Since the early 1900s, the diesel engine has been widely used in many industries to power vehicles and equipment. They have remained popular because of their overall efficiency and durability, although in the United States this may not be as apparent as in other countries. Worldwide, diesel vehicles account for 50 percent of vehicles on the road. In the United States, fewer than 10 percent are diesel!
BMW has been in the diesel engine club for quite a while. In the mid 1980s, they released their first diesel engine, the M21. This was based on the venerable M20 engine but with strengthened components to handle the increased forces from a diesel engine. It was available in both 3 Series models as well as 5 Series. It’s rare to see a BMW diesel from the 1980s in the United States. Any models you may come across are most likely gray market imports.
Thermal Efficiency
By operating at a much higher compression ratio than gasoline engines, diesel engines are able to compress the fuel/air mixture until ignition occurs. As the pressure inside each cylinder rises, the temperature also rises until spontaneous combustion occurs. The compression process lets the engine squeeze a little more energy out of the fuel. Diesel engines are known to have the highest thermal efficiency of any internal combustion engine design. This means diesel engines create the least waste energy [heat] of any internal engine design. Less waste equals more power and efficiency.
Glow Plugs
Diesel engines use glow plugs to aid in starting and smooth running. By increasing the temperature in each cylinder with a glow plug before cold start-up, proper combustion can be completed quicker, particularly when the engine is cold or in low ambient temperatures. In most modern diesel engines, the glow plug system is inactive until temperatures are below a set point. Most commonly, this is around 40 degrees F. The colder the ambient temperature, the longer that glow light will stay lit! On many diesel engines with bad glow plugs or glow plug modules, the vehicle may not want to start at all if the glow plug system is not operating correctly.Â
BMW diesel engines have a primary driver for the glow plug system, known as the glow plug preheating control unit. These are failing more frequently as many engines reach higher mileage. Most commonly, the control unit sets glow plug circuit faults for multiple cylinders. Rough running is often noticed during cold starts if there are issues with the glow plug system. During diagnosis, don’t forget the basics!
Always start by ohming out each glow plug if bad plugs or the control unit are suspected. Correct resistance values may vary, but you should never find infinite resistance on a glow plug. Although glow plugs are easy to test with a multi-meter, the time-consuming part of testing is the necessity to first remove the intake manifold. This is the case with BMW’s M57 and N57 diesel engines. The glow plug control unit is located under the intake manifold as well and can be tricky to remove because of its awkward location. In addition, it may be necessary to remove coolant pipes during module replacement.
If a faulty module is being replaced, it’s wise to replace all of the glow plugs at the same time. It’s also important to monitor coolant temps during glow plug diagnosis. If a lazy thermostat is keeping the coolant temps too low, this can result in excessive glow times, shortening the life of the module and glow plugs. Â
A side note: In higher-mileage vehicles, the glow plugs may become stuck in the cylinders from carbon buildup and corrosion, making them all but impossible to remove without stripping out the threads in the cylinder head. By pre-treating with a penetrating oil spray and getting the vehicle to full operating temperature before attempting removal, the risk of engine damage can be lowered. Do not heat the glow plugs directly! This can quickly destroy the aluminum head and ruin your day. If the glow plugs do break off in the cylinder head … well, have fun. Many tool manufacturers offer removal kits for broken glow plugs.
Fuel System
BMW utilizes a common rail direct injection fuel supply system on their modern diesel engines. It shares many of the same design principles as their gasoline engine counterparts. By directly injecting diesel fuel into the combustion chamber at extremely high pressure, more even fuel atomization is ensured. This allows for an efficient combustion event that can create more usable power. Pressures at the fuel rail are in excess of 30,000 psi! Fuel pressure this high can be fatally dangerous if proper safety precautions are not followed.
