By Steve Campbell
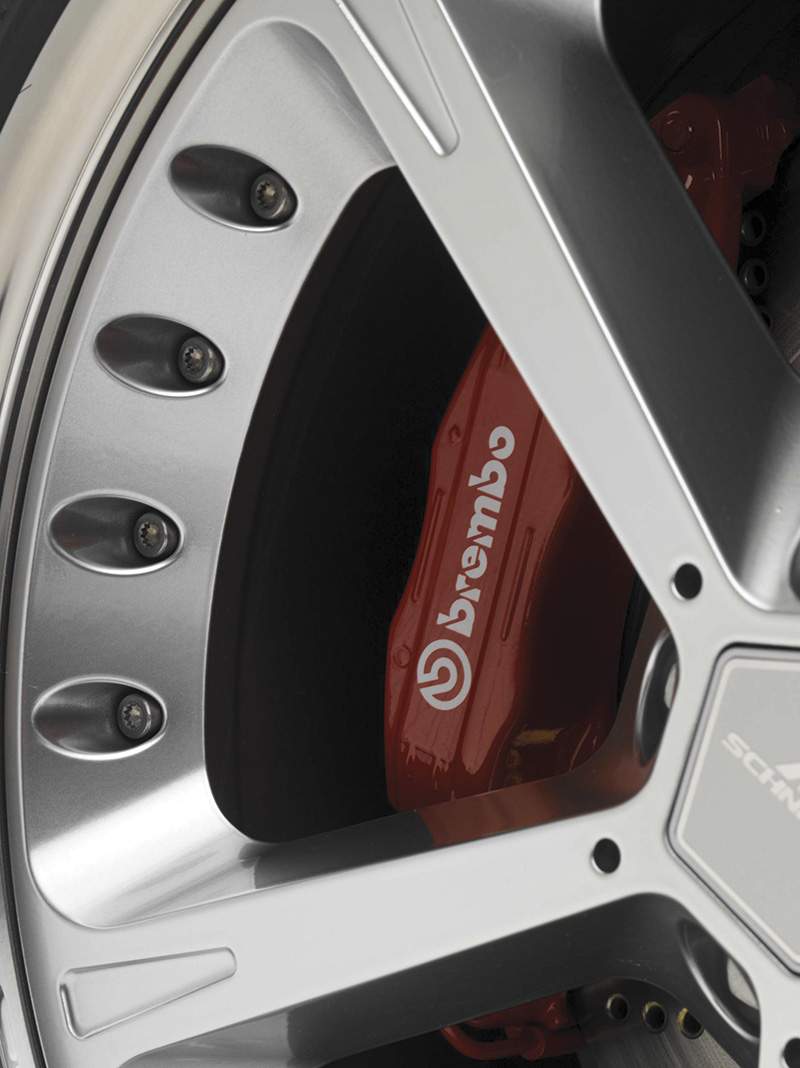
With today’s large-diameter, open-spoke wheels designs, brake packages are highly visible. Some customers will opt for a performance brake package on the basis of cosmetics alone.
Every car and truck requires replacement brakes numerous times during its driving life. That’s a given and consumers accept it. They tend to depend on their service center or dealership to recommend the most appropriate product, which often consists of direct replacement parts, including pads, rotors and, less frequently, calipers on newer disc-brake equipped vehicles. In many cases, however, a customer may benefit from the addition of performance brake components for a safer and more enjoyable driving experience.
