Why not route wasted energy back into the battery pack? Brake linings will last and last!
A quick physics lesson
When we talk about regenerative braking, the physical property we are dealing with is known as kinetic energy. Kinetic energy is the energy of mass in motion. The kinetic energy of an object is the energy it has because of its motion. Perhaps the most important property of kinetic energy is its ability to do work. Work is defined as a force acting on an object in the direction of motion. Work and energy are so closely related they are sometimes thought as interchangeable.
While energy of motion is usually expressed one-half the product of mass times the square of velocity (E = 1-2mv2), work (W) is more often thought of as force times distance (W = Fd). If we want to change the kinetic energy of a massive object, we must exert work on it. For example, in order to lift a heavy object, we must do work to overcome the force due to gravity and move the object upward. If the object is twice as heavy, it takes twice as much work to lift it the same distance. It also takes twice as much work to lift the same object twice as far.
Kinetic energy can be converted into other forms of energy and vice versa. For example, kinetic energy can be converted into electrical energy by a generator, or into thermal energy (heat) by the brakes on a car. Conversely, electrical energy can be converted back to kinetic energy by an electric motor, heat can be converted to kinetic energy by a steam turbine, and chemical energy can be converted to kinetic energy by an internal combustion engine.
In regenerative braking the kinetic energy of the vehicle is converted into electrical energy by the vehicle’s electric machine (the technical term for the drive motor). This energy conversion causes the vehicle to lose kinetic energy: It slows down. The generated electrical energy is then fed to the high voltage battery for storage. In conventional braking, the kinetic energy is converted into heat, which is basically wasted.
Not so new
The idea of a brake that could take the kinetic energy it absorbs and turn it into potential energy for later use has been around since the late 1800s. The earliest versions of this technology were a spring type regenerative braking system (RBS) on front wheel drive bicycles and horse drawn carriages. An early example of RBS technology was in the Baku-Tbilisi-Batumi railway in the early 1930s. In the 1950s, Swiss company Oerlikon developed the gyrobus, which utilized a flywheel as its energy storage method. (Unfortunately the gyroscopic motion influence it had on the bus led to its discontinued use). In 1967, the American Motor Car Company created an electrical energy regeneration brake for their concept electric car, the AMC Amitron. Toyota was the first car manufacturer to commercialize RBS technology in their Prius series hybrid cars. Since that time, RBSs have evolved to be used in almost all electric and hybrid cars, as well as some gasoline-powered vehicles.
Does it work?
If we want to evaluate regenerative braking, we really need to look at two different parameters, efficiency and effectiveness. Efficiency refers to how well regenerative braking recovers the energy from braking. Does it waste any of that energy as heat, or does it turn all of that kinetic energy back into stored energy? Effectiveness, on the other hand, refers to how large of an impact regenerative braking really makes. Will you really notice a difference in the range or economy of your vehicle?
According to Tesla, Inc., the efficiency of the regenerative braking process varies across many vehicles, motors, batteries and controllers, but is often somewhere in the neighborhood of 60-70 percent efficient. The regenerative process itself loses around 10-20 percent of the energy being captured, and then the drivetrain loses another 10-20 percent or so when converting that energy back into acceleration.
Trying to determine effectiveness of your the regenerative braking system gets a little tricky: Will it make your vehicle travel 5 percent farther? 30 percent? Many factors have to be considered to answer this question. What type of driving? Intuitively, open freeway driving with little braking is expected to be less effective than more typical suburban driving with its frequent acceleration and deceleration cycles.
Remembering our physics, the rate of deceleration as well as the mass of the vehicle are factors, as is the terrain. A long downhill will provide a greater opportunity for energy conversion. According to Mercedes-Benz, comprehensive road tests using different test subjects have shown that it only takes a relatively short time for additional savings to be achieved as drivers learn to make increasingly deliberate and effective use of the regenerative capabilities.
Intuitive driving can significantly affect the efficiency of the system. If you anticipate stops and slowdowns in traffic, the regenerative capabilities are used to a greater extent instead of hard stops that use the brake pads.
