What to do when the pistons “just ain’t fitting 
Everyone knows that Porsche engines are built to a very high level of precision. Factory engineers go to great lengths to specify materials, parts configurations, compatibility, and precise specifications in order to achieve the performance and durability expected from these cars.
This is especially important when faced with the task of rebuilding one of these engines when overhaul is needed, and even more so when the vehicle is one of the very high performance twin turbocharged powerplants like that found in the limited-production 993 models.
Building an engine back to factory specifications is relatively easy because much of the thinking has been done for you. You need only to look up the specifications, measure the parts and assemble things carefully. There are significantly more complications that can arise if you are using high performance aftermarket components.
True enough, in many cases some of these are better and stronger than what the factory delivered but they don’t always play well with all the other components that were engineered from the factory. Connecting rod interference with engine case internals, different bearing clearances, and concern about piston-to-valve clearances are just a few examples of non-stock parts that need to be checked during assembly.
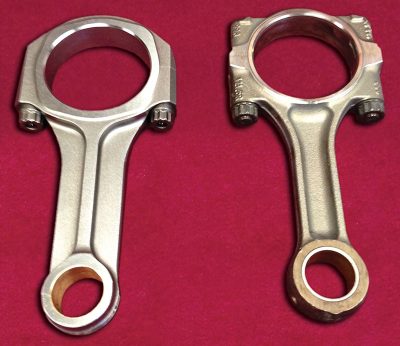
It is the engine builder’s task to assure that all the parts are going to work in concert with each other and nothing bad happens when the key is turned. It is not uncommon for an engine build to be put on hold if additional machining becomes necessary or a different part needs to be sourced. This becomes just a normal part of the process.
The choice of high-quality replacement parts is critical. But, in the end, the responsibility for the finished engine lies with the engine builder. Not the machine shop. Not the parts manufacturer. The engine builder.
It is up to the engine builder to examine, measure fit, check and re-check clearances and other critical specifications to assure that they are correct. In some cases, replacement parts may differ from the OE components, in design, construction, dimensions, or materials. In such cases it is incumbent on the engine builder to know the complete nature of the parts being installed, and to assemble the engine accordingly.
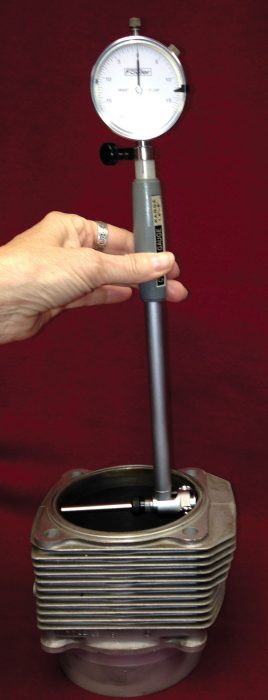
In the case of Porsche engine overhauls, it is common to purchase pistons, rings, and cylinder liners as a package. Doing so will assure complete compatibility of the various parts. Even so, it is up to the engine builder to measure and confirm all clearances and other specifications since the final product is on him (you….).
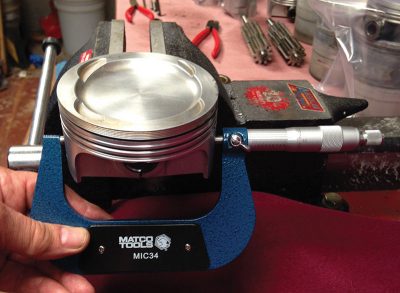
Some replacement pistons may be made of a different material from those used when the engine was first assembled. In such cases, coefficients of thermal expansion may be different from the OE pistons, the liners may have different metallurgy and, for these and other reasons, dimensions and operating clearances may differ from those specified in the OE service manuals. You may find the need for different piston ring end gaps and side clearances, the ovality of the new pistons may be different from OE pistons, and piston-to-bore clearances may be different from the factory specifications.
It is important to buy replacement parts that you’re familiar with and have confidence in. Depending on the supplier you use, for example, you may find replacement pistons, rings, and cylinder liners packaged separately. Or you may find that the rings are pre-fitted to the pistons, and the pistons are packaged with their respective liners. This is certainly the preferred method, since it implies that the rings are a proper fit to the pistons, have the correct depth and side clearances, and are sized to the cylinder liner they’re packaged with. This includes having appropriate piston ring end gap within the cylinder. It is still the responsibility of the engine builder to double-check all of these critical dimensions, but having them pre-matched certainly inspires confidence that the clearances will be correct.
