Mass airflow sensors rarely just die; they’re killed. By debris from or through the air filter. By deposits from bad gas. But the diagnostic problem is, they seldom die clean and quick. Instead, they tell lies until they’re caught and executed. They report false readings because of those contaminants. The computer has no reason to doubt a MAF sensor that’s always told the truth before, particularly if what it’s reporting now is within the range of plausible.
While the CEL in his ’93 400 SEL had been on for several years, the motorist couldn’t tell anything was different from the way the car ran. When he checked the oil, it didn’t show any more rapid consumption than before. When he asked a local shop about it, they pulled a code and reassured him, “That’s just your EGR. Don’t worry about it. The car will work fine anyway. We don’t have emissions inspections here.” The driver was reassured and drove with the lamp on. But after a year or so he moved to a more urban area, an area where they did have emissions inspections. However good a car you had and however well it ran, if your CEL was on, you weren’t going to get that little colored stickum square for the corner of your rear plate.
So he took the car to get the CEL turned off. Of course by that time, the EGR valve had seized in place. The frequent thermal cycles as the manifold warmed up and cooled down encouraged the growth of rust, which locked the valve permanently. It may have been nothing more than a porous vacuum hose to begin with, but leave things alone long enough, and new problems may spread to everything on the subsystem. While we’re talking about the EGR here, this is true for most other automotive systems as well, particularly those related to emissions controls.
A Bouquet of Trans Codes
Many people evidently cannot drive without snacking, and snacking means spilling. That may cause unpredictable problems, however, because it’s not clear what the effects on electrical contacts and connections in the gearshift console may be. Who knows what the resistance of sensor switch contact points soaked with Coca-Cola and then dried might be? Find a bouquet of transmission codes and the transmission locked in limp-home? Among your other tests, check to see whether there are any dried flakes of soft drink on the switch that tells the computer what the gearshift position is. So check the switch.
Wilts under Load
The car was a well-cared-for 126 with the 5.6-liter engine. It had always enjoyed careful maintenance and still looked showroom new. But, its owner reported, of late it lost power when you tried to accelerate. The car would always start easily, hot or cold. The engine could idle until the tank ran dry. There was no problem getting into gear or underway, until you opened the throttle. Then it would bog and stall.
The shop quickly found the fuel pressure, 70 to 80 psi. at idle, fell quickly to 50 when you opened the throttle. At that pressure, of course, insufficient fuel flows through the injectors, and the engine stops. The natural first step? Replace the fuel filter. It sounded just like a mostly clogged filter since enough fuel could flow for idle but not for load. Sawing the old one open to check was disappointing: There was no significant dirt, not enough to visibly clog the element. But there’s no harm in replacing a fuel filter, so on they went.
Next, they replaced the pressure regulator. This part is too expensive to use as a guess-and-hope diagnostic tool, but they had a spare on hand. There was nothing wrong with the original, it turned out. At least there was not much time spent in that SWAG-test.
You could hear and feel both fuel pumps (this system uses two, a ‘lift pump’ and a pressure pump), so that left the possibility something had clogged or crimped the in-tank pickup. This is not the easiest tank in the world to remove, nor the easiest to get back in once their inspection exonerated the pickup: There’s nothing there to pinch off fuel delivery.
So now the shop turned to a set of tests they realized they should have done earlier: pressure and volume. Pressure, as we saw above, was OK at crank and idle, but not at run. There’s no way to check volume during running, of course, but it seemed adequate with the line disconnected and routed into a graduated beaker.
Finally, they teed a pressure gauge between the tanks. The first pump, the ‘lift pump,’ put out a mere 5 psi., not nearly enough to keep the engine in business. Usually we think of the first pump as the quantity pump and the second as the pressure pump, but in fact, you won’t get enough of either if either pump has failed. Failure in a pump is not always electrical failure; in this case, the electric motor in the pump worked fine, but the impeller elements somehow did not move the gasoline along. Replacement of the worn-out rear pump restored the 126 to its usual order.
Checking Resistance under Load
Many electrical components change their current-draw properties under load, so a static measurement of resistance through the isolated circuit may be misleading: An imperfect connector on a radio circuit may have no detectable effect; the same condition on a starter circuit may leave the driver stranded. You need to check ground returns.
