New technologies and evolved fuels are making the compression-ignition engine more acceptable in terms of performance and emissions, and rising fuel prices assure a big demand that will put more and more on our roads soon.
Leroy Robert “Satchel†Paige, the legendary baseball pitcher, once said, “Don’t look back, something might be gaining on you.†Well, if technicians ignore that advice and look back, they’ll find that new diesel technology is gaining fast, and that they’d better do some learning if they want to stay in the lead. The popularity of diesels in Europe and the rest of the world has been growing rapidly, and now this trend is finding its way to the U.S. thanks to expensive gasoline. So, expect to see a huge jump in the sales of cars and light trucks thus powered. It’s time to sit up and take notice of this phenomenon so you’ll be ready when these vehicles roll into your bays.
Diesels have some advantages over gasoline engines for both carmakers and consumers. To the vehicle manufacturers, they offer better mileage to help satisfy the government’s Corporate Average Fuel Economy (CAFE) standards. They offer consumers lower fuel and maintenance costs, and more robust durability, which figure large in the Total Overall Cost (TOC) factor, something today’s savvy buyers consider. Of course, diesels carry a premium price (another plus for the carmakers), but the savings easily wipe that out over the life of the vehicle.
The Fuel Factor
The future success of diesel engines in the U.S. lies in the two fuels that are currently being developed to meet the demands of lower emissions and lessened dependency on imported petroleum: Ultra Low Sulfur Diesel (ULSD) and biodiesel.
One of the main reasons that most of the highly-sophisticated, electronically-controlled diesel engines so popular in Europe haven’t yet migrated to the U.S. is the lack of availability of acceptable fuel. European diesel is much lower in sulfur than ours, and advanced Electronic Diesel Control (EDC) systems are designed to operate on low-sulfur fuel only. That’s about to change. To meet the lower oxides of nitrogen (NOx) and particulate matter (PM) emissions standards for 2007, the EPA has mandated that diesel sulfur content be lowered from 500 parts per million (ppm) to 15 ppm, a reduction of 97%. The transition began on June 1st of this year and is slated for completion in 2010. The State of California mandated September 1st of this year as the deadline for many types of commercial and fleet operators, with a graduated changeover for recreational and private users. Several other states have also set restrictions. At this point, the unanswered question is: Will the higher cost of producing ULSD overshadow the efficiency advantage of the diesel engine?
Cooking Oil?
It shouldn’t come as a surprise that biodiesel will be a key fuel source for diesel engines. Back in 1893 when Rudolf Diesel built his first experimental engine, it burned coal dust. When it exploded, nearly killing him, he started looking at liquid fuels, which could be atomized and injected under pressure. Diesel experimented with vegetable oils and, for demonstration purposes, ran his engine on peanut oil at the 1900 World’s Fair.
Biodiesel contains very little sulfur, is nontoxic and biodegradeable. Raw vegetable oil is not usable in a diesel engine, combustion-wise or legally. Fuel-grade biodiesel must be made according to EPA and industry standards. In order to become a legitimate fuel, vegetable oil goes through a chemical process called “transesterfication.†This separates the glycerin and fat, creating methyl esters, which are the fuel.
While corn-based E-85 (85% ethanol and 15%gasoline) is already being implemented in “flex-fuel†gasoline-powered vehicles, the infrastructure for a nation-wide program for the production and distribution of biodiesel is still in limbo. Many small co-ops, municipalities and some individuals are already making biodiesel for their own use, often out of used cooking oil retrieved from restaurants. Some experimental larger-scale production is planned and the prospects are good in the near future for a substantial supply of mixtures of biodiesel and petroleum diesel.
