We’ve all seen it: Rotors down to throw-away thickness at relatively low mileage. Why it happens, what you can do to mitigate it, how it’s related to pedal pulsation, and why you should buy O.E. Also, a profoundly basic trend that flies in the face of traditional auto service practices
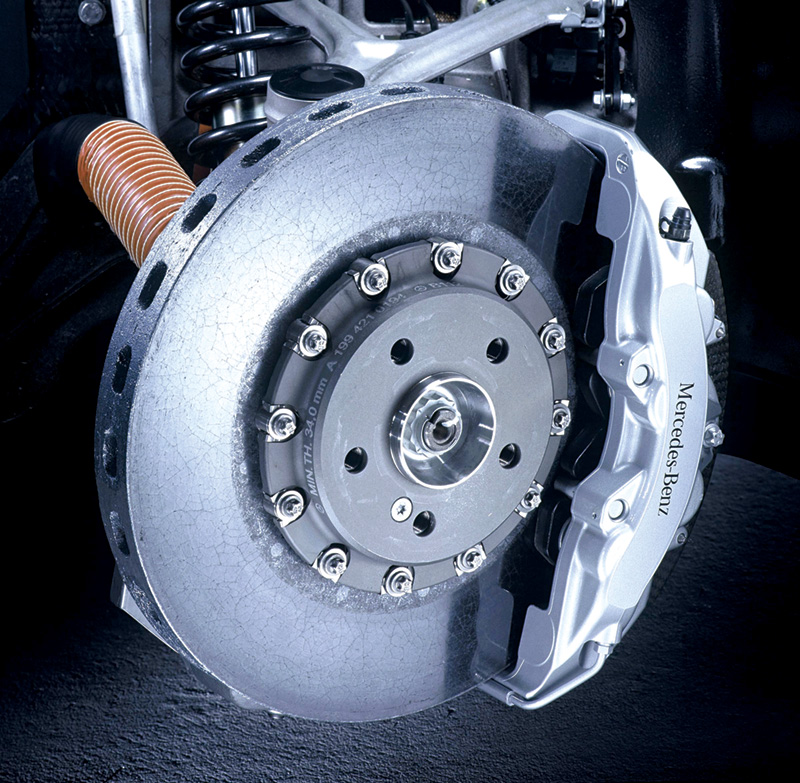
This is the kind of super high-performance brake you’ll be seeing from Mercedes-Benz in the future. You won’t be putting that futuristic rotor on your nasty old lathe, will you?
We’ve all seen it: Rotors down to throw-away thickness at relatively low mileage. Why it happens, what you can do to mitigate it, how it’s related to pedal pulsation, and why you should buy O.E. Also, a profoundly basic trend that flies in the face of traditional auto service practices
While most systems of modern automobiles are becoming more dependable and durable every year, brakes are still giving us as many opportunities for service and repair as ever. More, actually, because of numerous evolutionary factors, which we’ll explain.
Genesis
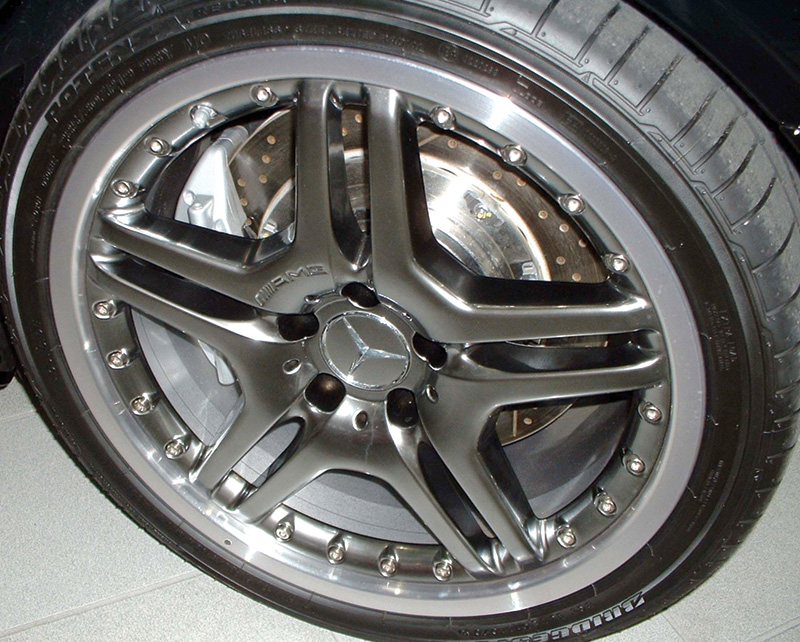
It would be foolish to use outmoded service procedures on something as highly-evolved as this AMG disc brake and wheel assembly. Your policy should be quality and careful craftsmanship above all other considerations.