“There’s a big benefit to selling performance brakes to customers who have bought late-model pickups or SUVs with larger-than-stock wheels from the dealerships,†explained Todd Gartshore, president of Baer Brakes. “Those vehicles have increased the rolling mass by 30 to 40 pounds per corner, depending on what style and what manufacturer of wheel, and the customer has no idea how badly the brakes were affected. From 60 mph, it could be 12 or 14 feet in increased stopping distance with the bigger wheel. Even in a light wheel—a 20-inch Weld wheel might actually be a pound less than a factory 17-inch wheel, for instance—the tire that goes with it weighs significantly more, so the package still ends up being plus 25 or 30 pounds. We sell a plus-size rotor that will give the customer the benefit of having increased leverage without extreme increases in noise, vibration or harshness (NVH). By increasing the rotor diameter, we increase the leverage and braking torque while offsetting huge performance differences that occurred when they put the wheels on.â€
Owners of performance vehicles may also be candidates for brakes upgrades. “The benefits to installing a performance brake system are two-fold,†said Dann Ingebritson, technical instructor for Affinia Under Vehicle Group, which includes Raybestos® brand brakes. “The number-one benefit is improved stopping ability. Performance vehicles are typically pushed to their limits and need the extra stopping ability that the driver demands. In addition, because performance brakes are generally installed on a vehicle that has been modified in some way—with a higher horsepower engine, wider tires or better suspension parts, for example—factory brakes are usually not sufficient to handle the vehicle’s faster acceleration and cornering abilities.â€
A third class of potential performance-brake customers—perhaps the largest yet least educated group—are those who frequently encounter conditions where braking is almost constant. “If a family goes into the mountains and the driver doesn’t understand how to use the transmission gears to slow the vehicle, he or she may ride the brakes halfway down the mountain and glaze the rotors,†said Geoffrey Wilsey, director of North American aftermarket sales for Brembo Brakes. “Once the rotors become glazed, the car won’t stop the same. Anybody who does a lot of braking will generate a lot of heat, and a cross-drilled rotor, for example, will allow them to dissipate that heat and clear the gases so that the pad bites better and provides improved stopping power and fade resistance. A vehicle driven in those conditions could really benefit from a performance rotor. In that case, spending a little more money buys peace of mind and safety.â€
Heat is the natural result of a friction-based braking system. But when allowed to accumulate, heat can also decrease braking efficiency. For instance, brake fade or pulsing can occur when material from the pad melts and glazes the rotor. In addition, heat may boil the brake fluid, resulting in a spongy-feeling pedal. A fluid with a high boiling point helps (as does a yearly flush and fluid change), but so can performance brake components that more efficiently dissipate heat. While there are complete ultra-high-performance braking systems, most customers who choose to upgrade will most likely replace the stock rotor with a performance replacement and a higher quality pad with a greater friction level.
PERFORMANCE PADS
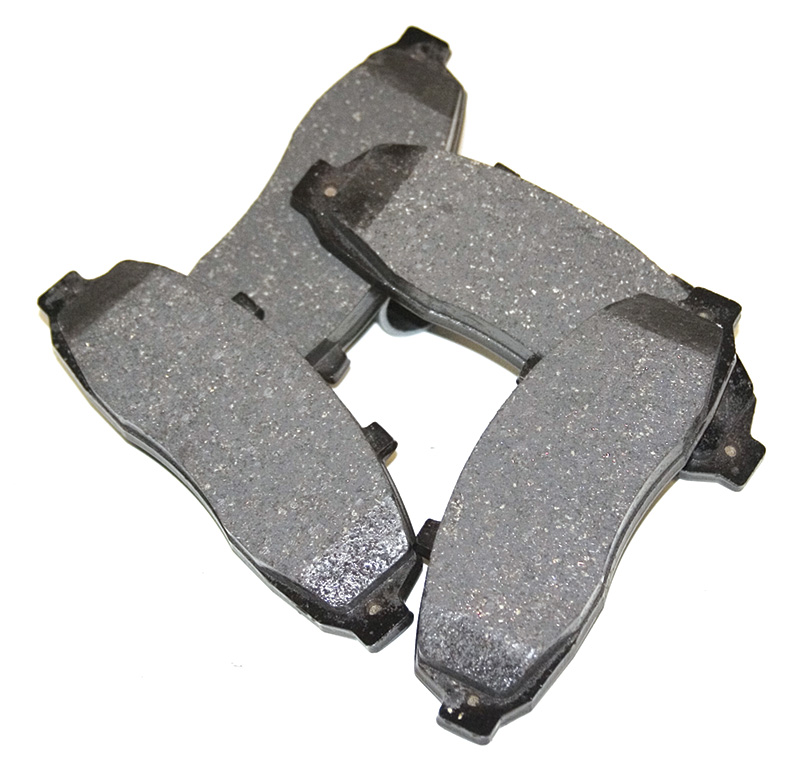
Disc brake pads have evolved from asbestos to organic to semi-metallic to ceramic. The new ceramic pads offer a host of advantages, including reduced noise, higher temperatures with less fade, reduced wear and minimal brake dust. Pads offer the easiest and least costly improvement to an OE system and are therefore likely to be attractive to the widest range of customers.
The easiest and least costly improvement in a braking system is installing better pads.
“Regular brake-pad construction is normally a compromise between noise, stopping ability and longevity,†said Ingebritson. “Performance brakes are typically most concerned with stopping ability and brake fade, and they utilize a higher metallic mixture to achieve improvements in these areas.â€
Semi-metallic performance pads reduce stopping distances and offer the added benefit of functioning better than OE replacements at high temperatures. That’s crucial for towing applications, particularly with diesel-powered vehicles that are inherently heavier than similar models powered by gasoline engines. Pads must be matched to the rest of the braking system, however. A high-friction pad used with a standard rotor may even increase the amount of heat generated, so proper combinations are mandatory.