BMW uses Bosch Piezo-electric fuel injectors on their direct injected engines. By using Piezo-electric elements in the fuel injectors, the DDE (Digital Diesel Electronics) can control fuel injection duration down to the millisecond. The fuel injectors contain a quartz Piezo actuator. By introducing an electrical current to the Piezo actuator, it actuates the pintle to release fuel spray.
This is where fuel pressure is at its highest, as it must overcome the spring pressure inside the injector at upwards of 30,000 psi. The extremely high pressure vaporizes the fuel into a fine mist, which readily ignites once cylinder pressure is high enough. Piezo injectors can be operated much faster than a standard injector, allowing for much tighter control over fuel delivery. This can drastically increase efficiency and power output.
When repairs are made to the fuel system, it must first be safely depressurized.  This doesn’t mean crack open a line on the fuel rail. This will damage components as well as send atomized fuel spray across the engine. By using factory level scan equipment, the fuel system can be safely depressurized to ensure a safe working environment.
Because of such high operating pressures, BMW fuel injectors lead a difficult life. At high pressure, any contaminants in the fuel supply system can quickly destroy fuel injectors as well as the supply system sensors. For example, if the high pressure fuel pump fails, it may send debris into the fuel rail. This will quickly clog and render the fuel injectors useless. At this point, the fuel rail, injectors, high pressure pump, and rail sensors would all have to be replaced. Thankfully, BMW has designed a fairly reliable fuel supply system, and these systems don’t usually fail catastrophically.
Fuel injector issues still arise from time to time. Usually, these issues appear as rough running at idle. On the M57 engine, smooth running faults are commonly stored for cylinders experiencing rough running conditions. Smooth running values can also be viewed live with factory-level scan equipment to determine which cylinders are running poorly. Zero-quantity adaptation faults can be stored for cylinders as well. This fault is almost always a bad injector.
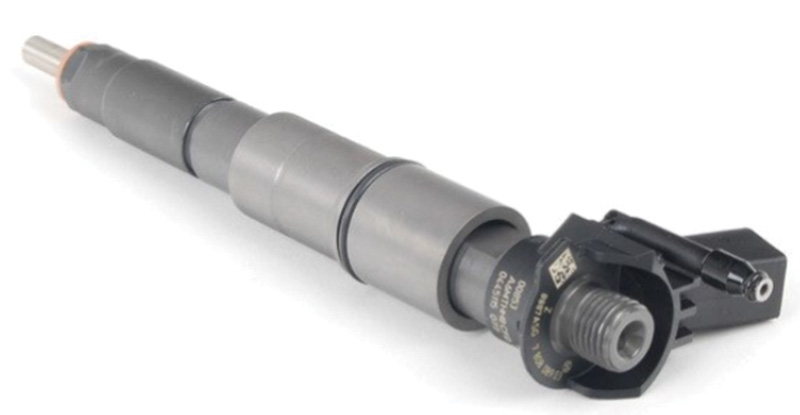
The classification values are visible on the plastic base plate on the injector. Note the fragile line fittings, be careful not to damage them.
If diagnosing a faulty fuel injector, it’s possible to move the injector to a different cylinder to see if the rough running will follow the injector. Each injector has a specific classification value that determines flow characteristics. These values must be entered for each fuel injector on the corresponding cylinder. Failure to store proper injector classification values can cause issues in itself and should not be overlooked when swapping or diagnosing injectors. This is a critical step with BMW injectors and can only be done properly with BMW ISTA software or a comparable factory-level tool.
When replacing fuel injectors, care must be taken not to damage them. Particularly on diesels, the injector can become quite stuck in the cylinder head. BMW offers a small slide hammer tool that threads onto the fuel injector to aid in removal. This is a necessity! If the fuel injector is equipped with a Teflon seal ring, do not use any chemicals or lubricants on the seal. It’s best to keep the seal covered until it’s ready to be installed. Always replace the copper crush washer as well, if so equipped.
