Some technicians even consider a fuel pump to be a draft horse that just happens to share a stable with more exotic thoroughbreds like the injectors, ECU (Engine Control Unit), and the various sensors that provide input to regulate fuel flow. But let’s give fuel pumps some respect. Granted, fuel pump technology is not as sophisticated as that of some other components, but without the pump, nothing else works. As an experienced technician you have no doubt witnessed the gamut of fuel system component problems, and you know when a fuel pump can’t deliver, it’s game over, time to call the tow truck.
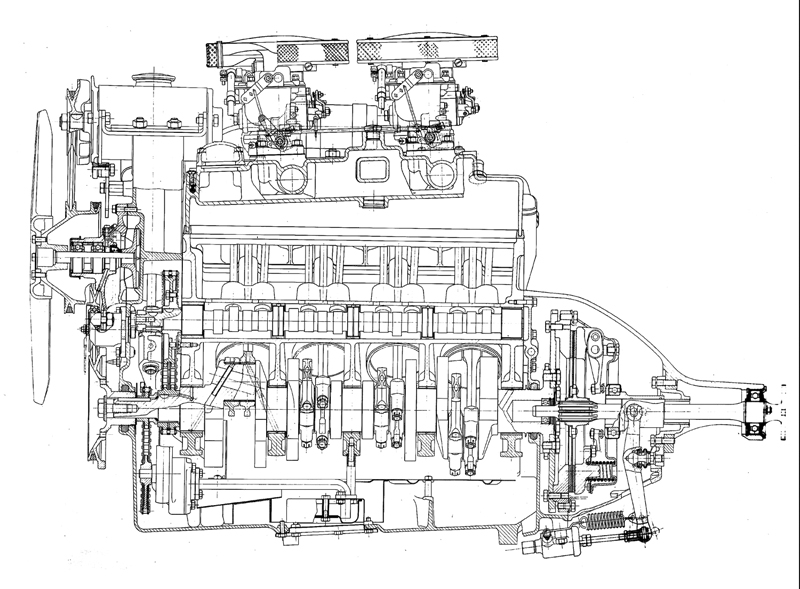
It was all so simple in the days of carburetors and mechanical pumps. Just a few psi would keep the bowl full, and diagnosis was a no-brainer.
Despite their somewhat lower stature in terms of sophisticated technology, fuel pump performance is impressive. Pumps are expected to immediately provide rated pressure the instant the ignition is turned on and to maintain that pressure as long as the engine is running. The design goal for most high quality pumps, like the ones used by BMW, is a service life of 10,000 hours or about 400,000 miles! That’s longer than just about any other electric/electronic component on the car. If you have to replace a fuel pump, remember that only a BMW pump, from a BMW dealer, is a sure thing to match the quality of the original unit. Aftermarket pumps may not be as good as BMW Original Parts and may cause installation and noise issues.
Another advantage of using only a genuine BMW replacement pump is that the new pump will exactly match the performance required for your customer’s car. To cut costs, many aftermarket pump manufacturers are following the path that the industry refers to as “parts consolidation.†Companies are reducing the total number of parts they make and distribute by offering a unit for multiple applications across several vehicle brands and models. This “one size fits all†or “one size fits many†approach may help to improve the parts maker’s bottom line. But this approach can result in a pump that you can’t be certain is an exact match to BMW’s original performance requirements. A pump that is off just a little on pressure and/or volume from BMW specs can cause all kinds of drivability and emission control problems.
Three Tips
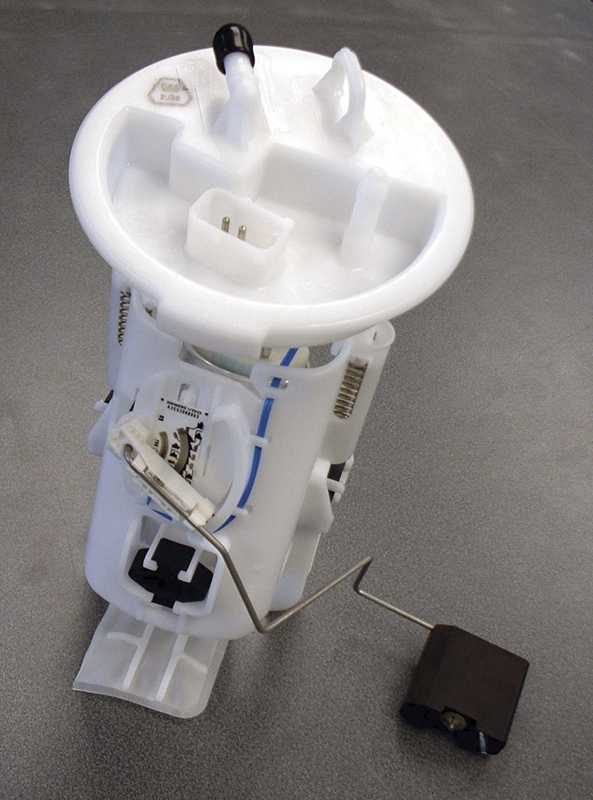
Quality electric fuel pumps, such as this genuine BMW replacement specimen, are designed to last just about forever, but all technicians know they wear out sooner or later.