Performance pads made of semi-metallic materials offer the benefit of shorter stopping distances and increased safety, but they also produce marginally more noise than original-equipment pads. Ceramic pads offer a new evolution in pad technology, which had previously progressed from asbestos to organic to semi-metallic types. Ceramic pads are quieter, accept high temperatures with less fade, and they reduce wear—albeit at an increased cost.
“The Baer Sport Touring pad, which is ceramic based, has about 135 different chemical elements,†said Gartshore, “but the real end result is that we get the highest level of performance we can with the least compromise to noise and, of course, minimal dust.â€
ROTORS
There are rotors available today at extremely low prices on the Internet and at some of the large auto-parts chains — but price point is their only benefit. In all likelihood, they were cast at the lowest range of iron properties. For instance, pig iron has a high carbon content that makes it very brittle. Under high heat, the metal used in some lesser rotors will migrate, creating soft and hard spots as the metal changes chemically. To overcome that problem, performance brake manufacturers add silicon to the material for greater stability and elasticity. With the proper compounds and treatments, a rotor won’t change shape when it gets ultra hot, even when it glows cherry red. The more stable material performs better at higher temperatures and is more durable.
Slotted performance rotors also work to dissipate heat as well as gas buildup that can be trapped between the rotor and the pad, decreasing braking effectiveness. Slots also dissipate water quickly so that brakes remain effective even when immersed, such as when the car is driven though a flooded intersection. Slotted rotors have also become popular for use with today’s large-void spoked wheels, since the brake rotors and calipers are more visible.
“Brembo’s performance discs are born from our OE disc,†said Wilsey. “There are absolutely no metallurgical differences between the two. The Brembo disc is going to meet or exceed the OE specs, and when we drill a disc for slotting, we know exactly how much material can be taken away, we know the exact alignment and location of the holes to be drilled into the disc
and how many holes to put in it. In some poorly made products, the holes are drilled right through the veins in the disc, compromising its integrity.â€
Consumers who brake aggressively or encounter conditions where the brakes are used frequently will benefit from replacement performance rotors. However, when a truly superior brake system is required, larger rotors may be appropriate. All performance brake manufacturers offer large rotors along with appropriate mounting hardware, calipers and pads. The Gran Turismo is the Brembo model.
“The size of the disc in the Gran Turismo is dramatically different,†said Wilsey. “A stock vehicle may use an 11- or 12-inch rotor, and putting a 14- or15-inch disc on it is like night and day. When you go to that type of system, you completely change the braking characteristics of the vehicle.â€
The rotor used with the Gran Turismo system is a floating disk, in which the bell or hat is mounted to the disc using special bolts with spring-loaded tensioners. As the disc expands and contracts under extreme conditions, it can move slightly so that it runs straight through the calipers. A solid disk, which is the type used in most OE applications, is cast in one integrated piece. Making the change to a larger rotor requires a complete change of the braking system and can be quite expensive, so it’s not for the casual user.
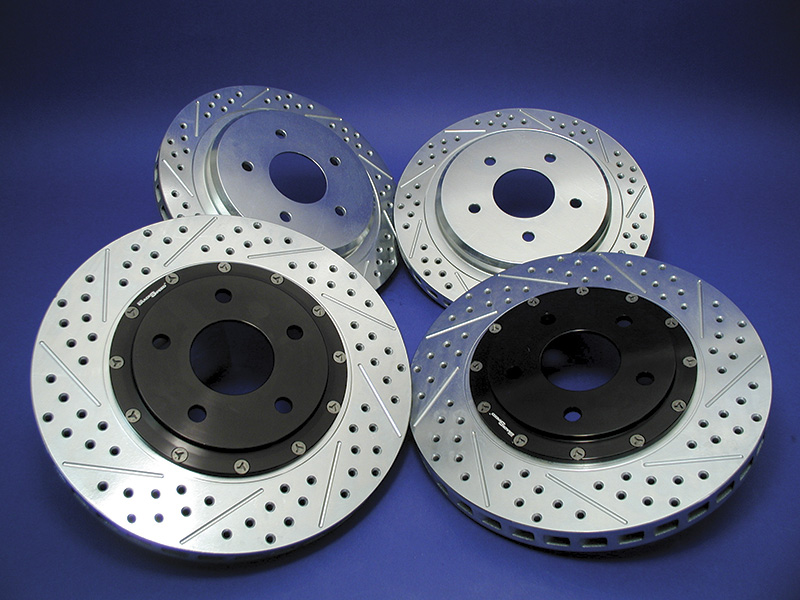
The range of rotor types is vast. The simplest are one-piece castings, and the high-end units are two-piece “floating†units that are cross-drilled and/or slotted for better high temperature and wet performance. A direct replacement disc is another low-effort swap that may appeal to not only performance customers but also those concerned with cosmetics alone.
