Fuel pumps are designed to go a long, long way, but many factors work against them. Pressure, current draw, and other tests will let you know how much life is left.

If the fuel pressure isn’t what it should be, you won’t get the carefully-engineered plume of atomized gasoline that assures high performance and low emissions (courtesy Bosch).
Unless you work on antiques, you haven’t seen a Mercedes-Benz with a carburetor and mechanical fuel pump for decades. That’s because the Stuttgart engineers had the foresight and intestinal fortitude to switch to fuel injection way back in the 1970s when that might’ve been considered a risky decision. With society’s growing environmental consciousness and worries over energy crises, however, that really was the right direction. So, Robert Bosch K-Jetronic continuous injection was adopted early on (at a local M-B specialist’s shop, we were just admiring a 1970 V8 coupe so equipped), followed in short order by L-Jetronic, LH-Jetronic and Motronic.
Regardless of the generation of fuel injection system involved, all use an electric fuel pump. Although it may seem hard to believe, we’ve heard people ask why we can’t have simple, old-fashioned mechanical pumps with fuel injection. While it wouldn’t be beyond mankind’s abilities to build a cam-driven pump that could produce sufficient pressure and volume, such a unit would take up valuable room under the hood and interfere with the design of the engine. And, unlike the situation with a carburetor and its built-in reservoir, injectors can’t supply any gasoline until the pressure’s up, so you’d have to crank for a while before the powerplant got enough fuel to start. There’d be no possibility of controlling it electronically, either.
In the days of carburetors, there was nothing subtle about fuel pressure. You either had enough to keep the bowl filled or not, period. No mysterious driveability issues were involved. Not anymore. Improper psi can cause all kinds of troubles that often get blamed on something else, much to the consternation of everybody involved. Symptoms include bucking on the highway, momentary cutting out, hesitation, low power, stalling at inopportune moments (typically, it’ll fire up again after it’s cooled off), and, of course, no-starts and hard starting.
Prelims
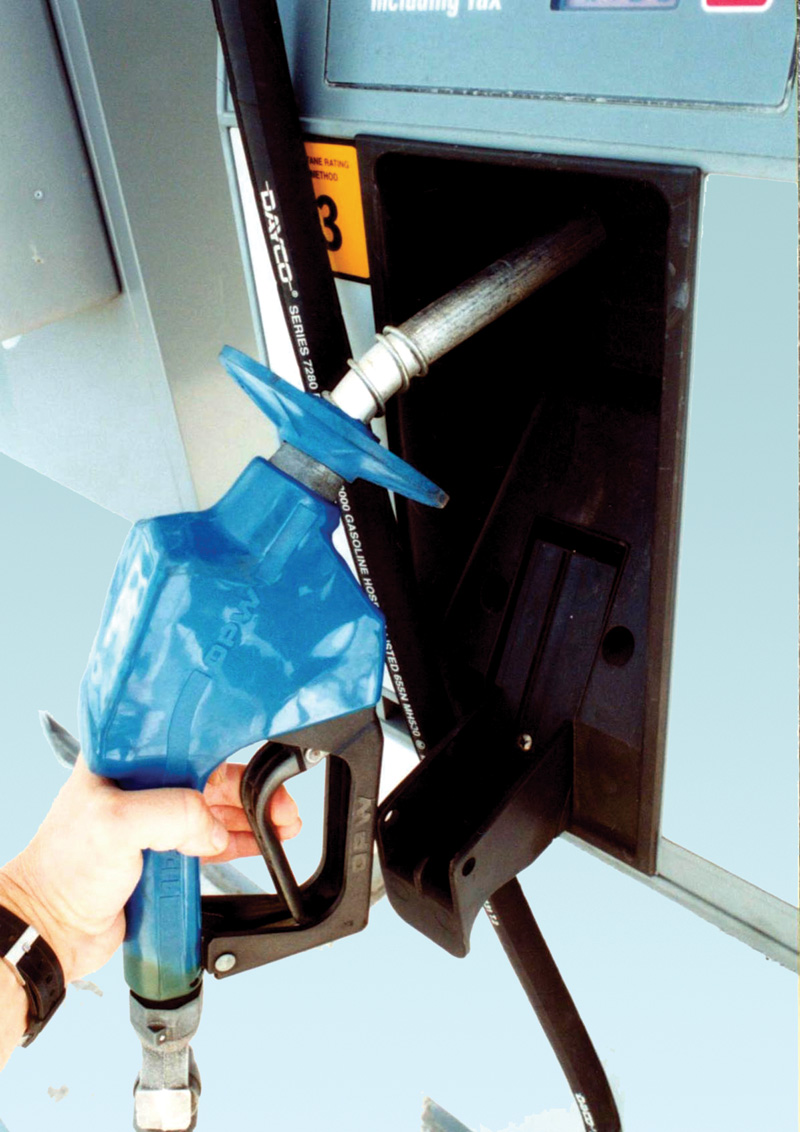
What, exactly, is being pumped into that tank? Certainly, there are some impurities, but some of the intentional additives may cause trouble, too.