BMW injectors incorporate a fuel injector return line. This is where unused fuel is returned to the fuel system. The return line setup on the fuel injector is quite small and prone to damage if not properly secured. If the return line feed is damaged at the fuel injector, the entire injector must be replaced. These are not cheap! Be careful.
Verification of Update Status
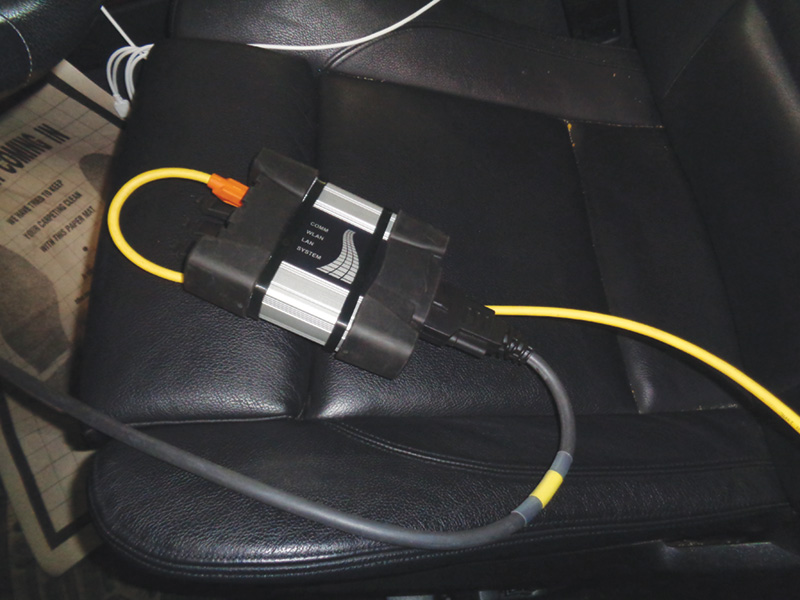
A BMW ICOM interface or factory level pass-through device is a necessity to diagnose and update vehicles.
The fuel injection system is controlled by the DDE. The first step in any diagnosis is to run a full scan of the vehicle as well as verify current I-level or Integration level of the vehicle. On BMW vehicles, the I-level is used to verify update status of all connected vehicle control units. Many issues and problems can be eliminated by updating vehicle systems to a current I-level. Most SIBs (Service Information Bulletins) list the I-level for the corresponding bulletin, so it can be quickly determined if the vehicle requires updates.
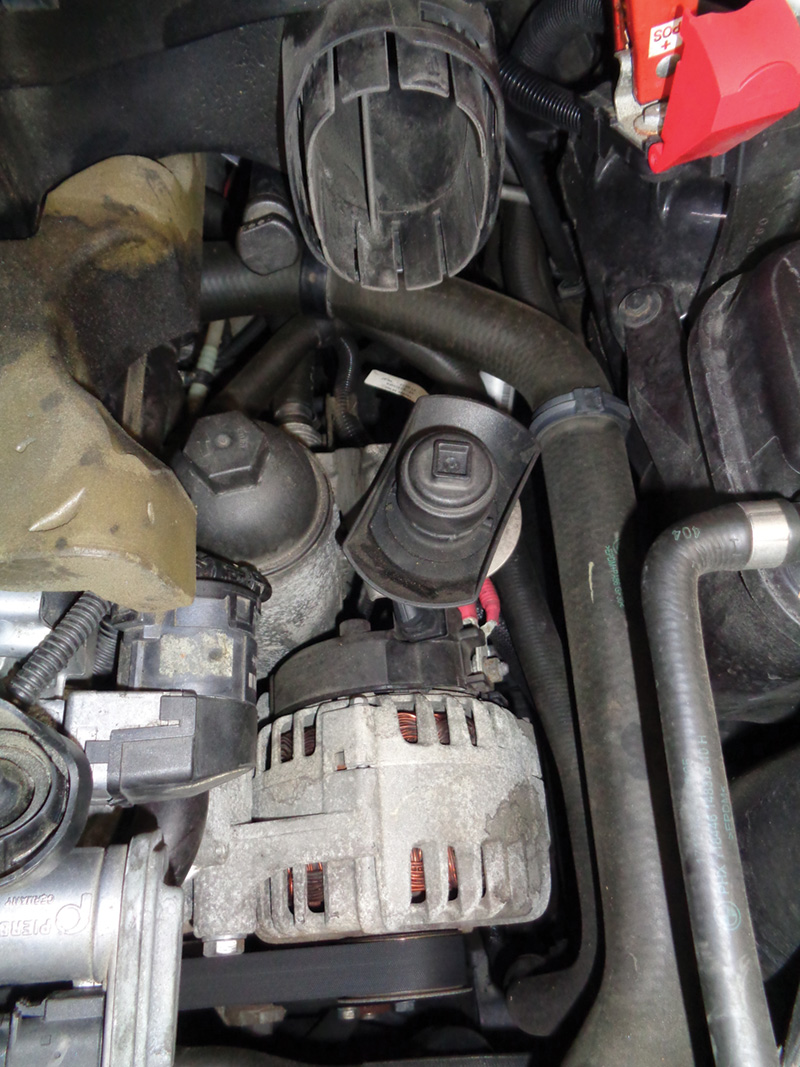
There are two fill locations for DEF on the X5. The larger DEF tank fill is directly next to the oil filter housing. The smaller active tank fill is located on the passenger front of the engine bay.