CALIPERS
“Most high-performance materials come at a higher price of the elements that must go into the material to satisfy customer requirements.â€â€”Jerry Forystek, Affinia Under Vehicle Group |
Many OE calipers are made of iron, which has a high resistance to temperature but retains heat once it has built up. Some automakers have begun to use aluminum calipers, which heat quickly but also cool quickly. Aluminum is also lighter than iron, so there is a weight benefit. Because of the quick thermal recovery time, the OEs can use smaller brakes for some applications. Because they’re using aluminum mostly for the weight savings, however, the often don’t take full advantage of designs that maximize performance. For instance, manufacturing a caliper out of a single piece of aluminum—called monoblock construction—and using multiple pistons is common in performance brake systems.
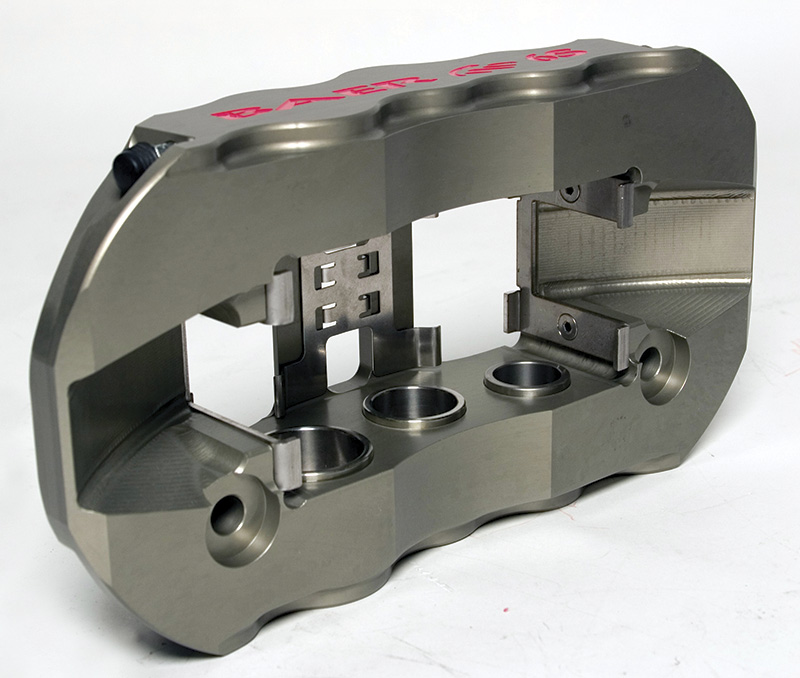
Various caliper options are also available within the performance braking universe. The top-end units are monoblock (one-piece) aluminum units that feature multiple pistons on each side. A greater number of pistons provide greater and more evenly distributed clamping force.
“Going to a monoblock six-piston caliper that is receiving equal pressure from both sides increases the mass and the brake torque to increase stopping power dramatically,†said Wilsey.
Gartshore pointed out that a one-piece aluminum caliper decreases deflection. “That technology renders a caliper that doesn’t bend, doesn’t deflect, doesn’t move around, so what you apply at the pedal more directly translates at the wheel. Combine that with a pad that has good resistance to temperature, and you have a brake that should operate over the full spectrum, whether you’re driving down the highway and need them stone cold under a panic circumstance or you’re running around a local racetrack with the Corvette club.â€
PROVIDING A REALISTIC ASSESSMENT
While many customers might benefit from one or more elements of a performance braking system, not everyone is a good candidate for an upgrade. “The main drawbacks to performance braking systems are higher pedal effort and increased noise,†Ingebritson noted. “The higher pedal effort is most noticeable when brakes are cold because the different compounds used in these brakes typically need heat to reach optimum performance. In general, the formulations used in a typical performance disc pad have a tendency to generate more noise than most standard brakes. The new performance materials used in our Raybestos brand premium products are using new technology to gain this improved performance along with quiet operation.â€
The OEs build their brakes to minimize noise, vibration and harshness, sacrificing some performance for comfort. And while there is some compromise for increased stopping power, the noise differences are subtle.