Big Market Penetration —Elsewhere
Consider the surprising fact that diesels now account for more than half the passenger cars and light trucks in Europe, with an even higher penetration in the UK. This didn’t happen by accident. While America pretty much ignored diesel power for automobiles over the last seven decades (hey, gas was cheap and we want our performance), the rest of the world — led by Europe —developed the basic diesel engine first used in a passenger car in 1936 (the Mercedes-Benz 260D) into a modern, clean and efficient power source. Older-style fuel charging systems are being replaced by various forms of direct injection, which offer better combustion, quieter operation, lower emissions and higher overall efficiency.
Indirect Injection
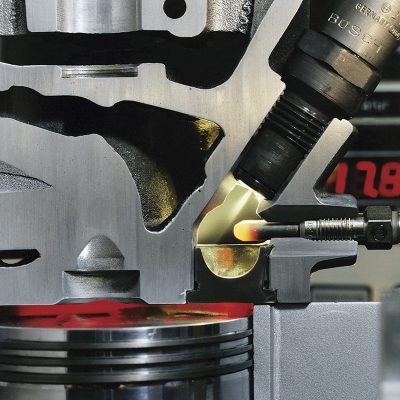
Ever since the pre-chamber concept was patented by engineer Prosper L’Orange in 1909, the standard method of injecting and igniting fuel in small, high-speed diesels has been the indirect injection system. A pump sprays fuel into a pre-chamber adjoining the combustion chamber where it mixes with air that has been heated by compression. Ignition begins in the pre-chamber and spreads smoothly into the cylinder. This slows and softens the combustion rate, thereby reducing noise and stress on the mechanical parts. The downside is reduced efficiency, partially due to heat loss from the pre-chamber to the cooling system. Another serious problem was high particulate matter and NOx emissions.
Electronic Controls and Really High Pressures
The mandate for lower emissions in Europe during the late 1980s led to the development of electronically-controlled, very high pressure direct injection systems, a victory for the “Green†party. The first in production was Volkswagen’s Turbo Direct Injection (TDI) system, the electronics of which allow fuel to be injected directly into the combustion chamber in two stages, which softens operation. The combination of five-hole injectors and almost 14,000 psi makes a fine mist that contributes, too. A turbocharger and intercooler increase the amount of air that gets into the cylinders, allowing for greater performance while decreasing emissions.
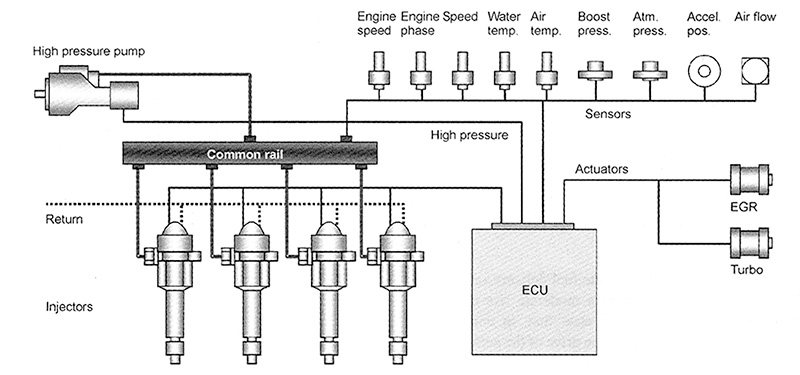
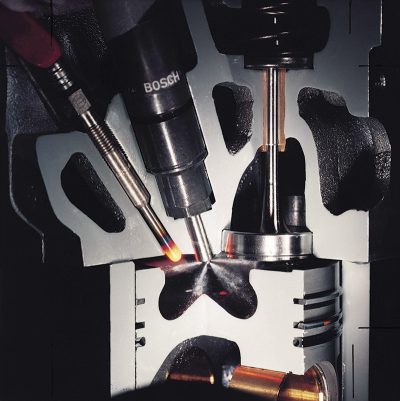
That was a good start, but now direct-injection technology has become even more advanced. Take the common rail system, for instance. The pump supplies continuous pressure (up to 30,000 psi, which allows smaller injector holes — the fuel isn’t just atomized, it’s vaporized) to an accumulator that feeds electrically-actuated injectors. The solenoid type can be opened up to five times per combustion event. There’s also the piezoelectric type that operates even faster. These crystal structures react instantly when an electrical charge is applied to achieve a lightning-quick response interval of .1 millisecond, which makes up to 10 pulses possible.
