Everybody who remembers high school chemistry, raise your hand. No? Well, that’s not really surprising since knowledge of most of the principles involved isn’t used very often in the course of normal life.
That is, except for the chemical reaction that allows a lead-acid wet cell do what it does. This has been understood for a long, long time. In fact, the ancestor of the modern automotive battery predates the automobile itself. Gaston Plante, a French inventor, produced the first practical and rechargeable lead-acid battery in 1859 — that’s 27 years before the first real automobile (the Benz Patent Motorwagen of 1886). While Plante would surely recognize the modern battery, every aspect of performance has been studied and improved upon.
A quick recap of battery theory and anatomy will help you understand the changes that are going on. If two dissimilar metals are placed in an electrolyte that can attack them, voltage potential is created. Electrons will flow if a connection is made between the metals, and that’s what electricity is.
In a wet cell, the metals are sponge lead (Pb) and lead peroxide (PbO2), and the electrolyte is dilute sulfuric acid (H2SO4). The reaction begins as sulfate (SO4) breaks away from the acid and unites with the lead of both the positive and negative plates to form lead sulfate (PbSO4). The oxygen (O2) is thereby liberated from the lead peroxide and joins with the hydrogen (H2 what’s left over after the sulfate left the acid) to produce ordinary water (H2O), which dilutes the electrolyte. Eventually, both the plates turn into lead sulfate, the electrolyte becomes very weak, and current stops flowing.
But reversibility is the wet cell’s most important characteristic. When an outside power source pushes electrons through the cell in the opposite direction to that of discharge, sulfate separates from both plates to rejoin the hydrogen in the water, forming a new batch of sulfuric acid. The oxygen goes back to the positive plate to recreate lead peroxide, and the electrical potential is restored. If charging continues after all the sulfate has gone into the electrolyte, the water starts to decompose, releasing free hydrogen and oxygen, an explosive couple.
The traditional automotive battery has plates made of a combination of lead and antimony impregnated with the metals involved in the reaction. The positive plates are separated from the negatives by sheets of porous material that insulates them electrically from each other, but allows the electrolyte to pass (although such things as balsa wood have been used, sealing the positive plates in plastic envelopes is commonly done today to keep the active material in place that had previously been allowed to drop piece by piece into the space under the elements, lowering the cell’s capacity and sometimes shorting out the plates). Numerous plates of each metal are interlaced within one cell, but whether two or a dozen are used the cell produces a “pressure” of 2.1 volts. Six cells are connected in series to give the 12.6 volts almost all cars have needed since the fifties.
Computer designed radial grids, thinner plates, and other refinements greatly increase the energy density of modern batteries. To illustrate, a typical old fashioned unit could deliver maybe ten cold cranking amps per pound, whereas a more highly evolved specimen might produce 18.
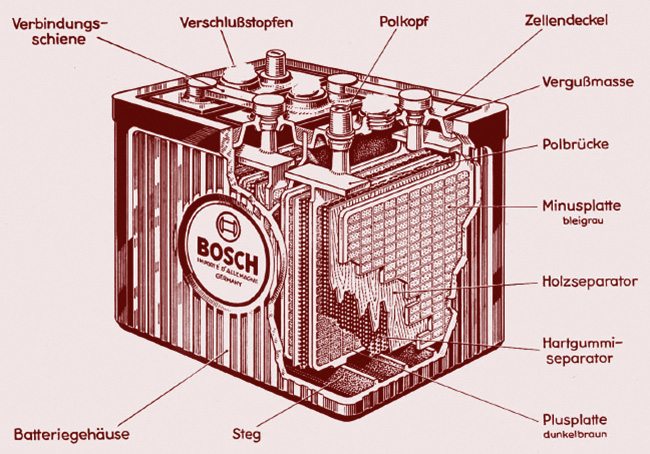
While the principles of the lead-acid wet cell battery have been known since 1859, designs and materials have sure changed. This old battery actually used porous wood for the plate separators.
A big change we’ll be seeing in the relatively near future is the adoption of 42-volt systems (that number refers to alternator output, but they can also be seen as 36-volt systems because they use 18 two-volt cells), something the Europeans are especially hot about.
Why tamper with a standard that’s been around for half a century? Lots of reasons. First, those flywheel-mounted combination starters/alternators you may have heard about allow such quick, quiet starting that the engine can be shut down any time you come to a stop, which will save gas and cut pollution (no more idling in traffic jams), but they need plenty of voltage to do their job efficiently. Then there’s the idea of using electric motors to drive such things as A/C compressors and rack & pinion steering gears, and that’ll draw lots of power. Instead of resorting to gigantic cables to deliver sufficient amperage, increased voltage can be enlisted. Another possibility is solenoid-actuated engine valves, which concept will also require more moxie than 12 volts can offer. Of course, this will put a whole new spin on service safety. Nobody ever minded a 12 volt shock very much, but 42 will be another story.
Finally, are there any new combinations of active materials (called “couples” in the industry) that show promise as a practical replacement for lead acid? In a word, no. As one of the battery engineers we interviewed for this section puts it, “I don’t think we’ll see a switch from lead acid. Its cost is low relative to any other couple, nicad for instance. And lead acid is eminently recyclable.“
0 Comments