In addition to requiring updates, DDE can have problems of its own. The DDE control unit houses individual drivers for each fuel injector. In certain cases, the drivers can fail inside the control unit. The problem if the driver fails is that the DDE will not recognize the internal failure.
Most commonly a failed injector driver will manifest as a rough running in one or more cylinders. Often, smooth running faults are stored and the vehicle will point blame toward the fuel injectors. Even after swapping fuel injectors and performing a de-carbon service, these faults can return with a bad DDE. The only way to be certain of a bad DDE is to monitor the fuel injector signal with an oscilloscope. Only then can you verify proper grounding of the fuel injector circuit.
When diagnosing customer complaints of rough running, carbon buildup can often be the main culprit. The BMW diesel has a few issues that make carbon buildup worse. First, the fact that BMW diesels are direct injected leads to carbon buildup. Without fuel washing over the intake valves during engine operation, carbon will begin to take hold and begin to build up. This carbon can originate from the crankcase ventilation and exhaust gas recirculation systems.
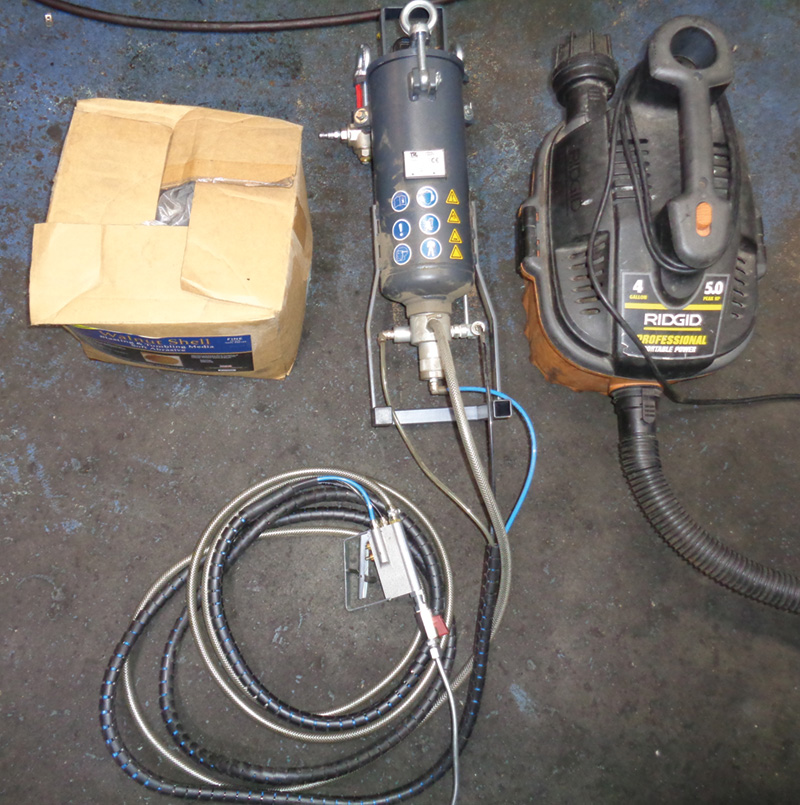
A pressure controlled media blaster has anti-clogging purge action! It’s best to use medium or fine walnut shells for de-carbon services.