The best way is to measure voltage drop. This involves using volts to detect resistance. Set your multimeter to its lowest DC voltage scale and bridge each connection in sequence. Only the load itself should show any significant voltage drop (but remember a ballast resistor is a load). If you find more than a trace of voltage drop, that is a positive voltage reading, you’ve found excessive resistance. How much resistance? It doesn’t matter, more than may be compatible with proper electric function. Clean or replace that connector.
Stumbling Hunter
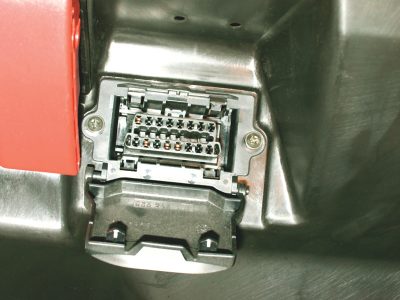
This one was a ’93 CE with the 3.2-liter engine. The problem occurred only at idle and only once the engine warmed up. At every other speed, there was no noticeable problem at all.
When cold, the engine idled steady as a rock at about 900 rpm, but once the coolant began to warm toward normal and the computer tried to lower the idle speed, it began to hunt, surging back and forth over several hundred rpm, nearly stalling at the bottom.There was an unhelpful code for fuel trim.
Fuel pressures were right, as were all the scope patterns for spark. You could hear some static on the radio, so the shop replaced the static suppression condenser, but that had no effect on how the engine idled (did get rid of the program static, of course).
They checked for vacuum leaks, though realizing afterwards that would only have increased idle speed, not necessarily made it hunt. Finally, they substituted a known-good MAF sensor, and the problem went away.
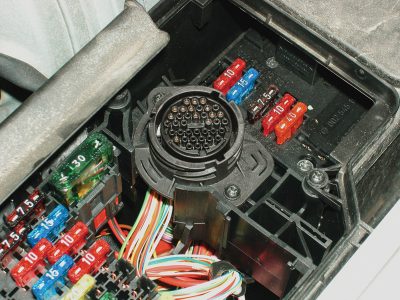
So what was going on? Why did the engine hunt for true idle when warm? Why did the computer think the problem was fuel trim? We’re in the realm of conjecture now, naturally, but let us know if you have a better guess. I think the MAF was contaminated but just barely, perhaps by something covering just a fraction of its surface. At most operational loads, this constant inaccuracy was so small the signal from the oxygen sensor was enough to correct for it. That was even, my conjecture continues, enough when the engine was cold and turning over relatively fast (there’s about twice as much air going through an engine at 900 rpm as at 600 factoring in friction and pumping losses).
But when the coolant warmed enough to drop the idle, the inaccuracy from the MAF sensor loomed proportionately larger, and the oxygen sensor was unable to correct beyond its range. That meant engine speed dropped as the MAF sensor thought there was less air going through and reduced the fuel volume, and then it picked up when the computer noticed the crankshaft speed was too low and opened the idle speed control. Of course, then the MAF inaccuracy went away and the mixture fell back within the oxygen sensor’s correction authority. Then the engine speed increased too much, and the computer closed the idle passage, repeating the hunting cycle. Got a better theory? Yours may be right, so tell us about it.
Misfire, Stalling, Hesitation Cold
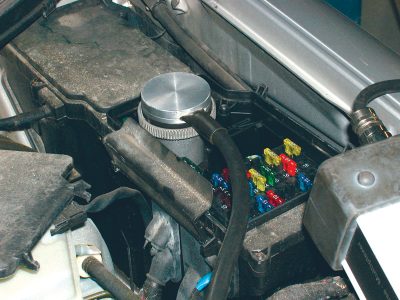
This particular car was a 1991 300 SL, but it could have been almost any other model or year once you know the problem. The customer used it infrequently, but for long trips when he did. So at first he ignored it when the engine ran a bit rough when first started up. After all, the car hadn’t been started in several weeks, he reasoned. It needed a bit of a run to get everything working properly again.