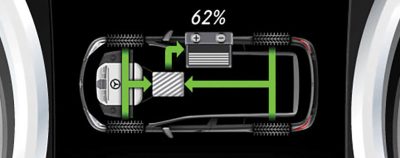
To help the driver achieve better effectiveness, Mercedes-Benz models incorporate a Display Concept for the driver to monitor. The central display provides information on the current energy flow and the charge status of the batteries, as well as an illustration of the drivetrain and colored energy flow indicators. The driver is able to monitor fuel consumption via energy/time graphs.
Radar sensing braking
Introduced with the B-Class electric vehicle, and standard on all hybrid vehicles, Mercedes-Benz offers selectable levels of regenerative braking. Using paddles on the back of the steering wheel, the driver can customize how aggressive the regenerative braking is, in three stages: D- mode is the most aggressive, with considerable braking effect; D mode is much like a gasoline-powered model, with a moderate braking effect; and D+ mode is ‘coasting’ mode, where no regenerative braking occurs.
A fourth setting, D-AUTO, uses the existing radar sensor to base the amount of recuperation on the traffic situation. This is the default setting when selecting a forward drive gear. When approaching a vehicle, recuperation is increased, while when either no vehicle, or a very distant vehicle is detected in front, recuperation is decreased to allow coasting. Recuperation is also increased when a steep downhill slope is detected. This is a convenient feature that also helps boost battery range.
EQC 400 Electric SUV
Speaking of intuitive driving, the new EQC 400 employs a new feature, Eco Assist, that might be described as an interface between driver and machine in order that engineers may squeeze more efficiency from that powertrain. The system, under certain driving conditions, actually tells the driver to lift his or her foot off the accelerator to let the system manage the momentum during a coasting situation, improving the regenerative braking capability without compromising speed at the same time. Like the B-Class, the system uses navigation data, traffic sign recognition, radar, and the car’s stereo cameras to anticipate things like cresting hills, traffic, or upcoming reductions in speed limits, then signaling the driver with a “foot off accelerator†icon in the instrument cluster. The car then modulates motor activity to either let the car coast, or engage the regenerative function to transfer power to the battery while slowing the vehicle.
Brake pads that last
As might be expected, vehicles with regenerative braking have much less wear on the mechanical components of the braking system e.g. the pads and rotors. It is important to note that the hybrid or EV vehicles you service will still have a conventional braking system in addition to the regenerative braking system. Due to the effectiveness of the regenerative braking system, the mechanical brake pads and rotors won’t be used as often, meaning they will last longer than one might expect. It’s not unusual to see a hybrid with 70,000-100,000 miles on the odometer that still has the original set of front brake pads.
This does not mean that other components, like hardware, rubber seals/boots, or that brake pads can’t fail for other reasons other than general wear: Weather and time still play a major part in the overall condition of the components. This means that it’s still a good practice to check the brake components during a routine inspection of the vehicle. In harsh climates, corrosion may build up between the backing plate and friction material due to water intrusion and road salt and ice-removal chemicals. A thorough inspection of the system is still warranted at the recommended intervals.
It is important to understand how the two systems function so you can be well informed, not only when servicing hybrids and EVs, but when explaining the nature of the system to your customer. This question is a common one fielded by Mercedes-Benz: “Why does the brake pedal in my Mercedes-Benz Hybrid feel different the first time I step on the brakes after I start the vehicle and sometimes during normal driving?†Engineers have offered this explanation:
“Hybrid vehicles utilize both regenerative and conventional hydraulic (friction) braking to reduce the speed of the vehicle. With regenerative braking, the kinetic energy of the decelerating vehicle is absorbed by the electric motor to generate a brake torque. The generated electrical energy is then fed to the high voltage battery for storage. Conventional hydraulic brakes utilize hydraulic fluid to apply pressure to the brake pads which squeeze against a rotating brake rotor. Friction is created between the pads and rotor which generate a brake torque to stop the vehicle. Depending on the driving conditions, the total braking torque requested by the driver can be divided into a regenerative component and a hydraulic component. If the required total braking torque can be achieved using regenerative means alone, then none of the braking is done hydraulically: In this case deceleration is achieved solely by using the electric motors to generate electricity.