Carbon generally builds up around the intake valves and intake ports closer to the valves. As the buildup gets worse, air flow begins to be disrupted to each cylinder. Not enough air entering the engine affects the combustion cycle on both diesel and gasoline engines. This is often felt as a slight misfire at idle or slight engine load. Most commonly, the rough running is worse when the engine is first started, not at full operating temperature. Many manufacturers have struggled with carbon buildup on direct injected engines, and the struggle continues. De-carbon services are a fact of life with BMW diesels. Depending on how the vehicle is driven, every 30–50K miles a de-carbon service should be performed. Also, there are chemicals on the market that can help prevent carbon build-up on the intake valves.
Invest in a walnut shell blaster, it will definitely be put to use often. BMW offers a very nice media blasting machine that is very reliable. Less expensive options exist but these units usually clog up constantly and become a headache. Intake port adapters are also a requirement when performing a de-carbon, otherwise media can quickly cover the engine. Not good! BMW offers specific intake port adapters for different engines.
Due to the intake design on the M57 engine, there are two different intake ports: One set of intake ports is in the standard position on the cylinder head of the engine, and the second set travels straight down through the valve cover. Through use of swirl flaps in the intake manifold, intake tracts can be switched depending on engine load. The upper intake port that passes through the valve cover assembly on M57 engines generally has more carbon buildup then the secondary intake port, as this is the primary air path under load.
BMW uses swirl flaps in the intake manifold to control and divert air flow from the primary intake runners to the secondary ports. These swirl flaps are located at the base of the intake manifold toward the cylinder head. These flaps can become heavily coated in carbon buildup, which restricts their movement if left unchecked. Eventually, the swirl flap system can become completely seized from carbon buildup.
During a de-carbon service, it’s also necessary to inspect and clean the intake manifold. These intakes, particularly on the M57 engine, can become loaded with carbon. You will knock considerable sticky black carbon out of the intake runners, which can become quite thick. Be careful while cleaning the intake. Use of chemicals is only recommended when directed, as the use of inappropriate chemicals can damage and warp the intake manifold. Lots of picks, scrapers, and patience are necessary here.
The M57 and N57 engines both have charge air pressure sensors on the intake manifold. These are susceptible to failure because of blockage from carbon buildup as well… lots and lots of carbon. These pressure sensors generally cannot be cleaned or repaired and must be replaced if found to be faulty.
