We’ve previously looked in depth at the M270/274 and M276 engines. What about their replacements? What’s new about this engine plus service tips and hints. Also an introduction to the M254 engine.
Replacing the M27x-series engines, the M260/264 engines have already started showing up at independent workshops worldwide. Both engines are nearly identical: The M260 designation refers to the transverse mounted front-wheel/all-wheel-drive version and the M264 refers to the longitudinally mounted rear wheel drive version. These are the new four-cylinder gasoline engines in the family line of comprehensively redeveloped engines from Mercedes-Benz. The output of these 4-cylinder engines approach the power of the previous higher capacity six cylinder engines. At the same time, they consume significantly less fuel than a corresponding six-cylinder engine. Although introduced in 2017, the M264 began showing up in the U.S. in model year 2019 C- and E-class models.
Special Features
The engine includes twin-scroll turbochargers, an intake manifold having extremely short air paths and an exceptionally compact compressor housing that help guarantee a more spontaneous engine response and a fast reaction to accelerator pedal movements. This engine really approaches the performance of a true sports car. Standard also is direct injection with the latest generation high-end piezo injectors. The valve train sports CAMTRONIC, Mercedes-Benz patented adjustable camshaft technology. A friction loss reduction package rounds out the improvements.
Twin Scroll Turbos
Mercedes-Benz is credited with the first successful application of a turbocharger in a production vehicle, namely the 300SD, they are also on the cutting edge with twin-scroll technology. Just as intake manifolds have developed over time to become more efficient with variable or shorter runners and configurations, the exhaust needed to be tuned more dynamically to optimize performance. Enter the twin-scroll turbo chargers. In the exhaust manifold, the flues of two respective cylinders are combined into one section and brought back together by the structure of the turbine wheel housing directly in front of the turbine runner. By directing the exhaust and “tuning†the pulses by pairing them into a more efficient configuration, the kinetic energy from the exhaust gases are recovered more efficiently by the turbine. The exhaust gas turbocharger is cooled via coolant and integrated into the engine cooling circuit. By incorporating the exhaust gas turbocharger into the oil circuit, lubrication is ensured. An electronically controlled waste gate actuator adds to the performance improvements. The net result of the twin-scroll package is higher output at lower rpms and an overall performance increase.
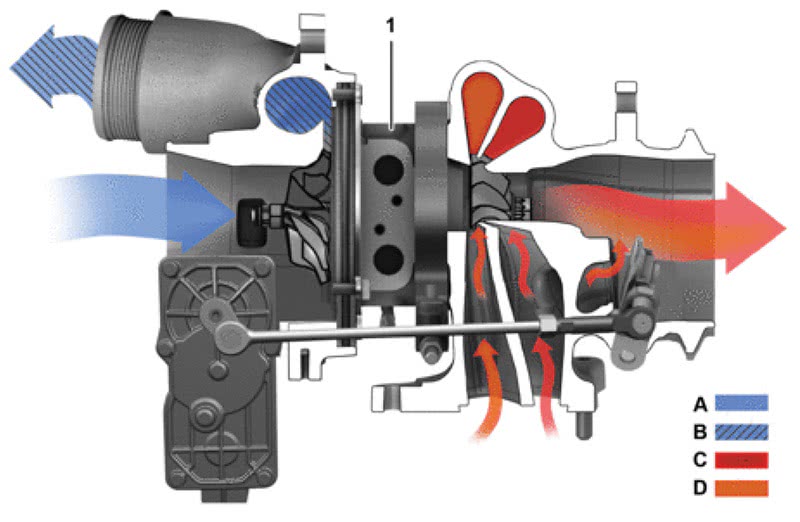
Internals
Both engines have die cast aluminum engine blocks with cast iron cylinder liners. CONICSHAPE technology is used in the production of the cylinder bores. This means that the cylinder bore is widened at the lower end of the cylinder liners and formed in a (slightly) conical shape, which minimizes piston friction and lowers fuel consumption. The new and old engine series share the same bore and stroke sizes except for the M264 1.5L engine (non-US version)—it was reduced by 2.6 mm cylinder bore size comparing to the previous 1.6-liter version (also non-US). Like the predecessor, the M260/M264 2.0L version has a balance shaft located in the lower section of the crankcase. In addition to that, engineers introduced a new centrifugal damper into the powertrain plus plastic engine mounts, making engine operation smoother and more comfortable. Pistons have cooling ducts and optimized piston rings to also help reduce friction and improve fuel mileage.