Well, that’s nonsense, of course. Either a car works properly or it doesn’t, and there’s no need to ‘circulate the juices’ or whatever. For a motorist to think so is one thing, but not for a professional mechanic. When it got to the shop, the pros there were not satisfied with that explanation. Unfortunately, there weren’t any codes, but the behavior of the engine started cold was consistent.
In this case, they made just the right spot-diagnosis: the coolant temperature sensor. Nothing else could cause those kinds of problems without preventing the engine from starting. Ordinarily, we expect to find a defective coolant sensor reading either direct continuity or an open circuit. But its repertoire of failure includes everything in between, and in particular, plausible but false readings. The computer has no independent source of temperature information to compare it against, so it will assume the CTS is right in the absence of clearly contradictory information. Often that’s enough to let the engine start but run poorly. Of course, once it’s warmed up the system will substitute other values for the temperature and let the engine run normally, sometimes but not always setting a code (depending on what the false reading was).
Smoke up the Shaft!
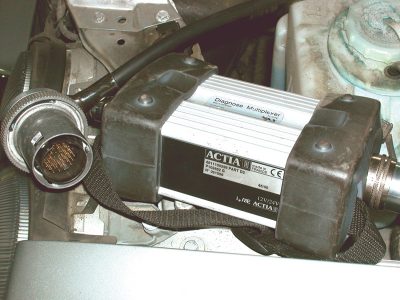
The car had come in with a ragged idle and an EGR code. Just a few days before, the shop had received its brand-new smoke machine to diagnose all the things related to vacuum leaks. They found a leak around the EGR valve shaft, so they ordered a new EGR valve and installed it. To their consternation, the new valve seeped smoke around the shaft, too! So they got another EGR, this time from the dealer. But it seeped smoke around the shaft, too!
There is no specification for testing smoke-machine smoke around the EGR valve. It has nothing more to do with rough idle than a misadjusted headlight might. In the absence of other ideas about how to solve a problem, it is not a reliable test to just roll up the latest piece of diagnostic equipment and see what you can do with it. Occasionally there are problems the carmaker did not anticipate, but these are seldom or very rarely to be discovered by random testing. If you have a ragged idle, go through the proper tests first. You could measure the resistance between the right front fender sheet metal and the rear bumper. You could check the headlight aim with the latest tool. What would those tests tell you about running problems? Nothing. Stick to tests relevant to the systems you’re working on.
CEL and EGR Codes
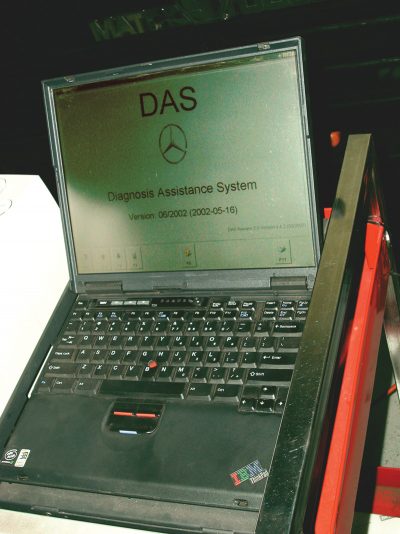
You have to wonder what happens to good EGR valves replaced by other good EGR valves. In any case, you know the replacement didn’t solve the CEL or other problem. When you have a code for an EGR valve or other good reason to suppose it’s not working properly, that does not mean the valve itself has failed. That is one of several possibilities, but not the only one. It’s at least as likely the EGR tube and passages have clogged with carbon, blocking the recirculation of exhaust gas. You can either ream these passages out with a steel cable frayed at one end or just replace them with new ones. The advantage of replacing them is the elimination of rough surfaces that will allow new carbon to deposit in the future, but just cleaning them will often work for a long time.
