Practical stopping requires a friction recipe that’s just right
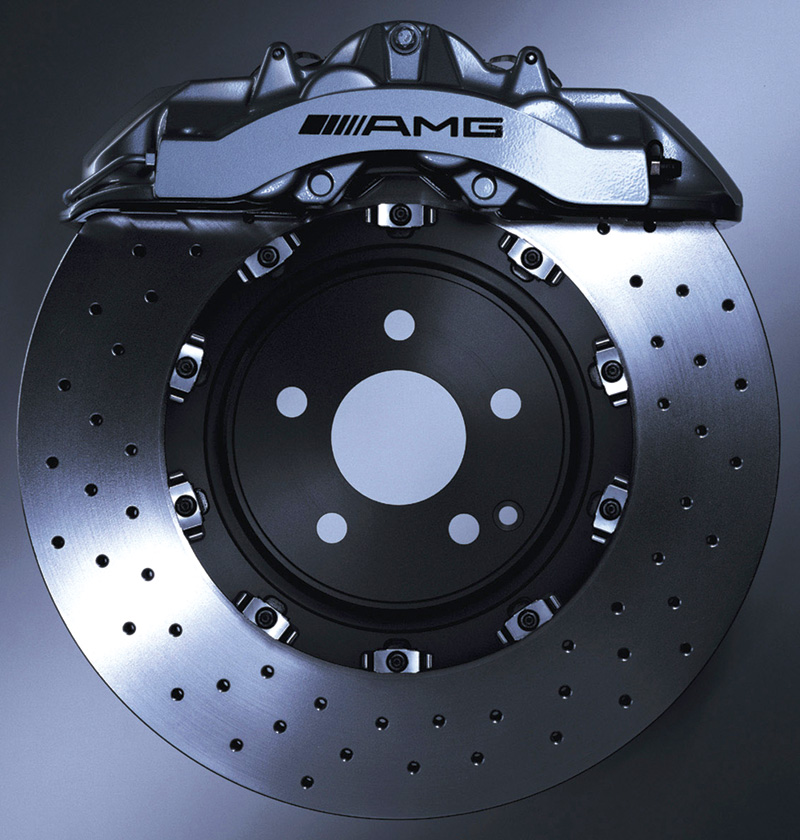
AMG, the official “tuner†for Mercedes-Benz, upgrades the brakes to match its power enhancements. A more aggressive pad is used with the modified brake system.
If you ignore those pesky things like controlling emissions, good fuel economy, and long-term durability, it is easy to select the right engine for a vehicle. If the goal is maximum speed, choose an engine that just keeps cranking out more and more horsepower as the revs continue to climb. On the other hand, an SUV that hauls a full load while towing a trailer needs an engine with lots of torque in the lower RPM range. Because most vehicles operate between the extremes of maximum speed and maximum torque, most engines offer a good balance of low-end torque with an acceptable level of horsepower.
Things are not as simple when you take your foot off the gas and depress the brake pedal. Brakes slow and stop a vehicle by converting the kinetic energy of motion to heat by creating friction. In scientific terms, friction is the resistance to motion, typically caused by the roughness or texture between two surfaces. The rougher the surface, the greater the friction, the smoother the surface, the less friction. On a disc brake system, the pad is the rough surface that presses against the relatively smooth face of the rotor.
Friction increases as the brake pedal is pressed harder. And as friction increases, more heat is created. This heat must be removed or it can cause the rotor and other parts of the brake system to distort.
The kinetic energy propelling 3,000 to 5,000 lbs., or more, of vehicle at highway speeds, or faster, must quickly be converted to heat by the friction between the brake pads and rotor. If the only thing that brakes had to do was stop the vehicle as quickly as possible, designing a brake system would be as easy as selecting an engine based on horsepower and torque. You simply formulate the hardest, most abrasive pads possible and have them bite into the toughest rotors you can make.
Of course, with those extremely aggressive pads and a tough rotor, every time the driver touched the brakes, he or she would have to put up with a screeching noise that makes fingernails on a chalkboard sound like a baby’s lullaby, clouds of dust clinging to the wheels, a pedal that requires abnormal leg strength to depress, and the expense of replacing pads and rotors every few weeks after they have mutually sacrificed each other to stop the vehicle. But drivers don’t ignore things such as noise, dust, pedal feel, and maintenance expense. As a result, a well-designed brake system must juggle many factors to reach an optimal balance of sometime conflicting requirements.