The newly designed cylinder head is made of aluminum-silicon alloy. It features four valves per cylinder, double overhead camshafts and, as mentioned earlier, CAMTRONIC technology for the valve side of things. The CAMTRONIC system allows two-stage adjustment of the valve lift. In addition to the variable valve lift, there are two hydraulic camshaft adjusters providing variable valve timing for both intake and exhaust sides. The M260 and M264 use a toothed timing chain.
CAMTRONIC
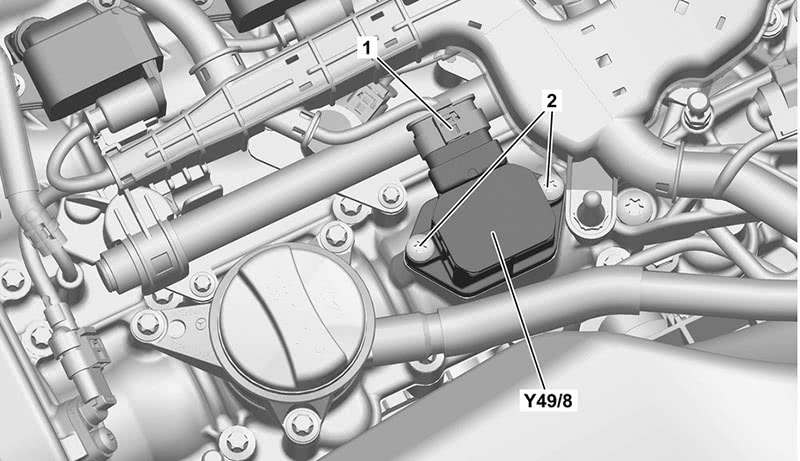
Let’s take an in-depth look at how the valve timing adjustment is accomplished on this engine. Variable valve control consists of mechanical, hydraulic and electromechanical control of the valve train by the engine control unit. This makes it possible to adapt both the valve timing and lift depending on the load and operating condition of engine. The technology incorporated here contributes to serious reductions in emissions and fuel consumption. Variable valve train can be implemented on both the inlet and exhaust sides. Two principles are at play here: Camshaft adjustment and Valve lift adjustment.
Valve lift adjustment or valve lift switchover is where the actual camshaft valve lift is changed to a flat or steep lift. By implementing a flatter or smaller lift when throttling down or partial load operation, fuel consumption can be reduced. A smaller valve lift also improves the friction loss which results in a cooling advantage. To ensure an optimal combustion despite the smaller valve lift, the fuel is injected multiple times. To improve the reduced turbulence of the fuel/air mixture in the combustion chamber around the spark plugs, the fuel/air mixture is ignited multiple times in low partial-load operation. To achieve a higher torque, a switchover takes place to the large valve lift so that a steeper valve lift can be applied such as in a full load situation.
The valve lift switchover is implemented by means of an electromechanical system. The electromechanical system works with a
switchover valve or CAMTRONIC actuator that engages mechanically with the camshaft. The camshafts are designed with two parts, i.e. a hollow shaft with cam pairs and spiral-shaped grooves that enclose a solid shaft with cams. Depending on the rotational speed and engine load, the actuators engage in the spiral grooves on the rotating camshaft pieces. The actuators move each of these axially to one of the end positions (large or small valve lift). This causes the cams to be moved on the camshaft.
