The lowdown on these humble but critical components
Mercedes-Benz vehicles use thousands of fasteners to keep things from coming apart and, as technicians, we encounter dozens of these each day in our work. The majority of these fasteners do their job, day in and day out, for decades without trouble. But some fasteners serve a critical safety function, where failure could result in a crash, injury or death.
Most fasteners — not limited to nuts and bolts — can be reused until they show signs of deterioration. But some fasteners can only be used once — a so-called Single-use Fastener. Blind rivets, for example, are an obvious example, as they are destroyed during the removal process. Others, like stretch bolts, are designed to deform during installation and are likely to break if reinstallation is attempted. And still others have self-locking features that are destroyed during removal. It is these fasteners we will discuss here.
Daimler engineers design fasteners and connections for their intended usage using science and math. While one of the biggest influences of fastener performance is the installation torque, even a properly-torqued bolt can come loose. It is a well-documented fact that cyclic loading, which is the regular and repeated increase and decrease of the load on a fastener, can cause a fastener’s clamping force to be reduced over time and increase the risk for loosening and failure.
For this reason, certain fasteners are designed with self-locking features, designed to ensure that the fastener remains tight. Here we will explain how to recognize and work with these fasteners so you don’t accidentally reuse them.
But why?
In speaking with technicians, we found that few of them really understand why these fasteners need to be replaced. They’ve been reusing caliper bolts (for example) for years and years without any problems. Well, you might continue to do that, and the fasteners might be fine, until one day, they aren’t. If your failure to replace a self-locking fastener causes a death or injury, how are you going to defend yourself in the resulting lawsuit? Think hard on that.
There are also several advantages to replacing single-use fasteners, and not just for safety and liability reasons. It is just the right thing to do. It’s difficult to get in trouble if you follow the manufacturer’s recommendations. You’ll also sell a few more parts, and everyone knows new fasteners are easier to install and, when removal time comes, they are often easier to remove as well. Remember: This is not just for your own protection, but for your customers’ safety as well. Studies show that deceased customers don’t offer much in the way of repeat business.
In the Mercedes-Benz Workshop Information System (WIS), many of the work instructions start with a statement to review the “Notes on self-locking nuts and boltsâ€, found in WIS document AH00.00-N-0001-01A. Any time you see this message, you can be sure that the work procedure has at least one self-locking fastener that needs attention.
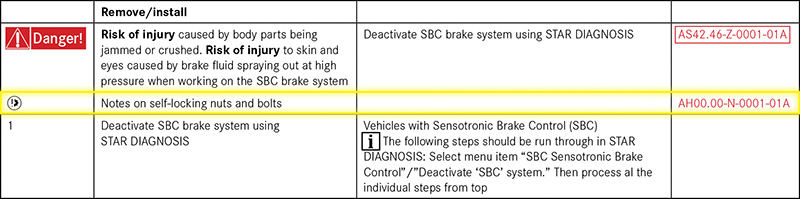
Locking features
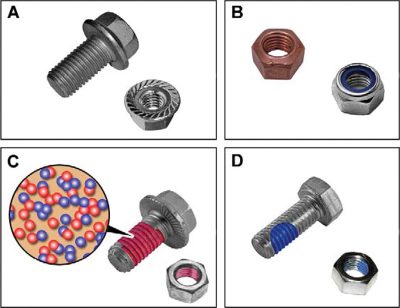
The locking features of fasteners fall into two categories: Mechanical and Coating-based. Mechanical features include locking splines and deformation, while coatings include micro-encapsulated and polyamide coatings.
General precautions
Bolts and nuts with locking splines, self-locking nuts, and micro-encapsulated nuts and bolts must always be replaced after they have been used once. The removal process permanently damages the locking feature.
No greases, oils, waxes or other materials may come into contact with, or be applied to, bolted connections and their contact surfaces. This contamination can affect the locking feature and tightening torque and lead to connection failure.
Locking splines
This mechanical feature involves teeth on bolt heads or nuts, which work their way into the material of the parts being fastened. The increased friction helps prevent loosening. When using fasteners with locking splines, care must be taken to ensure that both the nut and the bolt have the locking feature: It is of little use if only one has it, since the connection can then still work its way loose. It is also possible that anti-corrosion coatings can be damaged, increasing the risk of corrosion: After tightening a fastener in areas likely to get wet, spray the fastener with anti-corrosion wax. These fasteners must always be replaced after loosening.
Self-locking nuts
All-metal self-locking nuts depend on the physical deformation of the nut to significantly increase friction, with a resulting locking effect. The friction is created by the elastic re-straightening of the collar, which starts out with a slightly oval shape. Other self-locking nuts have a vinyl (or other material) ring, which achieves increased friction by deforming the vinyl ring. In both kinds of nut, the act of tightening permanently changes the locking feature, so when loosened it has lost its self-locking ability. These fasteners must always be replaced after loosening.
Microencapsulated bolts and nuts
These fasteners are recognized by the colored adhesive coating applied all the way around. The color is not significant. The coating has a dull, pale and porous appearance. During tightening, the microcapsules of adhesive and hardener are broken open, mixing them. The resulting chemical reaction creates a rigid adhesive layer, locking the fastener in place, with a sealing action as well.
During tightening, be sure to reach the final tightening position without delay, within a minute or so. Once tightened, microencapsulated fasteners must not be moved, as this will destroy the adhesive layer and render it ineffective.
When loosening a microencapsulated fastener, be careful of their habit of breaking loose suddenly. After removing a microencapsulated fastener, re-cut the threads in holes (blind and through) to remove all traces of adhesive before reassembly. These fasteners must always be replaced after loosening.
Polyamide coating
Self-locking bolts and nuts with a polyamide (Nylon) coating can be recognized by the spot of colored material that is only part-way around the fastener, with a generally shiny and waxy appearance. Some fasteners do have a coating all the way around, however. These self-locking fasteners can sometimes be re-used several times, and sometimes can be used only once. If both the fastener and the polyamide material are in good condition, re-use is possible, as long as the WIS work instructions don’t specifically require replacement. If the coating is worn or deteriorated, replace it.
Replace every time!
So there you have it: We know that even a properly designed and installed fastener can come loose, so for critical connections an additional self-locking feature is added to help reduce the risk of failure. The technician has considerable legal liability if a repair was performed contrary to the manufacturer’s instructions. Most self-locking fasteners must be replaced after each use. So do the right thing, every single time, by learning to recognize self-locking fasteners and replacing them.
0 Comments