The whole thing started back in the 1970s with the energy crises, which pushed automotive engineers into ambitious weight-reduction programs. Eliminating drag, both mechanical and aerodynamic, was another hotly-pursued quest — we got overdrive and streamlining, among other things.
So, we went from heavily-built, boxy cars that slowed down when you took your foot off the gas to lithe, aerodynamic vehicles that not only coasted forever, but also blocked air flow to the brakes. Throw in 70-mph speed limits and you can see that we’ve got what amounts to a continuing challenge.
Compare the brakes on a twenty-something-year-old car to those of a recent specimen, any of which (especially a Mercedes-Benz) would certainly be considered a high-performance vehicle by older standards. The vintage model used asbestos pads against massive well-ventilated discs with a large friction area and average surface temperatures of maybe 175 deg. C. (350 deg. F.), while the newer one has abrasive semi-metallic, NAO, or ceramic linings against thin rotors that reach twice that temperature at the slightest provocation. Aggressive friction recipes and all that heat in a slender little rotor can obviously contribute to wear and warpage. Why light rotors? Two reasons: To dissipate heat efficiently instead of holding it in a mass of iron like a Dutch oven, and to reduce unsprung weight, thus improving handling and ride.
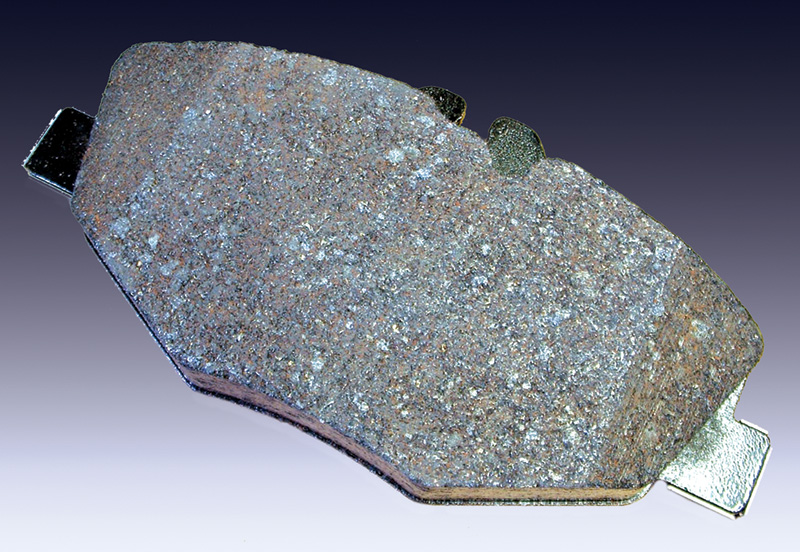
Friction materials have evolved to the point that they’re far superior to early semi-mets. This M-B O.E. recipe is the ultimate combination of performance, noise reduction and good wear characteristics.
If you’ve tended to blame accelerated wear on modern friction materials and have wondered why we can’t go back to asbestos, you can stop now. By law, the carmakers had to quit using asbestos in ’93 — nobody wanted to have that dangerous fibrous mineral around, either in a manufacturing plant or a service shop. But with smaller brakes doing more work, a new friction material was badly needed anyway, regulations aside. Asbestos had done a pretty good job for about 80 years — it was durable, cheap, and quiet. But it had a couple of drawbacks that were to spell its eventual demise. One, its use in certain circumstanses is linked to some forms of lung disease.