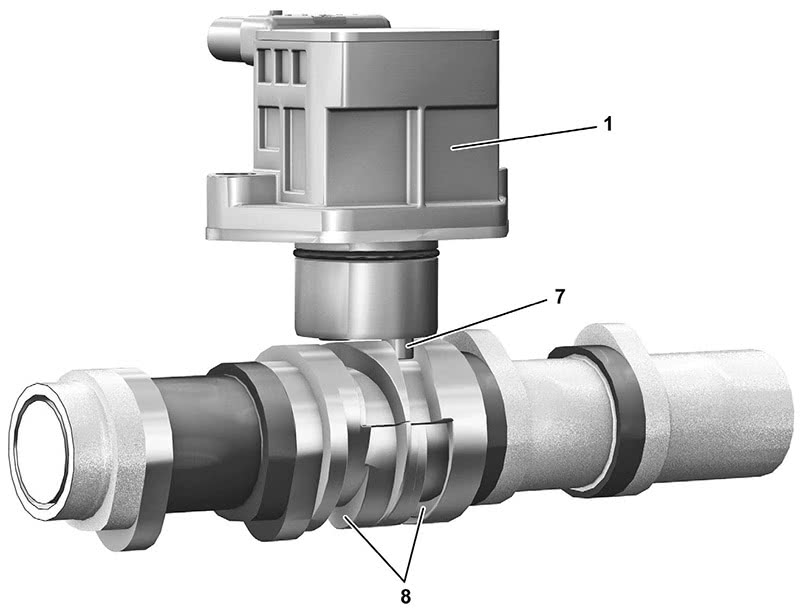
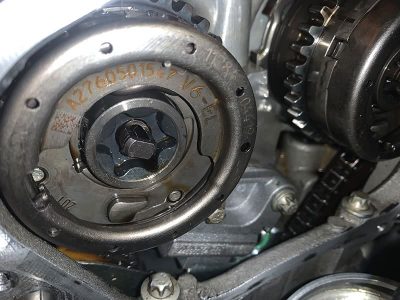
In the operation of camshaft adjustment, the valve timing is changed by rotation of the camshaft, thereby producing a valve overlap. The camshaft can be rotated in the “advanced” or “retarded” direction while the valve lift remains constant. The camshaft is rotated via camshaft positioners at the power-transmitting ends of the camshaft. The camshaft positioner sets the camshafts with regard to the crank angle, thereby enabling a valve overlap during gas exchange. This looks quite similar to what you’re used to in other modern Mercedes-Benz engines.
The camshaft adjustment is performed by the engine control unit, depending on the engine speed and engine oil temperature. Application of the adjustment of the exhaust camshaft does not occur until a higher engine speed as compared to the intake camshaft. This ensures that the lock position is still reached on the exhaust stroke against the retarded reaction moments of the camshaft even when the oil pressure is low. There is a return spring located for support in each camshaft positioner. If both camshafts are adjusted, adjustment of the exhaust camshaft takes place after a delay. This prevents oil supply problems and ensures a reliable functioning of the locking mechanism.
XENTRY Tips
Despite being in the market for a few years, there are relatively few service bulletins so far regarding the M264. XENTRY Tips document LI54.30-P-073761 points out some potential problems with the oil level indicator in the instrument cluster: The oil level is not correctly displayed while the instrument cluster display is in workshop mode, or the oil level is reported in an inverted fashion when a correction is carried out (e.g. instead of an instruction to increase the oil quantity, an instruction to reduce the oil level is displayed, or vice versa). The remedy calls for an update to the instrument cluster control unit (N133/1) software using XENTRY Diagnosis.
Service and Maintenance
So far, we know of few reported problems with the M260/264, but time will tell as they get more miles on them and you start to see more of them in the shop. For now, routine A and B services are the norm. Oil service is fairly straightforward as well. Similar to most Mercedes-Benz service, you will need to remove the oil filter cartridge, gaining access by removing some intake ducting. Allow the oil to drain properly from the canister housing into the sump and then lift the vehicle.
It’s always a good idea to remove all three underpanels and not just the middle one to gain access to the drain plug, so that you can give the vehicle a good inspection. As we’ve said many times before, your customers depend on your technical expertise to spot potential problems before they affect the vehicle’s operation. Not to mention, most customers will thank you for recommending a needed repair that you’ve identified.
Introducing the M254
After only three years, the engineers developed a ‘third generation’ engine if you will: The new M254 engine is a longitudinally-mounted four-cylinder in-line spark-ignition engine also direct injection. The engine is turbocharged by means of an exhaust gas turbocharger with a switchable flow connection. The 2nd-generation integrated starter-alternator (ISG) can deliver an additional 15 kW (20 HP) output for a short time (the ‘boost effect’).
The new M254 is characterized by intelligent thermal management. To ensure rapid heating of the catalytic converter, the exhaust system in the M254 is also installed directly on the engine, as in the M260/264. The catalytic converter is a two-box catalytic converter and is installed directly downstream of the exhaust gas turbocharger. The exhaust system is equipped with a new coated gasoline particulate filter (COPF) with a third lambda sensor.