“A slotted disc takes a micro shaving off of the pad every time it rotates,†explained Wilsey. “It takes a clean swipe of the pad and then expels the debris from the slots with centrifugal force as it goes around. At very low speeds when coming to a stop, the driver may hear a bit of a dit-dit-dit just when those slots are coming over the pad. On a drilled disc, you have a little bit more of a sensation or a sound of a performance brake system. It’s not loud, it’s just different. The slotted disc will also go through pads a little faster than a normal disc because it’s a more aggressive disc. Of course, that also depends on driving style.â€
If a customer is adamantly concerned about noise, a factory replacement may still be the best alternative. The crossover buyer who is just looking for safety or enhanced performance and is not a committed performance enthusiast is probably most comfortable with a pad change or a pad and rotor combination that provides an aesthetic look behind a modern open wheel.
A PRICE TO PAY
The cost of performance brake upgrades varies widely depending upon the extent of the change (pad, pad and rotor, complete system) and the parts being compared. There really is no way to evaluate the cost of a complete system change because of all the elements involved, but it is fair to look at the other types of improvements. If it’s a comparison between OE pads and rotors versus replacement performance parts, the cost to upgrade will probably be 15 to 30 percent more for the performance parts. If the customer compares prices using low-end, bargain-basement off-shore replacement parts, however, there may be as much as a four- or five-fold difference—but the customer should also be informed of differences in warranties between the various parts, which can be substantial.
“Most high-performance materials come at a higher cost due to the increased price of the elements that must go into the material to satisfy customer requirements,†explained Jerry Forystek, director of friction product development for Affinia Under Vehicle Group. “In a performance friction material, most customers are looking for improved stopping power over the OE brakes. They are also often looking for improvements in fade resistance along with longer life. Typically, this has come with a cost increase.â€
In addition to the better materials used in performance brakes, machining operations such as drilling or slotting the performance rotors also adds cost, as do the finishes and graphics applied to rotors and calipers for their aesthetic appeal.
“The salesperson needs to understand his customer and what the vehicle is going to be used for and how the customer drives and what drives that customer,†said Wilsey. “He might find out in conversation that the guy owns a boat. If so, that’s a great customer for performance brakes. He needs to dissipate heat so that he can have longevity. If he glazes those rotors and then has to have them turned on a brake lathe, he’s taking a bunch of life and longevity out of that original-equipment rotor. It would be better for him to make the investment now than pay a lot later over a long term.â€
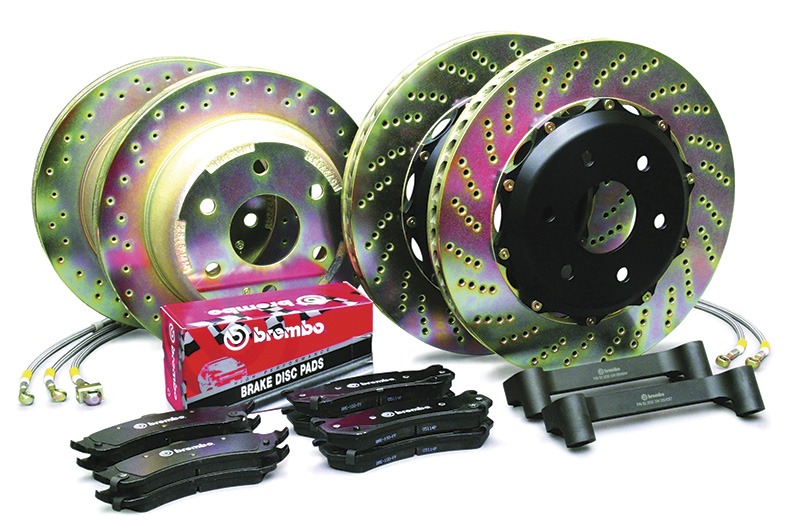
A top-line performance brake package features larger-than-stock rotors, monoblock calipers, braided-steel lines and complete hardware. These systems are expensive, since they call for a complete system replacement, so they will probably appeal to only the true “car guy†enthusiast,but the result is the ultimate in stopping power.
IN THE END
“Safety plays the most important rold in performance braking, but aesthetics are almost equally importantâ€â€”Dann Ingebritson, Affinia Under Vehicle Group |
The range of customers who might be open to performance upgrades is significant. A conversation about how a driver uses his or her brakes and any problems that might be alleviated by better equipment can reveal the needs and possibilities. While the towing applications are obvious candidates, salespeople and technicians should also keep an eye out for the customer who has already changed the vehicle’s tire and wheel combination.
“Of course, safety plays the most important role in performance braking,†said Ingebritson, “but aesthetics are almost equally important. To most ‘car guys,’ money is not the biggest issue—looks are. Seeing an oversized, coated brake caliper through the chrome spoke rims is a big part of the appeal of performance brakes. Most vehicles equipped with performance braking systems will never experience the type of driving the brakes are designed for, but they really look good.â€
0 Comments