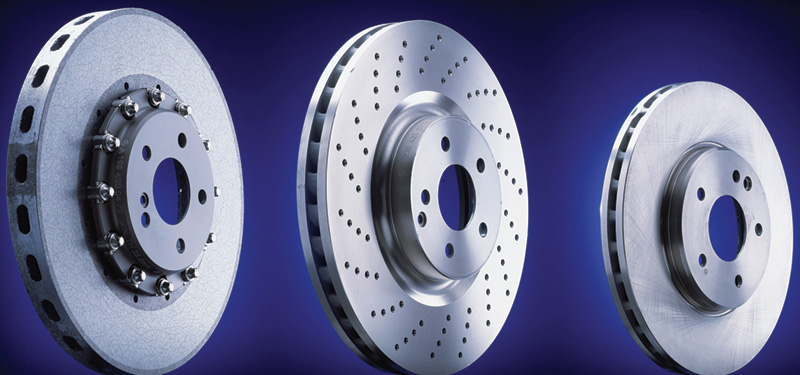
Different rotors are used for different applications. In terms of maximum stopping power, the most aggressive rotor is on the left, from the SLR McLaren, next is a SL 55 AMG rotor, and finally a rotor from an SLK 320.
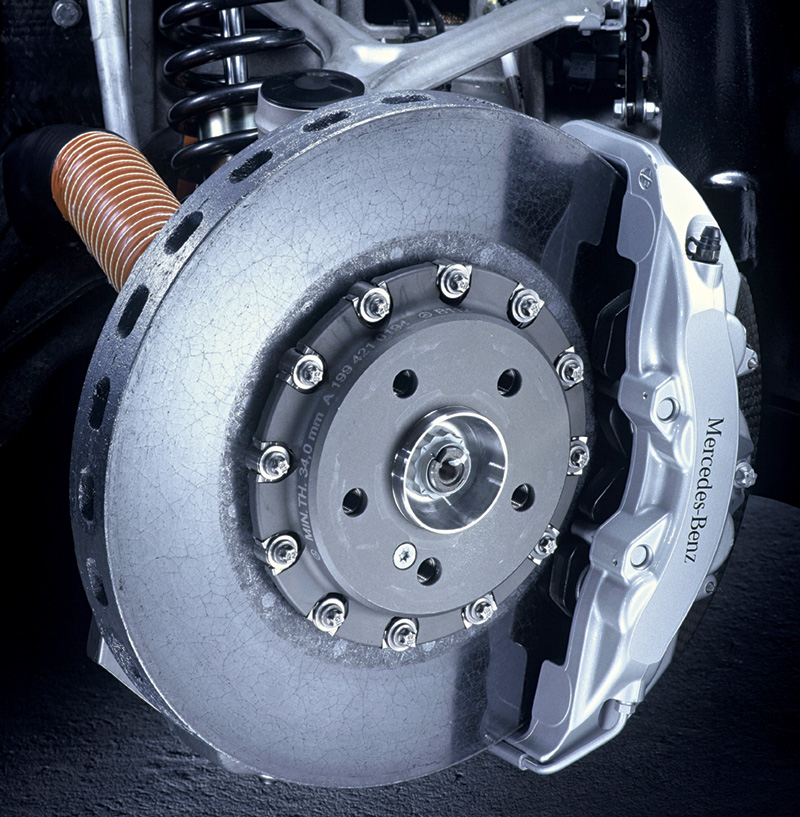
The pads and rotors in the SLR McLaren are the most aggressive brake setup Mercedes-Benz offers for street use.
Conflicting Demands
Although brakes are truly a system where everything must work together to perform properly, the composition of the pads gives engineers the greatest flexibility in terms of adjusting performance factors. Changing pad size and composition is much easier and less expensive than making similar changes to either the rotors or the calipers.
For optimal performance, pads are specifically designed for each type of vehicle. For example, the composition of the pads Mercedes-Benz developed for its small and lightweight C230 Sports Sedan is very different from that for the much larger and heavier GL450 SUV. And the pads for the C230 and GL450, in terms of design and composition, are distant cousins to the pads in the brake system of the ultra-high-performance SLR McLaren.
For quick stopping in a performance vehicle, or to stop a heavy SUV, the friction material in a brake pad must generate a large amount of friction. High friction means high heat, so the material must be able to either absorb a lot of heat energy or dissipate it quickly so the pad doesn’t distort.
Mercedes-Benz, like other carmakers, carefully guards its brake pad formulations as proprietary information, so we can only talk about pad formulations in general terms. The reason for keeping pad formulations confidential is simple. Mercedes-Benz has too much time, labor, and money invested in determining optimal pad composition for each of its vehicles to give away the information.