High-pressure electric pumps come in three varieties: roller cell, gerotor, and turbine. The first type, which appeared at the outset of the era of fuel injection and continued for years and years, uses rollers in a notched rotor to catch gasoline and force it into a small-volume area of the housing. It has lots of moving parts and can be noisy. Gerotors use a different principle. Similar to an oil pump, they squeeze liquid by means of the eccentric action between a star-shaped rotor and a matching element that surrounds it. As for turbines, an engineer tells us, “The trend is toward the turbine-type fuel pump, both single- and dual-stage, mainly because there’s less noise. But there can be a noise complaint about turbines, too: Since they turn a lot faster, you could get a high-pitched whine.” They’re not good at handling any debris, by the way.
Regardless of the type, how long should we expect electric pumps to last? The engineer tells us, “We’ve been looking for a pump life of 10,000 hours [say, 400,000 miles]. That’s been our bogey. Now, we’ve been asked for life-of-car longevity. We’re building pumps with lower amperage draw, well-balanced armatures, and more compatible materials in the brushes and commutator to increase life.”
Well, that’s all admirable, but every technician knows that they simply don’t last anywhere near that long in most cases. In fact, we commonly see failures sometime before 150,000 miles, certainly not an especially long distance for a typical Mercedes-Benz to travel before retirement. What’s happening?
