purge valve can cause the air/fuel mixture to become too rich or lean, depending on fuel level and engine speed, and require excess adjustment from the ME control unit in order to keep the engine running efficiently.
If the purge solenoid is stuck open, it is applying vacuum to the EVAP system whenever the engine is running, regardless of conditions. If the EVAP canister was saturated with gasoline vapor, the fuel trim adjustment has to play catch-up with the rich condition caused by those extra fuel vapors being dumped into the engine. Once all of the fuel vapors have been drawn out of the EVAP canister, we are then drawing fresh air through the open vent solenoid and into the engine, causing an undesired lean condition. Either way, a stuck open purge solenoid is considered by the ME control unit to be a gross leak, and sets a code.
Under normal conditions during the canister purge cycle, the FTP sensor should see vacuum in the line in order for fuel vapors to be drawn from the EVAP canister into the engine. If the sensor registers no or inadequate vacuum in the purge line after the purge solenoid is commanded open by the PCM, a fault code is set.
The lack of vacuum could have a long list of potential causes. These include an inoperative or clogged purge or vent solenoid, clogged or disconnected purge line, cracked or damaged EVAP canister, misrouted vacuum hose, rusted filler neck, open or short in the purge valve wiring, faulty purge valve, or a failing fuel tank pressure sensor.
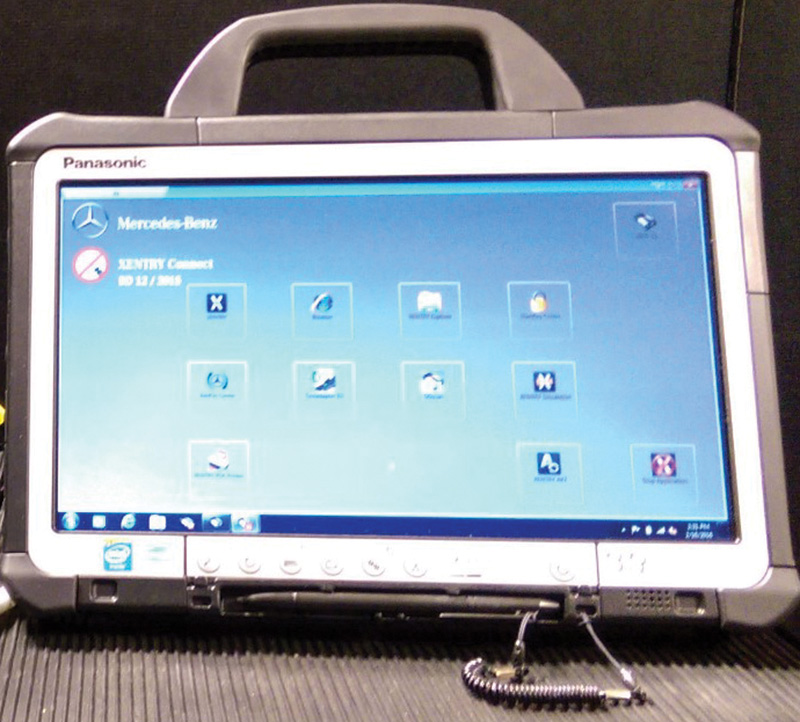
With XENTRY you can read current configurations of various systems on Mercedes-Benz vehicles, access and troubleshoot any system or control module, stream real-time sensor data, conduct sensor actuation and testing, read and clear fault codes, and perform online or offline initialization and coding of sensors and modules.
On many Mercedes-Benz models featuring the 272.9 series engine (and others), the purge solenoid is normally closed, and is actuated by the ME control unit. Using a pulse-width-modulated (PWM) signal, the ME control unit provides precise purge volume by varying the frequency and duration of purge solenoid open times. If vacuum is found when there is no command from the ME control unit to open the purge solenoid, the valve may be stuck open. Rust, particles from deteriorated seals, or other debris can enter the purge solenoid valve and prevent it from closing completely.