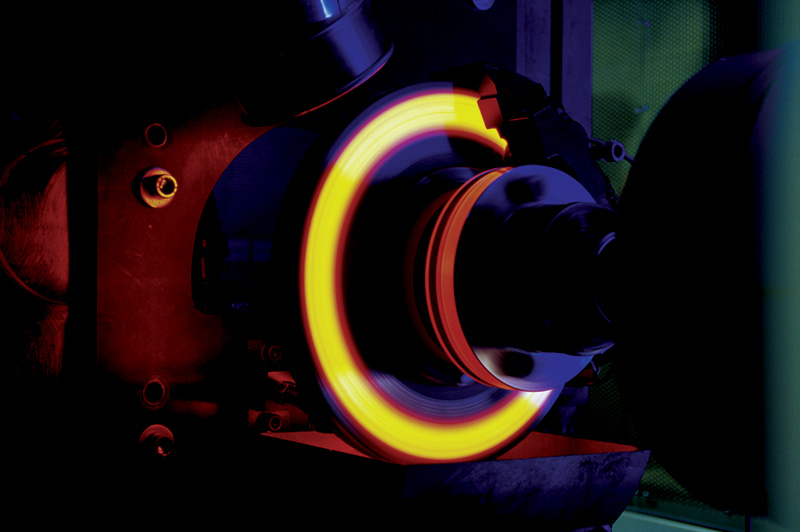
Under hard braking, the composite rotors in a SLR McLaren rotors glow. The pads must be specially formulated to deal with the high temperatures.
The main reason why you should always replace worn pads with genuine Mercedes-Benz parts is that the Mercedes replacements are the only pads that you know will have the exact formulation as the OE pads. Not even the premium brand aftermarket pads can claim to be “as good as†the OE formulation and the discount brands certainly are no match for Mercedes-Benz quality.
One of Mercedes-Benz’s leading brake engineers has several other reasons to always use Mercedes-Benz replacement pads:
- Genuine Mercedes-Benz pads not only match OE pads in performances and durability, the pad are “optimally configured†for the electronic control systems such as ABS, ASR, and ESP used by Mercedes.
- Mercedes-Benz replacement disc brake pads are fully compatible with all Mercedes-Benz vehicles.
- Because the replacement pads are made from the same top-quality material as the OE pads, the replacements have the same high level of mechanical strength, high thermal conductivity, and effective heat diffusion to minimize distortion and wear. In addition, the pads minimize noise and pedal pulsations.
Given the quality of Mercedes-Benz replacement pads, why risk the uncertainty of aftermarket brakes? For every vehicle, the Mercedes-Benz pads must satisfy requirements for performance, driver acceptance, and longevity. These factors are not equal and the importance assigned to each will vary by vehicle. The specific composition for a given pad will represent the best trade-off among performance, acceptance, and longevity for the application. For example, the demands on the C230’s brakes for performance are not as high as those for the SLR McLaren. The driver of a SLR McLaren will tolerate a lower level of longevity than the C230 owner in return for superior performance in terms of consistent stopping under repeated hard braking conditions.
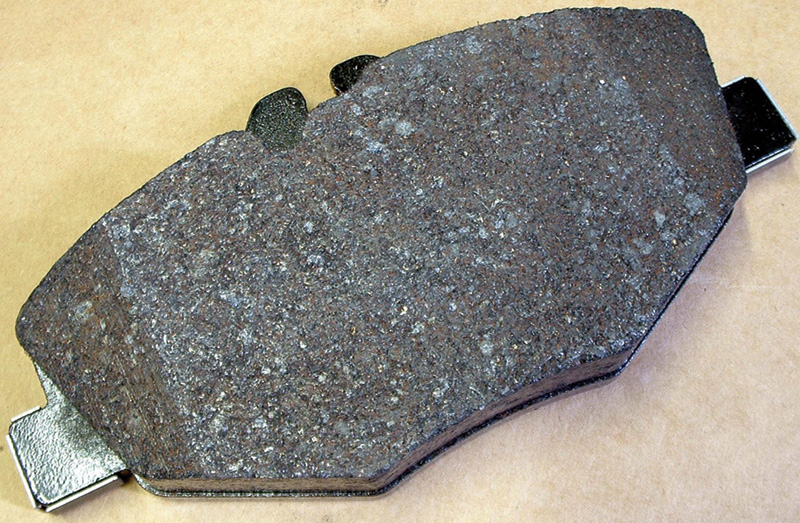
The color variations across the front of this Mercedes-Benz brake pad are caused by the different materials blended together to create the pad.