Two, its friction characteristics degrade in really severe service resulting in the scary phenomenon you probably know of as “fade.”
So, we got semi mets. Initially, these were steel wool, iron powder, and other metal particles molded together with a phenolic resin binder, which handled heat well, and in most cases gave quite long service. Early semi met recipes, however, had big problems with noise and tended to eat rotors. But today’s formulas, especially those so painstakingly researched by Mercedes-Benz engineers, are vastly improved in every aspect. To achieve high-performance braking, the friction material and the metallurgy of the disc must be matched to the application. The trick is in balancing lining and rotor wear against stopping power and pedal feel, and compromises come at the expense of wear, which is just as it should be. Still, there’s no denying that modern friction materials do take a toll of discs more severe than asbestos would.
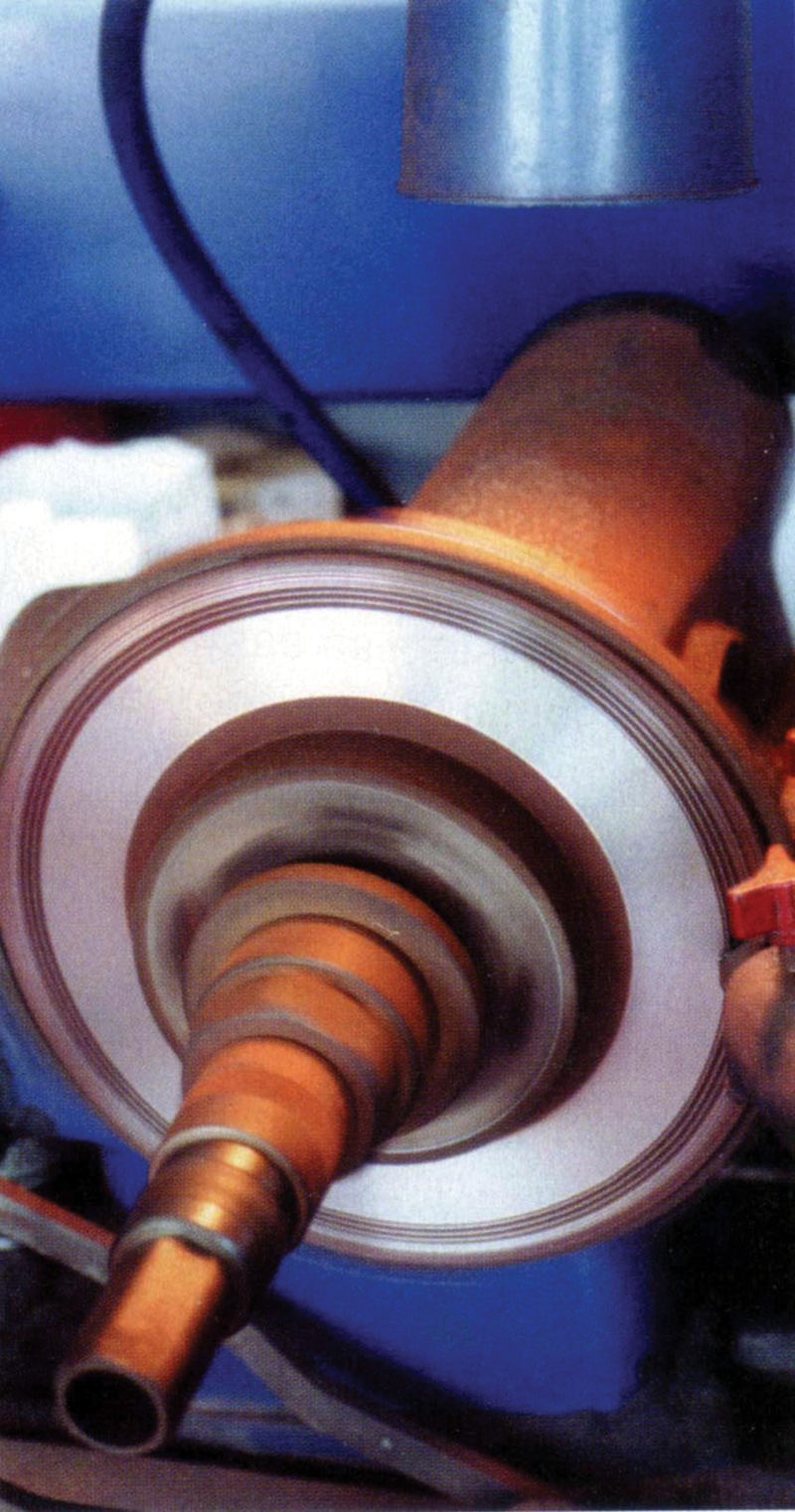
Not that many years ago, every shop in the galaxy turned rotors as S.O.P. at reline. Not anymore. As one M-B service manager says, “Our brake lathe went into the trash.” Replacement is becoming the rule.