It is a tribute to BMW’s quality standards that its fuel pumps, unless they have seen a lot of years and a lot of miles, seldom fail because of component wear or breakage. Pump failure is almost always caused by external problems. To maximize pump life, recommend that your customers follow three rules:
- Always buy reputable brand-name gasoline, preferably at a station(s) doing a fairly good volume of business. Contamination is a major cause of fuel system problems, including pump failure. Buying quality gasoline from a busy station reduces the risk of contamination. It is no guarantee against contamination, but it is the best your customers can do short of carrying a miniature laboratory in the trunk to test for contamination before each refueling.
- Buy gasoline often. A BMW fuel pump is lubricated and cooled by the gasoline in the tank. When the fuel level is close to empty, the pump can overheat. If a driver runs the tank close to empty too often, the overheating can cause pump failure. Tell your customers they should refuel when the tank is at or close to a quarter tank.
- Only buy gasoline. BMWs are not designed to run on ethanol (E85), methanol, or any other fuel that contains over 10% alcohol by volume.
Return/Returnless
For years, BMW has used a one-piece “saddle†fuel tank that straddles the drive shaft. The fuel pump is inside the right (passenger) section of the tank. All fuel delivery is done from the right side. The gasoline from the left half is drawn into the right side via a siphon tube that flows to the fuel pump.
Like all fuel-injected vehicles, BMW pumps are designed to provide more fuel, at higher pressure, than the injectors can handle. This assures that the injectors always have an adequate supply of fuel with plenty of pressure to deliver and properly atomize fuel to the engine. The excess capacity also permits the pump to continue providing an adequate volume at the required pressure even as pump capacity slowly deteriorates due to normal wear and tear over time.
The fuel pressure regulator valve controls the pressure delivered to the injectors. The pressure is regulated by returning excess or, to use BMW’s term, “displaced,†gasoline to the tank.
On early fuel injected BMWs, the pressure regulator and return line were part of the fuel rail. In recent years, BMW has converted to a “returnless†system to reduce the number of fuel lines and also to reduce potential gas vapor emissions. On a returnless system, the pressure regulator and fuel filter are incorporated in a single unit in the tank. The pressure regulator limits system pressure to the specified level. When the pressure exceeds system requirements, the regulator opens a discharge hole. “Displaced†fuel flows through the discharge hole and returns to the right hand side of the tank. Just like with a return line system, the movement of displaced fuel drives the siphon feed in the right side of the tank to deliver fuel to the pump in the left hand side.
Operations and Testing
Normal fuel pump operation in a BMW is fairly simple. As soon as the ignition is turned on, the ECU grounds the pump feed to complete the circuit and the pump pressurizes the system. The residual pressure in the fuel line provides the gasoline to start the engine and then fuel flow from the pump takes over.
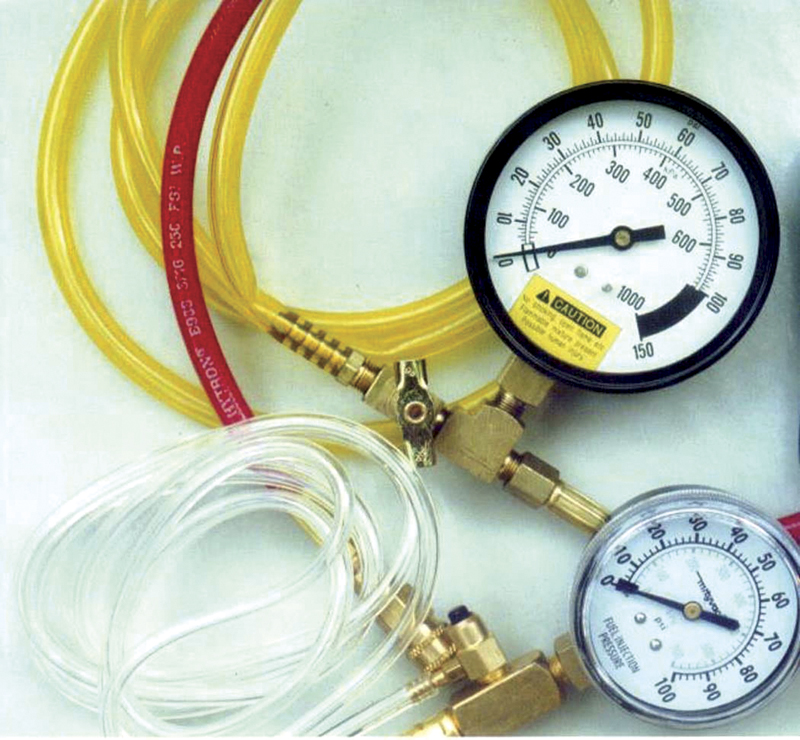
A good fuel pressure gauge is absolutely essential to any auto service operation. Many misdiagnoses have been caused by inaccurate gauges.