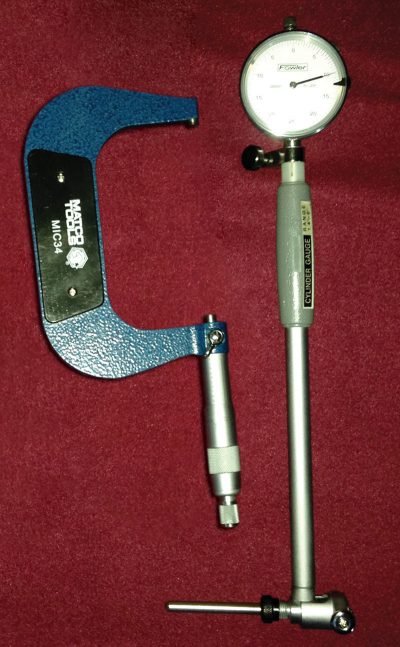
Being familiar with an engine family is surely a plus, but it can also lead to complacency. Consider this scenario. You know from experience that the factory spec for piston-to-bore clearance for factory pistons in the Porsche engine family is 0.004. Yet when double-checking pistons and liners in hand, you find clearance of just 0.0015. And the mystery deepens when you find exactly the same clearance on all six pistons and their cylinders.
Double-checking your service data, you re-confirm that 0.004 is indeed the factory spec. So why would new pistons and liners have much tighter clearances, that are consistent across the board?
The answer lies in the construction of the pistons.
Pistons for these engines may be cast, forged, or hypereutectic. Now we all know what cast and forged pistons are. And we know that they can have different rates of thermal expansion. So assembly clearances may vary depending on the construction and metallurgy of the pistons.
Forged pistons are the most expensive option when building an engine due to material and machining costs. A forged piston starts life as a billet which has been subjected to extreme pressure giving the material higher ductile strength, allowing it to handle the loads from high compression and RPMs. Far more machining is required, however, because a billet’s shape is much different from the end product when compared to a casting. A lot more material winds up on the floor in the form of aluminum chips in the manufacture of forged pistons.
Cast pistons, on the other hand, are much cheaper to make. Molten alloy is poured into a mold that rather closely resembles the end product. Less machining is required than that of its billet forged counterpart. The ductility is lower due to the fact that they were not formed under pressure and the alloy is not as dense, so cast pistons just aren’t as strong.
However a third alternative is hypereutectic pistons, and these pistons typically require clearances that are much different from those for cast or forged pistons.
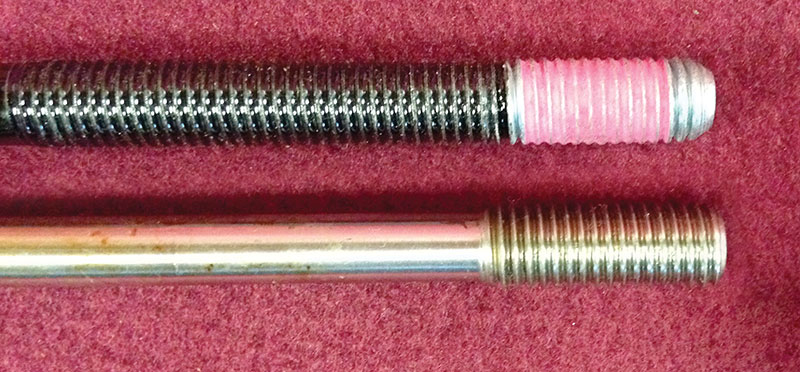
With hypereutectic pistons, silicon is added to aluminum alloy to help with scuffing and to control thermal expansion. The word eutectic refers to the proportion of silicon in the aluminum alloy that makes up a piston. When silicon is added to aluminum in its molten state, the aluminum can only absorb a certain amount of silicon and remain soluble.
The highest amount of silicon that can be added to aluminum and remain soluble is about12% of the alloy, and this is referred to as its eutectic state. If more silicon is pushed into the mix, it remains as a crystal structure which is dispersed evenly throughout the aluminum alloy. This now becomes a “hypereutectic†alloy, and its benefits are greater than its eutectic counterpart as expansion is much more limited and it is stronger.