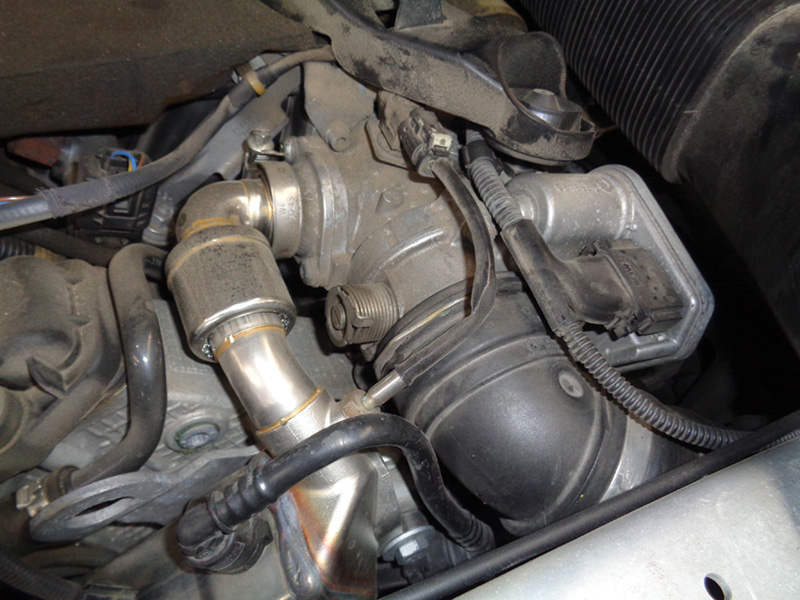
The EGR valve is mounted between the intake manifold and throttle unit. Also note the small flex pipe on the EGR. These do fail occasionally, leaking exhaust gases.
Don’t forget to inspect and clean the EGR (Exhaust Gas Recirculation) valve if necessary during de-carbon service. On the M57 engine, this is located forward of the throttle unit. Due to air flow around the valve, carbon tends to build up around the valve sealing surface, eventually disrupting full airflow and in extreme cases restricts the EGR valve from proper movement.
The EGR valve is necessary to help lower nitrogen oxide (NOx) emissions. EGR valves operate by recirculating a small amount of the vehicle’s exhaust gases back into the intake tract. BMW diesels come equipped with EGR coolers, which lower the exhaust gas temperatures on their path to the intake manifold. By using exhaust gases, it’s possible to lower the oxygen content of the intake charge. The goal of this is to lower peak combustion temperatures, which can greatly reduce NOx emissions. This is particularly important in diesel engines, which already have extremely high combustion temperatures.
Exhaust Emissions Components
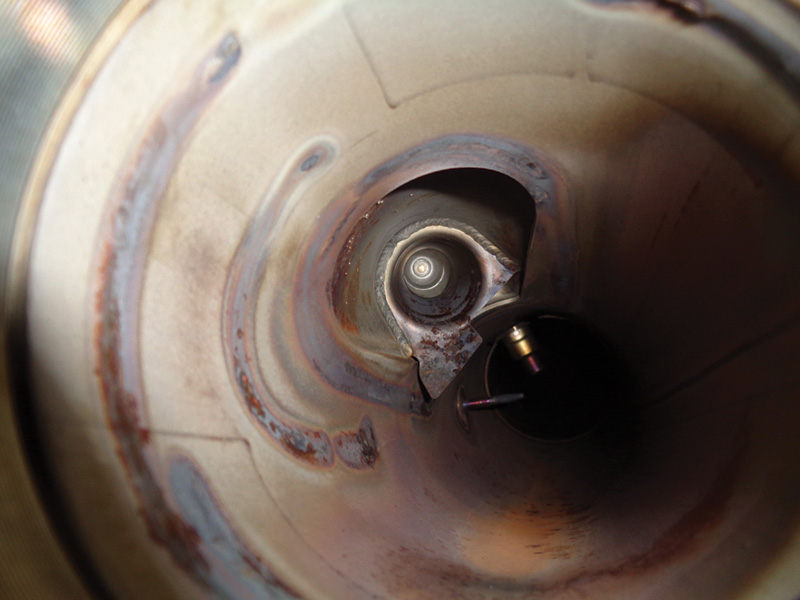
This view of the inside of the exhaust system shows just how clean BMW diesels really are! The DEF injector can be seen top left.
The final and most commonly repaired components of many BMW diesels are the exhaust emissions components. Modern BMW diesels have a multi-stage exhaust treatment system that scrubs even more NOx from the vehicle’s exhaust.