Bye bye brake lathe
Now for the earthshaking trend we mentioned in the opening paragraph. A lot of editorial space in trade magazines has been devoted to the proper methods of achieving the smoothest possible disc surface on a brake lathe. You were supposed to use premium carbide bits, keep them well dressed and use a slow feed rate. Also, you were admonished to use abrasives to knock down the relatively rough directional finish that’s left by the lathe to achieve a 40 60 RMS/36-55 RA (for those of you used to the Roughness Average scale, the conversion is RMS = RA X 1.11) non-directional swirl.
Guess what? None of that matters anymore — you can just put it all out of your mind to make room for something else. As one M-B service manager says, “Our brake lathe went into the trash.” Yup, fewer and fewer professionals in the auto service business are machining discs. They’ve sworn it off in favor of buying new ones. Now that’s a profound change considering that it wasn’t that long ago when it was standard operating procedure to automatically turn rotors on a lathe during a reline (providing they weren’t down to their legal throw-away thickness). A successful Mercedes-Benz specialist puts it this way, “We’ve gotten rid of our brake lathe. The tolerances on late models are so close, any appreciable wear demands that the rotors be replaced.” Also, new discs will be extra insurance against a recurrence of a pulsation complaint simply because they haven’t been cut, so are thicker.
DiplomacySo replacement is becoming the rule. Besides being fast, it amounts to a profitable parts sale for the shop. But how do you choose among the available options? Do you try to save the customer a few dollars, or would you rather feel confident that the job won’t come back to haunt you?
Here, we bump into a delicate diplomatic situation. Suppose you replaced a regular customer’s rotors with the proper O.E. units at the last reline. Now, he’s been driving a lot and he’s worn out his pads in a relatively short period of time. You’ve wisely adopted the no-cut policy, but there’s still plenty of meat left on the existing discs to assure they won’t wear past the throwaway-thickness in the next cycle. You can’t help but feel that selling this loyal patron another new set of rotors after just, say, 40,000 miles might be perceived as excessive, even if he or she trusts you enough to bite the bullet. That, of course, puts an even heavier responsibility on you to do the right thing in this particular case. So, if there’s no evidence of pulsation, you might opt to just install new linings. While the notion of “hanging pads” might be offensive to your sense of craftsmanship, there are cases where it’s the only reasonable route. Just make sure you do it right so that you don’t generate a comeback.
Regardless of these occasional exceptions, the simple fact is that rotors aren’t as meaty as they once were, so you’ll be replacing them much more often than you used to.