The EVAP Vent Solenoid
A P0449 code means that the ME control unit has detected a fault with the circuit that controls the EVAP system vent solenoid. The cause could be a short to power, short to ground, an open, a failure of communication between the ME control unit and the solenoid, blockage of the valve or line to it, or less likely with a P0449 code, a faulty valve.
Two wires service the vent solenoid. One supplies voltage from the fuse or junction box, and the other carries the ground commands from the ME control unit to activate or deactivate the vent solenoid (by controlling when the circuit is grounded). Do a voltage drop test between the fuse and the wiring connector at the valve to make sure that the solenoid is receiving enough current (12V) to actuate opening and closing.
To check if the EVAP vent valve is receiving open and close commands from the ME control unit, actuate the solenoid using your scan tool. Close the vent. If the solenoid is working and receiving commands from the ME control unit, you should hear a “click†when it closes. If the vent valve does not open or close when commanded, check for power and ground in the wiring connector at the solenoid.
With the vent solenoid closed, open the purge valve and let vacuum build in the tank for 6-8 seconds, then watch for vacuum decay. If the tank holds vacuum for at least 30 seconds, open the vent solenoid and close the purge valve. Fuel tank pressure should rise and stabilize at a level pre-set by the ME control unit.
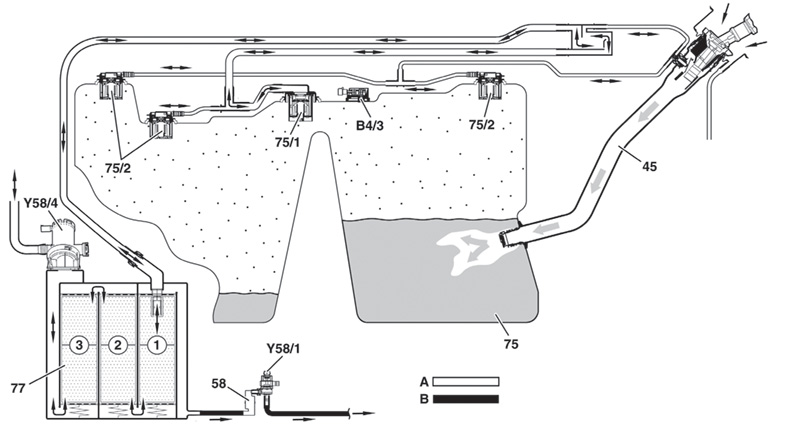
The EVAP vent line includes many potential leak points, including the charcoal canister (77), canister shutoff valve (Y58/4), purge valve (Y58/1), fueling, limiting and vent valve (75/1), breather valve (75/2), FTP sensor (B4/3), various lines and hoses, fuel filler neck (45), and the fuel tank itself (75). On this typical E350, the vent line (A) is shown clear, and the purge line (B) is solid black.
Check potential fuel cap issues
A gross leak code such as P0455 may not automatically be a sign that there is a problem with the fuel cap. If vacuum does not build up in the fuel tank when the purge valve opens, the computer simply sees a lack of vacuum and sets a leak code. It does not always set a more specific code that tells you whether other conditions, such as a stuck purge solenoid, are causing the lack of vacuum. You can do the detective work by using your enhanced scan tool to actuate various EVAP system components and watch the responses from the fuel tank pressure (FTP) sensor.
Of course, check that the fuel cap is tightly screwed into the filler neck. If not, tighten cap, delete the code and re-check for EVAP system leak tightness.
Inspect the fuel filler neck. Is there excessive rust allowing leaks through the neck, or preventing a good seal with the cap?
Is a leak actually occurring?
As already mentioned, it pays to check first using the best scan tool you have available, preferably. Once you verify there is a leak, you can switch to the Mercedes-Benz-approved EVAP smoke machine to quickly find it. The approved smoke machine features low-pressure test procedures, so it does not alter or harm components in the vehicle EVAP system. That combined with the procedures outlined above will guarantee the accuracy of your diagnosis.
Download PDF 〉
0 Comments