By tailoring the pulses instantly to the mode of operation, great improvements in efficiency, emissions, smoothness, noise and performance can be made. The duration of the pulses determines the amount of fuel injected, somewhat like a gasoline engine’s EFI system.
Several styles of direct injection systems are in use today, each championed by the system manufacturer or vehicle maker. Some prominent examples:
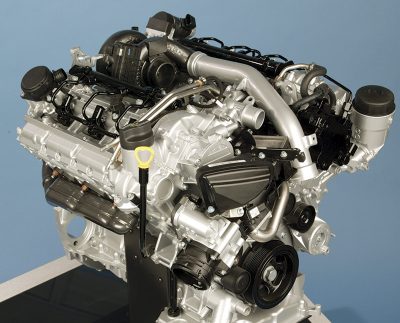
- Mercedes-Benz calls its Robert Bosch common rail system CDI, which is currently found in the 2.7L Dodge Sprinter and the 3.2L M-B E320 CDI. By the way, for 2007 the E-320 will incorporate BLUETEC, an advanced exhaust treatment system, called Selective Catalytic Reduction (SCR), to remove particulate matter and NOx.
- DaimlerChrysler’s CRD is being used in the Jeep Liberty 2.8L and its sucess or for 2007, the Jeep Grand Cherokee turbocharged 3.0L. Future versions will have piezo injectors.
- Denso has improved its high-pressure common-rail diesel injection system that operates at over 26,000 psi (that’s 1,800 BAR), creating finer atomization for better combustion. The injectors are capable of opening up to five times during the combustion cycle, providing a smoother, more uniform burn, and thereby reducing noise and vibration. This also results in lower NOx levels and less solid particulate matter.
- Siemens VDO has developed a common-rail direct-injection system that utilizes piezo actuators to provide up to nine injection sprays per cycle. It’s getting excellent economy, emissions and NVH results in European vehicles.
Unit Direct Injection
The newest technological breakthrough in diesel fuel systems is the unit injector idea. Instead of being fed high-pressure fuel from a central pump, each injector receives fuel at low pressure, then generates the necessary high pressure internally. This is accomplished by the action of a small-diameter cylinder and a piston driven by the engine’s camshaft. The actual injection pulses are controlled electronically as they are in common rail systems. The claimed result is more consistent pressure and more comlete combustion. These systems operate at 30,000 psi (2,050 bar) and up.
Particulate Filters and Exhaust Treatment Systems
Diesel particulate filters (DPFs) are being used in the newest diesel exhaust systems to trap particulate matter (soot), then burn it away under catalytic reaction.
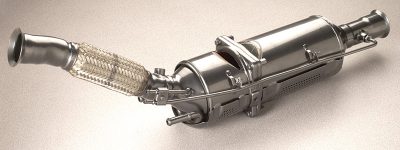
DPFs are damaged by the sulfur in diesel fuel, so they must be replaced regularly — about every 75, 000 to 90,000 miles — at what can be assumed will be great expense (a future profit opportunity for you). The advent of ULSD will prolong the life of DPFs and result in cleaner emissions. Tenneco, Denso and others produce DPFs for the OEMs and the aftermarket.
A number of systems for “scrubbing†diesel exhaust ranging from catalytic reaction to chemical additives are beginning to reach the market. In Europe, Selective Catalytic Reduction (SCR) is being used to decrease NOx and particulate matter. Also, a urea-based chemical called Adblue, can be injected in small quantities into the exhaust system to further reduce NOx.