Mercedes-Benz S-Class to Debut PRE-SAFE RadarAccident avoidance system has been shown in M-B studies to potentially reduce rear-enders by 75 percent When the next-generation Mercedes-Benz S-Class goes on sale in Europe this fall, the flagship sedan will be the first to feature a new version of PRE-SAFE, a revolutionary new safety system shown in Mercedes-Benz studies to potentially reduce rear-end collisions by up to 75%. The next evolution of Mercedes-Benz accident avoidance, PRE-SAFE uses two complementary radar frequencies to detect vehicles up ahead, warn of a likely impact and prime the braking system for faster response when the driver brakes the car. In addition, the front seat belts are tightened during the valuable time just before a possible impact, and the seats move to positions that can provide better protection – two measures that have been part of the current S-Class PRE-SAFE system since its debut in 2002. The latest version also closes the side windows to provide better support for the curtain air bags, and can inflate special front seat cushions that provide greater lateral support for occupants and help the side air bags provide even greater protection. The new PRE-SAFE is tightly integrated with the optional Distronic Plus system, which includes an enhanced version of the Mercedes-Benz Brake Assist system. Not only does it supply full-power braking assist in emergencies based on the speed by which the driver applies the brake pedal, as previously; Brake Assist Plus continuously measures the distance to the vehicle ahead and precisely modulates brake pressure if the driver doesn’t brake hard enough to come to a stop behind a decelerating vehicle at the available distance. During extensive testing, data recorders and video cameras documented more than 250,000 real-world miles covered by 200 drivers in the U.S. and Europe. 100 drivers participated in intense testing on the DaimlerChrysler driving simulator in Berlin, where rear end collisions were reduced by 75% in three different traffic scenarios with dense traffic. The newest PRE-SAFE system uses two different radar beams to scan traffic in front of the car. Newly developed short-range radar with a frequency of 24 gigahertz sweeps the first 33 yards in a fan-shaped 80-degree pattern, working in tandem with a narrower nine-degree beam of longer-range 77-gigahertz radar (already used for the car’s optional Distronic cruise control feature). The two radar frequencies complement each other to provide a full range of over 160 yards – more than one and a half football fields. The system can identify when the car is gaining too quickly to maintain the driver’s set following distance to vehicles with the Distronic system, and it decides whether or not to sound a warning, ready the brakes and trigger other PRE-SAFE measures. |
Pulsation frustration
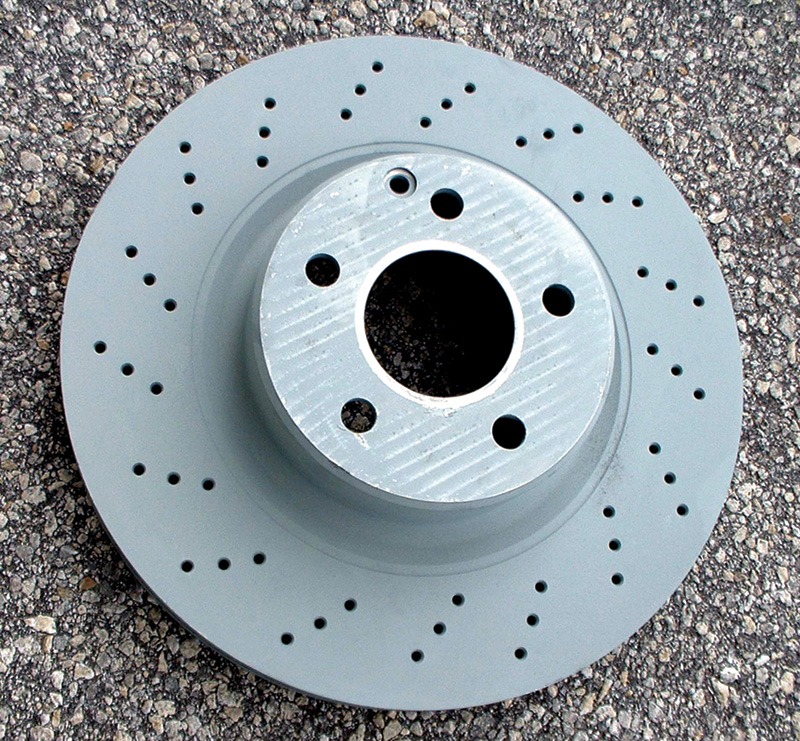
Nothing beats a genuine Mercedes-Benz O.E. rotor for avoiding comebacks and keeping your customers satisfied. By the way, don’t bother removing that gray anti-corrosion coating.