In a word, crud. You may have noticed that many of the fuel filters you replace are so jammed up you can’t blow through them. And if you checked the pump’s amperage draw (typically, this is easy to do at the relay) before removing the old filter, you might have seen up to twice the expected number — say, eight or ten instead of four to six. It shouldn’t take much of an intellectual leap to realize that a plugged fuel filter will make a pump work harder, and all that extra electricity will wipe out the brushes and groove the commutator, killing the pump prematurely. As the engineer put it, “Any time you add backpressure to the system, there’s going to be more arcing, heat, and wear.”
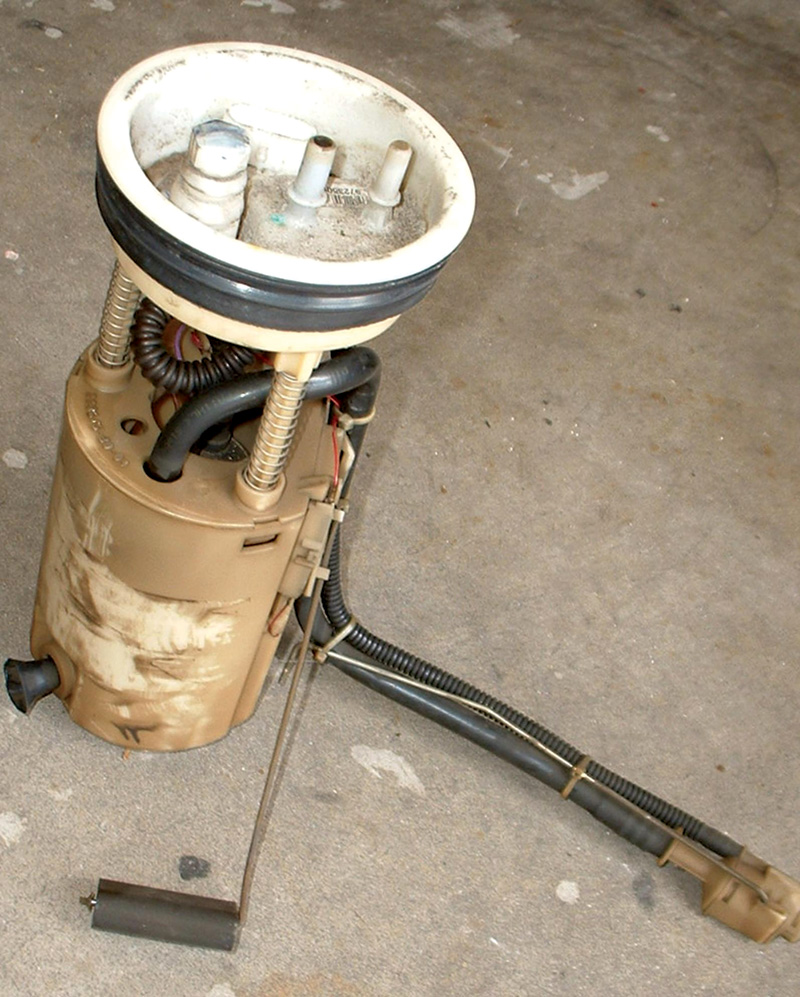
Late model Mercedes-Benz replacement pumps come assembled in a module, such as this M-Class specimen. That relieves you of the responsibility of putting all the parts back together so that there are no leaks past the strainer, and no unwanted contact between parts that can cause noise.
And here’s a suggestion that should help with customer relations: After you’ve replaced a fuel filter, it’s a good idea to open it up with a pipe cutter (a hacksaw will throw too many filings into the equation) and take a look at what’s inside. If you find lots of rust or other contamination, you can protect your standing with this patron by showing him or her the evidence, then recommending that the tank be removed and cleaned and the lines blown out. If he or she declines, make a big note on the repair order, and express the caution that filter replacement should be done regularly.
It goes in first
The idea that clogged filters ruin pumps may not come as a revelation to you, but a related statement from one fuel system service expert came as one to us: “Remember, whatever you find inside the fuel filter, the pump’s already had to eat.” Of course! But we’d just never thought of it that way.
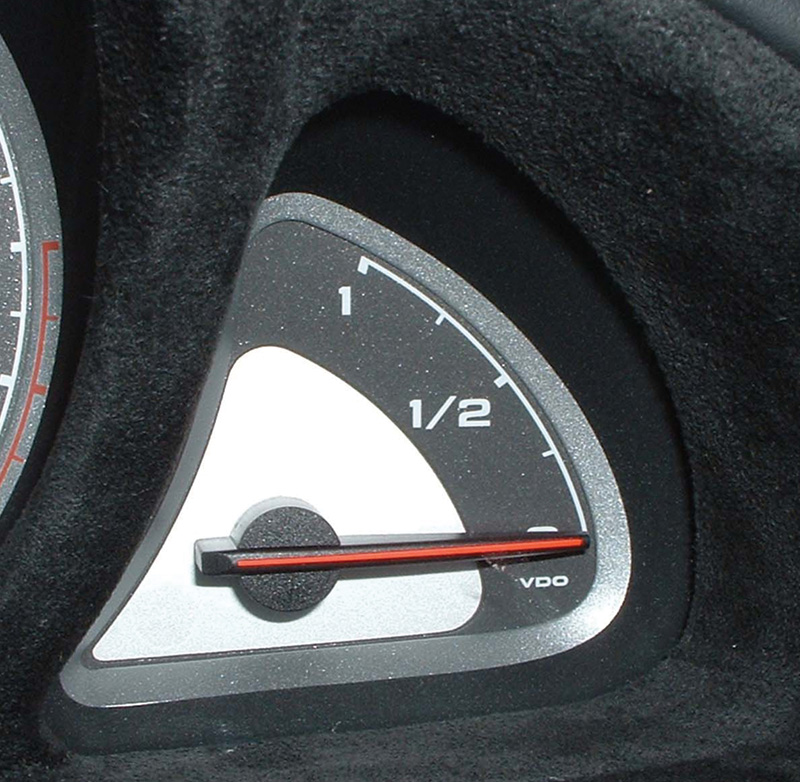
While it’s hard to prove that running on empty damages a fuel pump, it certainly can’t be doing it any good.