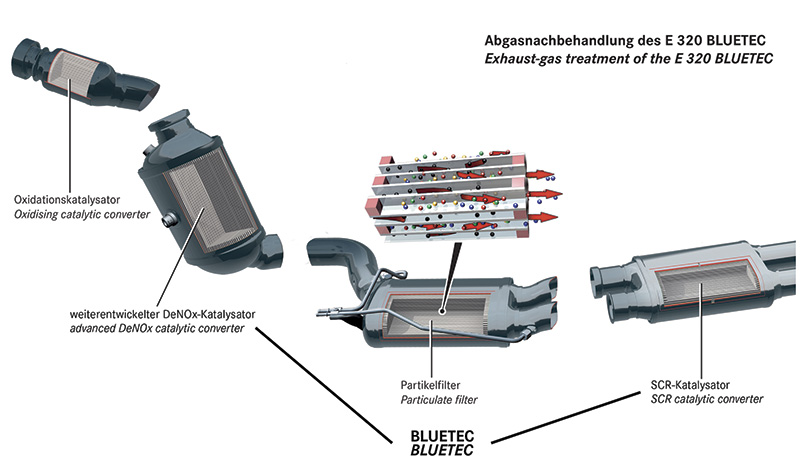
More Facts to Consider
If you aren’t convinced that diesels will become much more common in our passenger car and light truck population in the near future, and thus have a huge impact on the service business, consider these facts:
- BMW plans to bring 3.0L and 4.0L diesel engines that operate on ULSD and use Selective Catalytic Reduction (SCR) emissions systems to the U.S. in 2008.
- GM has successful diesel programs in Europe, Asia and Australia. The General is poised to bring its high-tech diesels to our shores as early as 2008.
- Ford is one of the top producers of diesel cars in Europe and the UK. Ford-owned Land Rover, Volvo and Jaguar are deep into diesel-powered vehicles. Many of Ford’s diesel engines may be earmarked for the U.S.
- DaimlerChrysler’s assembly plant in Belvidere, Illinois has started production of the 2007 Dodge Caliber equipped with the Volkswagen 2.0L TDI engine for the European market. It can easily be tweaked for use in America.
- Isuzu has been one of the biggest suppliers of diesel engines in the Asian market for a long time — the company produces diesels for some of the largest automakers. Surely, Isuzu will be a player in the growth of diesel engines here.
- Honda has declared that it has a high-tech diesel engine under development and will start selling it in the U.S. in the next year or two.
- Volkswagen will bring several 2.0L models to North America for 2008, thus extending its domination of the diesel passenger vehicle market. We will also see a new version of the powerful V-10 Toureg diesel on this side of the pond.
So, Satchel Paige’s admonition notwithstanding, look back and see that diesels are gaining on us. We need to educate ourselves in the technologies of the new diesels and prepare to service them. They’re due to arrive sooner— and in larger numbers — than you may think.
Domestic Light Truck Diesel Update
Ford, General Motors and Dodge have offered optional diesel engines in their pickups lines for many years. Over 60% of full-size 3/4-ton and one-ton domestic pickups sold last year were diesel-powered. All three companies have upgraded their diesel engine designs, engine management and exhaust systems to keep up with rapidly advancing technologies and changing regulations. Here’s a look:
Ford E & F-Series
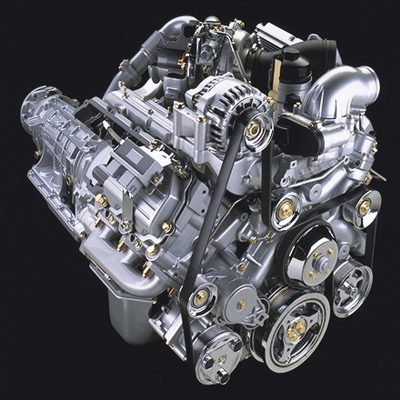
In 1983, Ford introduced the 6.9L V8 diesel (from International Harvester/Navistar). That was supplanted by the 6.0L 325 hp/570 lb-ft. Power Stroke engine in 2003.