A topic intimately related to rotor wear is pedal pulsation, a condition that seems to continue to grow. It tends to repeat, too. The car may go out of your shop with nice, smooth braking action, but in a distressingly high percentage of cases, it shows up at your door again within a couple of months, and there’s a good chance its owner will have lost faith in your work.
There’s no doubt that, whether mild or violent, pulsation takes the fun out of driving an otherwise fine vehicle. Nobody likes bumpy braking, but you have got to understand it before you can cure it.
One expert gave us a theory about why pulsation problems increased when semi-metallics supplanted asbestos. He believes it is related to what happens when you stop at a light. By their very nature, semi-metallics conduct heat away from the rotor, whereas asbestos is nothing if not a good insulator. This was intended, but it has an unintended consequence: The area of the disc that is gripped by the pads cools faster than the metal around it, causing warpage. Another authority says, “A fundamental fact that many technicians do not realize is that semi metallics are designed primarily to get the heat out of the rotor.”
So, heat is the enemy and such things as sluggish pistons that don’t retract properly help keep that temperature up.
ÂThickness variation out of wobble
The direct cause of pulsation is DTV (Disc Thickness Variation), which can also be seen as a lack of parallelism between the two sides of a rotor. Wobble causes the rotor to wear unevenly as it hits those abrasive pads in one spot on each side every revolution of the wheel, and the contact areas will end up thinner than the rest of the disc. Some authorities claim that .002 in. of runout can cause about .0004 in. of DTV in 3,000 to 5,000 miles. Typically, thickness variation should be held to .0002 in., although we know brake exerts who say it’ll take .0004 to generate a complaint. Either way, you’re going to have to take your time checking for discrepancies this tiny — measure thickness at eight evenly-spaced points around the disc.
As a diagnostic preliminary, make sure the condition is indeed due to the friction components and not the result of a malfunctioning ABS. The module could misinterpret a bad signal from a damaged or contaminated wheel speed sensor to be a skidding tire, so may pulse the hydraulics. If you take the time to carefully experience the condition, however, your technician’s instincts should allow you to differentiate between the two.
Next, you’ve got to determine whether the pulses are coming from the front or the rear (or both). Commonly, DTV in the front will cause the steering wheel to rock or shudder on light brake applications at low speeds. You’ll feel the side-to-side movement if you hold the wheel with just a few fingers. If you work on vintage Mercedes with rear drum brakes, you can find out if the rears are at fault by finding an uncrowded street, coasting in neutral at about 20-25 mph, and applying the parking brake gradually. Out-of-round drums will typically produce a heavy bumping and hitching during this test.
Get the car safely up in the air, but don’t pull the wheels yet. Instead, measure runout on the inside of the rotor with the wheel installed and the lugs torqued, if possible. This will tip you off to real-world runout.
Not so flat
Besides ordinary runout, there’s disc flatness, the kind of warpage that makes the rotor resemble a potato chip. With your dial indicator, check for this at points 90 deg. apart and close to the outer edge of the wear surface. Find the high point and mark it “1,” rotate the disc one-quarter turn, mark it “2” and record the reading. Do the same thing twice more to establish points “3” and “4.” The difference between “1” and “3” will be max runout, whereas the biggest deviation from flatness will be between “1” and “2,” “2” and “3,” “3” and “4,” or “1” and “4.”
In the past we were told we could check for flatness with a straightedge and feeler gauges, but most authorities today say that’s apt to be inaccurate and misleading.
Everything we’ve mentioned so far applies to both front and rear discs. Since rears only account for 40% or less of stopping power, however, they won’t be the cause of as many complaints.