Misfire, Backfiring
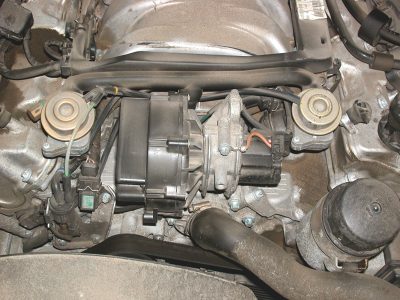
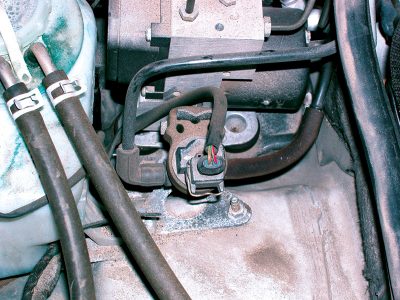
How can an engine have consistent and pronounced stumble, misfire and backfiring, yet show no codes and no peculiarities on the scope patterns, spark or fuel? That was the problem the shop had with a 1990 300 SE.
All the gravy work had already been done, and presumably paid for, at other shops. It had new filters everywhere, new wires, cap, rotor and wires. There were even new serpentine belts and tires, but the shop was reluctant to ask whether they had been an attempt to solve the problem. Blasting carb cleaner down the tube reduced the problem slightly as long as you kept up the spray, but there was no reason to doubt the fuel system. Besides the new filter, the pulsewidths were plausible and the volume and pressure were on the money. They suspected a bad EHA, but there was no difference in the way the engine ran with the EHA connected or not, other than the CEL that turned on.
When all else fails, as they say, go back to basics. If you were working on a 1965 car with the same symptoms, you’d check for fuel (which they had), for spark (which they had) and for compression (which they had). Then if you could get the engine running at all, you’d check for manifold vacuum, which they did. With cars sold all over the world and operated at all altitudes and climates, there’s no spec for that, but their reading was 12 in-Hg. They’d never seen an engine that ran with that kind of vacuum at idle.
A bit more testing led to the timing chain, which had worn enough to throw the camshafts out of time. You read sometimes about timing chains stretching. They don’t stretch, of course, because that’s not what happens to steel. But they wear at the pivot pins and might allow excessive slack, which is for practical purposes indistinguishable from stretch.
However subtle and complex automotive engines become, they are still cast metal and steel, and those parts are subject to wear. Diagnosis has to include the physical state of the engine if it is to discover all the problems that can occur.
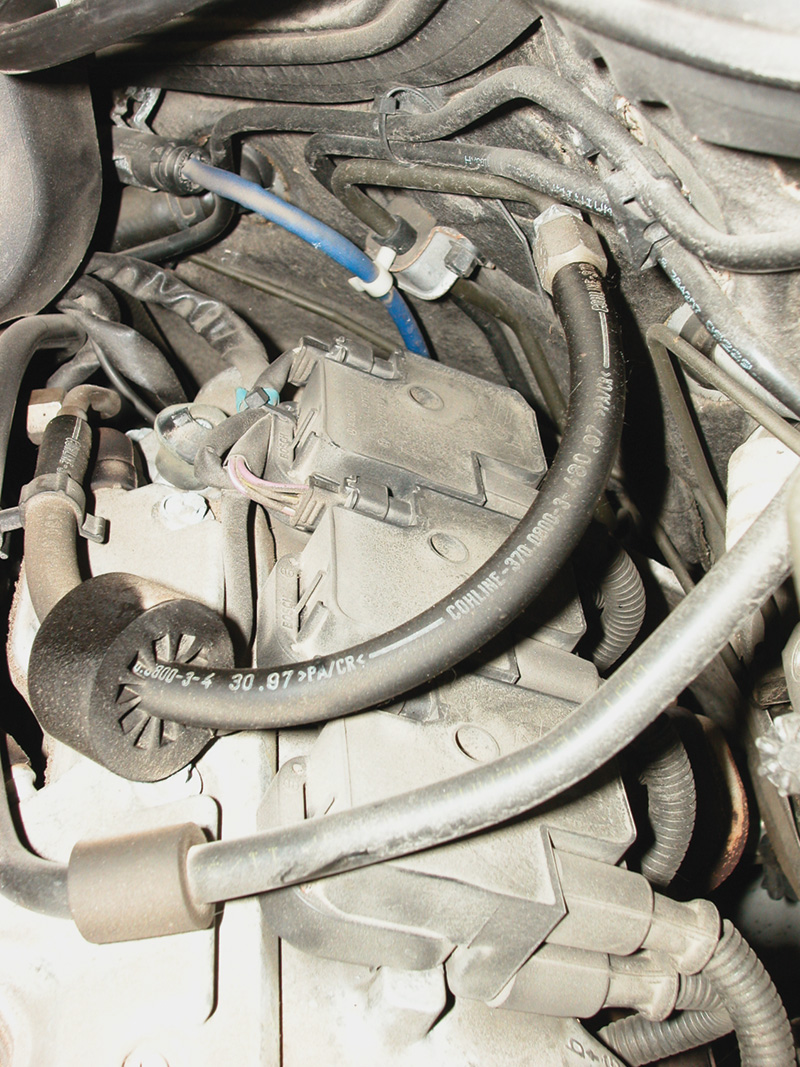
Plugged and Re-plugged, but!