This uses an electro-hydraulically actuated injection system for better fuel and emissions management. Ford plans an update in the near future, but no details are available at this time.
Dodge Ram
The 2007 Dodge Ram pickup will drop the long-used 5.9L Cummins diesel in favor of a 6.7L Cummins turbocharged, intercooled, I-6. The new engine will be equipped with a Bosch electronically-controlled high-pressure common rail injection system. The new 305 hp/610 lb-ft. powerplant is designed to run on Ultra-Low Sulfur Diesel (ULSD) fuel.
Chevrolet/GMC
The older-style 6.2L and 6.5L diesel engines were optional in 1982-2000 GM C/K series pickup trucks, Chevy Tahoe & Blazer, Suburban, GMC Yukon & Jimmy, G-vans, and motor home chassis, in naturally aspirated or turbo versions.
Since 2001, GM has used the high-tech 6.6L Duramax 6660 diesel engine in its Chevrolet Silverado and GMC Sierra HD trucks, as well as throughout its commercial line. The Isuzu-designed 300 hp/520 lb-ft. engine utilizes a Bosch common rail direct injection system. For 2007, the engine is being tweaked to handle ULSD fuel and is being fitted with further exhaust treatment technology.
Resources for Diesel Service Information and Training
Service Information
The following vehicle manufacturers offer diesel service information on their technical service information websites for a usage fee:
DaimlerChrysler ………… www.techauthority.com
Ford Motor Co. ………….. www.motorcraft.com
General Motors ………….. www.gmtechinfo.com
n Mercedes-Benz …………… www.startekinfo.com
Volkswagen …………………. www.eban.com/vw
Training Resources
Many community schools, colleges and vocational centers offer diesel training classes. Check your local schools for availability. The following is a list of just a few of the resources that offer diesel training:
Turbo Training specializes in on-site training courses, books and materials for the repair of Ford 6.0L and 7.3L engines. Bruce Amacker, the principal trainer, is a highly-skilled and respected technician, and one of the few people who provide training for light diesels. www.turbotraining.com
Universal Technical Institute (UTI) offers classes at three campuses: Houston, Phoenix and Glendale Heights, Illinois. www.techtraining.com
The Association of Diesel Specialists (ADS), the society for professional diesel technicians, offers training. Although primarily for heavy-duty truck, industrial, marine and locomotive engines, the site offers valuable information on all forms of diesel systems. www.diesel.org
Other Resources:
- U.S. Environmental Protection Agency, www.epa.gov
- Clean Diesel Fuel Alliance, www.clean-diesel.org
Draggin’ Diesels?
The National Hot Rod Diesel Association (NHRDA) organizes and promotes diesel motorsports, including drag racing and sled pulling competition. Check the NHDRA out at www.nhrda.com.
Diesel Service Tip from Turbo Training
A common problem on 2003-2006 Ford F-Series Trucks with the 6.0L diesel occurs when the PowerCore air filter doesn’t fit correctly in the intake housing, creating an air gap. This results in dirt settling on the mass air flow sensor (MAF), affecting engine operation –or worse, damaging the cylinders and pistons.
What’s happening is warpage caused by underhood heat and the too-thin plastic construction of the MAF housing. There are two snap clips holding the filter to the housing. If there were only a third clip on the passenger side, no problem would have developed.
Ford says that a 16mm (5/8â€) gap between the filter and the MAF housing is normal on the passenger side of the filter. This is not a 16mm gap for dirty air to go through, just a visual gap between the housings.
Annual maintenance should include removal of the filter to check the sealing surface where it meets the MAF housing. Note any warping of the MAF/air cleaner outlet housing with the resulting 3/8†gap that allows dirty air into the engine. Look for dirt that has bypassed the filter and settled in the turbo intake duct and on the MAF.
It’s easier to remove the filter assembly (including MAF housing, inlet hosing, etc) than the filter element by itself. Do not use compressed air to clean the filter!
by Tom Nash
0 Comments