The exhaust first travels through the DPF (Diesel Particulate Filter). This is a specialized oxidation catalytic converter designed to trap the heavier “sooty†diesel exhaust. The DPF is equipped with differential pressure sensors to monitor exhaust flow through the DPF. These sensors can become damaged and clogged with exhaust soot occasionally. If diagnosing a faulty DPF sensor, always check and clear the feed lines of any blockage during diagnosis.
After traveling through the DPF, the exhaust is sent through BMW’s SCR (Selective Catalyst Reduction) component. This is the final resting place for any nasty NOx that has passed through the exhaust system.
The SCR system uses Diesel Exhaust Fluid (DEF) to lower NOx levels. DEF fluid is basically a urea and water mixture. By injecting the DEF fluid into the exhaust, it becomes vaporized in the hot exhaust stream. The chemical reaction between the DEF and NOx in the diesel exhaust breaks down the nitrogen oxide into nitrogen and water. This system is widely used by most diesel engine manufacturers and has proven to be the most effective tool to lower NOx emissions levels.
The entire exhaust system as well as the EGR system are monitored closely with NOx sensors and Exhaust Gas Temperature (EGT) sensors. These sensors do fail occasionally. However, always check for necessary updates to the DDE when replacing sensors. Often software update is a necessary step to complete the repair.
BMW uses a urea dosing valve mounted at the front of the SCR converter to inject DEF into the exhaust stream. This is followed by a “mixer†gasket to aid in DEF vaporization.
These valves are exposed to extreme conditions and occasionally fail. During inspection, check for any DEF residue or blockage around the nozzle. A leaking dosing valve can wreak havoc on the exhaust system!
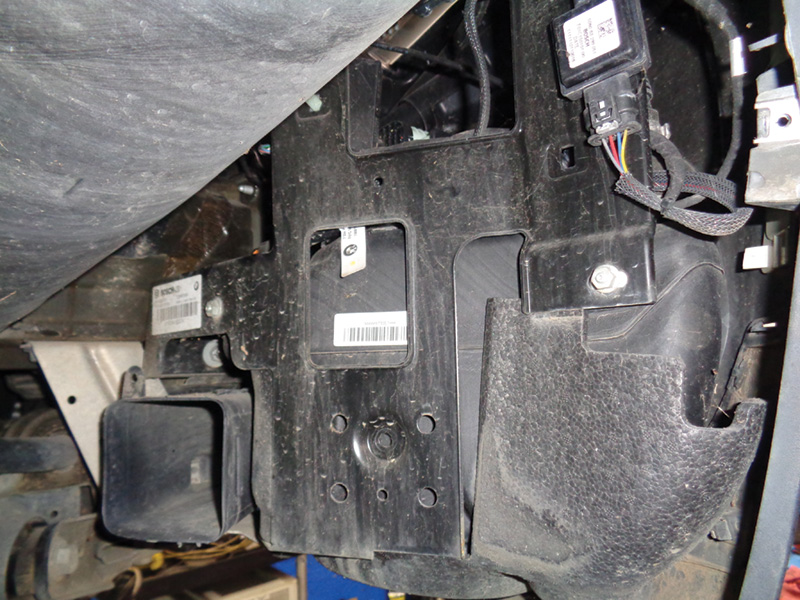
This is the active DEF tank on an E70 chassis diesel. Located in the passenger front wheel well, access is very limited without removal.
The DEF tanks have become a common failure item on many BMW diesels. These tanks are equipped with multiple sensors to monitor and condition the DEF for proper delivery. Heater circuit failures and temperature sensor failures are extremely common for BMW DEF tanks. At this time, it’s necessary to replace the entire tank assembly to replace the faulty sensors. No serviceable parts are available separately from BMW for this equipment.
Unfortunately DEF fluid can be hard on sensors, particularly when exposed to air for extended periods. It’s important to keep any DEF tank as full as possible. By keeping sensors covered with fluid away from oxygen exposure, their lifespan can be increased. Don’t run your DEF tanks low!Â
Download PDF
0 Comments