Performance standards are determined by the pad’s ability to:
- Maintain a consistent friction coefficient throughout the range of vehicle operating conditions.
- Resist compression under high pressure.
- Maintain dimensional stability.
- Avoid corrosion.
- Transfer heat energy to resist thermal distortion and changes in shear resistance.
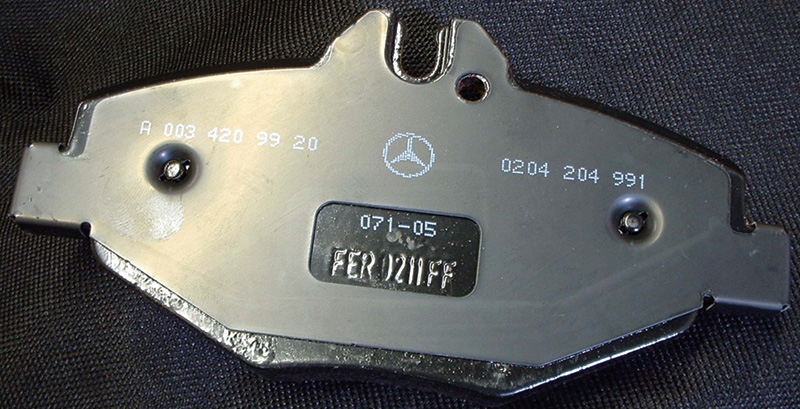
The three-point star logo and the part number on the metal backing plate show this is an authentic Mercedes-Benz replacement brake pad.
Driver acceptance is based on noise, dust, and harshness. Sound or noise is the result of pulsations or rapid changes in air pressure striking the ear. Whenever anything that is surrounded by air vibrates, it has the potential to cause a sound that the human ear can hear.
Preventing brake noise is complicated by the fact that other factors besides system design contribute to noise. Brakes that are quiet under certain conditions may be very noisy at other times because brake vibration is influenced by:
- Changes in brake fluid pressure on the brakes as pedal pressure varies.
- Temperature of the pads and disc.
- Vehicle/wheel speed.
- Atmospheric conditions.
Although it is virtually impossible to completely eliminate vibration in a brake system, as long as the vibration is low frequency, it is not objectionable. Based on various tests, if brake system vibration is less than 500 Hz, drivers and passengers simply cannot hear it. At 500 to 1500 Hz, occupants will hear a noise, but probably won’t recognize it as coming from the brakes. It is only when vibration exceeds 1500 Hz that it generally becomes loud enough and shrill enough to be objectionable. A properly formulated pad will do its share to reduce brake system noise by resisting vibration under the widest possible range of conditions.
Mercedes-Benz pads use a number of features to help reduce pad vibration, including:
- Special backing plates that resist corrosion and extend pad life.
- Chamfered, not squared, edges. The chamfer allows the pad to smoothly contact the rotor which reduces vibration between the pad and rotor.
- Vibration absorption material incorporated into the pad formulation.
All pads create dust. For most applications, engineers want a pad that generates as little dust as possible.
The third factor for good driver acceptance is “pedal feel.†An aggressive pad typically causes a stiff pedal and the driver may also complain of harshness. For all but performance applications, the Mercedes-Benz pads are designed to have a comfortable pedal feel with as little harshness as possible. A stiffer pedal is found, and is more acceptable, in pads intended for performance or competition driving.
Of course pedal feel refers to the hydraulic powered brake system that has been used by the automotive industry since the 1920s. The Mercedes-Benz “electro-hydraulic†brakes or Sensotronic brake system, introduced in 2003 on the SL roadsters and E-Class vehicles, changes the concept of “brake feel†at least as far as pressing the pedal is concerned. Depressing the pedal on this brake system activates an electronic signal and computer that regulates braking pressure. The system responds to not only how hard, but also how fast, a driver presses the pedal. Tied in with the antilock brake system (ABS), the computer regulates brake pressure at each wheel individually for maximum stopping power. A backup hydraulic master cylinder activates the brakes with consideralbly more leg force and pedal travel if the computer system malfunctions. With this system, the driver doesn’t “feel†the brakes as he or she would with a conventional hydraulic system.