Due to the operating principles involved, the perceived brake pedal feel may be different during regenerative braking when compared to conventional braking. On the regenerative braking system, there is a length of free travel integrated into the connection of the brake pedal. This is used during the regenerative braking function. A pedal force simulator is used to create a brake pedal resistance which mimics the brake pedal feel of conventional hydraulic brakes. During the first brake actuation, the system is checked for proper operation and the regenerative braking system is activated. The pedal force simulator is switched off for the first pedal application, resulting in slightly longer pedal travel compared to subsequent brake pedal applications when the system is active.â€
It is important to note that if an ABS (Anti-Lock Brake System) intervention takes place, regenerative braking is terminated for this brake application and the braking torque is provided solely via the conventional hydraulic brakes. Regenerative braking is not possible below speeds of approximately 13 MPH. As soon as the vehicle drops below a speed of approximately 13 MPH during a brake application, the system switches from regenerative braking to hydraulic braking, possibly resulting in a change of brake pedal feel.
How does it work?
In regenerative braking, the electric motor that drives the vehicle is turned into a generator, and the wheels transfer the vehicle’s kinetic energy via the drivetrain to the generator. Some of us old-timers remember the days when vehicles actually had generators instead of alternators: To test them we would turn them into an electric motor by applying voltage. The opposite happens when regenerative braking takes place, the electric motor is turned into a generator. This is an example of Faraday’s law which states that a change in the magnetic field near a wire will cause a voltage (Electro-Motive Force, or EMF) to be induced into the wire. No matter how the change in the magnetic field is produced, a voltage will be generated. The change could be produced by changing the magnetic field strength, moving a magnet toward or away from the wire, moving the wire into or out of the magnetic field, rotating the wire relative to the magnet, etc. With regeneratve braking, the change that happens is the force of the drive train acting upon the electric motor of the vehicle, transforming most of the kinetic energy into electrical energy, which is then stored in a high-voltage battery. At the same time, the generator exerts a physical resistance to turning (due to the electricity created), which acts to slow the vehicle. When more braking torque is required than the generator alone can provide, additional braking is accomplished by friction brakes.
How Formula 1® racing has helped the development of EV technology and regenerative braking
Mercedes-AMG Petronas Motorsport scored its first victory of the Formula 1 hybrid-electric era at the 2009 Hungarian Grand Prix, with driver Lewis Hamilton. That early system relied on discrete battery pack and power electronics modules that sent energy to, and recovered it from, a 60-kilowatt (80 HP) electric-assist motor. It also laid the groundwork for the mighty Mercedes-Benz SLS AMG Coupe Electric Drive of 2013, according to Andy Cowell, managing director of Mercedes-AMG High-Performance Powertrains, in a video released by the F1 team.
Formula 1 termed these systems “Kinetic Energy Recovery Systems†or “KERS.†“Today we would call that a ‘regenerative braking system,’ recovering waste energy from the car,†said Cowell. “The mass and velocity of the car, recovering that energy through an electric motor, energy converted in the power electronics and stored in the cells of the energy store, using that energy to then propel the car as the car accelerates.â€
While hybrid-electric production models seek to improve fuel efficiency, the technology at work is the same. “In motorsport we use it to go quicker, in the road car world we use it to go further with the same amount of fuel,†he explained.
Maintenance
As of this writing, there really is not much in the way of maintenance in a regenerative braking system. The conventional part of the braking system will require routine service but, as noted earlier, wear items will need replacement less frequently. It should be noted that in some cases at low temperatures, the customer may report that the regeneration indicator on the dash is indicating a low regeneration rate, particularly if the EV is not at full charge. That is considered normal and is the processor’s way of protecting the battery pack until it warms up. The XENTRY Diagnostics system has menu-driven test routines to guide you though just about any possible regenerative braking system concerns your customers may have
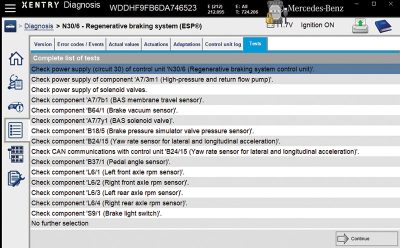
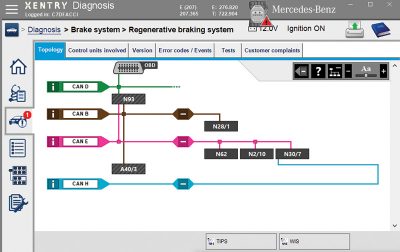
0 Comments