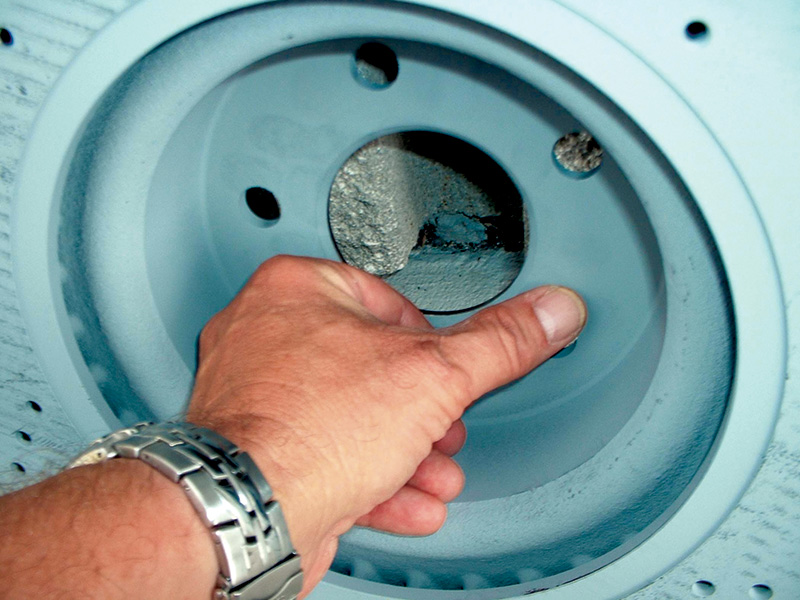
If you buy new O.E. discs, you won’t have to worry about getting the mounting surface perfectly clean. The hub is a different story, however. Take your time removing all corrosion so that the rotor will run as true as possible.
Don’t be a troublemaker
Sure, today’s brake systems are prone to problems for all the reasons stated earlier, but that doesn’t mean you shouldn’t do whatever you can to avoid aggravating the situation. In other words, don’t cause trouble.
This begins with what should be the simple matter of tightening the wheel lugs. This should always be done with a torque wrench, but we all know that just about everybody out there in the trenches of auto repair does it with a 1/2-inch-drive impact gun. Speed, you know. Shops that use a torque wrench typically have fewer comebacks for pedal pulsation (of course, they employ other careful procedures, too, which we’ll mention later).
As one veteran brake expert explains it, “What happens is you tighten the first lug to 90 ft. lbs., and that cocks the wheel. Then, you may tighten the second to 90 also, but the wedge effect makes the other one actually closer to 130, which puts an uneven strain on the rotor. After a couple of months, or 1,500 to 4,000 miles, the iron relaxes to match the stress, and you’ve got a pulsation problem. You can avoid this by installing the wheel and tightening the lugs while the car’s on the lift, lowering it, backing them each off half a turn, then torquing them.”
Good point, and we’ll add that you should use the proper tightening pattern, either star or criss-cross, depending on the number of lugs. Even more important, though, is anything that interferes with the trueness of the rotor mounting. For example, corrosion on the hub or axle flange that keeps the disc from seating properly, hence introducing runout. In our shop, we use our “whizzer” with abrasive discs and various powered wire brushes to get those flanges as clean as possible before mounting the rotor. If there was no pulsation problem and the disc is to be reused, we index a lug and the rotor “hat” with punch marks or paint so we can be sure to put it back in the same position.
It’s a worthwhile precaution to check runout whenever a new rotor is installed. If it’s less than .002 in., send the car out. If it’s anything more, remove the rotor, rotate it one lug, remount it, and check again. Keep doing
this until you arrive at the position with the least wobble.
Break ’em in, don’t burn ’em up
Some authorities say overlooking proper lining break-in is the Number One cause of noise and hard pedal complaints. As one brake expert tells us, “It’s not unusual to see a perfectly good brake job ruined in the first five minutes by improper break-in.” The ideal way to start new linings off is to make 30 slow stops (spaced two minutes apart) from about 30 mph using light to moderate pressure.
Obviously, no working tech is going to take that much time. But you’d be foolish not to make at least 10 moderate stops at 30 second intervals (you should be able to feel the action smooth out), then caution your patron to avoid heavy braking for the first 200 miles.