If the key is on, but the engine isn’t turning over, the ECU opens the pump ground to turn off the pump. The ECU relies on the signal from the Crankshaft Position Sensor to determine if the engine is spinning.
Weak fuel delivery, which may or may not be the fault of the pump, will cause a lean condition, hard starting (both hot and cold), poor idle, hesitation or stumble under acceleration. The vehicle may even stall on the road, only to restart and run normally for a while after it has cooled down. Any lean condition can trigger diagnostic codes because of high HC levels and misfire.
Obviously, if the pump has failed, there will be no pressure at all in the system. However, in a no-pressure situation, if you can’t hear the pump running when the ignition is on and the engine is turning over, your first thought should not be bad pump! Instead, think “no electricity.†Check voltage to the pump. If voltage is low, look for a corrosion or loose connection problem. If there is no voltage, check the fuse and relay. If a fuse is blown, don’t just replace it. A blown fuse is a symptom, not a problem. Find out what caused the excessive current draw that blew the fuse.
A low pressure output with higher than normal amperage draw can mean a badly worn pump that is about to die. It can also mean a pump that is working too hard and not getting enough fuel pushed through because of dirt or other contaminants clogging the fuel system. The contamination can be at the inlet screen to the pump, in the fuel lines, a badly clogged fuel filter, or any combination of the three.
Because contamination can cause higher than normal current draw, and more current accelerates wear on the pump motor, a pump that has been forced to deal with contamination for a prolonged period should be carefully tested. It may be a candidate for replacement due to excessive wear.
Some techs think that if the fuel pump relay feels hot, the pump must be bad because it is drawing too much current. Wrong. A hot relay almost always means a bad relay or corrosion somewhere in the circuit that is causing excessive resistance. It is rare for a failing pump to draw enough amperage to heat up a relay.
Interpreting PSI
BMW has specific procedures for interpreting fuel system pressure readings for each model, but the following steps are representative of the general technique.
- If your customer has drivability complaints, or the engine lacks power:
Run the engine at idle speed and measure fuel pressure. If the pressure reading is 0.2 bar (three psi) below normal, the pressure lines or fuel filter are clogged, or the pump voltage is low.
If the reading is 0.2 bar (three psi) above normal, turn off the engine and observe the pressure gauge. If the reading drops to normal, there is an obstruction in the fuel return or there is a kink in a fuel line. If the pressure remains high, the pressure regulator is probably faulty. A much less likely cause is a completely blocked return line.
- If your customer complains of hard starting:
Run engine briefly at idle speed and then turn it off. Record the pressure reading when the engine is shut off and then check the reading 20 to 30 minutes later. If the pressure dropped by more than 0.5 bar (7.25 psi), restart the engine and allow the pressure to stabilize. Shut off the engine while also clamping off the supply just ahead of your pressure gauge. Note that reading, then recheck 20 to 30 minutes later.
If the reading dropped by less than 0.5 bar, the problem is a fault in the fuel delivery lines, including the in tank lines; or a defective non-return valve in the fuel filter.
If the reading dropped by 0.5 bar or more again, the pressure regulator is faulty.
Test tips
There are a number of tips for fuel system pressure testing that come in handy:
- Make sure you take accurate readings. A deviation of just 0.2 bar or three psi from spec can cause problems.
- Readings should react quickly, almost violently, between “dead head†(return line clamped) and running pressures. A slow rise means problems with the pump or clogging.
- After you’ve bled the air from the hose to your gauge, you should see rapid, almost violent changes when the ignition key is turned on. Again, a slow increase means problems.
- Having adequate pressure doesn’t mean you also have good flow. Check system output to make sure the pump can deliver not only pressure, but also volume.
- Don’t be surprised if in some cases the pressure reads normal, but as soon as you open the system for testing the test flow bleeds off enough pressure to kill the engine.
- System leak down can cause hard starting and other problems. If psi won’t hold, pinch off the supply line. No change? Then the check ball in the pump isn’t the culprit. In cases where leakdown disappears when the return line is pinched, the problem is a perforated diaphragm in the pressure regulator, or possibly a leaking injector.
Parting shots
These tips will help ensure a successful fuel pump installation:
- If you find any contamination in the pump and or filter, check the tank for junk also. Installing a new pump in a dirty tank is a sure recipe for a comeback that you will pay for.
- Never reuse any seals, O-rings, screens, etc. when installing a new pump. A new pump deserves all new accessories.
- Never “test†a pump by running it dry on your bench. Without gasoline to providing cooling and lubrication, you can quickly ruin a pump. Always start a pump after installing it and filling the tank.
- Check the fuel lines whenever you replace a pump. Replace any lines that show signs of wear or physical damage.
0 Comments