This one didn’t fit the trouble-tree charts at all, nor did it set any codes, and you’ll understand why. The ’93 190 ran fine at all speeds but idle. It worked fine at idle for two or three seconds, after which the idle speed motor shut down and dropped idle to stall the engine.
The shop checked the crankshaft signal, which had to be there for the engine to run at any speed, but they wanted to see whether there was something odd about the trace. It was normal. The coolant temperature and the CTS signal were right on the money. So were the airflow signal, the oxygen sensor signal and everything else they could think to check, including voltage drops at grounds everywhere the engine management system worked. This was beginning to look like what the car needed was a new ECM.
But they knew from the owner, this car had made the rounds to different shops previously, not for this problem but for a high idle, solved by replacement of a non functional TPS. So they began looking it over for boners that may have been built in. There was nothing obvious, no golf tees in vacuum lines, no slabbed-off EGR valves. Oddly, unplugging the new TPS did not affect the idle speed. But the prospect of buying a new ECM that might prove unnecessary makes you very careful about your inspections, and eventually they found the problem. The connectors to the TPS and to the airflow position sensor had been inadvertently switched! Each of them uses the identical three-pin terminal, but the TPS circuit has four wires instead of the airflow position sensor’s three. Once the connectors were correctly attached, the idle problem was gone. The moral of the story? Always speak well of other shops, but check their work.
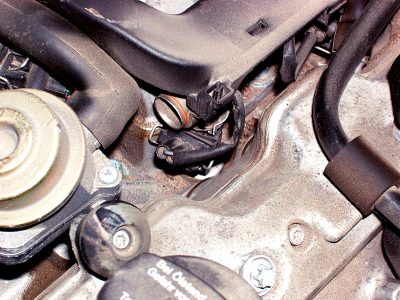
Scrambled Brains
The car, a ’93 300E, came in under its own power, but backfiring and running very poorly at any throttle setting. The motorist, however, wanted the charging system checked since his battery had gone completely dead overnight and he’d had to start the car with a jump.
The charging system was working perfectly, and once fully charged the battery held its charge. There was no continuing power drain, so the shop supposed the motorist must have left a door open or something else pulling a small current load. Poor running, however, proved much harder to solve.
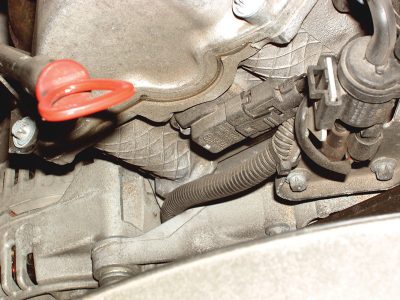
The CEL was on and there were many codes set, too many to be of any help. After recording them all and clearing them, the one that persisted was 13, oxygen sensor at lean/rich limit. When they checked the sensor, it went to full rich at idle and to full lean at every other throttle setting. The shop went over each of the sensors and each of the actuators, and everything was working properly. Realizing that if they had good information going in but bad information coming out, they realized this was one of those rare ones that really did need a new computer. But why?
Once the motorist returned he did explain that when he first hooked up the jumper cables, there was a big spark. So he turned the cables around and got the car started that way. He’d reversed the polarity, one of the best ways to scramble microprocessor brains. Evidently the reason it didn’t pop the fuse on the overvoltage protection relay was that the battery was discharged so much that the bulk of the current went through it rather than into the circuits, leaving just enough to fry the fuel control circuits but not enough to melt the fuse.
0 Comments