Miscellaneous
We’ll conclude with some random, but important, points:
- That gray anti-corrosion coating on new M-B O.E. rotors? You don’t have to waste any time removing it. It’ll disappear after just a few light stops during lining break-in, and leaves no harmful residue.
- Following the “no turn ’em” philosophy doesn’t relieve you of the responsibility of repacking wheel bearings and replacing the grease seal when a rotor is reused.
- Mercedes-Benz has made special “cleaning pads” available to improve the wear surface of rotors that are to be reused without taking a lot of meat off. You drive no more than 300 meters at 30 kph (roughly 300 yards at 20 mph) while repeatedly applying the brakes moderately.
- While Torque Sticks are a big improvement over just blowing those lugs on with your thermonuclear gun, a torque wrench is still superior.
- In that vein, some shops are using a 3/8-inch-drive air gun turned low to run the lugs up lightly, which won’t produce enough torque to cause warpage, then finishing with a torque wrench.
- It’s been found that overly hard friction material can amplify any variation in a disc to the point of unacceptable vibration. So, use only the best, meaning O.E., to avoid complaints.
- An Mercedes-Benz-approved brake paste applied to the hub and the mounting surface of the rotor will go a long way to prevent corrosion, and will also help heat dissipation.
- Dragging brakes will obviously result in overheated rotors. One cause is sluggish caliper pistons, another a clogged hose that lets psi into the cylinders under that substantial pedal pressure, but not out from the wimpy return force of the piston seal. Regular brake fluid changes can head off both.
- Never use aerosol brake cleaner to wash rotors or pad surfaces. We mean it. The thing that works best here (and is cheapest, too) is detergent and water applied with a scrub brush. That floats metal particles and other hard contaminants out of the pores. Thin, volatile solvents just make the iron absorb them.
Brake Assist Can Stop in 45% Less DistanceMercedes-Benz was the first automaker to make standard an electronic brake-assist system that can recognize emergency braking and automatically apply full-power brake force for shorter stopping distances. Called Brake Assist, the system is activated only in emergency braking situations and doesn’t affect normal brake operation. Brake Assist made its debut in model year 1998 on most Mercedes-Benz models. In tests on driving simulators and on the track, Mercedes-Benz safety researchers discovered that even experienced drivers may not apply full braking force in emergency situations. Although the reasons for this are unclear, the solution is relatively simple: use technology to design a system which can recognize emergency braking (whenever the pedal is being depressed very quickly), then react with split-second electronic speed to apply full brake assist force automatically. Tests showed that 99 percent of drivers were slow in applying the brakes, or only applied full brake pressure when it was too late. Mercedes-Benz researchers found that the new brake assist system can provide 45% shorter stopping distances for many drivers, and even most skilled drivers find about a 15% improvement. Most drivers during testing took 239 feet to stop a car from about 60 miles per hour, while cars equipped with the new Mercedes-Benz brake assist system came to a halt in just 131 feet. Even when drivers applied the brakes very late in an emergency, stopping distance was reduced by nearly 20 feet — more than a car length. The new Mercedes-Benz brake assist system can provide the critical difference between an accident and a close call because the electronic system can react far faster than any human can. Brake assist is a driver-adaptive system that learns each driver’s braking habits by using electronic sensors to monitor every movement of the brake pedal and feed information to a mini-computer. As a result, the system can instantly recognize when the driver pushes the brake pedal more quickly than normal. If it ever reads pedal speed signals that clearly mean an emergency, the computer instantly applies an electronic valve on the brake booster system for full braking assist. The Brake Assist system takes advantage of the benefits of the standard ABS, which prevents the wheels from locking up under braking. As soon as the driver eases up on the brake pedal, normal brake control resumes. To exchange important data at lightning speeds, the Mercedes-Benz brake assist system networks with other in-car micro-computers for ABS brakes, ASR traction control or ESP stability control, and the engine/transmission electronics. The system even processes information about vehicle speed, so it is definitely a fully integrated system. |
0 Comments