Do replacement pumps have problems, too? “Contamination is the biggest killer of fuel pumps, original or replacement,” says the engineer. “On replacements, typically because the strainer wasn’t properly installed so there’s no seal, leaving a pathway for debris to get in. Whenever you’re replacing a pump, be extremely careful of how the parts go together — read that instruction sheet.”
Another fuel system authority tells us, “The most common call I get is, ‘That new pump I installed is getting noisy.’ This is usually within three or four weeks. What’s happening is dirt and contamination are getting into the pump. On the gerotor type, it scuffs up the gears so they drag on each other causing vibration and noise. The turbine type won’t tolerate dirt at all.
“We have a lab guy who tests returned pumps, and he says that the biggest problem is strainers that aren’t installed properly. They’re either not pressed on all the way, or they’re crooked. This lets unstrained gasoline into the pump.”
This isn’t an issue with many late models because you have to buy the whole assembly or fuel pump module already put together.
It costs more, but it’ll be much faster and easier to install, and there will be less chance of a comeback.
But there’s more to this situation, such as the question of whether or not the tank needs to be removed and cleaned any time a pump is replaced. On this, our expert says, “I try to educate technicians that every time you replace a pump you should drop the tank and clean it out thoroughly (some people use steam). Put in fresh fuel. Dispose of the old stuff even if you have to take it home and use it in the lawn mower, but don’t put it back in the car because fine, silty stuff tends to stay in suspension.” What, exactly, is this troublesome debris? “I’m no chemist, but I suspect corrosive additives that clean injectors. What’s it doing to the rest of the system?” he tells us.
Dirt’s not the only reason pumps burn out, however. Immersion in gasoline is necessary for cooling, yet people run around on “E.” Although some engineers we’ve talked to dispute this, an expert who’s done a lot of real-world research on the subject has pretty much proved its truth to us. We don’t know if this is due to increased temperatures in the tank — after all, in a typical system (not the returnless type) the gasoline is circulated up and around that hot engine, and the more there is, the smaller the rise in degrees. Also, the silt mentioned above is going to be a lot more concentrated in three gallons than in 15. Suggest to your customers that they try to keep their tanks at least half full.
One pump specialist sums up the most common reasons pumps go away as follows: “The failures we see are brush wear, gerotor lock up from contamination, and check valve leak down.” The expert who did the research mentioned above sees it a little differently, saying, “The commutator becomes rough, which makes the brushes bounce. This oscillates the braided copper wires to the brushes, and eventually one of them breaks. So, that tiny little brush spring ends up carrying the current, a job it’s certainly not up to, and it quickly turns to charcoal. Thus, that becomes a dead spot. I’ve seen that burned up spring 99 times out of 100 failures.”
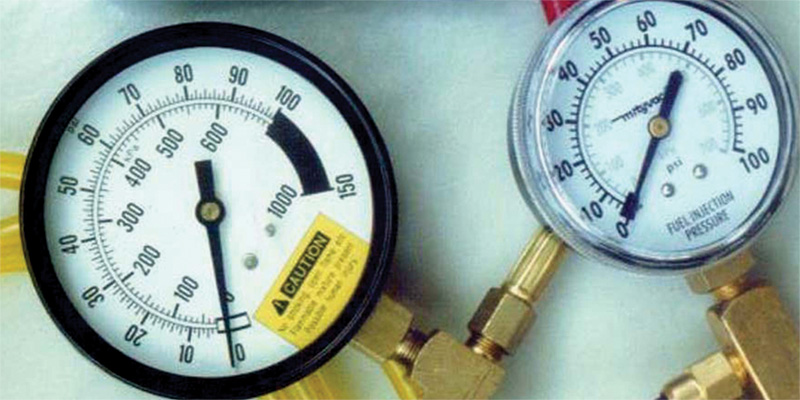
Nothing can tell you more about that pump as simply as reading the pressure it produces. How fast those psi come up is another telling factor.