The use of next-generation low-friction oils helps to ensure a friction-optimized engine. Also helping with friction loss, the cylinders are treated using Mercedes-Benz NANOSLIDE technology: Twin-wire arc spraying is used to apply an extremely thin coating of an iron-carbon alloy to the inner surfaces of the cylinders in aluminum engine blocks. This produces a nano- to ultra-fine, highly wear-resistant material structure with microporosity. This microporosity ensures effective lubrication in operation. It means that the heavy cast-iron liners measuring several millimeters in thickness are replaced in aluminum cylinder blocks. The result is a mirror-smooth surface, with friction between piston, piston rings and cylinder wall reduced by up to 50 percent, along with weight savings of several kilograms.
Valve Train
The biggest difference you find between the M254 and M264 engines is that the M254 has the timing chain in the rear of the engine. Addressing the valve train is quite different in the M254 compared to the M264. Although they both use CAMTRONIC technology, if find yourself having to check the camshaft timing, the initial inspection and adjustment for the M264 is very similar to what you’re used to on the older M274/276 engines. To check the basic setting on both is similar, you remove the cam/hall sensors and rotate the engine to line up the marks. To make an adjustment, say after a repair, on the M264 engine you remove the cylinder head cover and install the hold down tools just like in the M274/276 engine. Then remove the camshaft positioners, remove the locking brackets and make your adjustment following the procedure in the Mercedes-Benz Workshop Information System (WIS).

The M254 Camshaft adjustment has a cam setting adjuster that locks the cams from the top without having to remove the cylinder head cover. A rear access cover allows removal of the camshaft adjusters with the aid of a special locking tool. If you plan to service these valve trains you’ll need to add some special tools to your arsenal and, as always, follow the procedures in WIS. Having the timing components in the rear may seem like a pain but they are engineered to last. If you do find you have to get into some deep timing chain repairs then you will find yourself pulling the engine.
There’s a new wrinkle in the oil service in M254 and other Mercedes-Benz models you may encounter: The oil drain plug is required to be replaced each time when changing the oil, so be sure to stock up so that you will have these on hand when needed. Instead of a tightening torque, you tighten it until it hits the stop.
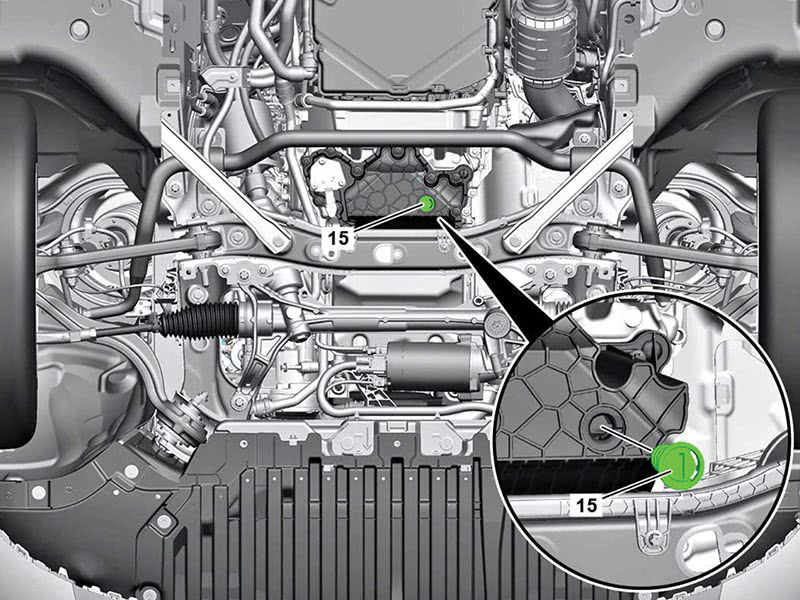
As these engines rack up the miles you will see more and more of them in your shop as time goes on. Do thorough inspections on the ones you do see in your shop and become as familiar with them as possible to stay ahead of the game. As always, knowing what to do and what to avoid leads to better shop efficiency, making everyone happy.
Good stuff!
this site is very helpful thank you