The composition of the pad is a major factor for brake system longevity. A very aggressive pad will stop the vehicle quickly, but often at the expense of a short service life for both the pad and rotor. Relatively short pad and rotor life can be acceptable to a driver who demands maximum brake performance. It is not acceptable to a driver whose driving requirements are “typical.â€
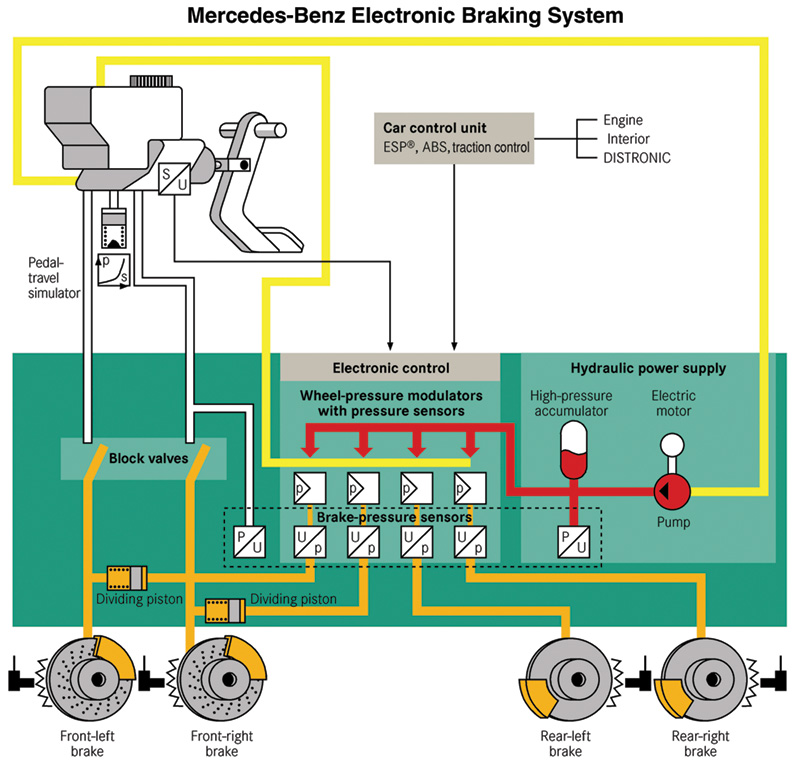
The “electro-hydraulic†brake uses sensors and a computer to regulate hydraulic brake pressure. The hydraulic system is a backup if the computer system malfunctions.
Friction Formulas
Brake pads are typically multi-layer. The friction material on the face contacts the rotor. Behind the friction material is a filler or intermediate layer. The final layer is the metal backing plate that is pushed on by the caliper piston. The contact between the friction layer and rotor creates the friction that converts the energy of the vehicle’s motion to heat, which must then be dissipated to the atmosphere.
For decades, Mercedes-Benz, like all carmakers, relied on asbestos as the primary friction material. Asbestos is an excellent friction material, except for two problems:
- Under repeated hard braking, asbestos will not dissipate heat quickly. The heat build-up in the pad causes distortion and “brake fade.â€
- Health concerns. Exposure to asbestos fibers has been linked to a fatal cancer, mesothe-lioma. Although there is still controversy regarding the risk of exposure to asbestos fibers from brake material, the automotive industry stopped using asbestos for a long time. Although asbestos is again permitted in automotive brake applications, its use is being discontinued, not by government edict, but because other materials are proving to be more effective.
Instead of asbestos, Mercedes-Benz pads are blended from several friction products, including:
- Non-asbestos organic (NAO) material that has outstanding performance in terms of reducing/eliminating noise, vibration, and dust.
- Semi-metallic components that offer excellent braking performance and fade resistance, but can be noisy. Semi-metallic pads have excellent brake life in high temperature applications.
- Ceramics are growing in use because they tend to be less abrasive, which extends pad and rotor life. The potential of ceramics has made them the fastest growing friction material in the automotive industry. Ceramics have excellent brake life in low or average temperature applications, which is why ceramics are popular for “average†driving applications. Ceramics are not recommended for vehicles that are used for towing.
In addition to the actual friction material, Mercedes-Benz pads are also formulated with fillers, friction adjustors, and other materials. The ratio of these different products varies by application.
More Than Just Pads
Because this article has focused on brake pads does not imply that just “hanging pads†is an acceptable practice for any brake service, especially for a Mercedes-Benz. As your customer’s trusted Mercedes-Benz technician, your brake jobs should always include:
- A complete inspection of the brake system.
- Measuring the rotors for runout and thickness. Rotors that fail to meet specifications have to be machined or replaced.
- Replacing rotors with any crack or other physical defect.
- Annual purging and replacement of the brake fluid.
- A road test after you finish the job.
0 Comments