Symptoms and testing
What are the symptoms of a failing pump, exactly? One fuel system authority says, “Typically, no-start after shut-down. You usually have some warning on the highway.” A veteran diagnostician and shop owner tells us, “The problems we see are mostly intermittent failures on the road. The car cuts out, bucks, then stalls. But it’ll often start again once it’s cooled off.”
Everybody in this business should know by now that checking fuel pressure is one of the requisite basics of performance troubleshooting, but we keep hearing that many of you out there don’t bother to do it for some inscrutable
reason. Get with it and your life will suddenly become easier as customer complaints become more comprehensible. As one seasoned veteran says, “If you don’t check pressure, you might start replacing sensors or the computer to fix the problem when the pump or a clogged filter or screen might be the real trouble.”
This is the ideal place to mention some troubleshooting reminders we’ve learned over the years:
- Take the time to check pressure accurately — a reading just a little below specs can cause driveability and power problems.
- You should see violent needle swings between dead head (return line clamped) and running pressures. A slow rise means trouble.
- Pull the pressure regulator’s vacuum hose and you should see a rise.
- Once you’re sure the hose to your gauge has all the air bled out of it, you should see that needle spring to attention almost instantly when you switch the key on. Once again, a slow pressure build points to a problem.
- Low pressure suggests not only a weak pump, but also a clogged filter or pick up sock, a crimped line, or resistance in the pump electrical circuit.
- Too many psi may be due to a restricted return line.
- Just because you’ve got specified pressure doesn’t mean there’s sufficient flow. Total system volume at the Schrader of one pint in 20 seconds will run any car. You’ll find cases where just opening your gauge set will kill the engine, yet the psi reading was fine.
- System leak down can cause hard starting, among other things. If psi won’t hold, pinch off the supply line. No change? Then the check ball in the pump isn’t the culprit. In cases where leak down disappears when the return line is pinched, the problem is a perforated diaphragm in the pressure regulator. If that doesn’t make a difference, you’ve got seepage through an injector.
- On a conventional fuel delivery system, a dirty inline filter will reduce fuel volume, reduce fuel pump rpm, and increase fuel pump current. This is because the plugged or restricted filter acts like a dead-head. On a returnless system, the restricted filter will have no effect on fuel pump speed or current, since these systems are always dead-headed anyway.
- A dirty pick up screen will reduce fuel volume, possibly increase fuel pump speed, and decrease fuel pump current, since it will cause pump cavitation. Either a conventional or a returnless system will react the same way since there’s no essential difference on the “suction” side.
Electrical issues
No or low pressure may mean the pump’s circuit is faulty. A bad control relay is a possibility, but check for poor connections before you think about new parts. Test for the presence of battery voltage at the pump’s positive terminal or wire, and keep in mind that a bad ground is a common cause of both no-starts and performance problems. As a pump engineer tells us, “A local shop had a car that ran intermittently. It would stop, then you could slam the door and it would start up again. That was a bad pump ground.”
Voltage-drop testing is the best way to locate high resistance. With the circuit powered up, use an accurate voltmeter to see if you get a reading across connections and lengths of wire. Anything more than about .2 volt (or, 200 millivolts) is too much.
If the pump won’t run at all, it’s natural to check the fuse or the fusible link. If it’s blown, and the car starts after you replace it, you should still find out how many amps it’s being forced to carry. Fixing high draw now may head off a future breakdown.
You’ll need either a low-reading analog ammeter or a DMM (Digital Multi-Meter) with sufficient current-carrying capacity. As we hope you know, amperage testing is done either by hooking up the meter in series with the load, or with an inductive pickup that you clamp around the wire. The latter works best with big current flow, such as you’d find in the starter circuit, so we prefer the former for diagnosing fuel pumps. That means you’ve got to break into the circuit. Connect one of the ammeter’s leads to the positive battery post and the other to the pump’s hot wire. Look this up in WIS (Workshop Information System, available at www.startekinfo.com). Ditto for the draw specs, but we will say that if you see anything over six amps with a mid-pressure system (45 psi), or 7 amps with a high-pressure version (60 psi) you’ve got a problem.