As with most things in life, there are trade-offs. Here the downside is that the pistons become slightly more brittle as additional silicon is added, but this is a small trade off given the added overall strength. Hypereutectic pistons typically contain anywhere from 16% to 18% silicon. The cost of hypereutectic pistons falls in between that of forged and cast pistons, so they offer an excellent value when price is a consideration.
Performance and strength are important in piston construction, but hypereutectic pistons offer more advantages beyond their use in performance applications. Automotive engineers have been constantly making refinements to internal combustion engines in an effort to achieve more with less. The use of hypereutectic pistons helps this effort in terms of both emissions and wear.
Most of us are aware of basic piston construction and that there is a significant gap between the cylinder wall and the top of the piston above the upper compression ring. This gap is known as a “quench zone,†or an area where unburned fuel can hide. Unburned fuel, of course, results in excess hydrocarbon emissions and reduced efficiency. By dramatically reducing this quench zone with hypereutectic piston technology, these losses are kept to a minimum.
By maintaining a much closer clearance between the piston and cylinder during all phases of operation, including cold to warm, piston scuffing and friction are kept to a minimum. The distance between ring grooves can also be reduced with a hypereutectic piston. This allows for a better seal and less pressure loss in the combustion chamber. The hypereutectic piston rocks less than a normal eutectic piston when it is cold which helps reduce premature ring wear.
Hypereutectic alloys also stand up to the additional loads that forced induction in the form of turbocharging and supercharging bring to the party. Forced induction engines have become commonplace in modern engines as a method of increasing power while reducing emissions.
It is apparent that this new piston technology is one that benefits both the racing industry as well as the passenger car industry. They are likely to become more commonly used as the demand for lower emissions and power become greater.
Certain concerns exist with other internal engine components as well. Compatibility between camshaft lobes and followers is just one example. Piston-to-valve clearance is another. Valve spring coil bind is yet another, and this concern can be compounded by the use of high-lift camshafts.
As with all engine builds, special attention must be paid to crankshaft and camshaft endplay, valve stem-to-guide clearance, and proper alignment of timing chain or belt sprockets. Engine sealing is another issue of concern, since many OE procedures involve formed-in-place chemical sealants in place of cut gaskets, and many OEs now recommend that chemical gaskets be used at the time of overhaul.
It would be easy to pass along responsibility for some of these tasks to your machinist or the parts manufacturer. But that would be a cop-out.
It doesn’t matter whose fault it is if you install main bearings and the crankshaft doesn’t turn. The ultimate responsibility for the functionality of any given part lies with the engine builder.
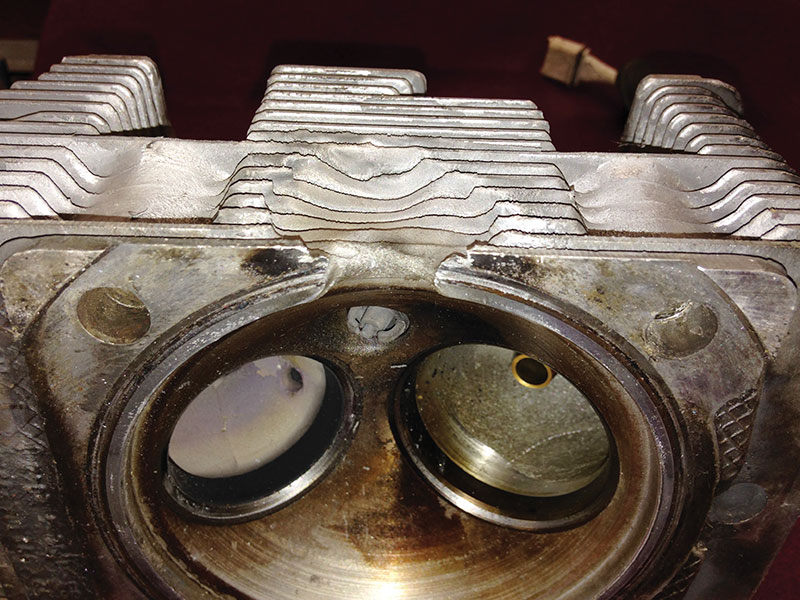
0 Comments