Leakorama
The fuel pressure regulator is a pretty simple device, but that’s no reason to overlook it. Whenever you see high emissions, some experts say to pull the vacuum hose off the fuel pressure regulator and look for gasoline. Diaphragms have been known to rupture — “I’ve had them come in with gas running out of the tailpipe!” one shop owner tells us. Although we’ve never seen it, we’ve heard that a diaphragm can rupture badly enough to fill cylinders with gasoline and cause hydraulic lock.
It’s fairly unusual to find a blockage in a line, whether from a crimp, dent, or big piece of debris, but it does happen. Identifying such a situation requires patience and lots of crawling around underneath with a good light and an inspection mirror. Speaking of lights, we should mention that more shops burn from droplight accidents than from anything else. Whenever you’re working around fuel, use only the fluorescent type.
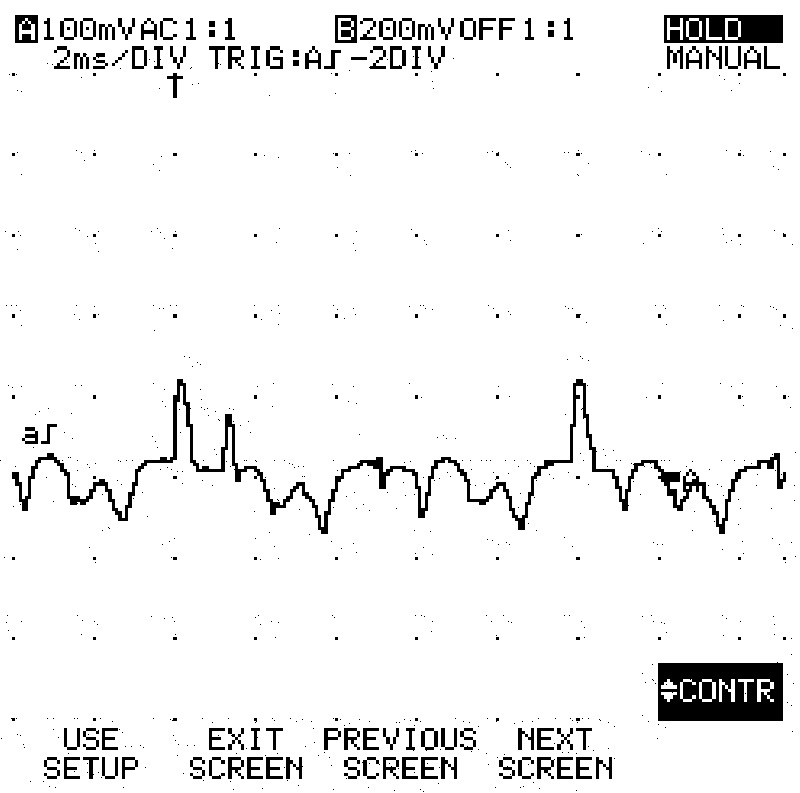
A lab scope will also display pump waveforms. No matter which you use, it takes some experience and experimentation to make the most of the current ramping procedure.
Can you predict the future with current ramping?
When we first heard that the concept of current ramping was being used as a way of judging the health of a fuel pump, we though it was going to be the next big thing in diagnostics. Just think of it: By taking a good look at the waveforms the electric motor generates, you can predict how much life that pump has left in it.
Well, not exactly. It turns out the reality isn’t so simple. Sure, it’s easy enough to tap into the circuit with a graphing multi-meter or a lab scope so that you can actually see the waveform, but interpreting it usually isn’t cut and dried. You really need to use exactly the same piece of equipment in exactly the same way over and over to collect a database, mental or otherwise, before you can be sure of what you’re looking at. Still, with a little comparative experience, it’ll help you nail down those elusive intermittents.
We’ll conclude with a safety note: Don’t even think about working on an electric fuel pump until you’ve disconnected the negative battery cable.
0 Comments